随着人们生活水平的提高,我国城市生活垃圾数量逐渐增加,许多城市面临“垃圾围城”的困境[1-3]。目前城市垃圾处理方式主要有卫生填埋、堆肥和焚烧等,其中焚烧是将城市生活垃圾当作燃料直接燃烧,利用其燃烧过程中释放的大量热量进行发电及供热等应用。垃圾焚烧方法具有许多优点,如设备占地面积小,垃圾处理周期短,能实现垃圾减容85%~95%、减重70%~80%,且高温可以有效杀灭垃圾中的细菌和病毒,降低疾病传播风险等[2]。高温腐蚀是造成垃圾焚烧炉停机的主要原因,在设备维护成本中占很大一部分比例。垃圾焚烧过程中水冷壁管、过热器管、筛管等金属部件因高温冲击、熔融氯化物和硫化物的腐蚀以及高速烟气侵蚀而极易发生失效。同时,随着人们的垃圾分类意识逐渐增强、垃圾分类措施逐步完善,垃圾的热值逐渐增加,垃圾焚烧锅炉的运行参数特别是燃烧温度不断提升,受热面金属的腐蚀环境更加严峻,极易发生爆管等事故[4]。在金属部件表面施加耐腐蚀涂层是一种最为常见的防护措施。该措施因良好的性能和成本优势,在高温腐蚀防护中具有较大潜力。为充分了解垃圾焚烧的腐蚀特征,以及各类涂层成分特点和制备工艺,从而有针对性地建立腐蚀防护涂层策略,本文综述了垃圾焚烧炉中常见的Cl、S等腐蚀元素的高温腐蚀机理,介绍了实验室中常见的腐蚀性能测试方法及耐腐蚀涂层成分设计方法,并对未来的研究方向进行展望。图1所示为本文的图形摘要。
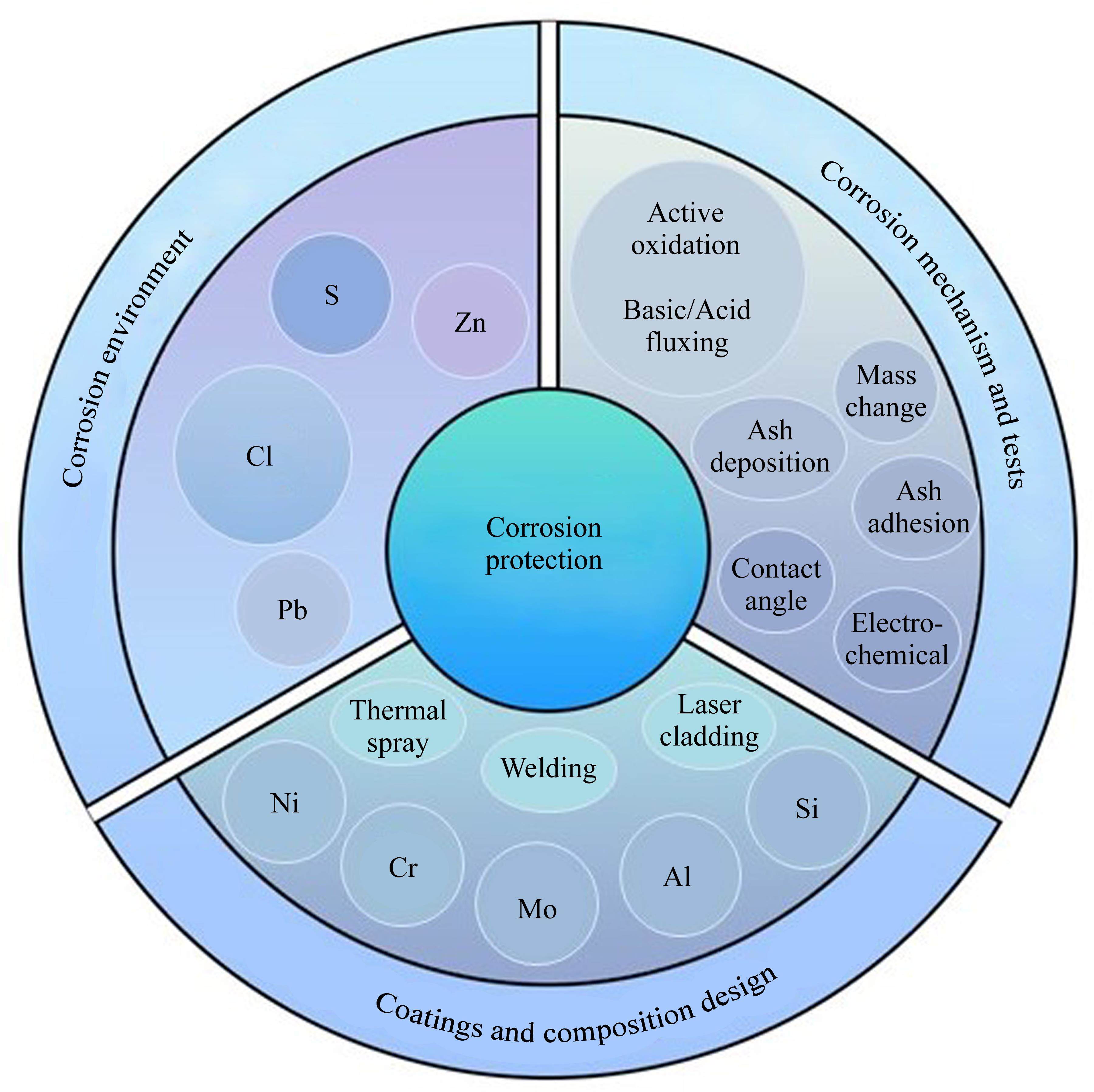
1 腐蚀环境与腐蚀机理
1.1 腐蚀类型
垃圾焚烧锅炉管道所受损伤通常包括物理和化学两个方面,前者主要通过高速颗粒对管道的物理撞击造成损伤,后者则通过一系列化学作用,腐蚀基体金属[5]。在实际情况中,化学腐蚀导致涂层表面形成疏松的腐蚀产物,在物理撞击的协同下,腐蚀产物更容易剥落,材料发生更严重的腐蚀[6]。受热面的腐蚀一般与Cl、S、碱金属及重金属等元素的存在有关,要使锅炉能在更高参数下安全稳定运行,需对垃圾焚烧系统中的腐蚀问题有更加全面的认识,从而找到更加经济有效的防腐手段。
1.2 腐蚀环境
城市生活垃圾是含有厨余垃圾、塑料、纸、木材等多种固体废物的复杂混合物。废弃物中的有机元素燃烧时产生的热量转化为电能,而无机元素则转变为飞灰和烟气。由于成分复杂、变化幅度大,城市生活垃圾焚烧产物具有较大的成分变化范围。与传统燃煤相比,城市生活垃圾品质较低,Cl和水含量较高、S含量较低。在典型垃圾焚烧炉中,HCl浓度可达数千毫克每立方米,而在传统煤燃料锅炉中,HCl浓度仅为几毫克每立方米[2, 7-8]。此外,焚烧过程产生含有碱金属和重金属元素的烟气,可直接或冷凝为沉积物与金属管壁反应。
典型垃圾焚烧炉中的腐蚀敏感区域为水冷壁、筛管、过热器、再热器等热交换管道,不同部位表面金属温度及腐蚀环境均有所不同。如图2所示,管壁温度低于300 ℃(腐蚀性介质熔点)时,受热面上发生液相腐蚀;当管壁温度高于320 ℃时,管壁金属与沉积相和气相的腐蚀反应加剧;温度高于500 ℃时,生成的氯化物和硫酸盐逐渐熔化,Cl-、O2-、

Boiler part | Steam temperature/℃ | Temperature/℃ | |
---|---|---|---|
Metal | Gas | ||
Waterwall | 265 | 200-300 | 800-1000 |
Screen tubes | 265 | 200-300 | 700-800 |
Superheater | 400 | 400-530 | 600-700 |
1.3 腐蚀机理
垃圾焚烧过程产生的高温烟气中含有大量酸性气体(HCl、SOx等)、气态氯盐(NaCl、KCl等)和成分复杂的飞灰颗粒。它们具有极强的腐蚀性,能够单独或者产生协同作用破坏金属表面形成的保护性氧化膜,从而加速材料的腐蚀过程。每种介质的腐蚀机理并不相同,现总结如下。
1.3.1 Cl元素引起的腐蚀
早期研究认为垃圾焚烧炉的腐蚀破坏主要由S元素引起,而目前看法有所改变。城市垃圾中的Cl含量较高,且Cl的高活性使得其在高温条件下几乎可以与所有的金属发生反应,并形成具有低熔点和高饱和蒸气压的氯化物。同时,Cl的存在提高了形成保护性氧化膜所需的氧分压,使氧化膜开裂并变得疏松多孔,降低了其有效附着性和保护性,进一步腐蚀基体。
1) Cl2和HCl
垃圾焚烧过程中往往会产生Cl2和HCl等有害气体。这些有害气体通常会与合金基体及表面氧化膜发生一系列的反应,使原本致密的金属氧化膜变得疏松多孔,从而丧失对基材的保护作用,引发严重腐蚀。许多研究者对腐蚀机理进行研究,目前普遍接受的理论为活化氧化机制(Active oxidation)[11]。以金属Fe为例,具体过程如式(1)~(6)所示:环境中的HCl和其他含Cl物质在氧化膜表面被氧化形成Cl2,随后Cl2和HCl通过氧化膜中的孔隙等缺陷向金属/氧化层界面扩散。在高Cl、低O分压处,Cl2容易与基体金属发生反应,生成金属氯化物[12],如图3左上角所示。金属氯化物挥发后向外扩散,在氧化膜表面被氧化,形成疏松多孔、无保护性的氧化物,且反应生成的Cl2重新参与循环,进一步加剧腐蚀。该机制示意图如图4所示。






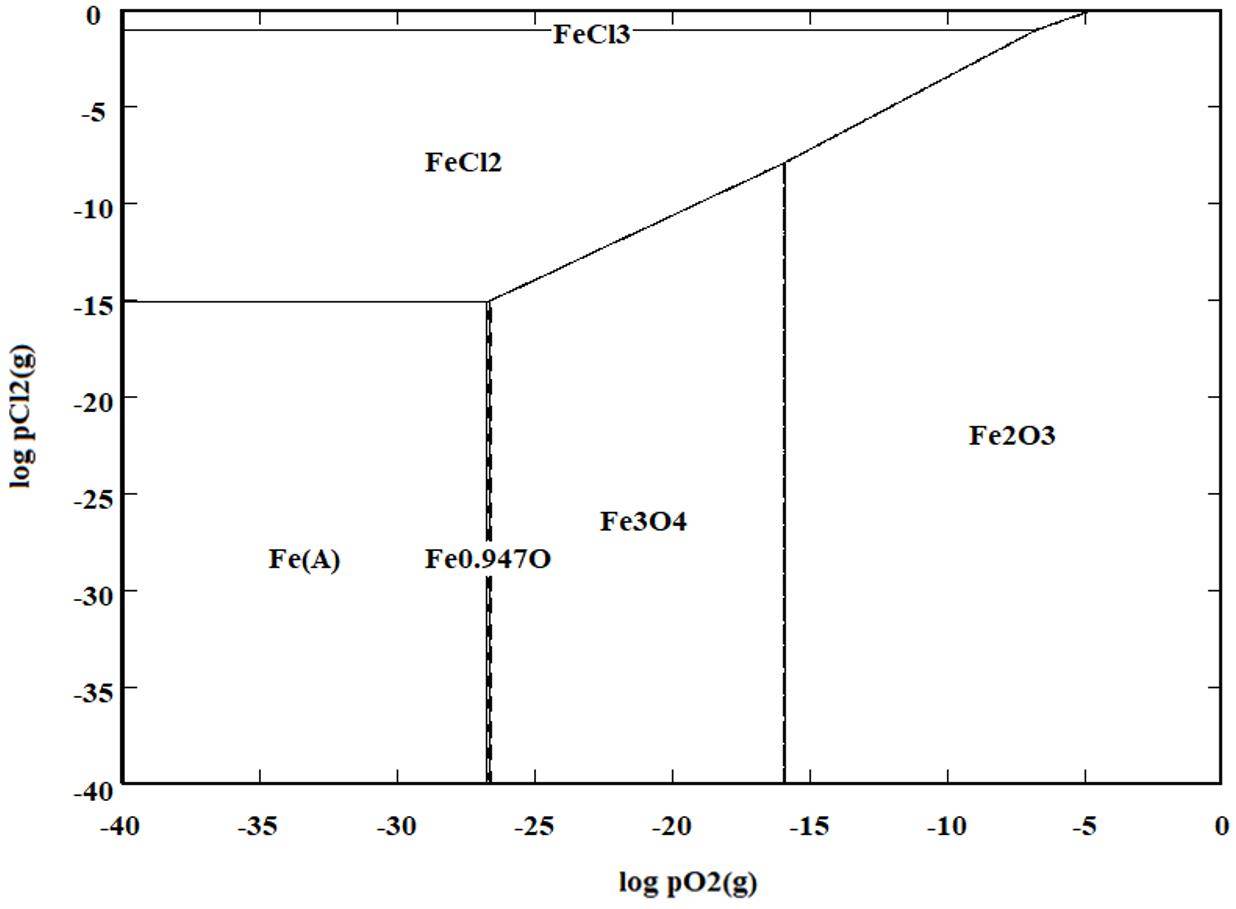
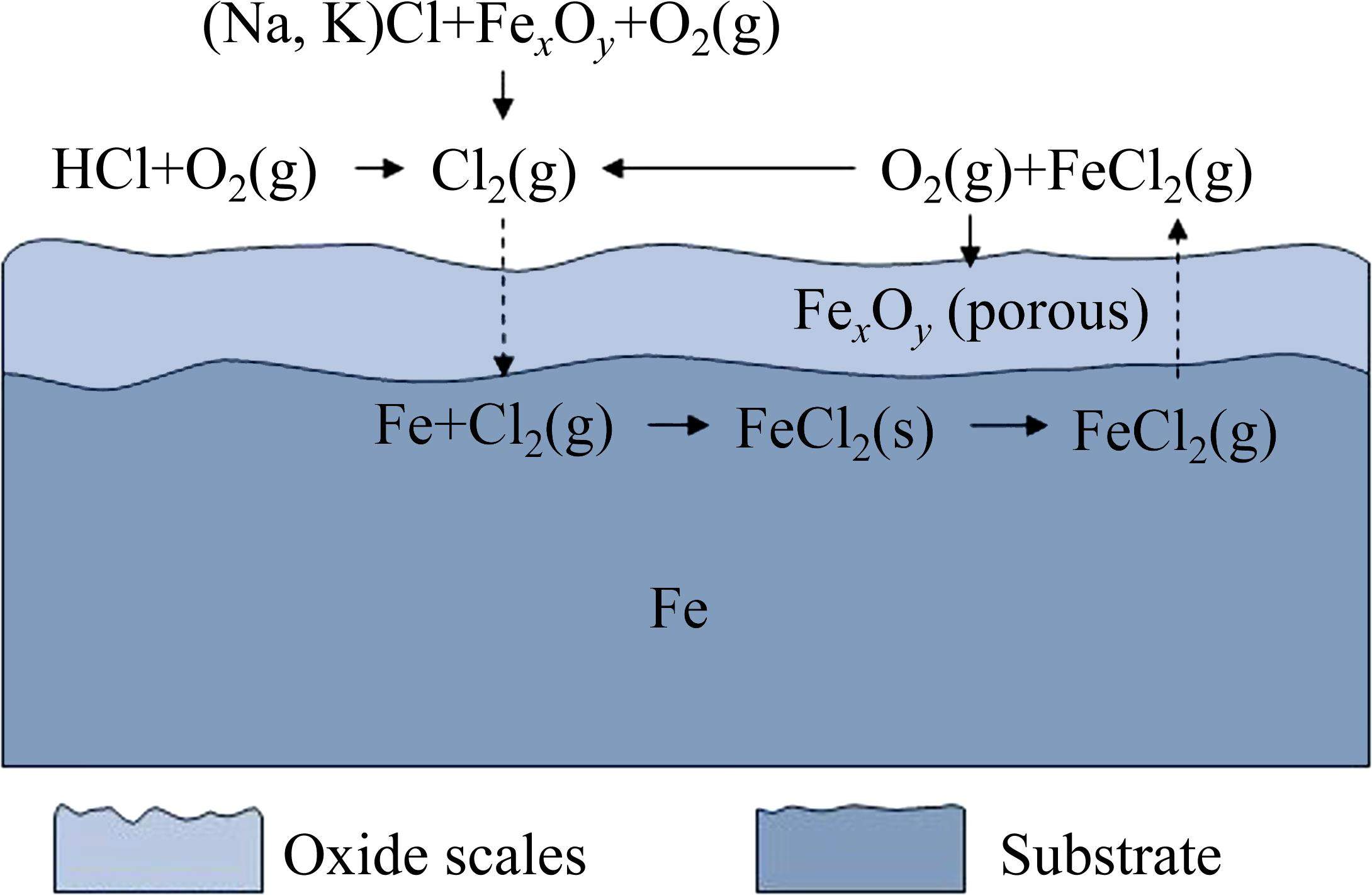
2) 氯盐
垃圾中的碱金属和重金属在燃烧时会以气态的形式迁移,或伴随烟气凝结,以固态形式沉积在金属管件表面,进而腐蚀金属。氯化物种类对腐蚀速率影响较大,常见的氯盐有KCl和NaCl两种,二者腐蚀性较强,且有研究表明,固态KCl沉积下Fe-Cr合金的腐蚀速率明显高于气态KCl环境下的腐蚀速率[13]。氯盐在氧气参与下与氧化膜反应,破坏合金表面氧化膜的完整性,同时生成铁铬酸盐和Cl2等物质。Cl2再次进入金属/氧化膜界面,继续进行活化氧化反应,进一步腐蚀基体。相关过程可以用以下反应式表示[14-15]:


此外,氯盐还可以直接和金属发生反应:
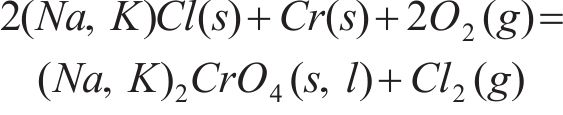
在表面氧化层破坏以后,氯盐可继续向内扩散,并与铁反应,生成氢氧化物,进一步破坏氧化膜:


Pb、Zn等重金属元素和飞灰中的含Ca物质也会与氧化膜发生反应[16-17]:






氯盐还可以与氧化膜中的金属碳化物反应(见式(18))。碳化物一般存在于晶界处,其溶解后更容易让腐蚀性介质通过,且生成的Na2O可以溶解金属氧化膜,进一步加剧腐蚀[18]。



除基于气相反应的活化氧化机制之外,高温熔盐中还会发生基于液相反应的电化学腐蚀。电化学腐蚀涉及电极过程和离子传输过程,电极过程包括阳极处的氧化反应和阴极处的还原反应。金属表面的局部区域可能成为阳极,金属失电子变成金属阳离子,并溶解入熔盐中。阴极处的O2、Cl2得电子变成O2-、Cl-,随后熔盐中的阳离子和阴离子可以在电解液中发生离子传输,从而促使腐蚀反应进行。在实际腐蚀环境下,往往是活化氧化机制与电化学机制的协同作用。在腐蚀初期,氯盐未开始熔化,大气中含氯介质和O2通过氯盐颗粒间的空隙靠近金属表面,在形成保护性氧化膜的同时发生活化氧化反应[11]。温度升高时,大部分盐混合物被高温熔化并在金属表面形成液相,此时发生一系列电化学反应[19]。
在合金/熔盐界面处,金属发生的阳极反应为:

式中:diss.表示溶解态。
在熔盐/气相界面处,O2、Cl2等发生的阴极反应为:


随后,金属阳离子与阴离子结合:


产生的金属氯化物像熔盐/气相界面扩散并被氧化:

该过程形成多孔无保护性的氧化膜,且释放的Cl2将促进活化氧化反应进行,进一步加速金属腐蚀[20]。
值得注意的是,多种金属氯化物混合时会形成低熔点共晶盐,造成液相腐蚀,并加速腐蚀发生。主要原因首先是液相中的化学反应速率比固相的更快,其次是液相能够作为电解质溶液,提供离子转移通道,促使液相与金属发生电化学腐蚀,从而加速腐蚀的发生。例如,NaCl的熔点为801 ℃,KCl的熔点为776 ℃,其混合后形成的共晶盐熔点仅为667 ℃,远低于单一氯盐的熔点[21]。实际锅炉中,基体一般为铁基合金,当环境中只存在KCl时,尽管纯KCl熔点为772 ℃、生成腐蚀产物FeCl2的熔点为677 ℃,但二者混合后形成的共晶盐熔点仅为340~393 ℃。各种常见盐的熔点和共晶点成分[22]如表2所示。
Composition | Melting point/ eutectic point/℃ | Mole fraction of eutectic point composition/% |
---|---|---|
NaCl | 801 | |
KCl | 772 | |
FeCl2 | 677 | |
FeCl3 | 300 | |
NaCl-FeCl2 | 370-374 | 50 |
NaCl-FeCl3 | 151 | 45.3 |
KCl-FeCl2 | 340-393 | 45.8-91.8 |
KCl-FeCl3 | 202 | 24-47 |
CrCl2 | 845 | |
CrCl3 | 947 | |
NaCl-CrCl2 | 437 | 53.7 |
NaCl-CrCl3 | 544-593 | 68-95 |
KCl-CrCl2 | 462-475 | 36-70 |
KCl-CrCl3 | 700-795 | 54-89 |
Na2CrO4 | 792 | |
K2CrO4 | 980 | |
NaCl-Na2CrO4 | 557 | |
KCl-K2CrO4 | 650 | 68.4 |
Na2Cr2O7 | 356.7 | |
NaCl-Na2Cr2O7(l) | 592 | 30 |
KCl-K2Cr2O7 | 366-398 | 25-27.5 |
1.3.2 S元素引起的腐蚀
通常来说,垃圾焚烧锅炉中S元素会以H2S、SO2/SO3、硫酸盐等多种形式存在,它们在不同环境中可以相互转化,且含Cl物质会影响其腐蚀过程,导致更加复杂的腐蚀行为,因此有必要研究其腐蚀机理。
1) H2S/SO2/SO3
S在不充分燃烧的情况下被还原成H2S,随后侵入氧化膜/金属界面,生成硫化物,并进一步与金属反应[23]。



充分燃烧时,S往往以SO2/SO3的形式存在。在温度较低时,气态SO2/SO3与碱金属氯化物结合生成熔点较高的硫酸盐(见式(30))。与氯盐相比,硫酸盐腐蚀性较弱,附着在氧化膜表面,从而阻碍Cl腐蚀过程,提高材料耐腐蚀性能[24]。然而,当温度进一步升高时,碱金属硫酸盐会与金属表面氧化膜反应,生成碱金属-三硫酸铁等物质(见式(31)),其熔点较低,易形成液相,加速腐蚀发生。


2) 硫酸盐
当温度较低且只存在硫酸盐时,其对氧化膜起到保护作用。相反,当存在氯盐等其他物质时,会加速腐蚀的产生。如图5所示,当只存在硫酸盐时,合金经过长时间腐蚀后,其质量增加较小,这是因为硫酸盐能附着在合金表面氧化膜上,且不与之反应,对氧化膜起到一定保护作用。相反,加入1%NaCl后,合金的腐蚀速率明显提高,且随着NaCl添加量增加,合金质量增加迅速变大,这说明NaCl的添加能够提高硫酸盐的腐蚀性[15]。具体原因有两点:首先,氯化物可以引起合金表面氧化膜的破裂,使得SO2/SO3、Cl2等腐蚀性介质能够快速扩散进入金属/氧化膜界面,进一步腐蚀基体,并造成氧化膜的剥落;其次,氯化物可以与硫酸盐形成低熔点共晶盐,在温度较低时即可形成液相。由于离子在液相中具有较快的迁移速率,故能加速腐蚀的发生。
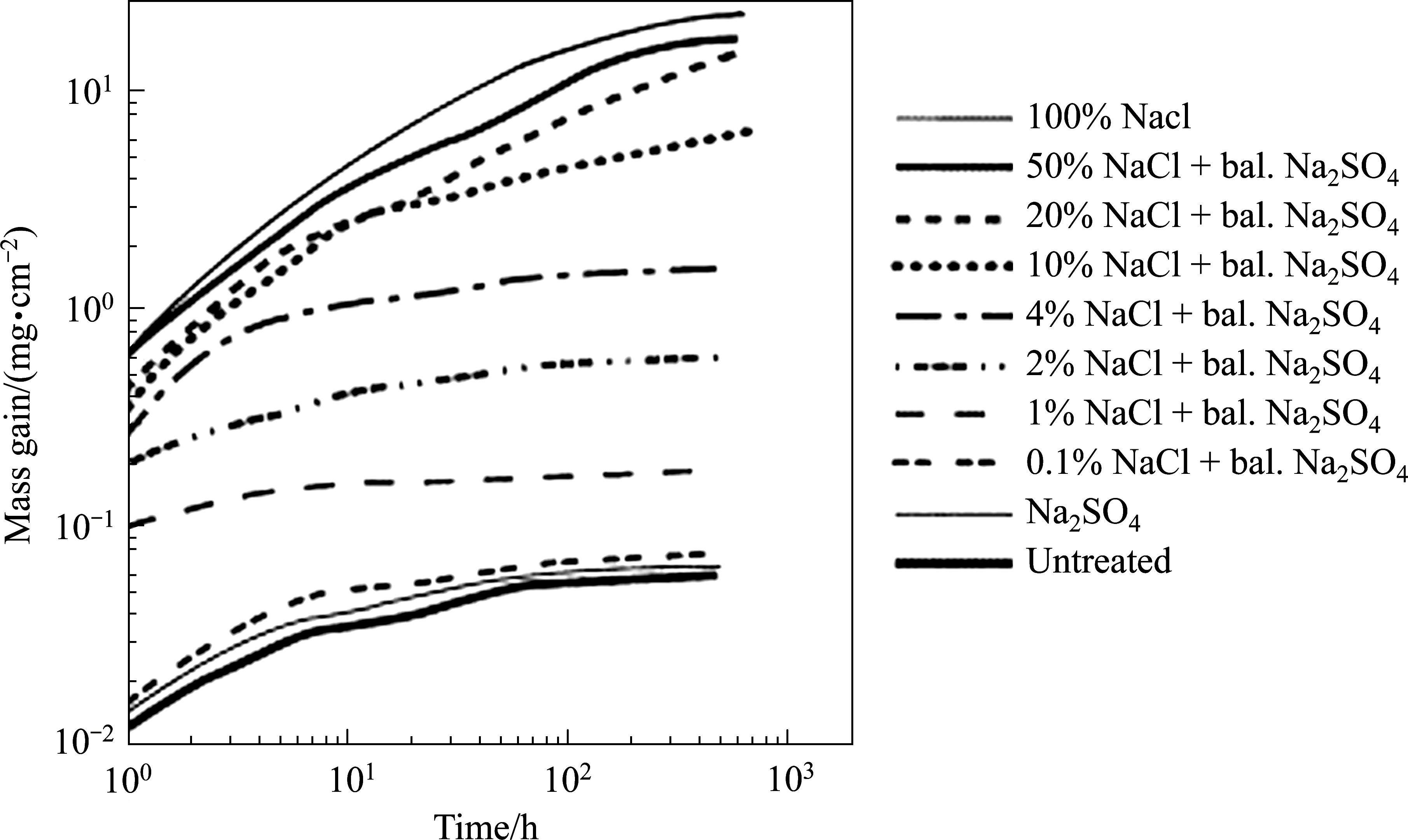
熔融态硫酸盐存在时,其腐蚀机理为酸碱溶解机制[25-26]。熔融硫酸盐中存在大量硫酸根离子,其分解后产生各种腐蚀性介质:


或

由于


当温度较高时,一部分硫酸盐会转化成焦硫酸盐。从表3可以看出,焦硫酸盐熔点较低(Na2S2O7熔点410 ℃,K2S2O7熔点325 ℃),其不仅能直接与金属反应,还能与氧化膜反应生成复合硫酸盐,这是过热器管壁发生腐蚀的主要原因。另一部分硫酸盐会与氧化膜反应,生成复合硫酸盐,其熔点低于550 ℃,易形成液相介质,对锅炉管道造成严重破坏[27-29]。因此,对于高参数垃圾焚烧炉,SO2和SO3对氯腐蚀的阻碍作用并不显著,甚至会加速腐蚀过程。




因此,熔融硫酸盐主要通过两种方式腐蚀金属:一是通过系列分解反应在氧化膜/盐界面产生大量O2-,改变氧化膜氧势,从而加速腐蚀;二是直接或间接与氧化膜发生化学反应,溶解保护性氧化层。
2 腐蚀性能测试方法
通常来说,评价涂层耐腐蚀性能最好的方法是将其置于实际垃圾焚烧环境中进行测试,然而,这是十分困难的。一方面,腐蚀实验周期长达数月数年,其经济成本和时间成本较大;另一方面,锅炉运行过程的不可控因素较多,极易对实验结果产生影响。因此,模拟垃圾焚烧炉内换热面的腐蚀环境,建立更为合适的耐腐蚀性能评价方法是十分有必要的。
2.1 质量变化法
质量变化法是通过测量腐蚀前后样品的质量变化来实现的,其关键在于是否去除样品表面腐蚀产物,若保留腐蚀产物,则为增重法,反之,则为失重法。通常来说,质量变化值越小表示样品耐腐蚀性能越好,但由于清除腐蚀测试后样品表面过量腐蚀介质及腐蚀产物时存在较大误差,如清洗时间过长会造成样品流失、清洗时间过短则无法完全清除腐蚀产物,因此,需要统一腐蚀测试标准,通常应根据不同应用环境设定具体的腐蚀性介质、气氛、温度等参数。对于模拟垃圾焚烧炉环境的腐蚀测试条件,可以参考国际标准ISO 17224: 2015,其规定了金属材料的高温腐蚀试验方法,将盐、灰分和/或其他物质沉积,并将其暴露在受控气体环境中的高温下,以评估其耐腐蚀性。总体来说,质量变化是评价材料耐腐蚀性能最常用和最实用的指标之一。
2.2 灰分沉积法
灰分沉积法是评价防腐涂层性能的一种较为直接的方法,其最初用于测定燃料在高温下的结渣或腐蚀倾向,灰分沉积越少,涂层越不易遭受腐蚀。CHEN等[30]采用该方法在立式积灰炉上比较了两种涂层的阻垢性能,其实验结果如图6所示。对于不同涂层,其灰分积累量存在显著差异,且灰分量越少,涂层寿命越长。
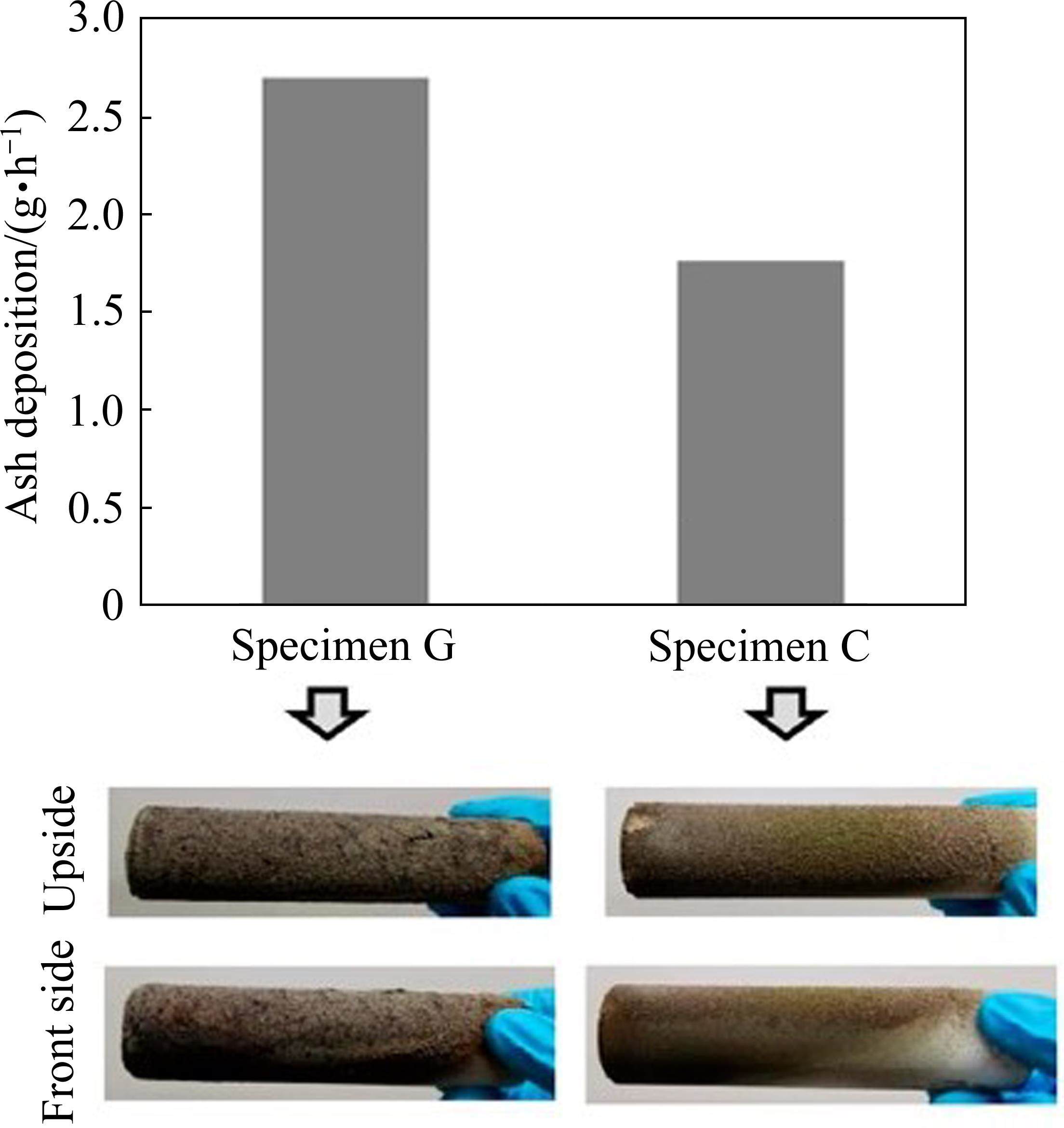
2.3 接触角法
接触角法是通过测量灰分与材料接触角来判断腐蚀倾向的一种方法,且角度越小,灰分润湿性越好,对材料腐蚀倾向越大,其原理如图7所示[31-32]。同时,接触角受其他因素(如传热、粗糙度、灰分粒径)的影响,在实际测试时,需考虑上述因素的限制。
2.4 灰分附着法
灰分附着法是利用拉伸试验机定量测量涂层表面灰垢附着力的一种巧妙方法,其试验系统如图8所示[33]。从图8右侧可以看到,两层涂层之间夹着一层灰烬,三层试样在炉内恒压加热,涂层与灰分完全反应后,上部试样以极小的速度向上移动,直至涂层与灰分分离,此时的最大张力可视为涂层表面的灰分附着力。拉伸力大则表明灰分与涂层结合性强,易发生腐蚀。由于现有仪器的限制,这种方法只能探索熔融灰造成的腐蚀,而不能探索腐蚀性气体的影响。
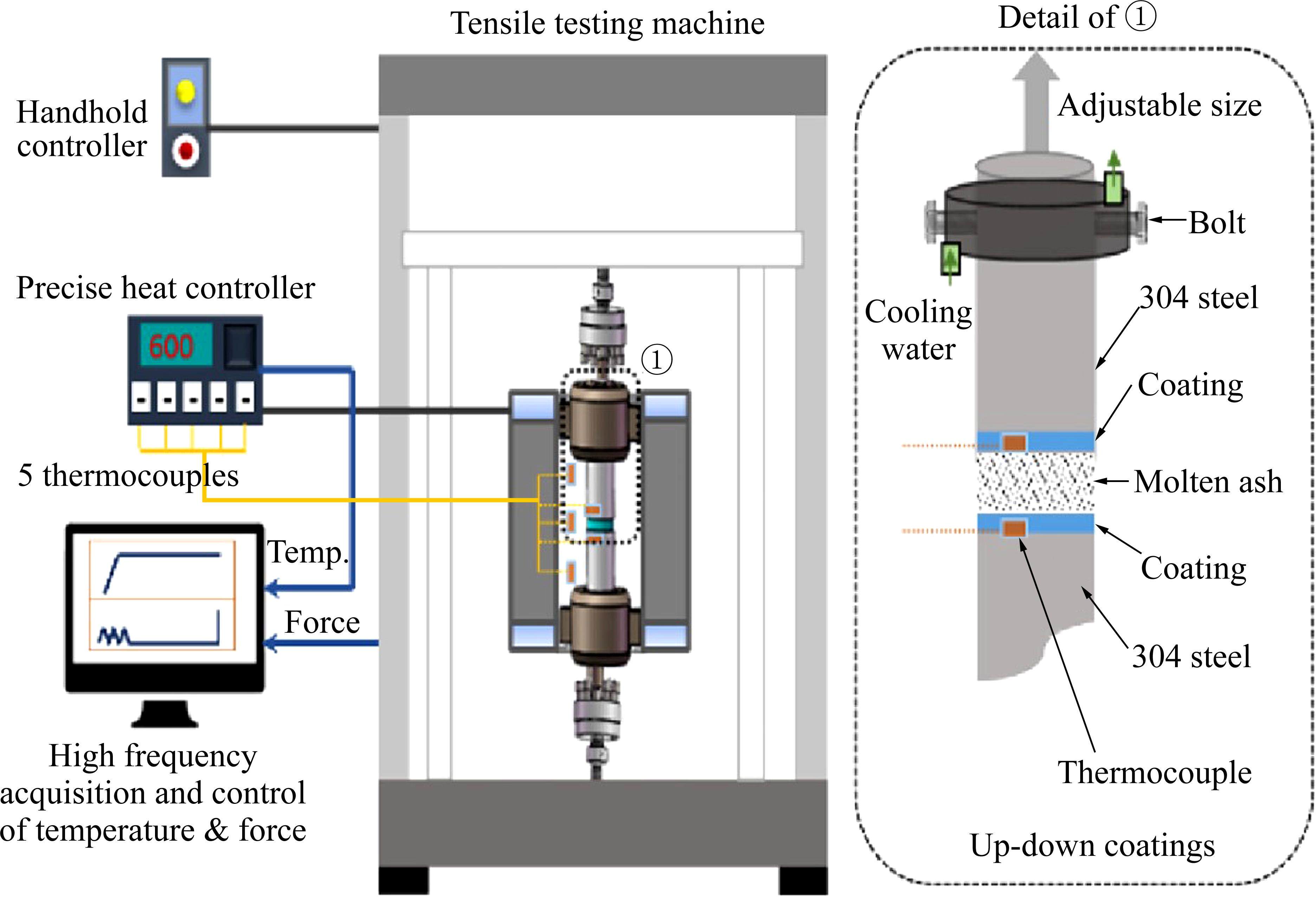
2.5 电化学法
热腐蚀通常被认为是一个电化学过程,并且总是伴随着电子的转移和腐蚀产物的形成。目前,熔盐腐蚀的电化学研究取得了很大的进展,发展了自由腐蚀电位、扫描极化、循环伏安法、恒电位极化、弱极化曲线拟合、线性极化电阻等电化学方法来研究熔盐腐蚀,可有效模拟高温熔盐腐蚀过程,了解腐蚀机制并评估耐蚀性[34-35]。例如,WANG等[36]研究了新型镍基合金Ni16Cr13Co4Mo在NaCl-KCl和NaCl-KCl-Na2SO4熔盐中的电化学行为,采用Mott-Schottky图研究了腐蚀层的半导体性质,并对腐蚀层的化学成分和截面结构进行了表征。结果表明,腐蚀层主要由Cr2O3组成,表现出p型半导体性质;在NaCl-KCl-Na2SO4熔盐中,观察到晶间腐蚀,腐蚀层由Cr2O3外层(p型)和TiO2-Al2O3内层(n型)组成,结果能够为耐腐蚀合金设计提供指导。
3 表面涂层防护
垃圾成分复杂多变,其产生的腐蚀性介质种类多样,且不同金属组成的管道耐腐蚀性和成本各不相同,碳钢的成本最低,但耐高温腐蚀性能较差;镍基高温合金具有较好的耐高温腐蚀性能,但成本远高于碳钢。随着锅炉蒸汽参数的提高,各部位将受到更严重的腐蚀,此时碳钢无法满足严峻的服役要求,将其更换为镍基高温合金虽然可以满足使用要求,但成本将大幅提高。涂层防护是受热面防腐的重要方式,通过在锅炉管道表面覆加较小厚度的涂层,可以大量减少昂贵合金的用量,大幅降低成本。同时,通过调整涂层成分,可实现较高的耐腐蚀性能,而无需改变基体成分,这有助于高参数垃圾焚烧炉的低成本、稳定运行。因此,根据具体使用情况,合理设计涂层成分并选择合适制备工艺是十分必要的。
3.1 制备方法
针对不同腐蚀环境及不同成分的耐腐蚀性涂层,研究者们已经开发出一系列制备方法,如喷涂、堆焊、激光熔覆等[37-41]。不同制备工艺对涂层微观组织特点有重要影响。例如,加工过程中形成的颗粒边界和孔洞等缺陷,会成为腐蚀介质的快速扩散通道,这极大地影响了涂层的耐腐蚀性能。耐腐蚀性能优异的涂层应形成均匀致密的微观组织,且与基体具有较强的结合力,这不仅可以阻碍腐蚀性介质的扩散,还可以促进金属基体表面钝化膜的生成[42-43]。
3.1.1 热喷涂
喷涂是借助热源将涂层和材料加热至熔融或半熔融状态,并由气体携带沉积在基体表面形成覆盖层的一种表面工程技术,如图9所示,其原料可以是线材、棒材或粉末[44-45]。喷涂过程在基体表面形成较浅的热影响区,对基体影响较小;且该过程工艺灵活,可针对不同形状的构件进行加工;喷涂材料类型广泛,可根据不同需求选择合适材料。根据热源与颗粒飞行速度的不同可按图10进行分类[45],其中,大气等离子喷涂(Atmospheric plasma spray, APS)是通过电离产生的等离子体加热粉末颗粒,温度高达10000 ℃,但粒子飞行速度较低,只有200~300 m/s,因此该技术主要用于沉积高熔点材料;超音速氧气/空气燃料喷涂(High velocity oxy/Air fuel spray, HVOF/HVAF)是目前制备涂层的热门技术,其颗粒温度可达到2000~2500 ℃、速度可达750 m/s。这些技术已经得到广泛应用,如FANTOZZI等[46]通过超音速火焰喷涂、冷喷涂和电弧喷涂工艺制备了In625涂层,所有工艺制得的涂层都能有效保护基体不受腐蚀,其中HVOF涂层和电弧喷涂涂层的防护能力最强,HVAF涂层的腐蚀降解程度最高。WANG等[47]通过等离子熔覆(Plasma transferred arc, PTA)、双丝电弧喷涂(Twin wire arc sprayed, TWAS)和HVOF制备了一系列耐腐蚀涂层。采用不同工艺制备的涂层在不同温度下的腐蚀情况各不相同:低温时,TWAS工艺制备涂层有较好的耐腐蚀性能;当温度高于550 ℃时,涂层会发生失效,进而加速腐蚀。在650 ℃时,HVOF涂层的耐腐蚀性能优于PTA涂层。
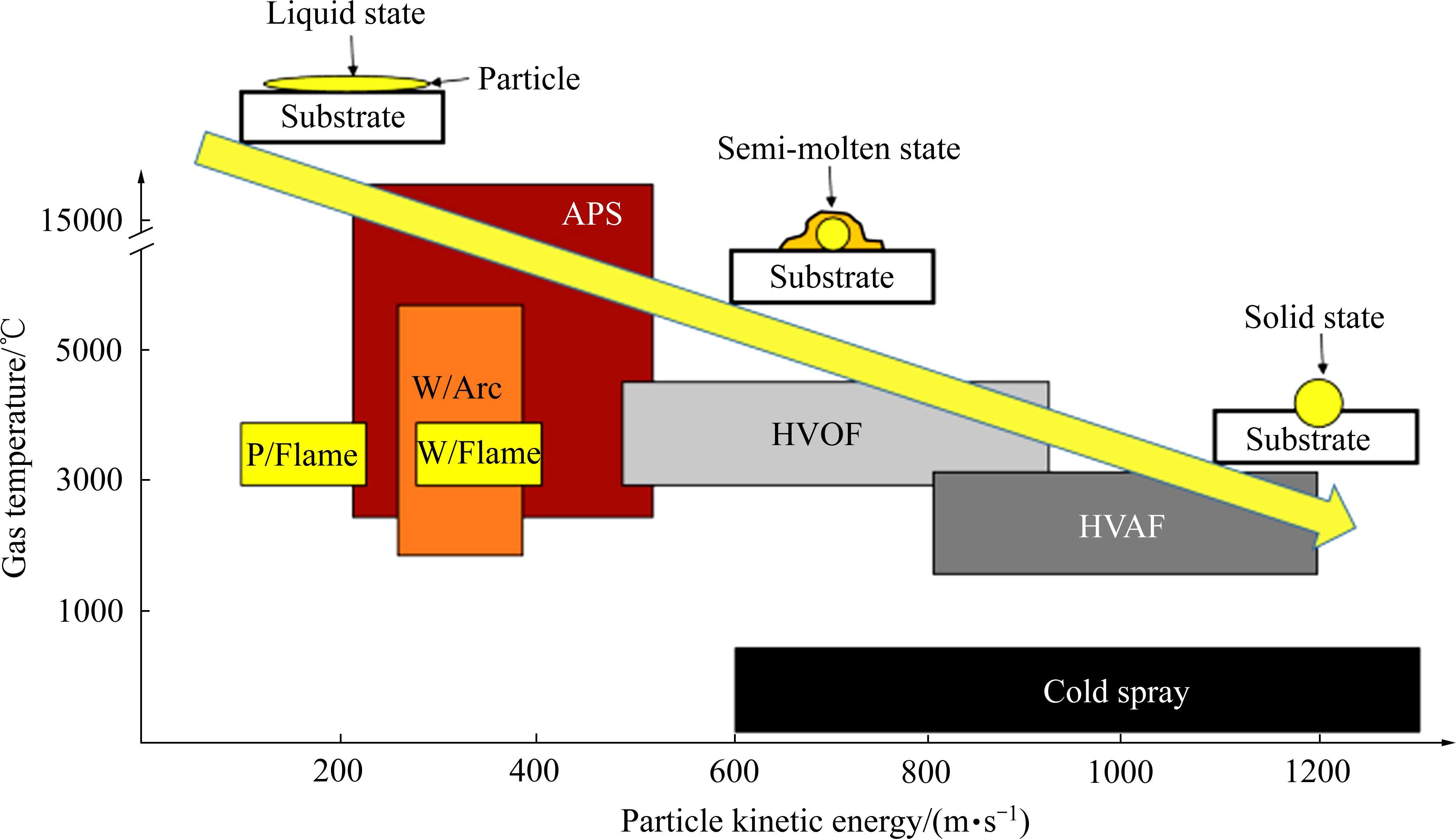
然而,热喷涂制备的涂层不可避免地存在颗粒边界、孔洞、未熔颗粒等缺陷,这些缺陷往往是腐蚀性介质快速扩散的通道,进一步促使腐蚀发生。针对这些缺陷,二次重熔技术可再次熔化部件上的涂层,可有效去除涂层内部的夹渣和气孔,实现涂层和基材的冶金结合,提高涂层结合强度和耐腐蚀性[48]。
3.1.2 堆焊
堆焊是一种低成本、快捷的材料表面改性方法。传统堆焊方法包括焊条电弧焊、埋弧堆焊、气体保护电弧焊。随着焊接技术的不断创新,新的堆焊方法如熔化极惰性气体保护电弧焊(Melt inert-gas welding, MIG)、熔化极活性气体保护电弧焊(Melt active-gas welding, MAG)、非熔化性极惰性气体保护电极焊(Tungsten inert-gas welding, TIG)和冷金属过渡弧焊(Cold metal transfer, CMT)等不断发展,在涂层防护中已得到广泛应用。NAGHIYAN等[49]采用激光熔覆和TIG技术在Inconel 738基体上制备Inconel 625涂层,并在900 ℃下进行热腐蚀试验。两种工艺制备的涂层无裂纹、孔隙等缺陷,均为单相γ-Ni组织,热腐蚀试验后均生成NiO、NiCr2O4和Cr2O3等腐蚀产物。激光熔覆试样中,由NiO和Cr2O3反应形成的耐腐蚀相NiCr2O4含量最高,其耐热腐蚀性明显优于TIG试样和未熔覆试样。与热喷涂相比,堆焊涂层与母材具有更优异的冶金结合,但同时也存在一些问题:在同一区域重复堆焊可能导致涂层脆化并萌生裂纹,且堆焊过程中基体元素如Fe等容易扩散进入涂层,导致堆焊层合金元素受到稀释,从而改变涂层性能;此外,堆焊层表面粗糙且不均匀,容易黏附炉渣加速腐蚀或产生较薄涂层区域,聚集热流。因此,堆焊层厚度一般在2~3 mm,以降低其导热能力,从而使热量流入锅炉其他部位[45]。
3.1.3 激光熔覆
激光熔覆(Laser cladding, LC)是通过在基材表面添加熔覆材料,并利用高能量密度的激光束使材料与基材表面薄层形成冶金结合的方法。激光束可以聚焦到极小区域,形成很小的热影响区,因此其制备出的涂层具有较低的稀释率,在锅炉管道防护中具有独特优势,并已得到广泛应用。例如,FANTINI[50]在意大利和欧洲的多家垃圾焚烧炉工厂开展了大量现场实验,他通过激光熔覆工艺制得初始厚度约为1 mm的In625涂层,在MSB和GKS过热器中分别运行15560 h和11650 h后(腐蚀温度分别为420 ℃和435 ℃),其年平均腐蚀量分别为0.15 mm和0.18 mm。结果表明,激光熔覆In625涂层具有优异的防护作用。此外,由于激光熔覆过程中热量的快速变化,涂层组织晶粒较细,可以起到一定细晶强化的效果,达到增强涂层力学性能的目的;但较快的冷却速率会造成严重的元素偏析,导致涂层无法形成均匀的保护性氧化膜。
3.2 涂层成分设计
为实现较好的耐腐蚀性能,涂层中通常需要添加多种合金元素,如Al、Cr、Si等。在不同腐蚀条件下,涂层成分设计原理也各不相同。因此,充分了解各种合金元素的行为及设计原则是相当重要的[51-52]。
3.2.1 各元素作用
目前,高温腐蚀防护涂层主要包括Fe基、Co基、Ni基高温合金涂层。Fe、Co、Ni三种元素在元素周期表中相邻,同为第Ⅷ族元素,物理和化学性质相近。Fe、Co、Ni的熔点分别为1538 ℃、1495 ℃和1453 ℃,以这三种元素为主要成分的涂层可以在高温下应用。其中,Ni基高温合金涂层占比最大,与不锈钢成分接近的Fe基涂层也有一定应用,Ni基涂层耐腐蚀性能普遍优于Fe基涂层。除基体元素外,涂层中还会加入其他合金元素。这些合金元素不仅影响表面保护性氧化层的形成,而且影响合金内部发生选择性腐蚀的程度,因此,了解不同合金元素的作用有助于设计新型耐高温腐蚀合金。
1) Ni元素
Ni金属是面心立方结构,组织和化学性质稳定,随着温度变化,Ni不发生同素异构转变。Ni只存在一种氧化物NiO,且其氧化速率远低于Fe的氧化速率。Ni具有较强的合金化能力,添加到十几种元素中也不会产生有害相。通过与其他元素的混合可以得到适用于不同服役条件的耐高温、耐腐蚀合金[53]。
2) Cr元素
Cr的氧化物Cr2O3具有六方刚玉结构,在O-Cl环境中具有极高的稳定性[46],广泛应用于高温环境(低于850 ℃)下的腐蚀防护。Cr在氧化气氛中可形成具有保护性的Cr2O3氧化膜,其腐蚀性介质如Cl2等在Cr2O3中的扩散速率很低,因此Cr的氧化膜具有保护作用[12, 54]。WANG等[47]通过HVOF制备了一系列NiCr涂层,随着Cr含量(质量分数)从7.72%增加到21.55%、Ni/Cr比从10.02降低到3.03,涂层质量变化呈直线下降趋势,说明其耐腐蚀性能得到显著提高。但添加过量的Cr元素反而容易造成选择性氧化现象的发生,进一步扩大内腐蚀区[55]。
3) Mo元素
Mo是耐高温腐蚀涂层中的常见元素。一方面,由于Mo的原子半径大,容易引发晶格畸变,阻碍位错移动,在涂层中起到强化作用,阻碍腐蚀性介质扩散[55];另一方面,Mo能在表面形成致密的MoO2膜,且Mo可以提高其他氧化膜稳定性,减缓腐蚀速率[53, 55-56]。SADEGHIMERESHT等[57]通过HVAF工艺制备了NiCrMo涂层,并对其在KCl和HCl环境下的腐蚀行为进行研究。结果表明,制得涂层具有优异的耐腐蚀性能,Mo在涂层中促进了富Cr保护性氧化膜的形成。Mo对耐腐蚀性的贡献取决于它的含量和分布,并不是越多越好。WANG等[55]通过激光熔覆技术在钢材表面使用合金化粉末制备了组织均匀且与基体实现冶金结合的NiCrMo及NiCr系熔覆层。在NiMo熔覆层中,随着Mo含量的增加,涂层表面裂纹数量和孔隙率增加,使合金耐蚀性降低。激光熔覆技术热传递量较大,容易造成Mo元素偏析,腐蚀后富Mo氧化物仍保持枝晶骨架,形成不连续富Mo层,无法阻止Cl2向内渗透,因此需合理设计涂层中Mo元素的含量。
4) Al元素
与Cr类似,Al同样在耐高温腐蚀涂层中得到了广泛应用,其在高温下形成热力学稳定的六方刚玉型氧化物(α-Al2O3)。该氧化物生长速率较慢,具有优异的保护性能。Al的氧化物还有θ-Al2O3、γ-Al2O3和δ-Al2O3几种形式,它们均不如α-Al2O3稳定,但α-Al2O3一般在较高温度下形成。因此,含Al涂层一般会经过预氧化处理,预氧化后形成的α-Al2O3涂层具有更优异的耐腐蚀性能[58]。Al2O3不容易被碱氯化物破坏,因为Cl-在Al2O3中的扩散激活能大约是在Cr2O3中所需扩散激活能的两倍,能够有效阻碍Cl-向内扩散[59-60]。ISRAELSSON等[61]研究发现,只有Al2O3膜形成的涂层中存在裂纹等缺陷时,Cl-/Cl2才能发生扩散并引起腐蚀。但是,只有单一的Al2O3涂层存在时,则无法抵抗氯盐和硫酸盐的腐蚀,其容易遭受碱性熔融机制的破坏。值得注意的是,Al添加量过高时,会降低涂层的力学性能及加工性。
5) Si元素
向合金或涂层中加入适量的Si,可以在保证力学性能的同时提高合金或涂层的热稳定性和抗氧化性[62]。Si的氧化物SiO2是一种酸性氧化物,如式(41)所示。SiO2难与硫酸盐反应,在熔融盐中的溶解度非常低,能有效阻碍S、O元素的扩散,进而抵御硫酸盐热腐蚀[63]。此外,Si容易在晶界处富集,可有效阻止腐蚀介质向内渗透[64]。已有大量研究表明,向涂层中添加Si元素能提高其耐高温腐蚀性能。HE等[65]研究发现,Si可以促进其他保护性氧化膜如Al2O3、Cr2O3的形成[66],从而提高涂层防护性能。刘功起等[67]制备了一系列含Si的铁基涂层,并在600 ℃下进行腐蚀性能测试。结果表明,含Si涂层耐蚀性能远高于不含Si涂层,主要原因是SiO2会在涂层中的孔隙和微裂纹处产生沉淀,进而实现封孔作用。LI等[13]研究了Al和Si元素对Fe-Cr合金在650 ℃时的KCl中腐蚀行为的影响,发现添加Si元素后的Fe-Cr合金内部形成了稳定致密的氧化层,抑制铁氧化物的生长,在KCl盐作用下具有较好的耐腐蚀性。

6) 其他元素
除上述元素外,Ni基高温合金涂层中还可以加入其他元素,如Nb、Cu、W、B等,它们通过一系列强化作用,提高涂层力学性能及耐腐蚀性能。Nb被氧化后形成的短棒状NbO2能提高NiO层的力学性能,从而抑制裂纹形成[55];Cu可以提高涂层在还原性介质中的耐腐蚀性能[68];WC等碳化物的加入可以提高涂层的耐磨蚀性能,如WC-Ni、Cr3C2-NiCr等[69-72]涂层已得到广泛应用;B可以细化晶粒,使得涂层结构更加致密,从而抵抗腐蚀性物质的渗透[73]。
3.2.2 设计原则
耐腐蚀涂层的成分设计应考虑其高温结构稳定性、高温强度、热加工性和可焊接性。为实现有效的腐蚀防护作用,垃圾焚烧锅炉受热面涂层应与基体形成较强的冶金结合,防止涂层快速剥落。同时,涂层与基体材料的热膨胀系数应保持相似,以防止热应力裂纹等缺陷的产生。此外,为实现耐热腐蚀性,涂层表面应形成一层连续完整的保护性氧化膜,以阻碍腐蚀性介质的扩散。对纯金属来说,其高温氧化原则如下:对于纯金属M,其与O2或其他气体在高温下反应并生成表面氧化物,要经历形核和长大的过程,最终形成连续的保护性氧化膜,阻止基体金属与氧化环境接触[74]。不同金属和氧化物的稳定性可通过氧势图比较,图中位置较低的金属更容易被氧化,且在不同温度下,金属氧化所需氧分压也可通过氧势图得出。为实现有效防护,保护性氧化膜应具备以下特点:1) 氧化膜生成速率较低;2) 氧化膜附着性强;3) 较低的氧化物蒸气压以减少蒸发;4) 生成氧化膜的热膨胀系数与金属接近;5) 氧化膜具有一定的高温塑性,以适应氧化物和金属在比热容和热膨胀系数上的差异;6) 氧化膜应具备较低的电导率和较低的金属离子、O2扩散系数。
此外,应力状态也对氧化膜的保护性有重要影响,PILLING和BEDWORTH提出通过金属氧化物体积与金属体积比(简称PB比)来判断生成的氧化膜是否具有保护性的观点[75]。通常来说。压应力状态下的氧化膜保护性高于拉应力状态下的氧化膜,如果生长出的氧化膜比容高于金属的比容(即PB比>1),则其内部应力状态为压应力,具有较强保护性。但仅根据PB比来判断氧化膜是否具有保护性是不准确的,有些保护性氧化膜在PB比小于1时也具有保护性[74]。
设计耐腐蚀涂层成分时,往往需要先根据热力学判断氧化物及腐蚀产物是否能够稳定存在,如图11所示,可通过优势区图判断不同氧、氯分压下腐蚀产物的类型,Thermo-Calc、HSC Chemistry和FactSage等软件都可以为判断合金腐蚀产物提供帮助[76]。这里以含Cl高温腐蚀环境为例,阐述合金内不同元素与腐蚀介质的反应过程。常见的耐高温腐蚀涂层中主要含有Fe、Cr、Ni等元素。假设涂层表面已形成一层保护性氧化膜,Cl通过表面氧化膜中的缺陷向涂层/氧化膜界面扩散。结合图11可知,当O分压较低、Cl分压较高时,容易生成碱金属氯化物[12],其发生的反应如下:



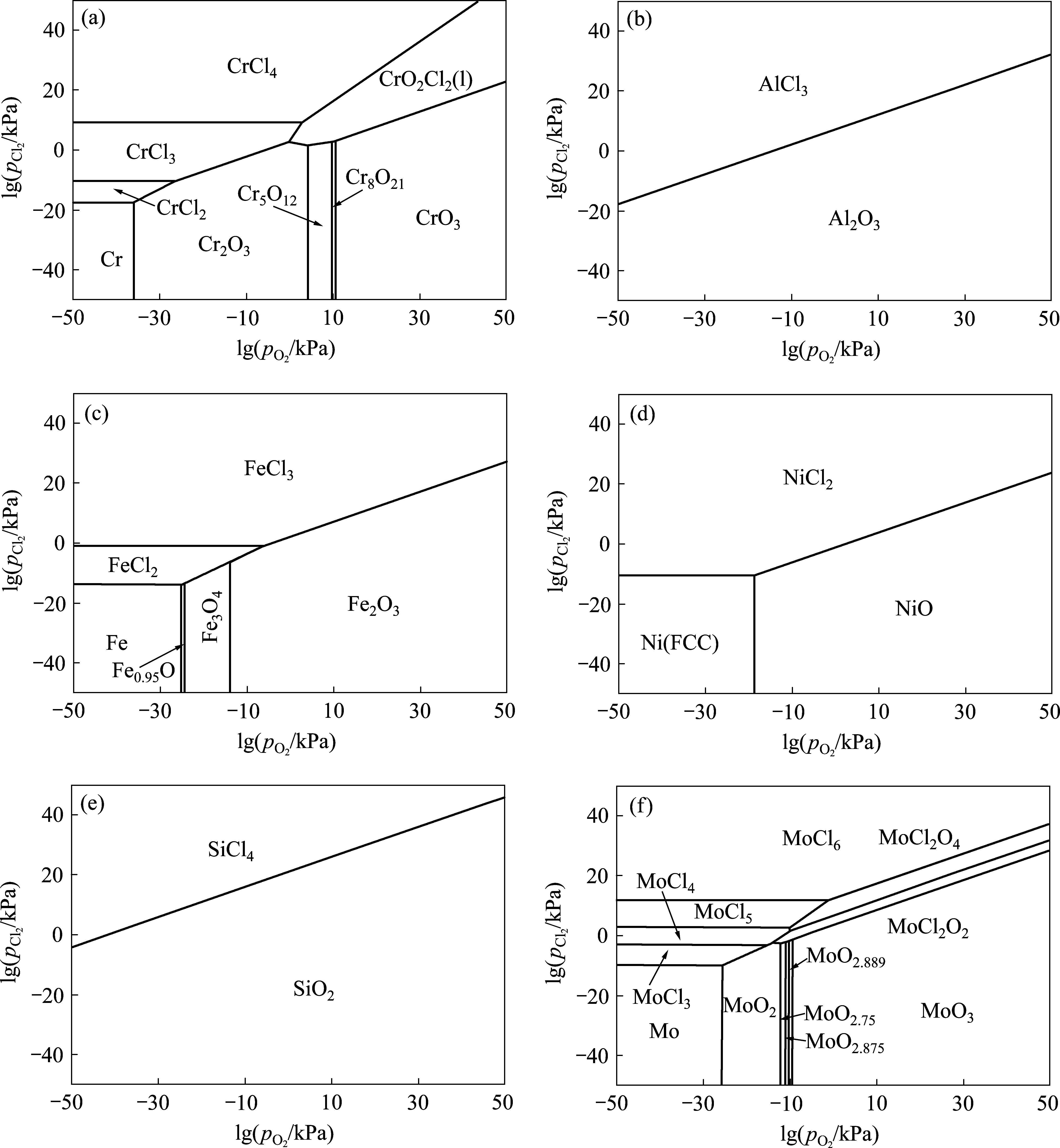
不同氯化物生成的吉布斯自由能不同,在600 ℃时,生成顺序为CrCl2>FeCl2>NiCl2。随后,固态氯化物通过涂层中的缺陷向外挥发,不同氯化物的平衡蒸气压与温度的关系如图12(a)所示,其氯化物挥发性从大到小依次为FeCl2>NiCl2>CrCl3>CrCl2[77-80]。在氧化膜表面,气态金属氯化物与O2反应生成多孔、无保护性的氧化膜和Cl2。由图12(b)可知,Cr的氯化物CrCl2/CrCl3转变成氧化物所需的氧分压远低于FeCl2/NiCl2所需的氧分压,从而优先形成Cr2O3,即在FeCrNi合金中往往会发生Cr的选择性氧化。因此,需要保证Cr含量以形成完整连续的保护性氧化膜。最终,在FeNiCr合金中会形成外层为富Ni、Fe氧化膜,内层为富Cr氧化膜的多层结构[77]。





因此,开发耐腐蚀涂层的关键是在涂层表面形成致密的氧化膜,以阻碍金属和腐蚀性介质的扩散。然而,由于高温腐蚀是非平衡过程,可能形成一系列亚稳相,且新腐蚀产物的形成会改变其附近的氧、氯分压,同时,合金成分在氧化及腐蚀过程中由于选择性氧化也会发生一定改变,因此根据热力学平衡状态计算得到的相组成往往与实际有较大偏差。热力学软件往往只能作为一种辅助工具,需要分析腐蚀后的成分与组织才能确定具体的腐蚀行为。综上所述,耐高温腐蚀涂层表面应形成具有致密且连续的保护性氧化层,以阻碍腐蚀介质与基体的接触;从热力学、动力学角度考虑,各种元素形成氧化层的倾向、氧化层与腐蚀介质反应难易程度、各种元素形成氧化层的速率,以及氧化层与腐蚀介质反应快慢是衡量涂层耐腐蚀性能的关键因素,需结合实际腐蚀环境,合理设计涂层成分。
3.3 垃圾焚烧炉用涂层材料体系
对于耐腐蚀涂层的组分,研究的大方向较为明确,主要是含Ni、Cr、Al元素的涂层,其在高温氧化环境下生成的氧化层含有大量NiO、Cr2O3、Al2O3,涂层表面氧化膜致密稳定,能够阻挡腐蚀介质的进一步渗透。因此,含Ni、Cr、Al等元素的涂层的耐腐蚀性能较好,与之相关的研究及应用也较多。
3.3.1 NiAl系涂层
NiAl涂层能有效减轻Cl元素的腐蚀,SADEGHIMERESHT等[81]通过HVAF制备了Ni21Cr、Ni5Al涂层,并研究其在KCl作用下的腐蚀行为。结果表明,无KCl存在时,两种涂层均具有良好性能;有KCl存在时,NiCr涂层被明显破坏,而NiAl涂层形成的保护性Al2O3氧化膜能够阻碍Cl-和Cl向内扩散,其耐腐蚀性能更好。值得注意的是,当腐蚀性介质中含有S元素时,Al2O3并不能提供比Cr2O3更好的防护效果。JAFARI等[82]通过HVAF工艺制备了Ni21Cr、Ni5Al涂层,研究其在KCl和KCl-K2SO4共同作用下的腐蚀行为。Cr2O3形成的Ni21Cr涂层在KCl中受活化氧化腐蚀机制控制,易受腐蚀破坏。而由于K2SO4不易与保护性含Cr氧化膜反应,故KCl-K2SO4混合盐的腐蚀性较弱。Al2O3形成的Ni5Al涂层在KCl中表现出更好的耐腐蚀性,但在混合盐作用下,其部分区域易发生选择性硫化作用,故其耐腐蚀性不如Ni21Cr涂层。
3.3.2 NiCr系涂层
NiCr系涂层以Ni、Cr元素为主,添加Mo、Nb等合金元素后,在多种元素的共同作用下能有效减轻Cl、S等元素的腐蚀。张秀菊[53]通过HVOF制备了一系列新型Ni基涂层,在相同的腐蚀环境中,Ni基涂层的腐蚀增重量仅为锅炉钢12Cr1MoV的10%~20%。在400~600 ℃时,温度每升高100 ℃,12Cr1MoV的腐蚀增重量就提高10倍左右,而在600 ℃时Ni基涂层的腐蚀增重量仅为锅炉钢的10%~20%,故该涂层适用于高参数化后的垃圾焚烧炉。Ni基涂层在腐蚀过程中生成了从外向内分布的分层Ni、Mo和Cr氧化物,可以阻止熔融盐等腐蚀介质向内扩散,使得Ni基涂层的损耗减薄量仅为锅炉钢的1/10。此外,他们还将涂层元素划分为主要元素(Ni/Fe/Co)、次要元素Cr和其他元素(Si、B、Mo、W等)三类,发现三类元素质量比为6∶2∶2时,涂层在实际腐蚀环境中的耐腐蚀性能最佳[33, 53]。
在NiCr系涂层中,Inconel 625涂层得到广泛应用,其主要包含Ni、Cr、Mo、Nb、Fe等元素,Ni含量约为60%(质量分数),Cr含量约为20%(质量分数),Mo和Nb等其他元素的含量之和约为20%(质量分数),与张秀菊[53]的研究结果相吻合。涂层在高温下可形成致密的Cr2O3氧化膜,具有优异的腐蚀介质屏蔽作用。同时,Ni元素具有良好的延展性,涂层与锅炉管壁有着几乎相同的热膨胀系数,可以避免由于热应力引起的涂层开裂和剥落现象;Mo、Nb等元素使涂层具备抗点腐蚀能力。WANG等[55]通过激光熔覆技术制备了一系列Inconel 625和其他成分的涂层。结果表明,Inconel 625涂层的耐高温腐蚀性能最好,其次是Hastelloy C22、Ni80Cr20涂层,而Ni60Cr40最易受到腐蚀破坏。总体来说,Inconel 625涂层具有出色的耐腐蚀性能,在实际垃圾焚烧锅炉中已得到广泛应用。
KAWAHARA等[83]通过在垃圾焚烧炉中进行实验,研究了合金中Cr、Ni、Mo的含量与最大腐蚀厚度之间的关系,其合金成分如表4所示。结果表明,在550 ℃下,随着Cr+Ni+Mo含量的增加,合金最大腐蚀厚度损失降低,耐腐蚀性能增加,JHN24合金与625堆焊层的耐腐蚀性能最好。特种金属公司在Inconel合金基础上,通过调整Mo等元素的含量,开发了一系列耐腐蚀性能更好的Hastelloy合金。如C-276合金,它属于Ni-Mo-Cr-Fe-W系合金,是现代金属材料中最耐蚀的一种,主要耐湿氯、各种氧化性氯化物、氯化盐溶液、硫酸与氧化性盐腐蚀,在低温与中温盐酸中均有很好的耐腐蚀性能,但C-276合金中没有足够的Cr来抵抗强氧化性环境的腐蚀。VIKLUND等[84]将一些常用的过热器材料暴露在内部具有冷却装置的探头上,并将其放置在垃圾焚烧炉的过热器附近,以测试这些材料的耐热腐蚀性能。该实验的腐蚀温度控制在440 ℃,所研究的材料包括铁素体钢13CrMo44、铁素体-马氏体钢HCM12A、奥氏体不锈钢Super 304、317L和Sanicro 28,以及镍基合金Hastelloy C-2000和Inconel 625。通过比较腐蚀速率和腐蚀类型可知,三种低合金材料(13CrMo44、HCM12A 和Super 304)和四种高合金材料(317L、Sanicro 28、Hastelloy C-2000、Inconel 625)之间有明显的区别:低合金材料的腐蚀表现为快速且相对均匀的腐蚀。这表明略微低合金材料并不能起到有效防护效果,这三种合金都形成了保护性较差的金属氯化物/氧化物层。在合金化程度较高的材料上形成的氧化层具有更好的保护性能,金属氯化物的形成被Ni和Mo以及足够高的Cr含量所抑制,合金表面能够形成富Cr的氧化膜。
Material | Composition | w(Cr+Ni+Mo)/% |
---|---|---|
SA213-T22 | 2.25%Cr-1%Mo | 3.16 |
TP347H | 18%Cr-12%Ni-Nb | 30.2 |
310HCbN | 25%Cr-20%Ni-Nb | 45 |
Alloy 625 | 21%Cr-9%Mo-4%Nb-62%Ni | 93.9 |
HR11N | 30%Cr-40%Ni-1%Mo-N | 69.9 |
Hastelloy C22 | 21%Cr-13%Mo-59%Ni-W-Fe | 91.9 |
HR30M | 30%Cr-28%Ni-1%Mo-N | 59.5 |
JHN24 | 20%Cr-18%Mo-58%Ni-Nb | 96.5 |
625M (Weld overlay) | 21%Cr-9%Mo-625Ni | 94 |
C-276M (Weld overlay) | 20%Cr-13%Mo-W, Co, Fe-57%Ni | 89.1 |
ALBINA[85]总结了不同腐蚀环境下(见图13)水冷壁及过热器使用的耐腐蚀合金成分,其结果如表5所示。对于过热器合金的选择,针对高Cl环境,可以选择Inconel 625和825合金,但其无法抵抗高S环境的腐蚀,此时可以提高合金中Cr含量。对于水冷壁合金的选择,其表面金属温度较低,高NiCr合金钢即可满足高Cl环境的使用要求,同样地,其无法抵抗硫酸盐沉积物的腐蚀,可选择添加大量Cr的高合金钢(如FeCr合金);当处于高Cl、S环境中时,可以选择高Ni-Cr-Mo含量的合金。
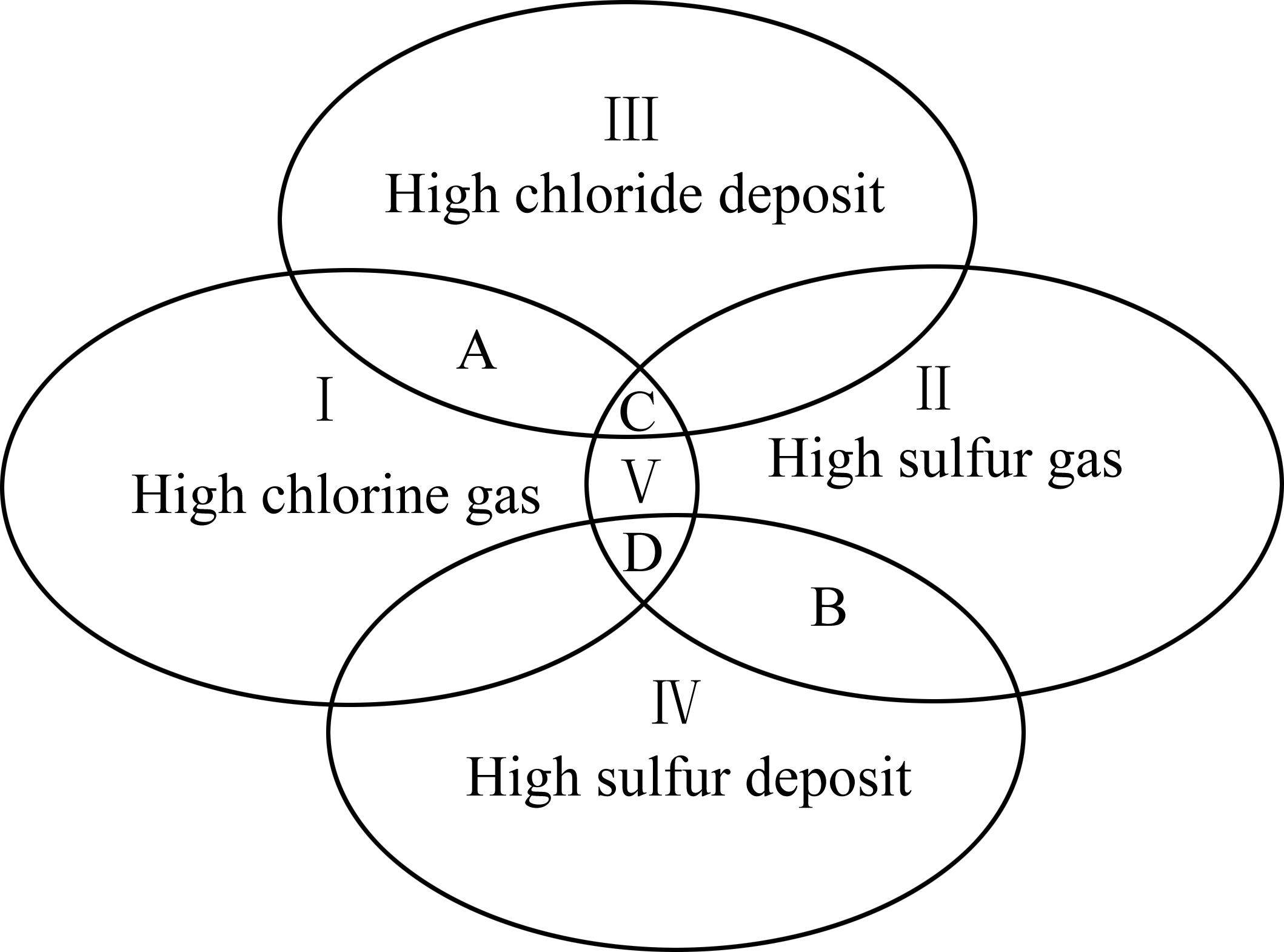
Parts | Regions | Suggested alloy combinations |
---|---|---|
Waterwall | Ⅰ | Ni-alloyed steels |
A | Ni-alloyed metal Ni-based overlay | |
Ⅱ | Cr-rich alloy steels | |
B | Cr-rich alloy steels | |
Ⅲ | Ni-based alloys | |
Ⅳ | Cr-based alloys | |
Ⅴ | High (Ni, Cr) steels | |
C | High (Ni, Cr, Mo) steels | |
D | High Cr steels with Ni-based overlay | |
Superheater | Ⅰ | Ni-based alloys |
A | Ni-based alloys | |
Ⅱ | Cr-based alloys | |
B | Cr-based alloys | |
Ⅲ | Ni-based alloys | |
Ⅳ | Cr-based alloys | |
Ⅴ | High (Ni, Cr) steels | |
C | High (Ni, Cr, Mo) alloys | |
D | High (Ni, Cr, Mo) alloys |
因此,为设计应用于实际垃圾焚烧环境的涂层,首先,应该确定炉内腐蚀环境,了解各种常见沉积物及气氛的组成;其次,应该确定锅炉运行过程中水冷壁及过热器管道金属的使用温度。通常来说,虽然Ni基合金耐腐蚀性能更好,但其成本较Fe基合金更高,应根据需求灵活调整合金成分。
4 总结与展望
本文针对垃圾焚烧锅炉中的耐腐蚀涂层,总结了常见腐蚀性元素对垃圾焚烧锅炉的腐蚀机理、常见的腐蚀性能测试方法、涂层制备及成分设计方法等。垃圾焚烧过程中会释放大量腐蚀性气体及飞灰颗粒,并在锅炉受热面管壁处沉积形成具有强腐蚀性的物质,它们单独或协同与金属发生腐蚀作用。腐蚀性物质中通常含有Cl、S等元素,其中含Cl物质的腐蚀性最强,可直接通过活化氧化作用腐蚀合金;含S物质有H2S、SO2/SO3、硫酸盐等,当温度较低、环境中只存在SO2/SO3时,会生成高熔点、低腐蚀性的硫酸盐,其会附着于氧化膜表面,阻碍腐蚀性元素的进入,起到一定的提高耐腐蚀性的作用,但温度升高时,硫酸盐会转变成腐蚀性更强的焦硫酸盐和复合硫酸盐。多种不同种类的盐混合后会形成低熔点共晶盐,当温度较低时,可在合金表面形成熔融盐,通过电化学机制快速破坏合金表面的氧化膜,最终造成材料的失效。总体来说,腐蚀主要分为两个阶段:1) NaCl、KCl等挥发性气态碱金属氯化物的释放,破坏金属表面形成的保护性氧化膜;2) 腐蚀性介质通过氧化膜与金属反应,生成疏松多孔、无保护性的氧化物,造成管壁减薄损失,最终导致腐蚀穿孔等现象的发生,引发爆管等严重事故。因此,需要采取适当的防护措施,以减轻或消除垃圾焚烧锅炉受热面所受到的腐蚀伤害。
常见的涂层制备方法有喷涂、堆焊和激光熔覆等,不同工艺制得的涂层具有不同特点。同时,由于缺乏细致、系统的研究,一些强化元素的作用规律、机理仍不清楚,如何调整涂层成分以提升其耐腐性能仍然缺乏具体的方向。此外,虽然文献研究中的耐腐蚀涂层的类型十分丰富,但实际应用的涂层类型仍较少,造成研究与应用脱节的原因在于,种类繁多的涂层从实验室走向实际应用必须与实际环境(腐蚀物质、壁面温度)接轨,这一过程需要大量时间与成本[73]。实验室中的腐蚀性能测试方法有增重/失重法、灰分沉积法、接触角、灰分附着法和电化学法,但实验室环境与实际垃圾焚烧环境相差甚远,因此需要根据材料的实际服役情况,综合力学性能、热导率、耐腐蚀性、最大服役温度、成本等多方面因素进行考量[86]。
未来的研究应从以下方面着手:
1) 充分了解不同垃圾焚烧时产生的腐蚀性介质种类及含量,以便针对具体腐蚀性介质选取合适防腐措施。
2) 深刻理解不同腐蚀介质的腐蚀机理。目前,对于含Cl介质的腐蚀,人们普遍认可活化氧化机制,但其也存在一定缺陷,如Cl2(g)与FeCl2(g)通过氧化膜/基体界面扩散的过程仍未得到解释,若Cl2是通过穿越氧化膜中的裂纹等细小缺陷渗透,那理论上O2也可以随时渗透并重新形成保护性氧化膜,使活化氧化反应无法进一步发生。对于此,目前学术界主要有两种观点[87]:一是Cl改变了氧化膜的结构,提高Cl的扩散系数;二是Cl先诱导发生局部腐蚀,并优先通过这些坑向内渗透,与金属反应后形成挥发性的氯化物向外逸出,但其具体扩散过程仍不清楚。
3) 深入理解不同金属元素的防护机理,结合高通量试验等方法快速开发低成本、高性能的新型耐腐蚀涂层。目前,新材料开发通常采取试错法,即结合实际经验,在一定范围内通过调整合金组元及成分,进行大量试验后确定最佳成分。这种方法的缺点在于成分设计范围巨大,而每次试验只能进行单一成分材料的制备、加工及表征测试,需要耗费大量时间及成本。为加速耐腐蚀合金的开发,并理解其腐蚀机制,可以结合高通量试验及建模方法,从而实现材料的快速设计。例如,WANG等[88]提出一种综合高通量合成、腐蚀测试、自动表征和机器学习的方法,并对一系列Cr-Fe-Mn-Ni合金在熔盐中的耐腐蚀性能进行了评估。结果表明,耐腐蚀合金的开发速率可以提高2到3个数量级。
4) 提出实验室条件下涂层腐蚀性能的快速评估方法,通过在实验室中模拟垃圾焚烧环境,快速准确地模拟涂层的实际服役性能。
彭嘉懿, 李开洋, 谭黎明, 等. 垃圾焚烧炉受热面腐蚀防护涂层研究进展[J]. 中国有色金属学报, 2025, 35(1): 57-77. DOI: 10.11817/j.ysxb.1004.0609.2024-44887
PENG Jiayi, LI Kaiyang, TAN Liming, et al. Research progress of corrosion protection coatings on heat surface of waste incinerator[J]. The Chinese Journal of Nonferrous Metals, 2025, 35(1): 57-77. DOI: 10.11817/j.ysxb.1004.0609.2024-44887