Al-Mg-Si系铝合金具有优异的导电性和高的比强度,可用于导体材料,在汽车电池汇流排、架空导线等领域具有广阔的应用前景,典型牌号有6101和6201[1-2]。由于导电和力学强化机制差异,两者常表现为背反关系,实现导电和力学性能的同步改善和提升一直是本领域研究者关注的目标[3-4]。
Mg-Si含量是影响该合金系导电和力学性能的重要因素,适量过剩Si可加速时效进程,获得较高电导率,若过剩Mg则会导致强化效应减弱,电导率也会下降[5-7]。杨昭等[5-6]和KHANGHOLI等[7]证实Mg、Si质量比为1.1∶1较为适宜,DONG等[8]优化获得Mg、Si摩尔比在1.18∶1时,合金的导电和力学综合性能更为优异。微合金化也是克服铝合金导电与力学背反关系的有效途径,La、Sr和Zr等均被证实可加速时效进程,促进元素脱溶,时效相更加细化,分布更为弥散,La和Sr不仅改善导电,还可以提升力学性能,而Zr在改善强度的同时略微降低导电性[9-11]。
形变热处理被证实在克服导电与力学背反方面具有显著效果。陈江华等[12-13]将传统固溶+时效工艺改进为“固溶+预时效+冷轧变形+终时效”,该形变时效工艺可提升力学的同时显著改善其导电性。进一步地,LENTZ等[14]对双辊铸轧6101合金进行形变时效工艺处理,合金表现出优异的导电性和很高的力学性能,SUNDE等[15]发现6101合金经预时效后进行50%轧制,再经仅2 h时效后合金的电导率比传统工艺提升2%IACS ~3%IACS。KHANGHOLI等[16]指出充分利用形变位错协同Sr、Bi微合化调控时效相的析出进程,是实现铝合金高强高导的重要途径。
上述形变时效工艺流程相对复杂,不利于实际生产实施。当前,对合金固溶后直接人工时效仍是企业生产导电铝型材的主要工艺,若要获得更高导电性,须在更高时效温度(280 ℃)下进行长时间(30 h)时效。基于此,本文提出对合金固溶后直接施加冷轧变形,然后进行人工时效,研究冷轧变形量和人工时效温度对合金电导率和力学性能的影响,并揭示微观机制,以期为高强高导变形铝导体的生产提供借鉴和参考。
1 实验
本文采用广西南南铝加工有限公司提供的厚度为10 mm的6101热轧坯料作为实验材料,其中Mg和Si含量分别为0.44%和0.41%,另含有少量Fe、Zn和Ti元素,其含量分别为0.06%、0.02%和0.01%。本文采取的形变热处理工艺具体流程如图1所示,对板材在520℃下固溶30 min后水冷,获得固溶态合金,对固溶态合金进行冷轧预变形,变形量分别为5%、20%、40%、60%和80%。对不同变形量轧制合金进行时效处理,时效温度设为190 ℃、230 ℃和280 ℃,时效时间为0~35 h。
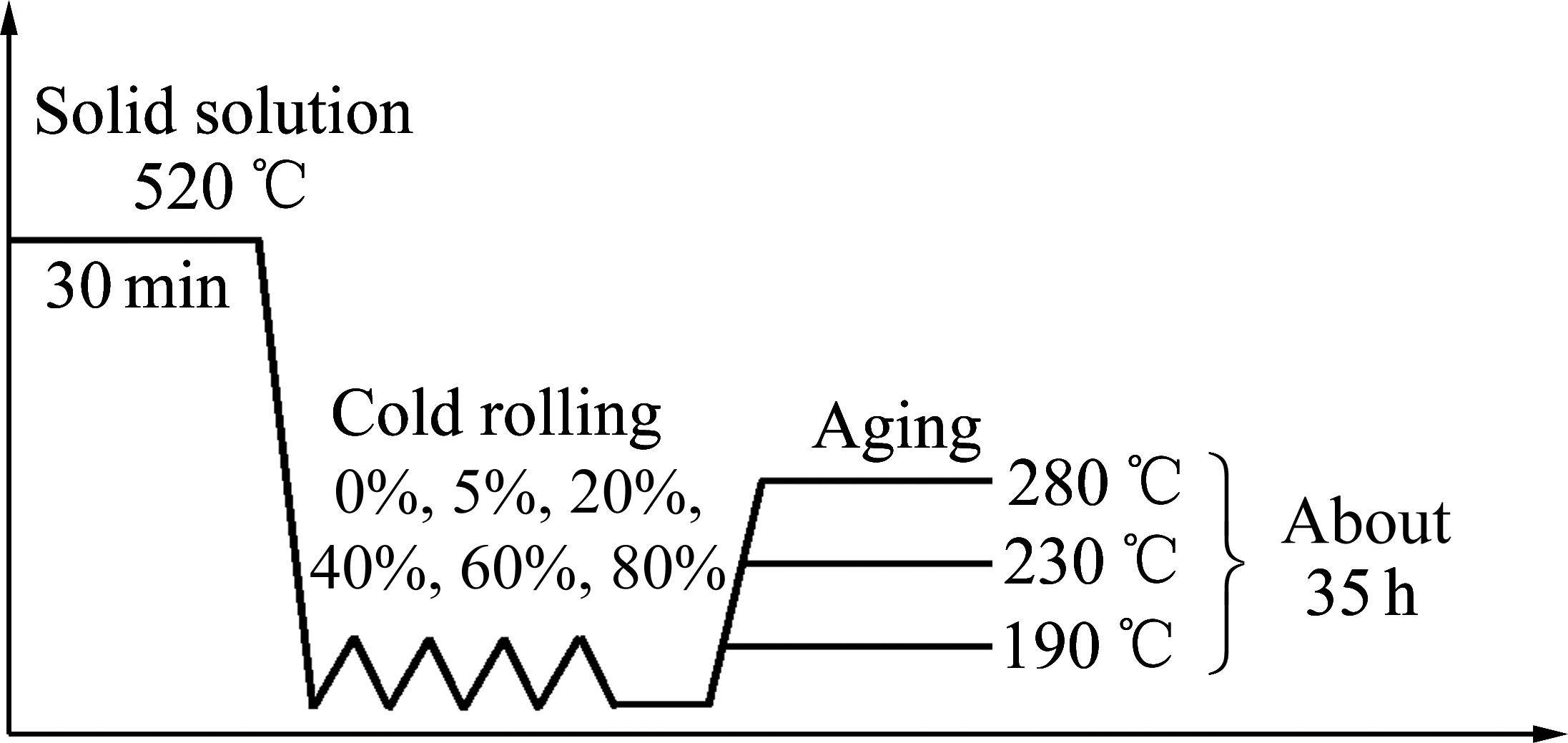
制取表面光滑平整的电导率测试样品,利用First FD-101型涡流导电仪测量合金电导率,测试10组,去掉最大值和最小值后取平均值。拉伸性能测试在岛津SHIMADZU AF-X100KN型万能试验机上进行,拉伸样品尺寸为6×t×30 mm2(t为不同预变形后的样品厚度,分别为10、9.5、8、6、4、2 mm),弹性变形阶段应变速率为0.25×10-3 s-1,塑性变形阶段应变速率为2×10-3 s-1,测试3次并取平均值。
合金的晶粒组织和析出相特征分别用Axio Observer 3m型光学显微镜观测和FEI Talos F200X型透射电子显微镜进行观测和表征,TEM图像在[001]Al晶带轴上拍摄。光学显微组织样品按照标准制样流程制备,利用Keller’s试剂腐蚀。TEM观测样品先经机械研磨后利用DJ-2000电解双喷仪进一步减薄穿孔。电解液为25%HNO3(体积分数)甲醇溶液,工作电压为15~25 V,工作电流为40~55 mA,温度为-35 ℃左右。采用差示扫描量热仪(DSC 3500)进行DSC分析,测试样品为d 3 mm×3 mm的小圆柱,测试升温速率为10 ℃/min,温度范围为50~500 ℃,保护气氛为氮气。
2 实验结果
2.1 合金的电导率变化
图2所示为固溶合金未冷轧、变形量为20%和60%冷轧后在不同温度时效过程中电导率随时效时间的变化。其他变形量(5%、20%、80%)合金的电导率变化与图2所示趋势相似。时效温度越高,变形量越大,初始上升速率越快,最终能达到的电导率也越大。与合金的时效硬度变化(时效动力学)不同的是,硬度在时效初始阶段也会迅速提升,但在达到最大(峰时效)后会缓慢下降趋势,而且时效温度越高,时效硬度往往越低。
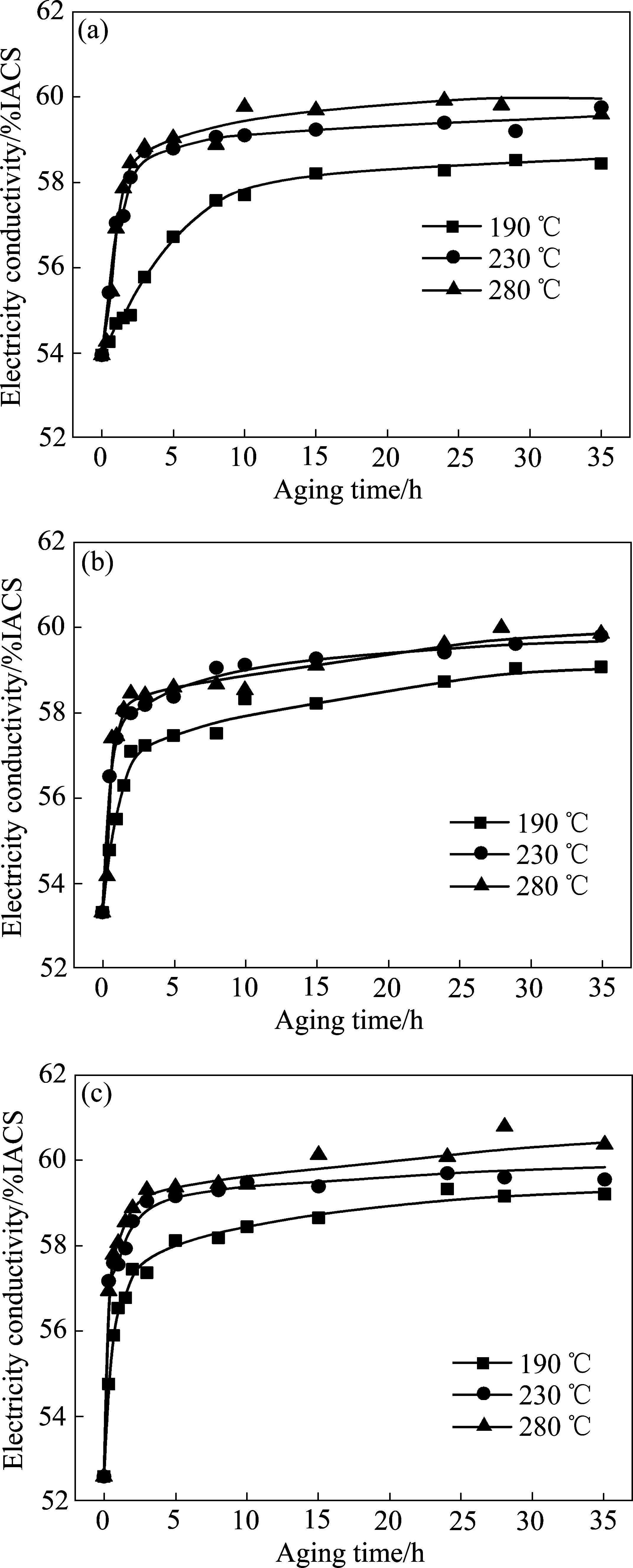
为更好地分析,本文将时效时间对合金电导率的影响趋势由图3示意。A为时效起点,B为初始线性阶段与过渡拐线的交点(拐线起点),C为过渡拐线与时效后期线性阶段的交点(拐线终点C)。A到B对应时效初始阶段,B到C为时效中间过渡阶段,而C到E为时效后期阶段。A、D和E对应的时效时间分别为0 h、25 h和35 h。由轧制变形量和时效温度对合金电导率影响曲线分析表明,变形量和时效温度对拐线起点B的影响较为显著,而对拐线终点C的影响较小。
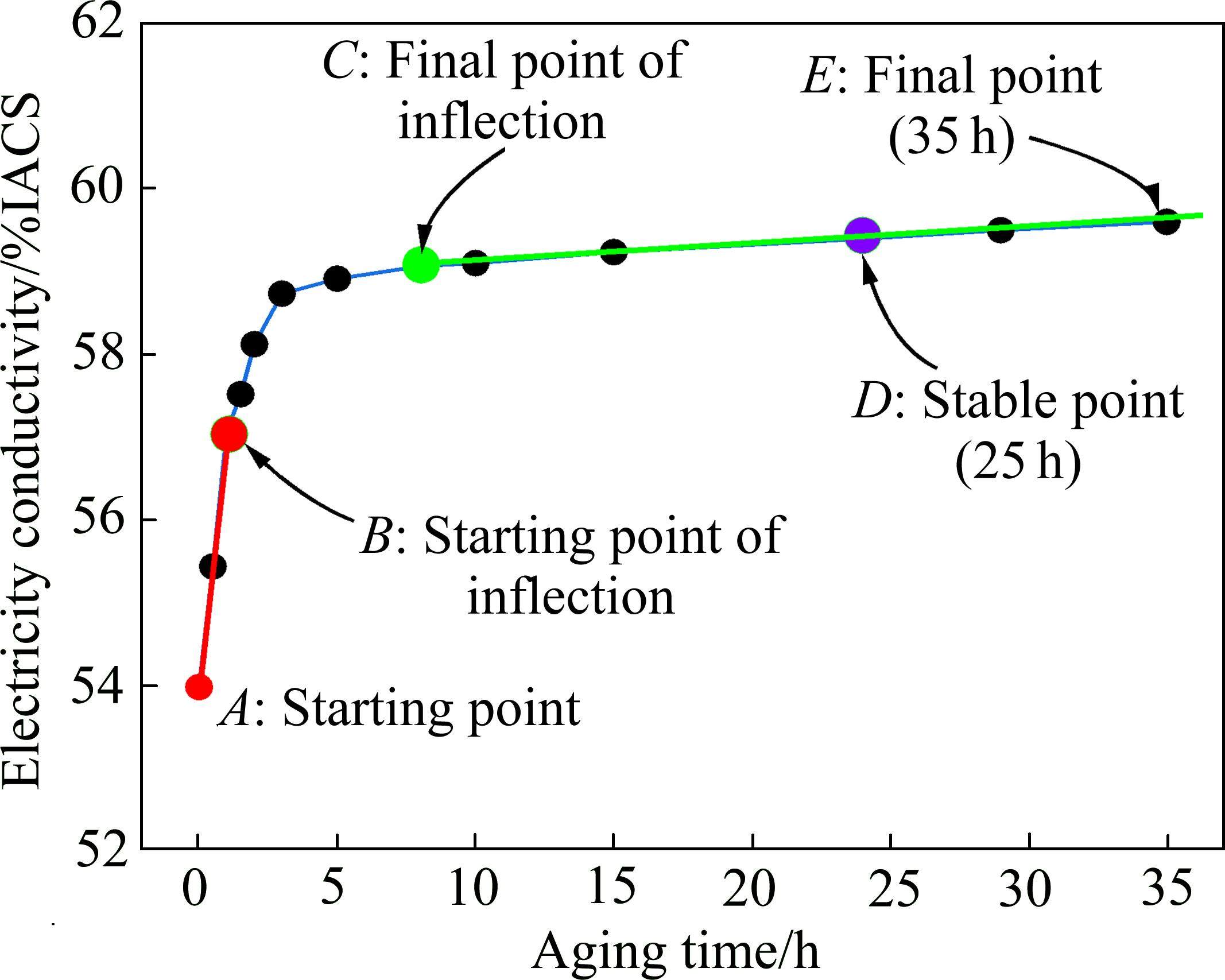
从实际生产考虑,初始阶段的提升速率和最终能达到的最高电导率非常关键,前者影响生产效率,后者决定产品性能。基于企业生产实际,本文以时效25 h时合金达到的电导率作为最高值。将初始提升速率和最高电导率作为关键指标进行分析。初始提升速度(Initial increasing speed, vi)定义如下:

式中:σA为初始起点电导率;σB为拐线起点电导率;tAB为时效开始到拐线起点间的时效时间。
根据图2可计算获得不同工艺条件下合金的初始提升速度,并将初始提升速度和最大电导率与冷轧变形量间的变化进行线性拟合,其结果如图4所示。由图4可以看出,合金初始提升速度随冷轧变形量增大而逐渐增加,且其初始提升速度与时效温度有关。提升速度可通过拟合直线斜率反映,时效温度190 ℃时,拟合直线斜率为7.4%IACS/h,时效温度为230 ℃时,拟合直线斜率为15.4%IACS/h;但当时效温度升高到280 ℃时,拟合直线斜率变化不太显著。对于最大电导率(σ),也体现出近似的变化规律,变形量越大,时效温度越高,合金最大电导率也逐渐升高。冷轧变形量与时效温度对合金电导率提升存在协同影响,其中冷轧变形量的影响更为显著。当合金冷轧变形量为80%时,在190 ℃、230 ℃和280 ℃温度下最大电导率分别达到60.2%IACS、60.5%IACS和60.7%IACS。
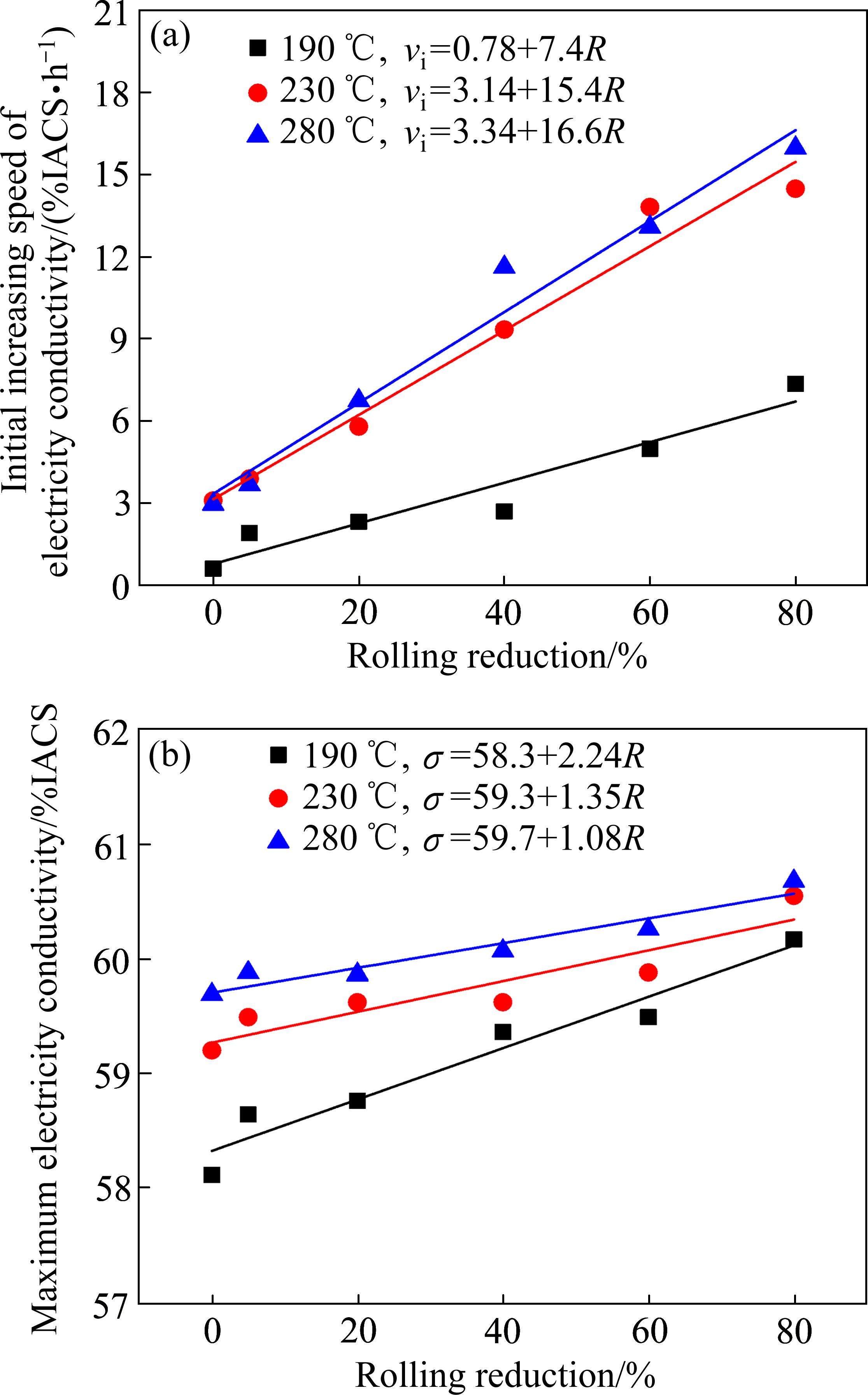
2.2 合金的力学性能分析
本文将图2中A、B、C、D和E点定义为不同的时效状态,其中A点对应固溶态(状态1),B点为时效初期(状态2),C点对应时效中期(状态3),D点对应时效后期(状态4),而E点对应时效末期(状态5)。对不同时效状态合金进行力学性能测试,结果如图5所示。由图5可以看出,时效初期合金的力学性能较固溶态均有提升,但提升幅度随变形量增加逐渐下降。
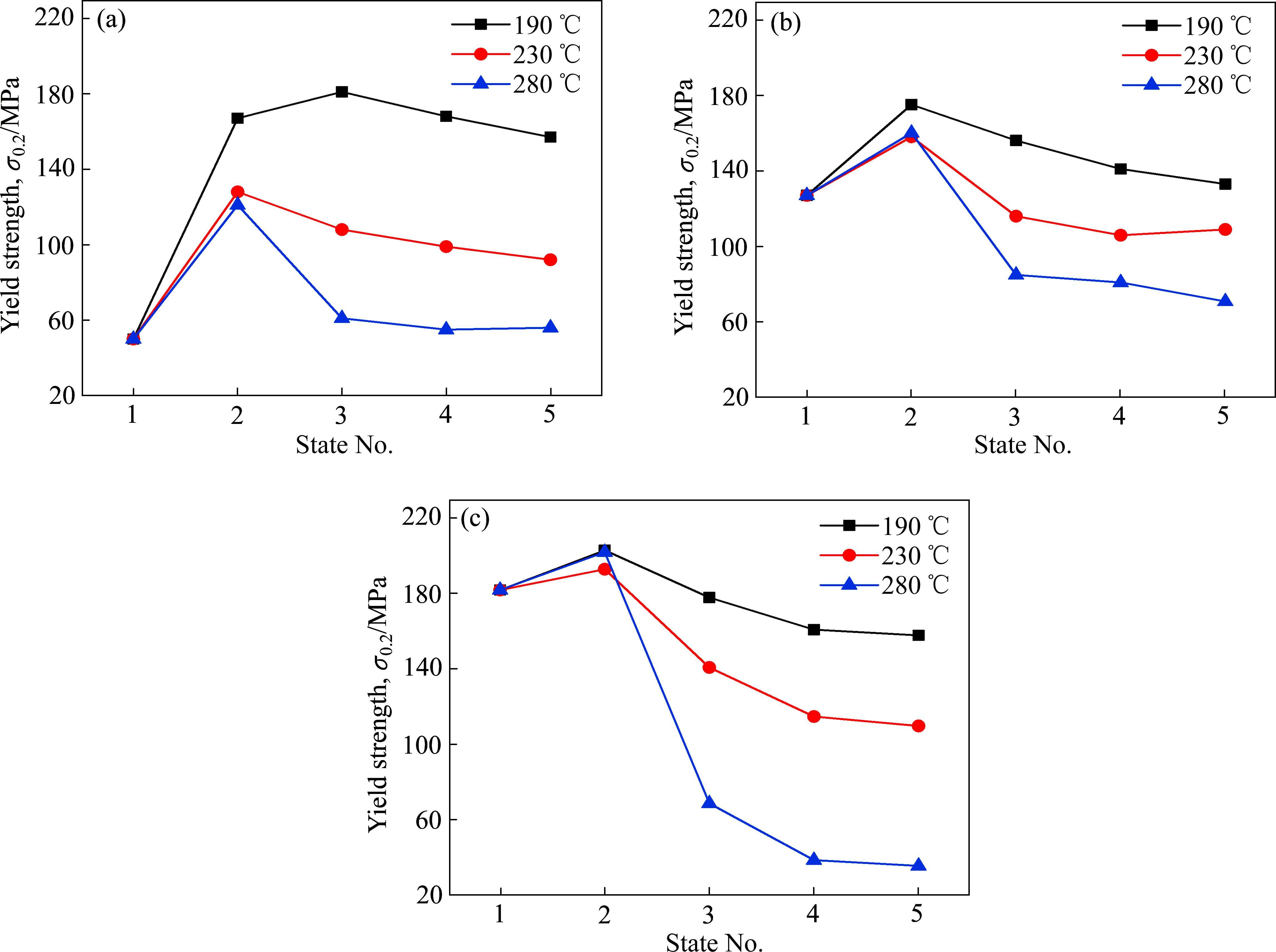
对未变形固溶态合金,其屈服强度仅为 50 MPa,时效后,屈服强度迅速提升,时效温度升高提升幅度下降(见图5(a))。经190 ℃时效15 h(状态3)后,屈服强度达到最大181 MPa,但经230 ℃和280 ℃时效后,合金在状态2时达到最大屈服强度。随即发生过时效,性能逐渐下降,且时效温度越高,下降速度越快。固溶态合金经变形量20%冷轧后,其屈服强度提升至127 MPa,在时效初期(状态2)时,屈服强度达到最大,但提升幅度小(见图5(b)),随后逐渐下降。当变形量提升至60%时,合金屈服强度进一步提升至182 MPa,也在时效初期(状态2)时,屈服强度即达到最大,但提升幅度小,仅约20 MPa。大变形合金经280 ℃高温时效后,在时效后期,合金屈服强度下降尤其显著,甚至低于40 MPa。
综上所述,对固溶态合金施加变形并在中等温度(230 ℃)下进行时效更为适宜。此时,时效初期电导率提升速度较快,能够达到的电导率更高,且过时效阶段合金力学性能不易发生显著下降,在确保合金获得高导电性能的前提下,可保证合金优异的力学性能,即使长时时效(35 h),屈服强度仍保持100 MPa以上(见图5(b)和(c))。
2.3 合金的光学显微组织分析
图6所示为未冷轧和变形量60%冷轧后合金在不同时效温度下时效25 h后的光学显微组织。热轧板材固溶会发生再结晶,经190 ℃时效晶粒仍略微呈扁长状(见图6(a));随着时效温度升高,晶粒逐渐等轴化,经280 ℃时效后,晶粒少许增大,约60 μm(见图6(c))。固溶合金经60%压下量冷轧变形后,晶粒被压延为纤维状,经25 h时效后仍表现出典型的纤维状组织特征(见图6(d)~(f))。但当时效温度为230 ℃时,在纤维状组织中出现未完全再结晶组织(见图6(e));当时效温度提高至280 ℃后,组织由纤维状晶粒和再结晶细小晶粒组成,其中再结晶晶粒尺寸约为25 μm(见图6(f))。
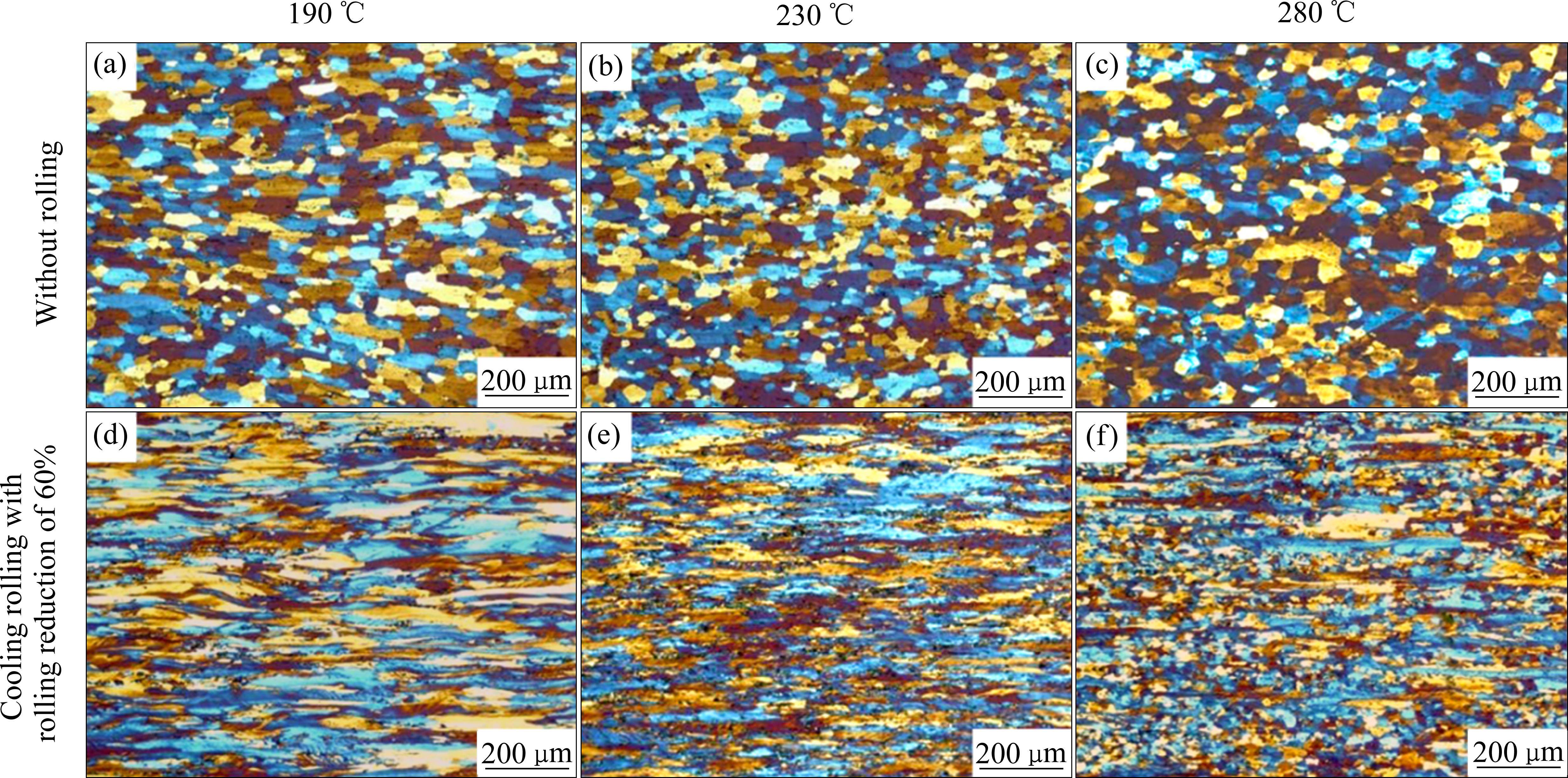
2.4 合金的TEM像分析
从以上性能变化可知,合金施加变形并在230 ℃下进行时效更为适宜。本文对230 ℃下时效合金进行TEM观测,主要分析其位错和析出相特征,其结果如图7所示。图7(a)、(b)和(c)分别为未冷轧、变形量为20%和60%冷轧后合金的未时效态(状态1);图7(d)、(e)和(f)分别对应未冷轧、变形量为20%和60%冷轧后合金分别时效1.5 h、1 h和40 min的状态(状态2);而图7(g)、(h)和(i)分别对应未冷轧、变形量为20%和60%冷轧后合金时效25 h的状态(状态4)。图7(a)所示为固溶未冷轧合金的明场TEM像,可以看出除少许位错外未发现明显第二相,呈现为典型的固溶态组织特征。经230 ℃时效1.5 h后,出现较多呈相互垂直分布的析出相(见图7(d)),而充分时效(25 h)后,析出相密度进一步增加,尺寸粗大,部分析出相长度甚至超过2000 nm。
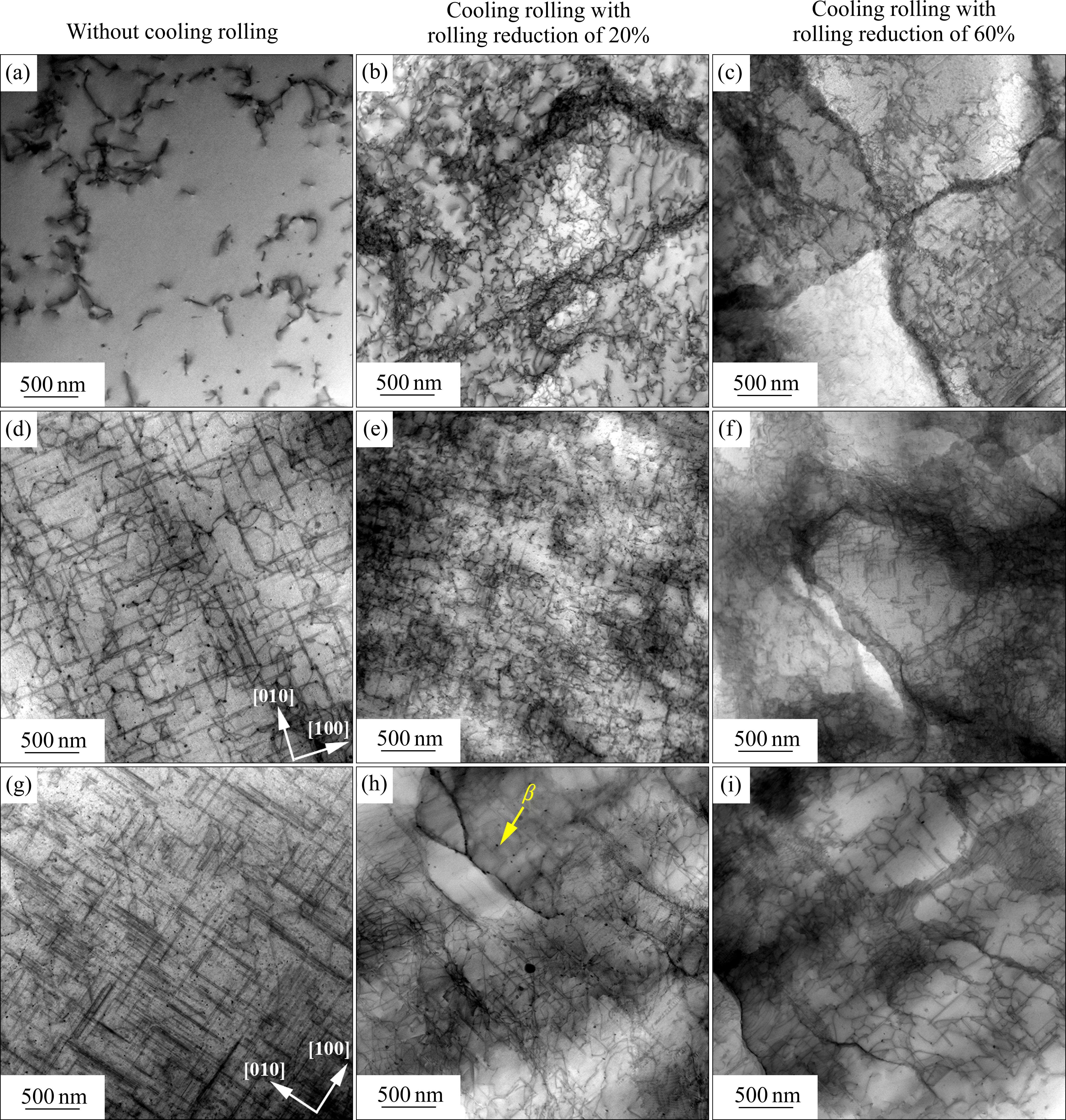
经冷轧变形后,基体中位错密度显著上升,特别在晶界处存在大量位错缠结(见图7(b)和(c))。在相同时效状态下,未冷轧和冷轧合金的TEM像存在显著差异。即使短时时效,在未冷轧合金中仍可清晰观测到时效析出相(见图7(d)),而冷轧合金在位错附近有少量垂直分布的棒状相,尺寸长度相对较短。经过长时(25 h)时效后,变形合金中位错密度显著下降,可观测到相互垂直分布的棒状析出相,密度增加,且除了位错仍在晶界附近富集外,晶内分布大量析出棒状相,但相比未变形合金,析出相显著细化。
3 分析和讨论
对于金属而言,固溶、第二相、位错和界面缺陷等都会不同程度地在电子传输过程中产生散射效应,从而降低电导率,而这些因素又不同程度地发挥强化效应[2, 17],导致导电和强度之间常表现为背反关系。同一元素在含量相同情况下,相比析出第二相,固溶对合金电导率的降低程度更大,相差1~2个数量级,固溶原子脱溶形成第二相后可以显著降低其不利影响,如La可促进AlSiLa析出而消耗Si,从而提升Al-Mg-Si合金电导率[9]。因此,抑制固溶并促进第二相析出,是实现电导率和强度同步提升的关键。分析图1~3可知,预变形可显著提高时效初始阶段的初始电导率提升速度、电导率和屈服强度,而时效后期阶段电导率增长趋于平缓,屈服强度下降逐渐平稳,电导率达到稳定最大值。
6101合金是Al-Mg-Si系合金,其时效过程的基本析出顺序为:过饱和固溶体→Mg-Si原子团簇→GP区→针状β″相→杆状β'相→β相(Mg2Si)[15]。图8所示为固溶态6101合金变形前后的DSC曲线。变形前后合金的DCS曲线整体较为相似,存在三个明显的放热峰Ⅰ、Ⅲ和Ⅳ,分别对应GP区、β″相和β相(或过剩Si相)形成。经轧制变形后,DSC曲线整体朝左移动,即相应的转变提前。放热峰Ⅰ由111.2 ℃提前至108.4 ℃,而放热峰Ⅲ由248.2 ℃提前至240.1 ℃。施加变形有利于GP区和β″相的快速析出,变形合金放热峰Ⅰ和Ⅲ的面积均大于未变形合金,放热峰Ⅳ向低温偏移(420.9 ℃),同时放热峰面积更大。
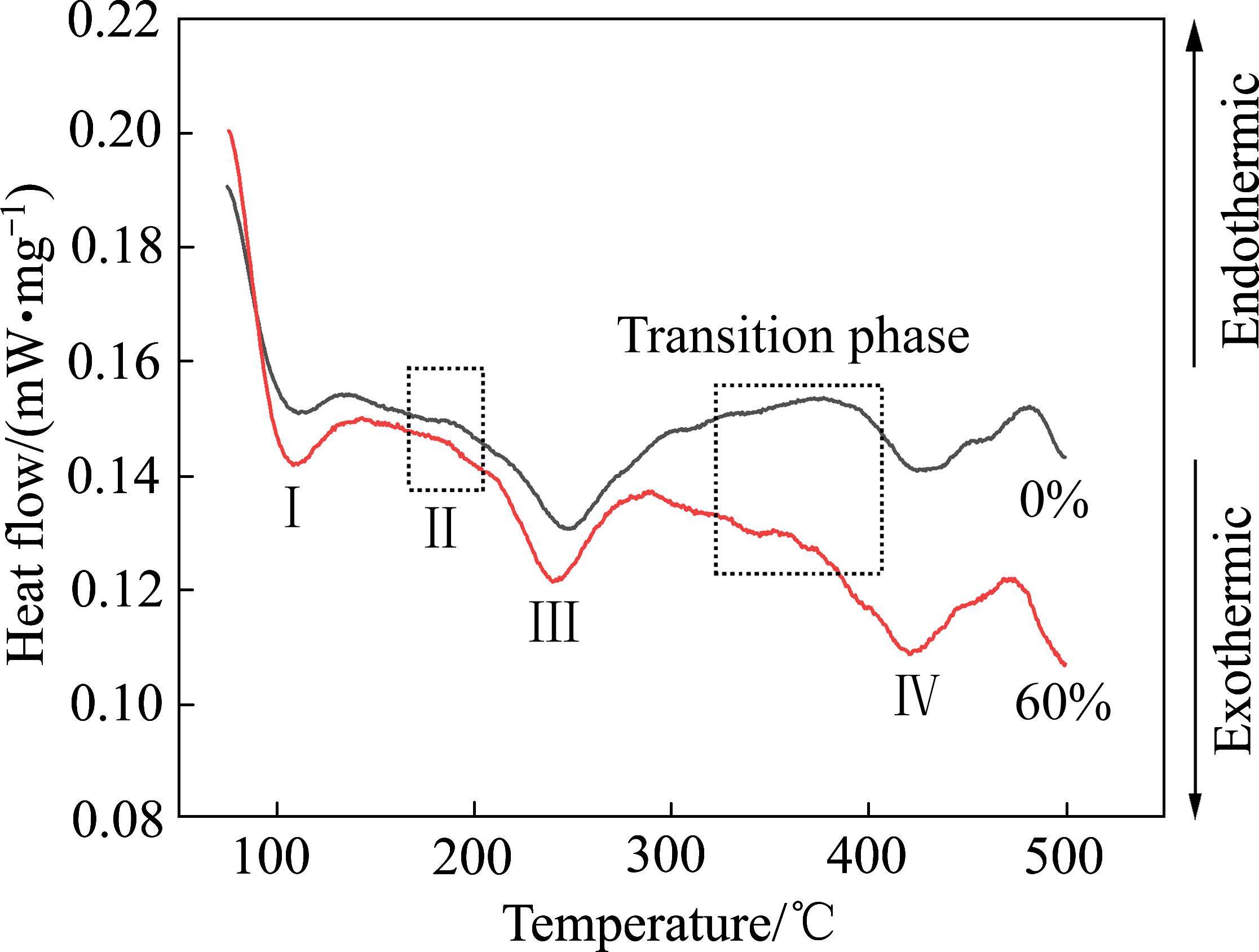
金属预变形后会引入大量位错缺陷(见图7(b)和(c)),同时还会产生高密度空位以及晶格畸变等,从而导致显著的加工硬化效应。经20%压下量冷轧后合金屈服强度由50 MPa提升至127 MPa,60%压下量冷轧后合金屈服强度进一步提升至182 MPa(见图5(a)、(b)和(c)中状态1)。变形引入的高密度晶格缺陷一方面可提供更多形核位点,降低形核界面能,提供形核功,从而促进时效相形核。同时,还可以提供快速扩散通道加速扩散,最终表现为加速合金的时效析出过程,并显著细化析出相[15-18],还有利于降低晶界沉淀相和无沉淀析出带宽度[19]。随着时效过程中GP区和β″相的不断析出,产生时效强化效应,屈服强度提升,与此同时,合金中Mg-Si原子的固溶度迅速下降,晶格畸变程度降低,电子散射效应降低,导致合金电导率迅速提升。变形量越大,内部缺陷密度越高,缺陷所致时效加速越快,初始电导率提升速度显著增大,并最终获得更大的电导率(见图4)。
高形核密度下生成的时效相更加细小,在未充分时效情况下,时效相与位错相互缠绕,难以分辨(见图7(e)和(f))。为深入明晰组织特性,对比分析合金的TEM明场和暗场相,并对时效相的主要组分Mg和Si元素进行面扫描,观测并分析析出相特征。图9所示为变形量60%冷轧合金在未时效和时效25 h后的明场(BF)和暗场(DF) TEM像及其Mg和Si元素面分布。固溶态合金经冷轧后,Mg和Si元素均匀分布(见图9(a)~(d)),经230℃长时时效后,合金中仍残留大量位错外,时效相已充分析出,具有更高的密度和更小的尺寸(见图9(e)~(h))。
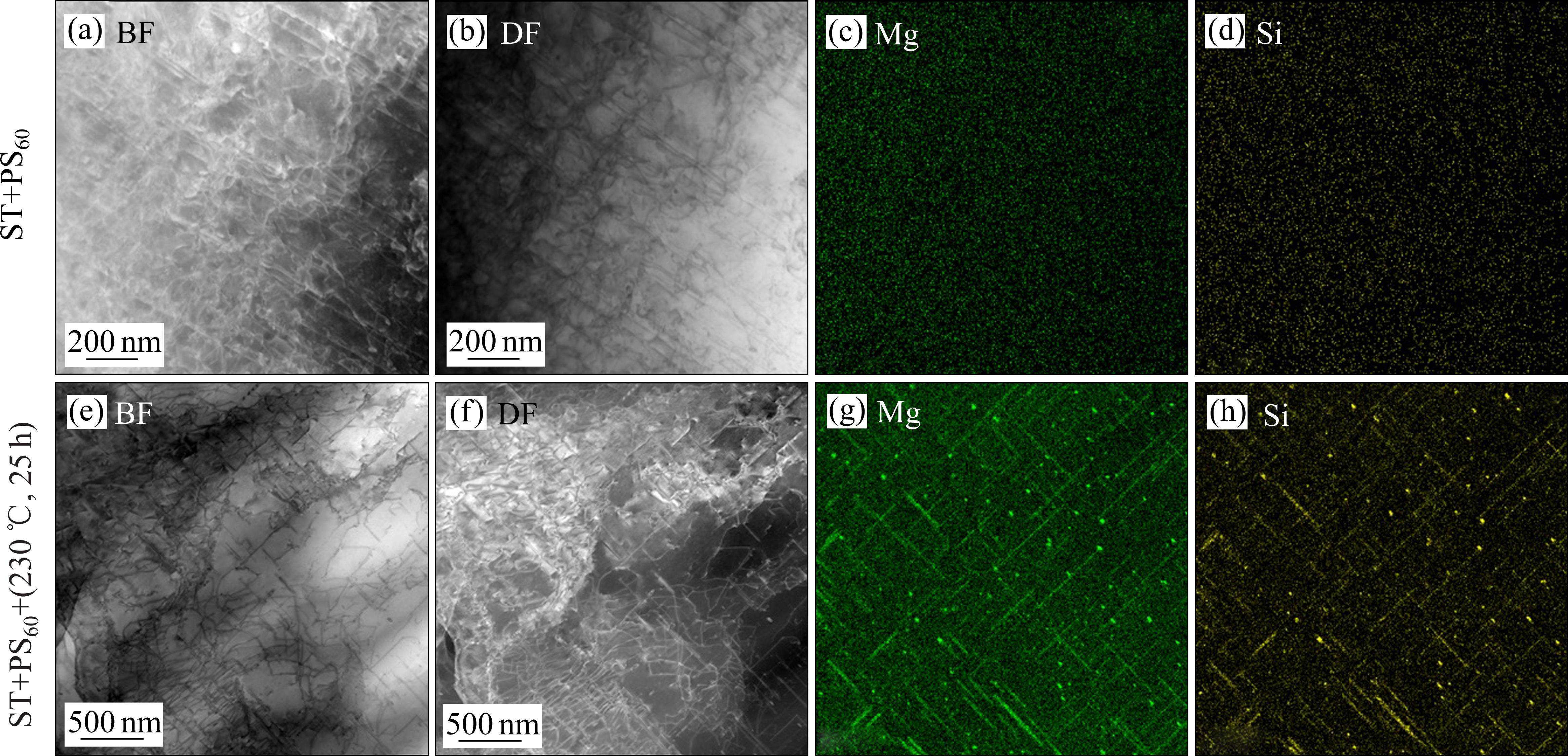
变形量60%冷轧6101合金在时效状态2(190 ℃时效1 h,230 ℃和280 ℃时效40 min)时表现出最高的屈服强度(见图5(c)),达到200 MPa。图10所示为变形量60%冷轧合金在230 ℃时效40 min后的典型TEM像、析出相特征及其Mg和Si元素面分布。由于合金内部具有较高密度的位错等缺陷,尽管时效时间短,但仍产生大量时效析出相(见图10(c)),其特征可由Mg和Si元素面分布清晰显示(见图10(g)和(h))。图10中箭头所指析出相是与基体间共格或半共格的β″或β'为主,析出相与高密度位错缺陷等相互作用,导致合金可获得更高的力学性能。此时其强化效果应是应变强化和析出强化等多因素共同作用所致[20-21]。且因Mg和Si原子脱溶,晶格畸变程度降低,合金表现出更高的电导率,超过了59.5%IACS。
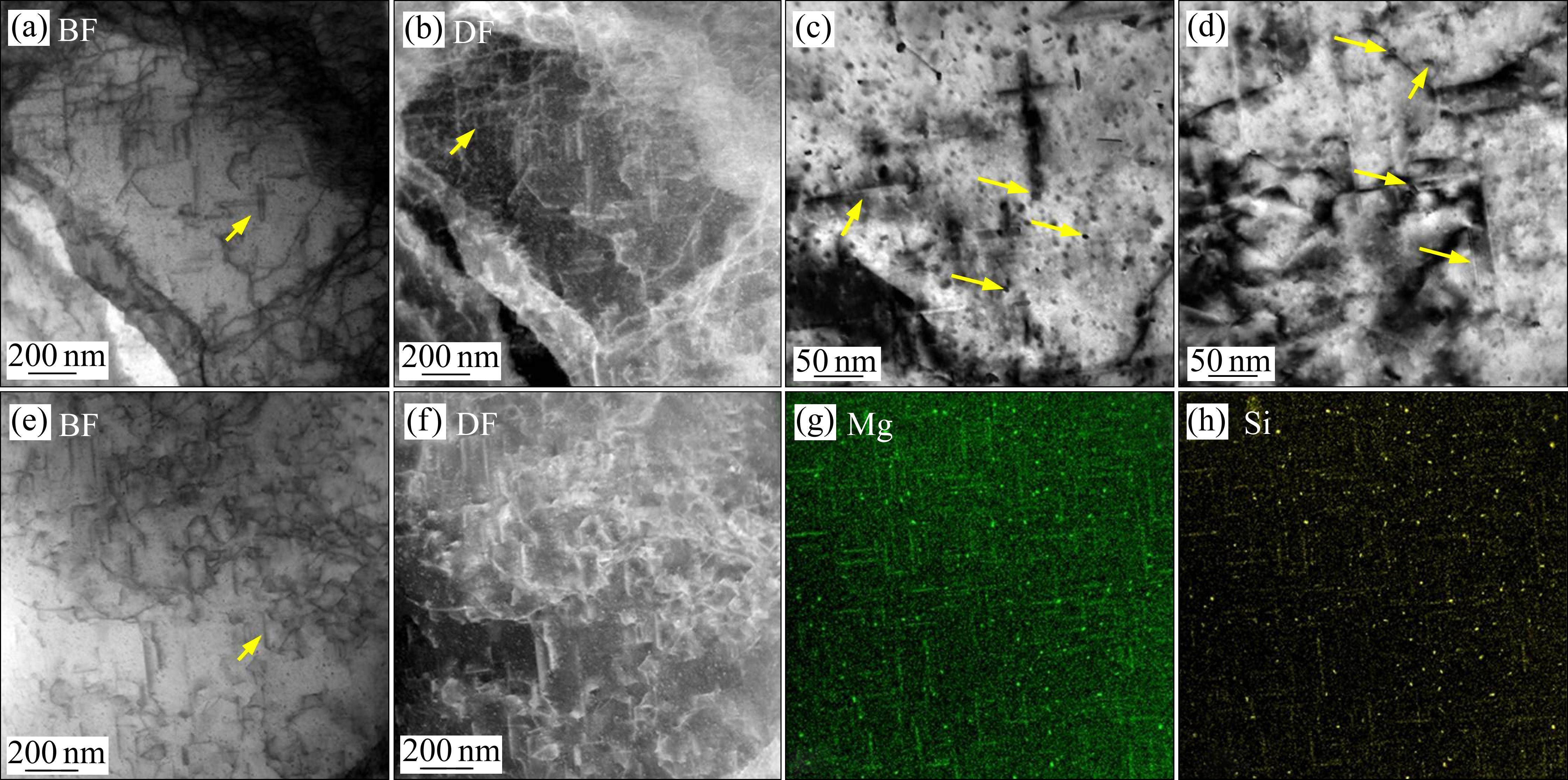
随着时效进程推进,固溶Mg-Si原子充分脱溶并析出稳定第二相,产生过时效,合金电导率始终会随时效时间延长而小幅增大,特别在大变形和更高时效温度下,时效进程更快,脱溶更加充分,电导率会更大。Al-Mg-Si基合金中稳定相为β-Mg2Si相,在后续的保温过程中,β-Mg2Si相会进一步增粗变长。变形量60%的冷轧合金在280 ℃高温下更易于发生再结晶并发生晶粒粗化(见图6(f)),且位错密度更高;β-Mg2Si析出相的密度更大,且在280 ℃长时间时效后变得更粗大,导致合金屈服强度显著下降(<40 MPa,见图5(c)),其屈服强度甚至低于未变形合金在高温(280 ℃)长时间(>25 h)时效状态的屈服强度(约60 MPa,见图5(a)),但此时合金的电导率提升超过60.5%IACS。
4 结论
1) 冷轧变形量和时效温度对时效初始电导率提升速度和最高电导率存在协同影响,变形量越高,时效温度越大,初始电导率提升速度越大,所能达到的最高电导率越高。
2) 时效温度较低(190 ℃)时,合金始终具有较高的屈服强度,相应地,初始电导率提升速度较小,最高电导率也较低。时效温度升高至280 ℃,具有最高的初始电导率提升速度和电导率,但大变形量下(60%)合金经长时间(>25 h)时效后,其屈服强度下降显著,甚至低于40 MPa。
3) 预变形引入以位错为主的高密度晶格缺陷,产生显著的加工硬化效应。晶格缺陷可为时效相析出提供形核位点,降低形核功,加速形核进程,导致时效过程合金电导率快速提升。形变时效合金的析出相更加细小弥散,残留位错与析出相协同导致合金强度显著提升,实现导电和强度同步提升。
4) 对合金施加变形,并在中等温度(230 ℃)下进行时效更为适宜,可确保合金获得更大的初始电导率提升速度、更大的电导率和更高的力学性能。经60%变形且在230 ℃下时效合金初始电导率提升速度可接近14%IACS/h,最高电导率可达60%IACS,屈服强度高达200 MPa,且长时间 (35 h)时效后,其屈服强度仍保持100 MPa以上。
黄程毅, 段守岗, 卢逸喆, 等. 预变形与时效温度对6101合金电导率和力学性能的影响[J]. 中国有色金属学报, 2025, 35(1): 156-166. DOI: 10.11817/j.ysxb.1004.0609.2024-44972
HUANG Chengyi, DUAN Shougang, LU Yizhe, et al. Effects of pre-deformation and aging temperature on electrical conductivity and mechanical property of 6101 alloy[J]. The Chinese Journal of Nonferrous Metals, 2025, 35(1): 156-166. DOI: 10.11817/j.ysxb.1004.0609.2024-44972