1 Introduction
Silver as one of the precious metals, in addition to its aesthetic appearance, has also been considered by the industry due to its unique properties. For example, it has the highest electrical and thermal conductivity among known metals [1]. However, high price and low strength usually limit its application [2]. Therefore, advanced and new materials are needed to replace single-layer silver sheets so that the use of multilayer composites can be fruitful. In fact, multilayer composites contain two or more similar or dissimilar metals, depending on the input layers, can offer different properties such as corrosion resistance, high strength, good wear properties and proper electrical conductivity [3]. So far, various combinations of silver sheets have been used to produce metal laminates like: Ag/Cu [4-7], Ag/Fe [8-10], Ag/Ni [11], and Au/Ag [12].
In this way, aluminum due to the low price and high specific strength [13] can be used as a desirable choice for the production of multilayer composite with silver. One of the common methods for producing multilayer metal sheets is the roll bonding process, which has an advantage over other methods due to simplicity, accessible equipment and its ability to work on sheets with different thickness [14]. In fact, cold roll bonding (CRB) process is one of the cold welding processes in which metals are bonded at room temperature by applying high contact pressures caused by the rolling machine [15]. Studies have shown that the roll bonding process can be influenced by many parameters such as surface preparation [16-18], speed and direction of rolling [19, 20], thickness reduction [21, 22], and rolling temperature [23, 24]. However, heat treatment after rolling seems to be one of the most important parameters affecting the mechanical and metallurgical properties as well as the ductility behavior of multilayer composites produced by roll bonding process. JAMAATI et al [25] investigated the effect of annealing conditions on the bond strength of Al/Al sheet produced by cold roll bonding process. The results showed that with increasing annealing temperature, the peeling force of the layers and consequently bond strength increase. In fact, annealing reduces the effect of work-hardening caused by the rolling stage, which in turn improves bond strength and formability of the specimens. WANG et al [26] used hot roll boning process to fabricate Al/Mg clad sheets and studied the effect of annealing on the mechanical properties of composite. It was found that with increasing annealing temperature, the yield strength of the sample decreases while the elongation has the reversed trend. So that the maximum value of elongation was obtained at 200 ℃, and after that, increasing the temperature leads to a drop. They concluded that the decrease in yield strength is due to the occurrence of recrystallization and increase in grain size of the magnesium layer, while the formation of intermetallic compounds is a limiting factor of elongation. KIM et al [27] studied bending and fracture behaviors of tri-layered Cu/Al/Cu composite sheets processed by cold roll bonding. After annealing at 200, 300, 400, 450 and 500 ℃, bendability was evaluated using a three-point bending test. During the bending test, for as-roll bonded and annealed at 200 ℃ samples, rupture was observed at the Al layer. Increasing the annealing temperature causes the local deformation to be distributed throughout the bending area, resulting in a relatively more uniform bending. MENG et al [28] determined the effect of different annealing temperatures on the Ag/Cu bimetallic strip produced by roll bonding process. The samples were annealed at 400-800 ℃, and it was revealed that as the annealing temperature increased to 700 ℃, the hardness of the copper and silver layers downturns continuously. However, at up to 400 ℃, the hardness value decreases dramatically and is balanced for higher temperatures. In other words, although signs of recrystallization were detectable at 250 ℃, it was much clearer at 400 ℃. In addition, at temperatures above 600 ℃, fine-grained areas appear first in the silver layer and then in the interface. In another study [29], they examined the microstructure of Ag/Cu interface annealed at 750 ℃. Only 30 min after the start of annealing, the first signs of recrystallization appeared in the interface region. As the annealing time continues, the thickness of the copper diffusion zone in the silver layer increases and as a result, the grain size in the silver layer becomes larger than that in copper layer.
Since sheet metal usually undergoes deformation after production and improvement of mechanical properties [30], it is very important to know their behavior during the forming process. To determine the safe deformation range of sheet metal, forming limit curve (FLC) can be used when the minor and major strains are displayed [31]. Research has shown that annealing heat treatment can improve the formability of aluminum sheets [32-35]. In other words, annealing provides the necessary conditions for recrystallization and grain growth, which can lead to an increase in the FLC [36]. Also, the evolution of dislocation density behavior during heat treatment can be another factor affecting the plasticity of metal sheets [37]. Like tailor laser welded blanks, where the welding quality is very effective in their mechanical properties, the strength of the bond is important in roll-bonded sheets [38, 39]. However, in multilayer composites, due to the quality of the bonding between the layers and the possibility of formation intermetallic compounds at the interface during annealing, FLC may show different behavior. Nevertheless, it seems necessary to study the formability of multilayer metal sheets [40]. SUN et al [41] compared the formability of Cu/Al cladded sheets produced by explosive welding process in annealed and non-annealed states. The results showed that during annealing, the stresses created in the sheet due to explosive welding are released and as a result, the formability increases. ATIFEH et al [42] investigated the effect of annealing on the formability of Al/Mg bilayer sheets produced by explosive welding technique. It was found that annealing at 250 ℃ causes the formation of intermetallic compounds, but its low thickness does not have a significant effect on the forming limit diagram. They attributed the decrease in formability at temperatures above 250 ℃ to the formation of a brittle intermetallic compound at the interface of the layers. In another study, RAHMATABADI et al [43] found that annealing Al/Mg roll-bonded sheet at 300 ℃ increases the formability of the composite. In fact, due to annealing, an intermetallic compound is formed in the interface, which helps to improve the bond strength. In addition, due to the occurrence of recrystallization and recovery in the composite, the effect of work-hardening eliminates and that of formability increases. MANESH et al [44] evaluated the formability of aluminum-clad steel sheets using Ericsson cupping test. The results showed that there is an optimum annealing temperature at which the bond strength and formability are maximum. The formation and growth of brittle intermetallic compounds during annealing was identified as the main cause of the change in the formability of the composite. In other words, the phenomenon of over-aging occurs at temperatures below 525 ℃, which limits the elongation.
Fracture toughness along with other mechanical properties such as tensile strength and elongation is effective in the selection of engineering materials [45]. In metallic materials, an increase in tensile strength is usually associated with a decrease in fracture toughness [46]. Therefore, recognizing this feature can be necessary for multi-layer sheets produced by roll bonding process. DELSHAD GHOLAMI et al [47] investigated the effect of applied strain and component percentage on the fracture toughness of Al/Mg multilayer composite produced by accumulative roll bonding (ARB) process. According to the results, under a certain applied strain and percentage of Al used in the Al/Mg composite, the highest amount of fracture toughness will be achieved (third pass for Al33.3%Mg). Therefore, increasing these values will reduce the fracture toughness. RAHMATABADI et al [48] evaluated the fracture toughness of Al ARB-ed sheets. They concluded that as the number of ARB cycles increases, the fracture toughness of the samples also increases. Tensile strength and elongation as well as grain refinement during ARB cycles were introduced as effective factors on fracture toughness of aluminum multilayer composites. PAHLAVANI et al [49] also studied the effect of thickness reduction on the fracture toughness of Al/Mg-Li/Al composite sheets produced by CRB process in rolling direction (RD) and transvers direction (TD). It was found that the maximum amount of fracture toughness for RD and TD directions occurs in samples with thicknesses of 1.6 and 1.2 mm, respectively. Therefore, the trend of fracture toughness changes was not similar to tensile strength. Examining the research results showed that annealing heat treatment can decrease and increase the tensile strength and formability of bilayer sheets, respectively. Since Ag/Al bilayer sheets are subjected to sheet metal forming processes such as embossing, increasing the formability and fracture toughness can be very important and vital. Although heat treatment after rolling seems to affect the fracture toughness of sheet metal [50], so far no research has been done on the effect of annealing temperature on the fracture toughness behavior of multilayer composites fabricated by CRB.
According to the review of the literature, the use of aluminum/silver bilayer sheets can bring the special properties of silver, high specific strength and excellent plasticity of aluminum, in addition to cost reduction, which can be used in fuel cells and batteries. In this research, the effect of annealing temperature on FLC and fracture toughness of aluminum/silver (Ag/Al) bilayer sheets was investigated. For this purpose, first, the composite sheets were produced by the CRB process, and then it was annealed at three different temperatures of 200, 300 and 400 ℃. It is expected that due to the recrystallization of aluminum in this temperature range, the mechanical properties and formability behavior of Ag/Al bilayer sheet will change.
2 Experimental procedures
2.1 Materials
In this research, pure aluminum and silver sheets with thicknesses of 3 and 0.5 mm, respectively, were used. The mechanical properties and chemical composition of the materials are given in Table 1. Before the cold roll bonding process, the aluminum sheet was annealed at 400 ℃ for 90 min and the silver sheet at 700 ℃ for 30 min to achieve a completely homogeneous structure.
Material | Hardness (HV) | Elongation/% | Tensile strength/MPa | Chemical composition | |
---|---|---|---|---|---|
Al | As-received | 67.63 | 15.47 | 129.25 | 98.81Al, 0.872Mg, 0.188In, 0.0861Mn, 0.012Si, 0.0102Ca, 0.0062Fe, 0.0155 others (wt%) |
Annealed | 51.39 | 49.36 | 69.65 | ||
Ag | As-received | 105.17 | 7.71 | 174.75 | Pure |
Annealed | 85.43 | 62.84 | 89.8 |
2.2 Cold roll bonding process
Roll bonding process can be applied to a wide range of sheets, which can be of one or more different materials. In this method, two or more sheets, plates or metal strips are placed on top of each other and then rolled. When the amount of deformation reaches a certain value, a bond will be created between the two metals [51]. One effective factor in the quality of the bonding between layers in roll-bonded sheets is the proper preparation of layer surfaces. For this purpose, aluminum and silver samples with dimensions of 80 mm×80 mm and thicknesses of 3 and 0.5 mm, respectively, were placed in acetone for 10 min. Then, to better bond and remove surface oxide, the sheet surfaces were brushed evenly with a steel wire brush. In order to achieve a good bond and prevent oxidation of the brushed surfaces, after preparation, the samples were immediately rolled at room temperature without lubricant. Rolling was done in several steps. In the first stage, the joints were fabricated with a thickness reduction of about 70%. Then, due to the special application of this composite in a type of lithium-ion battery, in a few rolling steps, the final thickness of the Ag/Al bilayer sheet reached 350 μm.
After the first rolling stage, it should be noted that to remove the hardness created due to plastic deformation, the samples were subjected to annealing heat treatment at 400 ℃ for 90 min. In order to investigate the effect of annealing temperature on the mechanical properties and formability of Ag/Al composite, the samples produced by CRB were annealed at 200, 300 and 400 ℃ for 90 min and cooled in a furnace. Figure 1 shows a schematic of Ag/Al composite sheet production by CRB process.
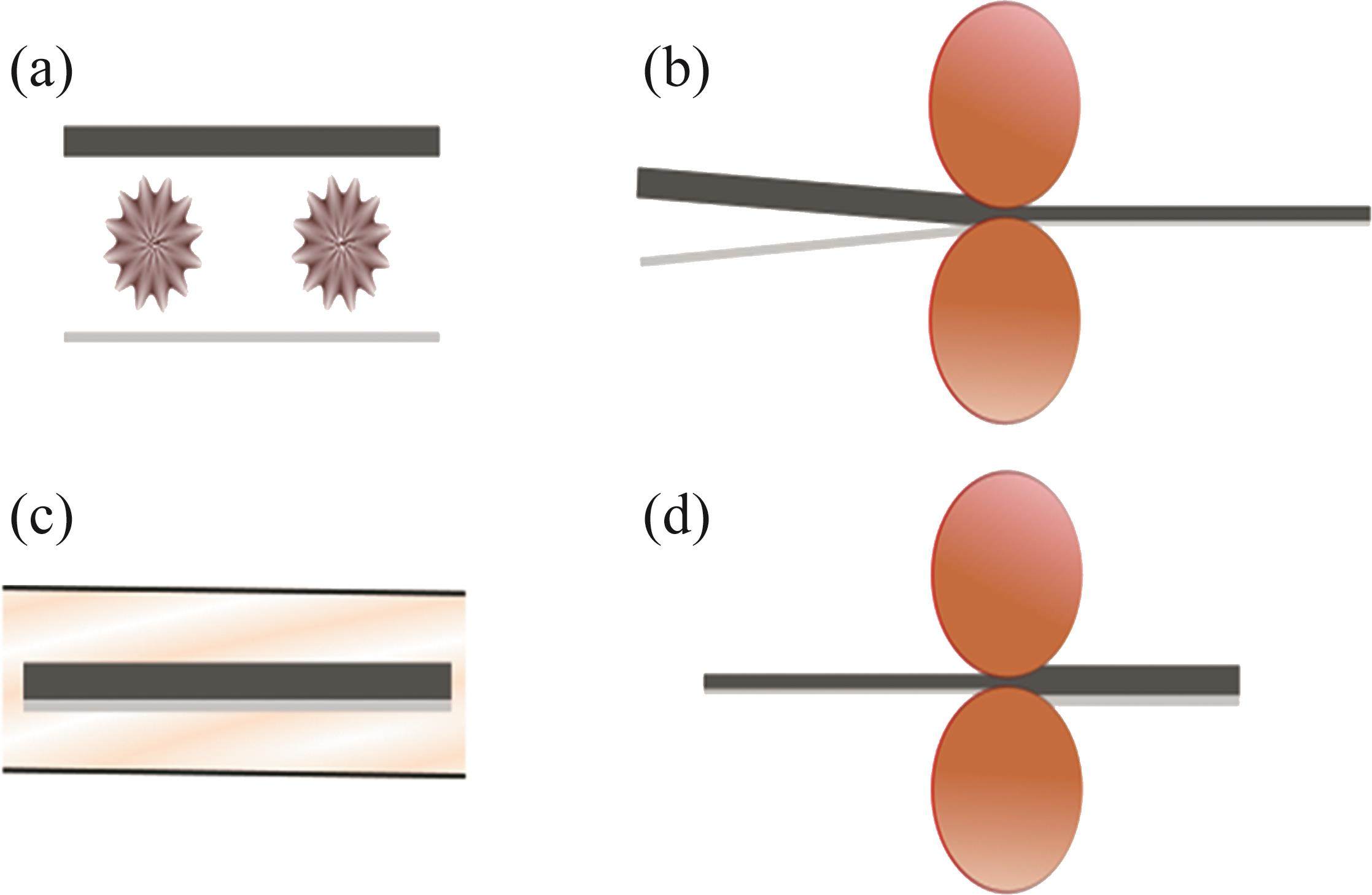
2.3 Mechanical properties
The mechanical properties of Ag/Al composite sheets were investigated using uniaxial tensile test at ambient temperature with a strain rate of 1×10-3 s-1 following the ASTM E8M-9 standard. For this purpose, three tensile test specimens were prepared for each sample using wire electric discharge machining (WEDM). So, if the results of the two initial tensile tests were different, the third sample would also be tested. Vickers hardness test was used to characterize the microhardness of the produced samples using digital micro-vickers hardness tester, test range: HV 1-HV 2967, hardness resolution: HV 0.1. The applied load and loading time were considered to be 0.098 N and 15 s, respectively. The microhardness in each layer of the composite was determined arbitrarily at six points by averaging the obtained values. The fracture cross-section of uniaxial tensile test samples also was checked by a 4th generation VEGA TESCAN S9000 Scanning Electron Microscope (SEM) with tungsten filament electron source, which combines SEM imaging with live elemental composition analysis in a single window software to evaluate the fracture mode of bilayer sheets and the effect of annealing heat treatment on bonding quality.
2.4 Fracture toughness test
In this study, plane stress fracture toughness tests are performed to evaluate the resistance of materials against crack growth. First, the compact-tension (CT) specimens were cut based on ASTM—E647 and ASTM—E399 standards [52] by electrical discharge machining (EDM) and then, using a special fixture, the fracture toughness test was performed with tensile testing machine. Figure 2 shows the dimension of fracture toughness sample and how it fits into the fixture. The parameters w and α0 are 19 mm and 7.5 mm, respectively. The quasi-static fracture test was performed only in the first failure mode at head speed of 1 mm/min. Crack growth was measured visually using a conventional camera and image processing software and following the ASTM E561 standard, R-curve was used to calculate CT samples fracture toughness [53]. Fracture toughness is calculated from the contact point of two graphs KR (for test sample) and Kapplied. For arbitrary values of Pi that are tangent to the R-curve. KR is calculated from Eq. (1) [54], in other words, this value is plotted according to the changes in crack length at several constant forces.
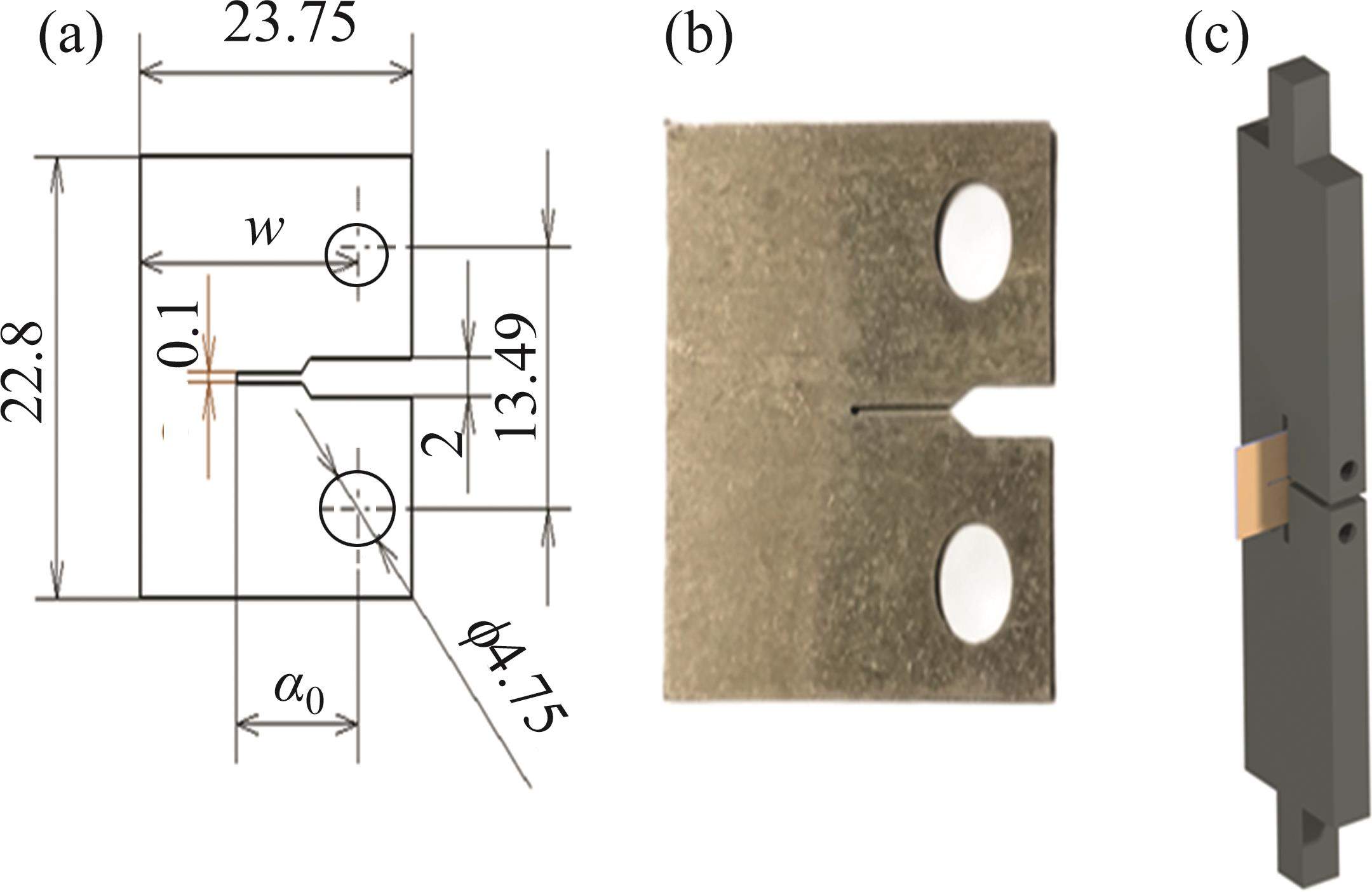
In Eq. (1), KR indicates the resistance of the sample to crack growth. In the CT specimens, the constant parameters were initial crack dimension (α0=7.5 mm), width (w=19 mm), and thickness (b=0.35 mm). Furthermore,
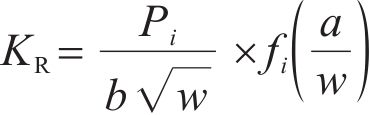
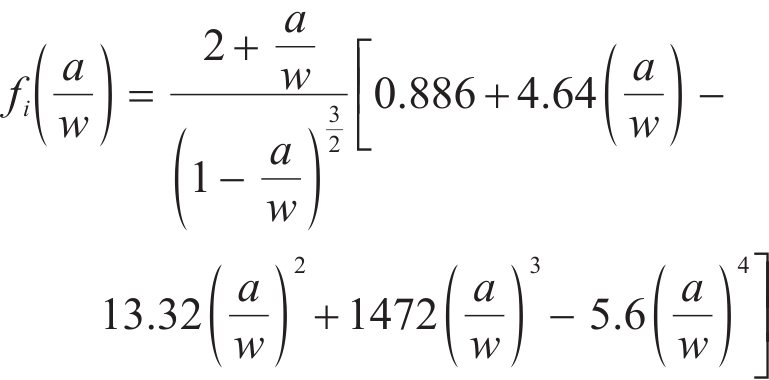
2.5 Experimental determination of forming limit diagram
The FLC actually includes various forming modes that predict the range of strains in which the necking occurs [55]. Nakazima test is one of the experimental methods to obtain FLC, which has been used by researchers due to the simple shape of its samples and also the possibility of considering the entire strain range [52, 53]. In this test, the samples are stretched by a hemispherical punch in accordance with ISO 12004—2, at room temperature. To obtain the strains formed in the samples, a 2.5 mm diameter circular lattice is engraved on the sheet by an electrochemical etching device that will turn into elliptical after the Nakazima test. By measuring the small and large diameters of the ellipse with Mylar tape and also using Eqs. (3) and (4), the true major and minor strains (ε1 and ε2) can be calculated [58].
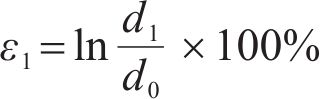
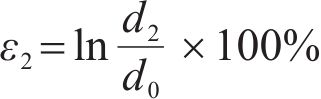
where d0 is the initial diameter of the circle (2.5 mm), d1 is large diameter and d2 is the small diameter of the ellipse. Figure 3 shows the samples before and after the Nakazima test and the die set used.
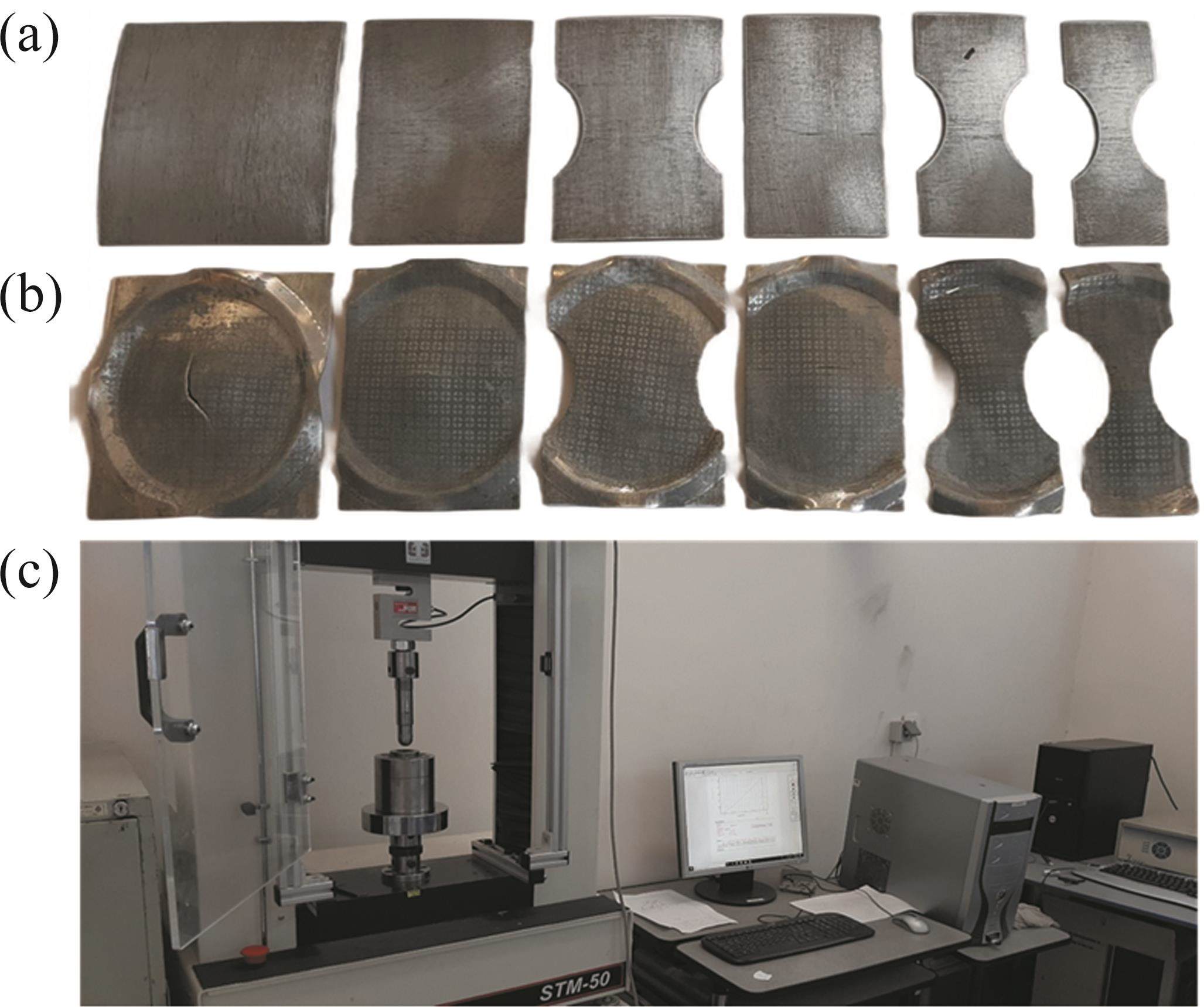
3 Results and discussion
3.1 Mechanical properties
Figure 4 shows the stress-strain curve of initial single-layer sheets and Ag/Al bilayer composites annealed at different temperature in rolling direction (RD). As can be seen, the Ag/Al composite fabricated by the CRB process has higher tensile strength and less elongation than the original aluminum and silver samples (Ag/Al non-annealed). So that the bilayer sheet compared as-received silver and aluminum sheets shows a 112% and 257% enhancement in the ultimate tensile strength (UTS), respectively. However, sharp drop in elongation is also observed for roll-bonded. This change in mechanical properties of the sheets fabricated by CRB process can be attributed to strain hardening as well as increasing density of dislocations caused by rolling [55-58]. Figure 5 shows the effect of annealing temperature on the UTS and elongation of Ag/Al bilayer sheets. According to the figure, it can be seen that the value of UTS for rolled aluminum/silver composite (without any annealing treatment) and samples annealed at 200, 300 and 400 ℃ was obtained 318, 242, 167 and 159 MPa, respectively. As known, annealing heat treatment reduces UTS while improves elongation. In fact, annealing causes the phenomenon of recrystallization and recovery in the layers of silver and aluminum, as a result of softening [59, 60]. But the change in mechanical properties varies at different temperatures. As it is clear, at 200 ℃, there is no significant difference in stress-strain behavior, which indicates the occurrence of recovery at low temperatures for the aluminum layer [61, 62]. According to the results, the temperature of 300 ℃ can be considered as the recrystallization temperature of the aluminum layer, because under this condition, the recorded changes in mechanical properties are meaningful. Also, with increasing annealing temperature, this discrepancy becomes more severe, so that the greatest decrease in UTS and increase in elongation compared to the non-annealed sample occurs at 400 ℃ by 50% and 340%, respectively. However, at 400 ℃, the strength changes are negligible compared to that at 300 ℃, while the elongation continues its upward trend. Therefore, 300 ℃ can be introduced as the optimal annealing temperature for Ag/Al bilayer sheets to achieve the appropriate strength. The microhardness variations of Ag/Al bilayer sheets at different annealing temperatures are shown in Figure 6. After CRB, microhardness for the aluminum and silver layers increases from HV 51.4 and HV 85.4 in the as-received samples to HV 87.5 and HV 138.3, respectively (70% and 62% growth). This sharp enhancement in microhardness can be due to dislocation tangles resulting from strain hardening and the formation of subgrain boundaries [63, 64].
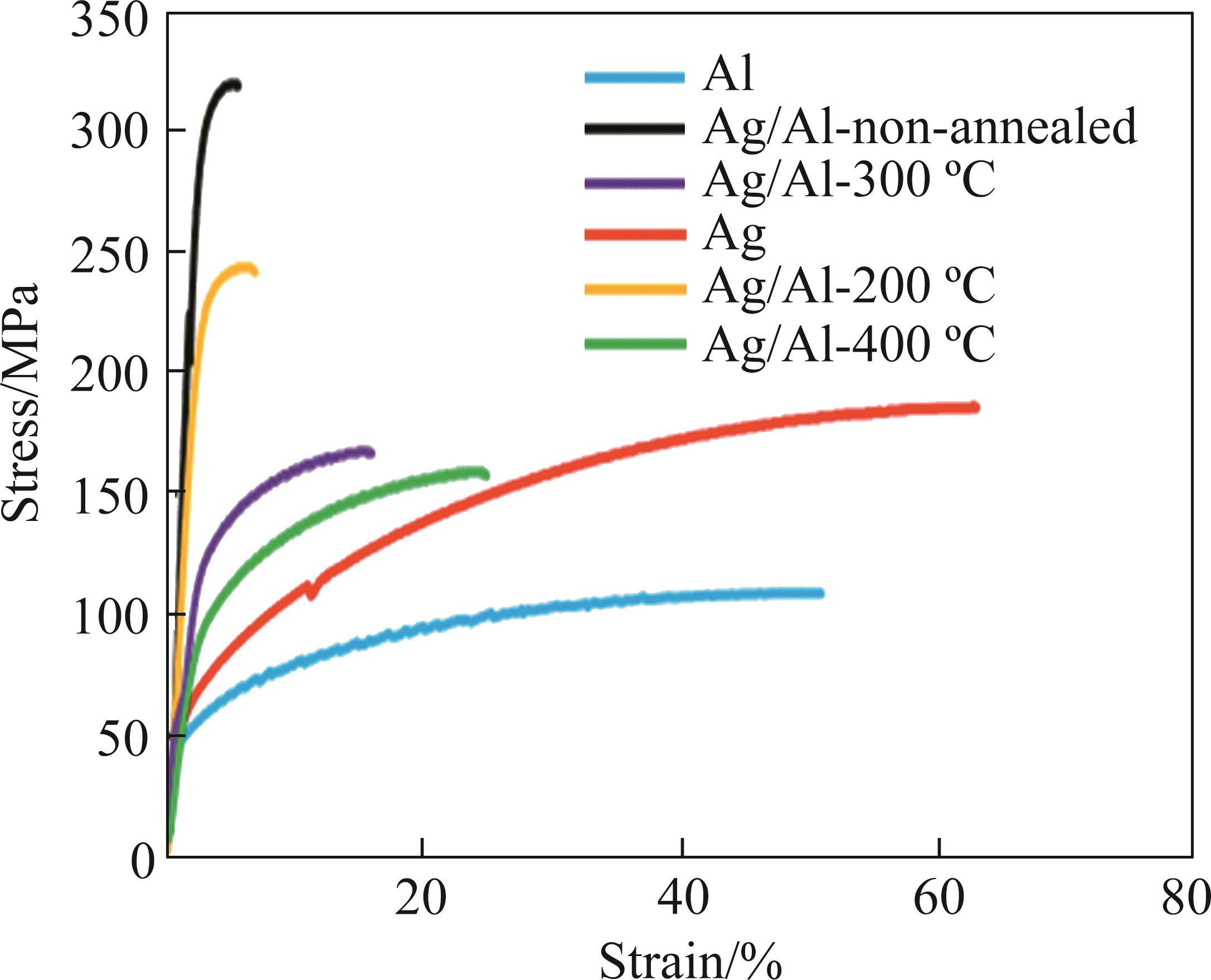
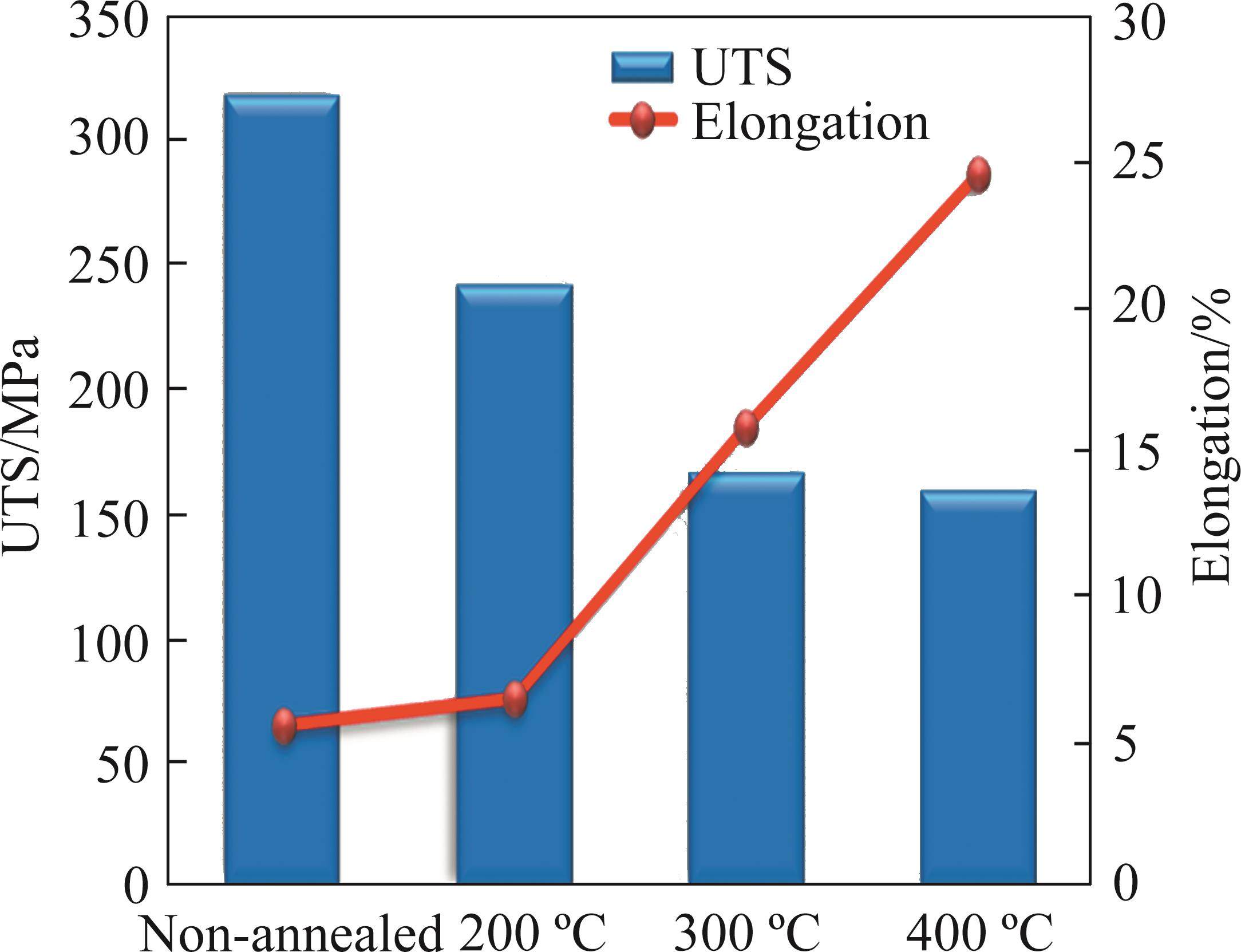
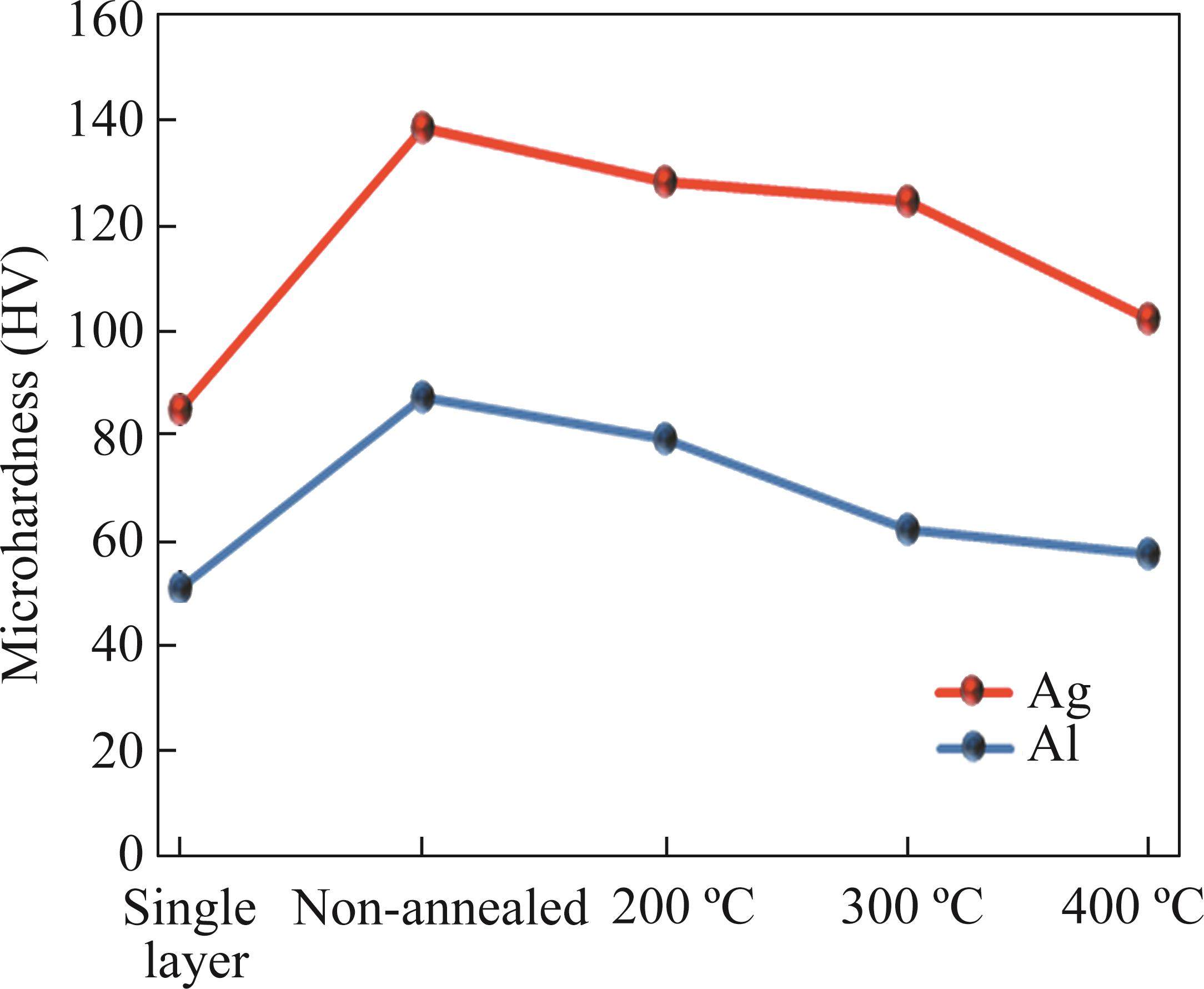
It is observed that annealing heat treatment and increasing its temperature reduce the amount of microhardness, but this decreasing trend is different for silver and aluminum layers. In the silver layer, the hardness drops relatively uniform up to 300 ℃, and at 400 ℃, a significant decrease is noticeable. Whereas for the aluminum layer, the greatest reduction in hardness in each annealing stage compared to the previous state occurs at 300 ℃. Therefore, it can be said that at temperatures above 300 ℃, partial recovery and recrystallization happens in the silver layer, while for the aluminum layer under these annealing conditions, fully recrystallization and growth of new grains occurs [65-68]. However, due to the high percentage of aluminum to silver in the Ag/Al bilayer sheet (thickness ratio of 3 to 0.5), the overall mechanical properties of the composite at different temperatures are affected by the behavior of the aluminum alloy. This claim can be obtained by comparing the results of microhardness and tensile test. In fact, 300 ℃ is the optimal annealing temperature; when at higher temperatures, UTS of the composite and microhardness of the aluminum layer does not change remarkably.
3.2 Fractography
Figure 7 shows the fracture surface of tensile test for as-received silver and aluminum specimens. The presence of dimples, which is the most important sign of ductile fracture, can be seen in both samples. However, it is clear that the number and depth of dimples in silver are greater than those of aluminum, which indicates a higher strain failure [13, 56].
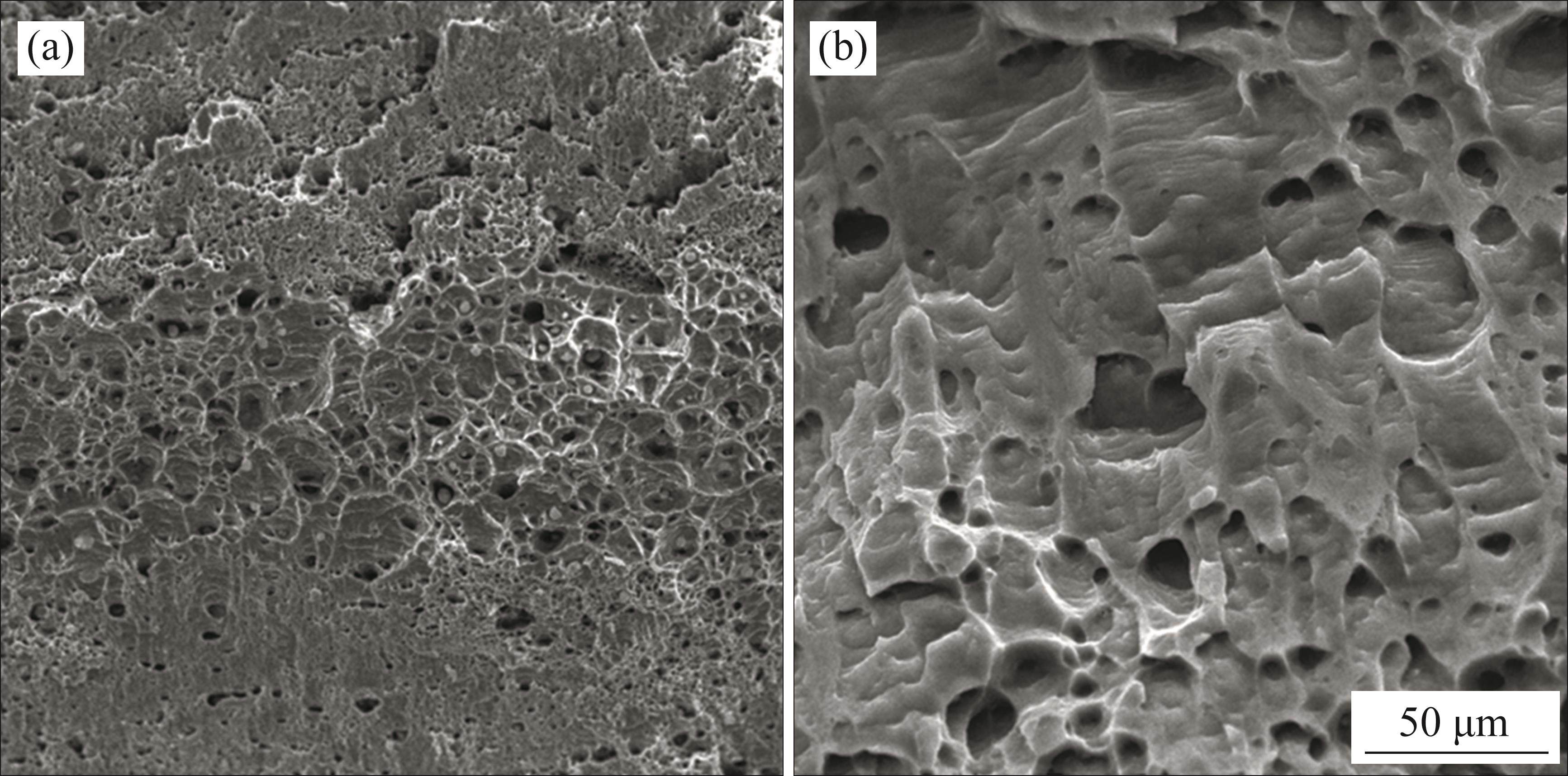
The effect of annealing heat treatment on the fracture surface of Ag/Al bilayer sheets produced by CRB process is shown in Figure 8. In non-annealed Ag/Al sheet, in addition to cavities and dimples, the flat surface in the silver layer is also clear, indicating brittle fracture [69, 70]. Therefore, it can be said that the fracture mechanism is shear ductile fracture. But in the sample annealed at 400 ℃, the fracture surface of the silver layer is full of dimples with different sizes and irregular shapes. Although areas with flat surfaces are also observed in this sample, its amount is much less than the sample without annealing. This evidence reveals that the ductile fracture mechanism is predominant in the annealed specimen, which requires higher deformation energy.
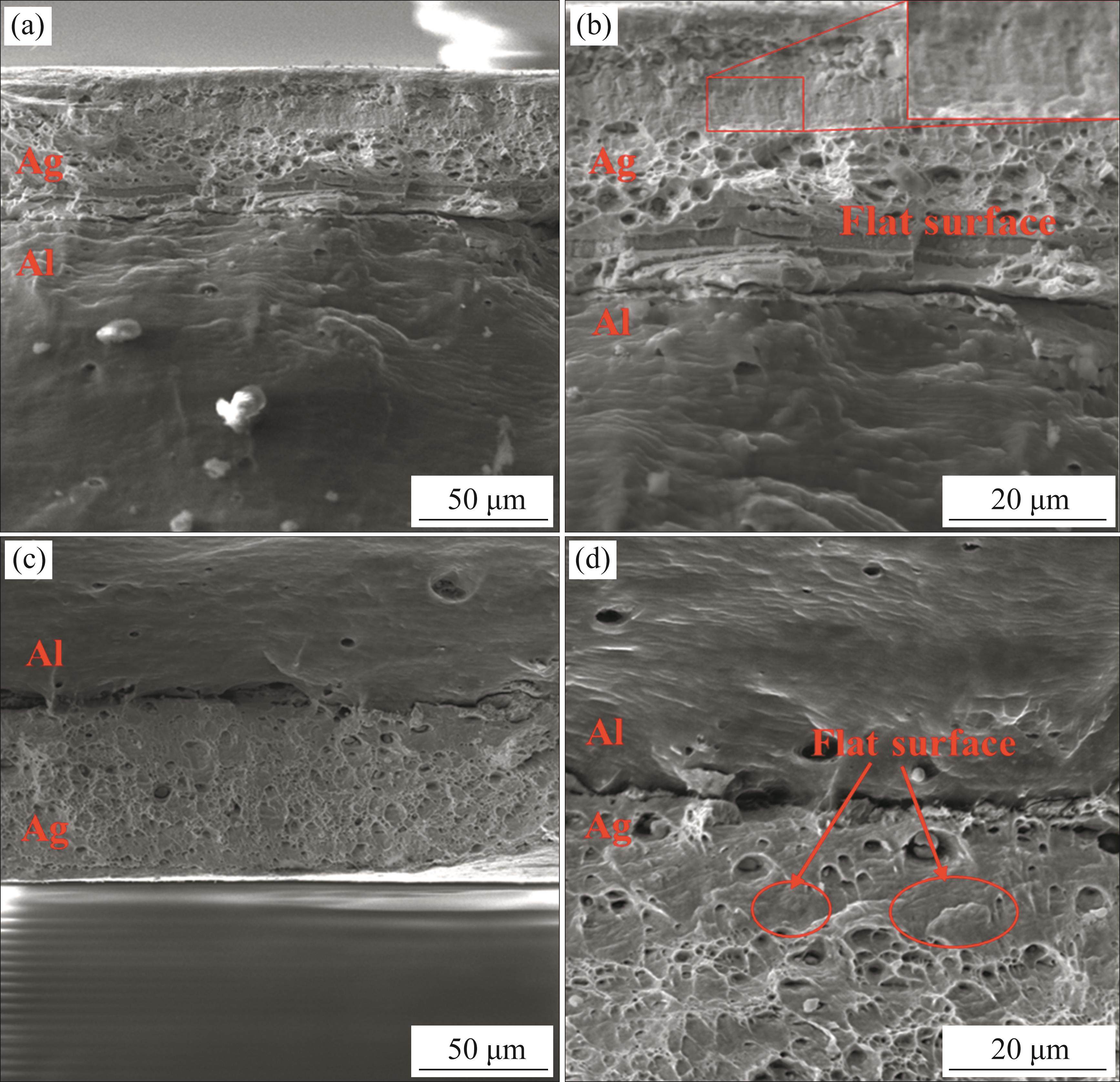
Further, the difference in volume fraction of the dimples formed in the annealed sample compared to the as-received silver sheet (Figure 7(b)) is significant, which represents the distinction in elongation of the two samples.
3.3 Fracture toughness test
In Figure 9, the force-displacement curve during fracture test can be seen for Ag/Al samples annealed under different conditions. All three curves contain a linear and ascending part to the maximum force at which crack growth occurs (Pmax) and then a sharp downward trend occurs until the point of rupture. These parts in the force-crack mouth opening of displacement (CMOD) diagram are related to the resistance of the material to crack growth in the elastic and plastic regions, respectively [53]. It is clear that after the elastic region and at the Pmax, first the crack mouth begins to deform and then cracks propagate and grow [71]. Based on Figure 9, the elastic region has the same slope for all three specimens, but the highest Pmax was obtained for the non-annealed sample (103 N). This phenomenon can be due to the increase of the dislocation density by cold work (increase in strength) [45, 50, 69]. The results also showed that Pmax for Ag/Al bilayer sheets annealed at 200, 300 and 400 ℃ was acquired 82.2, 63.2 and 52.7 N, respectively. Two reasons can be given to justify this fact: 1) Annealing heat treatment reduces the density of dislocations and tensile strength while increasing elongation. Given that the fracture toughness is affected by both strength and ductility parameters, it seems that the reduction of the UTS plays a key role in determining the Pmax of annealed specimens; 2) As the annealing temperature increases, the grain size of aluminum and silver increases, which increases the Pmax and, by its nature, the resistance to crack growth decreases [72]. After the fracture test, the crack growth rate at different time stages was determined by image processing software and Eqs. (1) and (2). The R-curves of Al/Ag bilayer sheets annealed at different temperatures are presented in Figure 10. Also, according to Figure 11, the maximum and minimum fracture toughness values were observed in non-annealed and annealed at 400 ℃ samples, respectively.
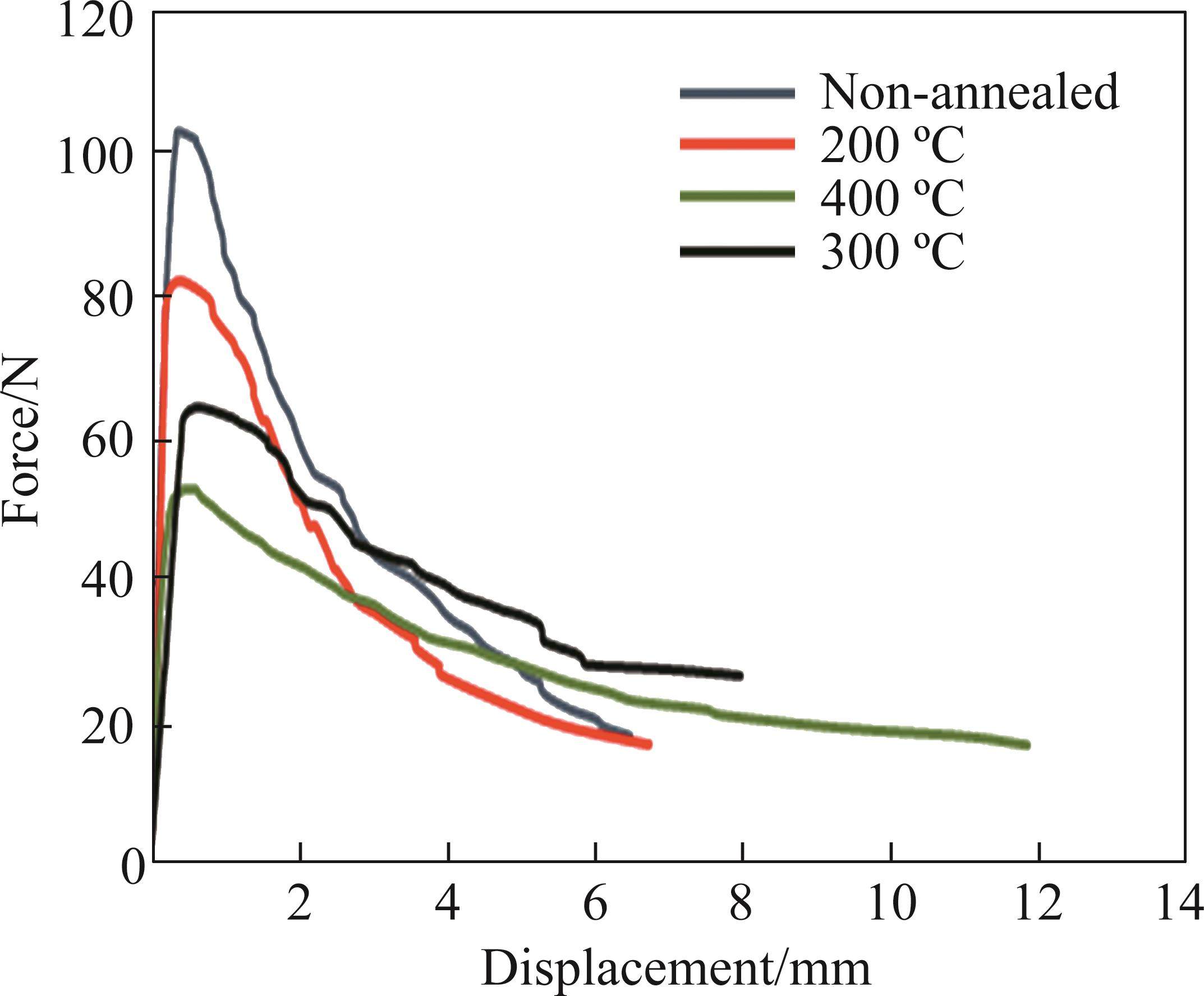
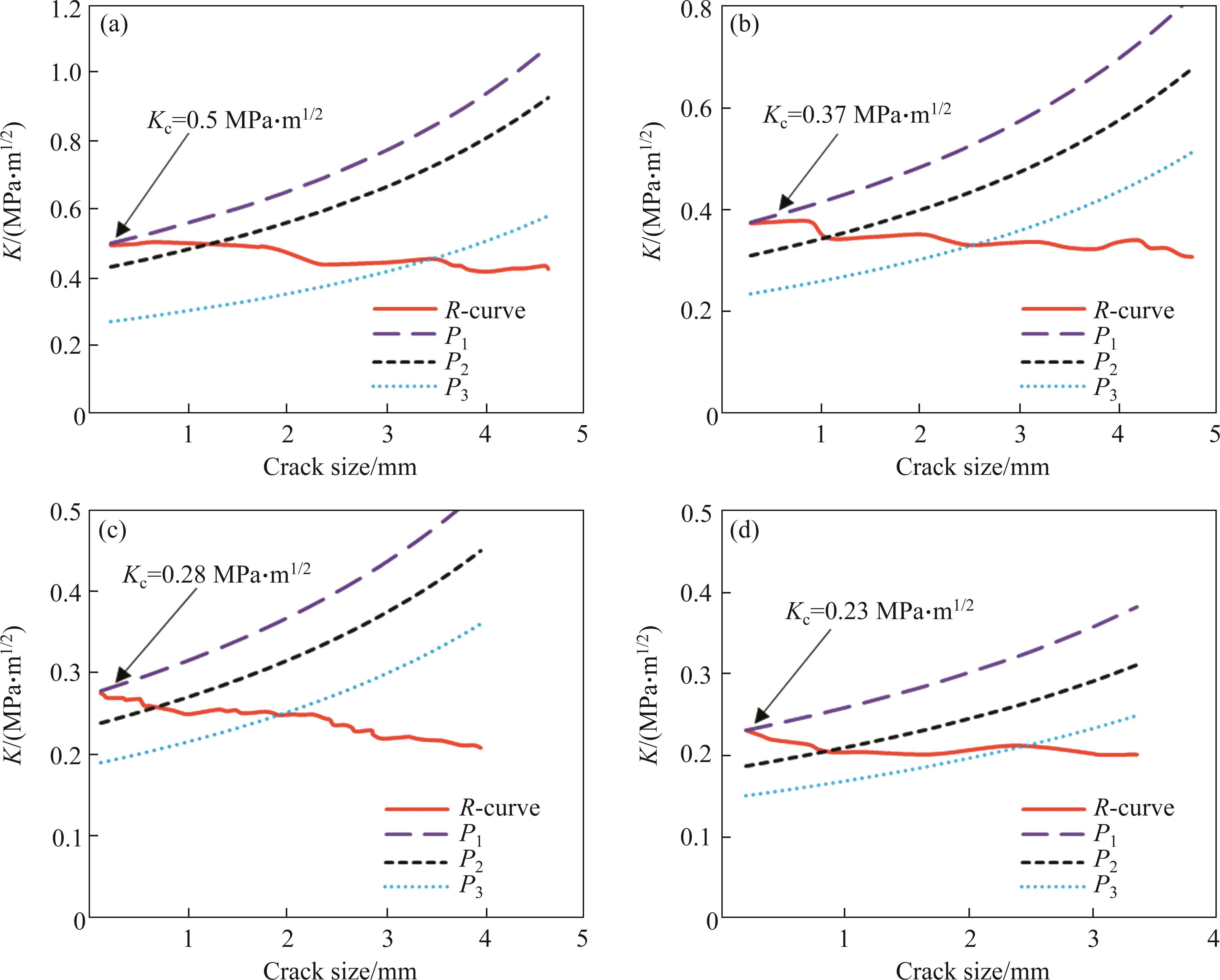
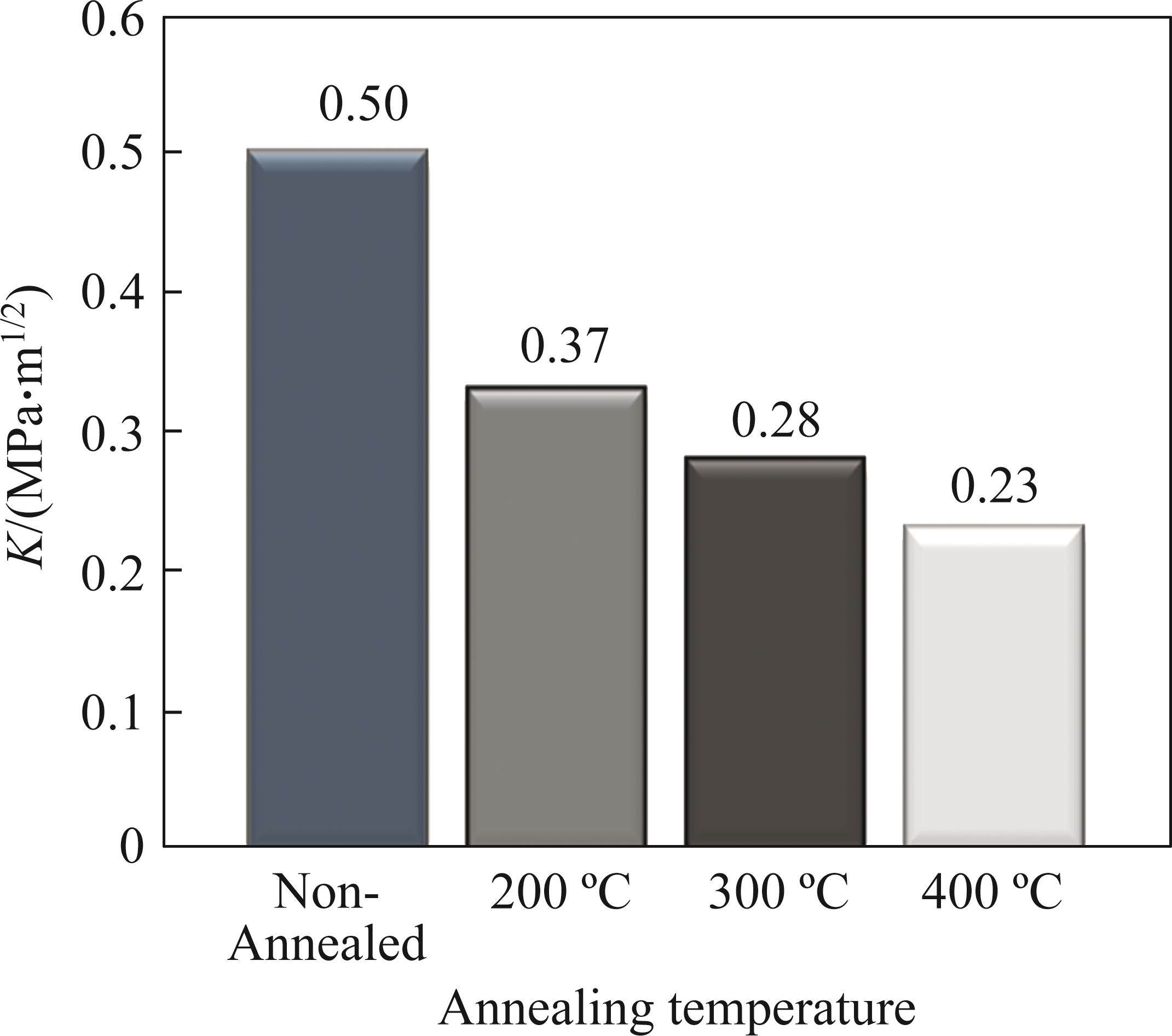
It is observed that the trend of changes in fracture toughness and tensile strength is similar for different annealing temperatures. However, the effect of annealing heat treatment on fracture toughness is greater than its temperature. The largest decrease occurred at 200 ℃, where the fracture toughness (Kc) dropped from 0.5 MPa‧m1/2 in the non-annealed state to 0.37 MPa‧m1/2 (26% reduction). Although many parameters are known to be effective in determining the fracture toughness of metallic materials [47], the decrease in strength and increase in elongation as a result of annealing is one of the most important reasons for the decline in fracture toughness of Ag/Al bilayer sheets compared to the non-annealed sample [45, 46, 73]. The results show that with increasing annealing temperature, the amount of fracture toughness decreases steadily.
3.4 Forming limit diagram
Figure 12 shows the forming limit diagram of Ag/Al bilayer sheets in annealed and non-annealed states. As can be seen, by annealing, the safe region (the upper part of the diagram) in FLC increases which indicates an improvement in the formability of the composite. So that annealing at 200 ℃ increased the FLC0 (the point where the major strain is zero) by 130%. This can be due to the elimination or reduction of work hardening created in the sheets after rolling, thus reducing dislocation density [38, 39]. Also, increasing the annealing temperature causes the FLC to shift upwards and have an ascending formability. However, the increase in ductility on the right side of the graph (major and minor strains >0) is more pronounced than on the left side (major strain >0, minor strain <0). Since annealing heat treatment at high temperatures is usually associated with recovery and recrystallization, softening and increased formability are expected in Ag/Al samples annealed at 300 and 400 ℃ [13]. According to Figure 12, at 300 ℃ the FLC0 experiences a sudden increase compared to 200 ℃ (34%); after that, at 400 ℃, not much change is observed at the surface below the forming limit diagram (about 13% increase in zero FLC0 compared to that at 300 ℃). However, annealing at 400 ℃ can improve FLC0 by more than 250% compared to non-annealed sample. According to the results and evidence obtained in the section of mechanical properties, it seems that the reason for this increase in formability at 300 ℃ is related to the recrystallization occurred in the aluminum layer. Upon an increase in temperature, sufficient internal energy for initiation of the recovery or recrystallization was generated. The combined effect of the recrystallization and recovery reduced the required stress for deformation. An increase in temperature reduced the internal stresses and strength, while increased the elongation and formability.
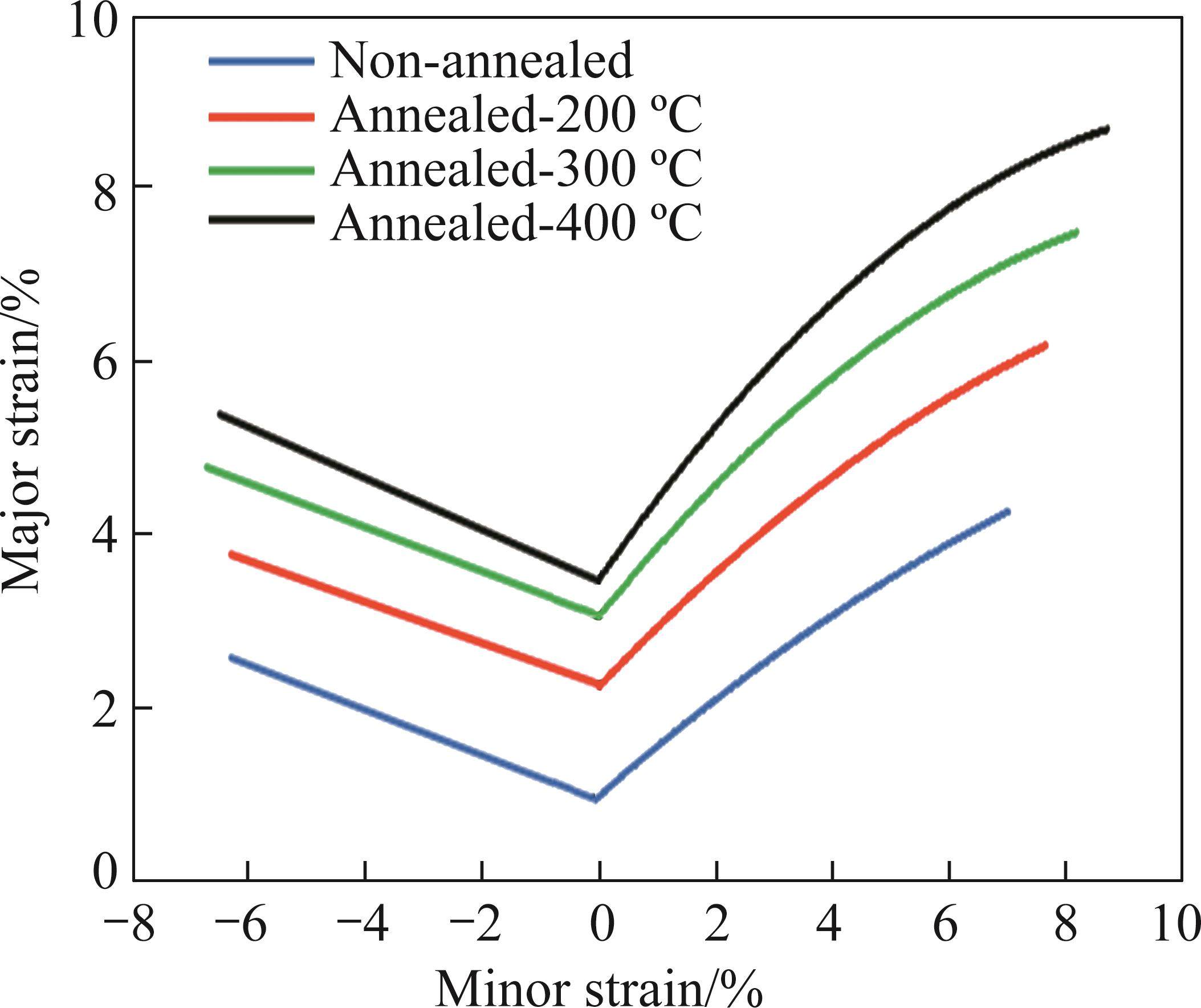
4 Conclusions
In this study, the mechanical properties, fracture toughness behavior and formability of Ag/Al bilayer sheet were evaluated by considering the effect of post annealing temperature, and the most important results are obtained as follows.
1) After CRB, the tensile strength of the bilayer sheets increases significantly while the amount of elongation decreases due to strain hardening and increasing dislocations density. Annealing heat treatment can cause the phenomenon of recrystallization and recovery in the layers, as a result of which softening occurs. So that the UTS for rolled and annealed samples at 200, 300 and 400 ℃ was obtained 318, 242, 167 and 159 MPa, respectively.
2) The results of microhardness test show that increasing the annealing temperature reduces the hardness, but this decreasing trend is not the same in the whole temperature range. The greatest effect of temperature on hardness for aluminum and silver layers occurs at 300 and 400 ℃, respectively. Since aluminum makes up more than 85% of the volume of the composite, 300 ℃ can be introduced as the critical temperature at which most changes in mechanical properties occur.
3) The trend of changes in fracture toughness and tensile strength is similar for different annealing temperatures. The maximum fracture toughness
for non-annealed state and sample annealed at 400 ℃ was determined 0.5 and 0.23
4) Annealing heat treatment and increasing its temperature improves the formability behavior of Ag/Al bilayer sheets. The results showed that annealing at 400 ℃ can improve FLC0 by more than 250% compared to non-annealed sample, which is considered a valuable achievement.
High-strength and high-conductive Cu/Ag multilayer produced by ARB
[J]. Journal of Alloys and Compounds, 2010, 506(1): 172-178. DOI: 10.1016/j.jallcom.2010.06.172.Microstructure and mechanical properties of the Ag/316L composite plate fabricated by explosive welding
[J]. Journal of Manufacturing Processes, 2021, 64: 265-275. DOI: 10.1016/j.jmapro.2021.01.026.Bimetal production and applications
[J]. Steel in Translation, 2011, 41(9): 778-786. DOI:10.3103/S09670 9121109004X.Mechanical properties of Cu/Ag multilayered composites
[J]. Materials Science and Engineering A, 1998, 255(1, 2): 20-32. DOI: 10.1016/S0921-5093(98)00788-6.Effects of rolling and sintering temperature on peel strength of bonding interfaces for Ag/Cu bimetallic strips
[J]. Materials Science and Technology, 2003, 19(6): 779-784. DOI: 10.1179/026708 303225002785.High strength, high electrical conductivity and thermally stable bulk Cu/Ag nanolayered composites prepared by cross accumulative roll bonding
[J]. Materials & Design, 2021, 200: 109455. DOI: 10.1016/j.matdes.2021.109455.Behaviors of the interface and matrix for the Ag/Cu bimetallic laminates prepared by roll bonding and diffusion annealing
[J]. Materials Science and Engineering A, 2004, 371(1, 2): 65-71. DOI: 10.1016/S0921-5093(03)00626-9.Preparation of microstructured and nanostructured magnetic materials by mechanical deformation
[J]. Journal of Magnetism and Magnetic Materials, 2002, 242: 581-584. DOI: 10.1016/S03 04-8853(01)01114-3.Formation of nanoscale Fe/Ag multilayer by repeated press-rolling and its layer thickness dependence of magnetoresistance
[J]. Materials Science and Engineering A, 2000, 285(1, 2): 412-417. DOI: 10.1016/S0921-5093(00)00680-8.Evolution of microstructures and properties leading to layer instabilities during accumulative roll bonding of FeCu, FeAg, and FeAl
[J]. Materials & Design, 2021, 212: 110204. DOI: 10.1016/j.matdes.2021.110204.Control of layer continuity in metallic multilayers produced by deformation synthesis method
[J]. Materials Science and Engineering A, 2005, 406(1, 2): 95-101. DOI: 10.1016/j.msea.2005.06.030.An investigation of Au-Ag interface formed by cold welding using focused ion beam/transmission electron microscopy
[J]. MRS Online Proceedings Library, 2006, 965(1): 1206. DOI: 10.1557/PROC-0965-S12-06.The effect of temperature on the mechanical properties and forming limit diagram of aluminum strips fabricated by accumulative roll bonding process
[J]. Journal of Materials Research and Technology, 2020, 9(2): 1831-1846. DOI: 10.1016/j.jmrt. 2019.12.016.Using cold roll bonding and annealing to process Ti/Al multi-layered composites from elemental foils
[J]. Materials Science and Engineering A, 2004, 379(1, 2): 164-172. DOI: 10.1016/j.msea.2004.01.021.Interfacial conditions and bond strength in cold pressure welding by rolling
[J]. Metals Technology, 1978, 5(1): 24-31. DOI: 10.1179/mt. 1978.5.1.24.Progress in cold roll bonding of metals
[J]. Science and Technology of Advanced Materials, 2008, 9(2):The effects of oxide film and annealing treatment on the bond strength of Al–Cu strips in cold roll bonding process
[J]. Materials & Design, 2014, 53: 174-181. DOI: 10.1016/j.matdes.2013.06.028.Cold roll bonding bond strengths: Review
[J]. Materials Science and Technology, 2011, 27(7): 1101-1108. DOI: 10.1179/02670 8310x12815992418256.Effects of processing parameters on the bond strength of Cu/Cu roll-bonded strips
[J]. Journal of Materials Processing Technology, 2010, 210(3): 560-563. DOI: 10.1016/j.jmatprotec.2009.11.003.Investigation of roll bonding between aluminum alloy strips
[J]. Materials & Design, 2008, 29(4): 909-913. DOI: 10. 1016/j.matdes.2007.03.020.The influence of roll bonding parameters on the bond strength of Al-3003/Zn soldering sheets
[J]. Materials Science and Engineering A, 2008, 487(1, 2): 417-423. DOI: 10.1016/j.msea.2007.10.019.Mechanism of warm and cold roll bonding of aluminum alloy strips
[J]. Materials & Design, 2009, 30(10): 4156-4161. DOI: 10.1016/j.matdes.2009.04.036.Effect of rolling temperature on interface and bond strength development of roll bonded copper/aluminium metal laminates
[J]. Journal of Materials Science, 1999, 34(2): 277-281. DOI: 10.1023/A:1004497304095.Effect of friction, annealing conditions and hardness on the bond strength of Al/Al strips produced by cold roll bonding process
[J]. Materials & Design, 2010, 31(9): 4508-4513. DOI: 10.1016/j.matdes. 2010.04.022.Effects of annealing on the interfacial structures and mechanical properties of hot roll bonded Al/Mg clad sheets
[J]. Materials Science and Engineering A, 2020, 792: 139673. DOI: 10. 1016/j.msea.2020.139673.Effect of heat treatment on the bending behavior of tri-layered Cu/Al/Cu composite plates
[J]. Materials & Design, 2013, 47: 590-598. DOI: 10.1016/j.matdes.2012.12.070.Diffusion annealing of copper–silver bimetallic strips at different temperatures
[J]. Materials Characterization, 2001, 47(3, 4): 269-274. DOI: 10.1016/S1044-5803(01)00182-6.Microstructure and elemental distribution of multicrystal Ag/Cu interface in bimetallic strips with diffusion treatment
[J]. Materials Research Bulletin, 2001, 36(9): 1729-1735. DOI: 10.1016/S0025-5408(01)00649-3.Rail surface spot irregularity effects in vehicle-track interaction simulations of train-track-bridge interaction
[J]. Journal of Vibration and Control, 2024: 10775463241232024. DOI: 10.1177/10775463241232024.Statistical evaluation of forming limit diagram for annealed Al1350 alloy sheets using first order reliability method
[J]. Applied Mathematical Modelling, 2014, 38(1): 145-167. DOI: 10.1016/j.apm.2013.05.050.Effect of annealing on formability of aluminium grade 19000
[J]. Materials & Design, 2008, 29(8): 1633-1653. DOI: 10.1016/j.matdes.2006.12.019.A crystallographic texture perspective formability investigation of aluminium 5052 alloy sheets at various annealing temperatures
[J]. Materials & Design, 2009, 30(5): 1804-1817. DOI: 10.1016/j.matdes.2008.09.011.Effect of annealing on combined forming, fracture and wrinkling limit diagram of aluminium 5086 alloy sheets
[J]. International Journal of Mechanics and Materials in Design, 2008, 4(1): 31-43. DOI: 10.1007/s10999-007-9052-0.Forming limit analysis for two-stage forming of 5182-O aluminum sheet with intermediate annealing
[J]. International Journal of Plasticity, 2013, 45: 21-43. DOI:10.1016/j.ijplas.2012.10.004.Novel ultra-high straining process for bulk materials: Development of the accumulative roll-bonding (ARB) process
[J]. Acta Materialia, 1999, 47(2): 579-583. DOI:10.1016/S1359-6454(98)00365-6.A real-time 3D scanning of aluminum 5052-H32 laser welded blanks: Geometrical and welding characterization
[J]. Materials Letters, 2021, 296: 129883. DOI:10.1016/j.matlet.2021.129883.Multi-objective topology optimization of deep drawing dissimilar tailor laser welded blanks: Experimental and finite element investigation
[J]. Optics & Laser Technology, 2020, 125: 106029. DOI:10.1016/j.optlastec.2019.106029.Formability of ultrafine grained metals produced by severe plastic deformation-An overview
[J]. Advanced Engineering Materials, 2019, 21(1): 1800316. DOI: 10.1002/adem.201800316.Optical measurement of forming limitand formability of Cu/Al clad metals
[J]. Journal of Materials Engineering and Performance, 2015, 24(4): 1426-1433. DOI: 10.1007/s116 65-015-1435-z.Effect of annealing on formability and mechanical properties of AA1050/Mg-AZ31B bilayer sheets fabricated by explosive welding method
[J]. The International Journal of Advanced Manufacturing Technology, 2022, 118(3): 775-784. DOI: 10. 1007/s00170-021-07999-z.The influence of post-annealing and ultrasonic vibration on the formability of multilayered Al5052/MgAZ31B composite
[J]. Materials Science and Technology, 2021, 37(1): 78-85. DOI: 10.1080/02670836.2020.1867784.Bond strength and formability of an aluminum-clad steel sheet
[J]. Journal of Alloys and Compounds, 2003, 361(1, 2): 138-143. DOI: 10.1016/s0925-8388(03)00392-x.On the fracture toughness of advanced materials
[J]. Advanced Materials, 2009, 21(20): 2103-2110. DOI: 10.1002/adma.200803322.Modulating fracture toughness through processing-mediated mesostructure in additively manufactured Al-12Si alloy
[J]. Materials & Design, 2022, 215: 110440. DOI: 10.1016/j.matdes.2022.110440.The role of applied strain and volume percentage of components on mechanical properties and fracture toughness in multilayered Al/Mg composite fabricated by the accumulative roll bonding process
[J]. Materials Research Express, 2021, 8(2):Experimental evaluation of the plane stress fracture toughness for ultra-fine grained aluminum specimens prepared by accumulative roll bonding process
[J]. Materials Science and Engineering A, 2017, 708: 301-310. DOI: 10. 1016/j.msea.2017.09.085.The role of thickness on the fracture behavior of Al/Mg-Li/Al composite processed by cold roll bonding
[J]. Materials Science and Engineering A, 2021, 824: 141851. DOI: 10.1016/j.msea.2021.141851.A comprehensive study on the effect of heat treatment on the fracture behaviors and structural properties of Mg-Li alloys using RSM
[J]. Materials Research Express, 2019, 6(7):Investigation of the parameters of the cold roll bonding (CRB) process
[J]. Materials Science and Engineering A, 2010, 527(9): 2320-2326. DOI: 10.1016/j.msea.2009.11.069.Crack propagation and fracture toughness of Ti6Al4V alloy produced by selective laser melting
[J]. Additive Manufacturing, 2015, 5: 68-76. DOI: 10.1016/j.addma. 2014.12.006.Evaluation of fracture toughness and rupture energy absorption capacity of as-rolled LZ71 and LZ91 Mg alloy sheet
[J]. Materials Research Express, 2019, 6(3):Fracture toughness investigation of Al1050/Cu/MgAZ31ZB multi-layered composite produced by accumulative roll bonding process
[J]. Materials Science and Engineering A, 2018, 734: 427-436. DOI: 10.1016/j.msea.2018.08.017.Instability and localization of plastic flow in shear at high strain rates
[J]. Journal of the Mechanics and Physics of Solids, 1987, 35(2): 185-211. DOI: 10.1016/0022-5096(87)90035-4.Experimental and theoretical formability analysis using strain and stress based forming limit diagram for advanced high strength steels
[J]. Materials & Design, 2013, 51: 756-766. DOI: 10.1016/j.matdes.2013.04.080.Finite element and experimental method for analyzing the effects of martensite morphologies on the formability of DP steels
[J]. Mechanics Based Design of Structures and Machines, 2020, 48(5): 525-541. DOI: 10.1080/15397734.2019.1633343.The effect of temperature on the mechanical properties and forming limit diagram of Al5083 produced by equal channel angular rolling
[J]. The International Journal of Advanced Manufacturing Technology, 2019, 105(10): 4389-4400. DOI: 10.1007/s00170-019-04586-1.On the microstructure, texture and mechanical properties through heat treatment in Al-CuO nanocomposite fabricated by Accumulative Roll Bonding (ARB)
[J]. Materials Science and Engineering A, 2021, 828: 142080. DOI: 10.1016/j.msea.2021.142080.Influence of rolling temperature on microstructural evolution and mechanical behavior of AZ31 alloy with accumulative roll bonding
[J]. Materials Science and Engineering A, 2019, 754: 112-120. DOI: 10.1016/j.msea.2019.03.047.Study of mechanical properties and wear resistance of Al1050/Brass (70/30)/Al1050 composite sheets fabricated by the accumulative roll bonding process
[J]. Journal of Manufacturing Processes, 2021, 71: 407-416. DOI: 10.1016/j.jmapro.2021.09.032.Nano/ultrafine grained AA2024 alloy processed by accumulative roll bonding: A study of microstructure, deformation texture and mechanical properties
[J]. Journal of Alloys and Compounds, 2017, 712: 517-525. DOI: 10.1016/j.jallcom. 2017.04.117.Effect of annealing on microstructure and tensile properties of 5052/AZ31/5052 clad sheets
[J]. JOM, 2016, 68(5): 1282-1292. DOI: 10.1007/s11837-015-1755-3.Annealing behavior of nanostructured aluminum produced by cold rolling to ultrahigh strains
[J]. Metallurgical and Materials Transactions A, 2009, 40(1): 204-214. DOI: 10.1007/s11661-008-9678-z.Effect of concurrent accumulative roll bonding (ARB) process and various heat treatment on the microstructure, texture and mechanical properties of AA1050 sheets
[J]. Journal of Materials Research and Technology, 2022, 18: 1295-1306. DOI: 10.1016/j.jmrt.2022.03.001.Effects of grain size and dislocation density on strain hardening behavior of ultrafine grained AA1050 processed by accumulative roll bonding
[J]. Journal of Alloys and Compounds, 2016, 658: 854-861. DOI: 10.1016/j.jallcom. 2015.11.032.Microstructure and mechanical properties of ultra-fine grains (UFGs) aluminum strips produced by ARB process
[J]. Journal of Alloys and Compounds, 2009, 474(1, 2): 406-415. DOI: 10.1016/j.jallcom.2008.06.161.Mechanical behavior, deformation mechanism and microstructure evolutions of ultrafine-grained Al during recovery via annealing
[J]. Materials Science and Engineering A, 2020, 772: 138706. DOI: 10.1016/j.msea.2019.138706.Effect of heat treatment on hot deformation behavior and microstructure evolution of 2195 Al-Li alloy
[J]. Journal of Central South University, 2023, 30(5): 1417-1434. DOI: 10. 1007/s11771-023-5337-1.Design of friction stir welding for butt joining of aluminum to steel of dissimilar thickness: Heat treatment and fracture behavior
[J]. The International Journal of Advanced Manufacturing Technology, 2021, 112(7): 1951-1964. DOI: 10.1007/s00170-020-06406-3.Mechanical properties and microstructure evolutions of multilayered Al-Cu composites produced by accumulative roll bonding process and subsequent annealing
[J]. Materials Science and Engineering A, 2014, 601: 40-47. DOI: 10.1016/j.msea.2014.02.023.Effect of equal channel angular pressing on fracture toughness of Al-7075
[J]. Engineering Failure Analysis, 2016, 65: 1-10. DOI: 10.1016/j.engfailanal.2016.03.010.Structural, mechanical and corrosion evaluations of Cu/Zn/Al multilayered composites subjected to CARB process
[J]. Journal of Alloys and Compounds, 2021, 867: 158973. DOI: 10.1016/j.jallcom.2021.158973.DIC-based experimental study of fracture toughness through R-curve tests in a multi-layered Al-Mg (LZ91) composite fabricated by ARB
[J]. Journal of Alloys and Compounds, 2021, 883: 160843. DOI: 10.1016/j.jallcom.2021.160843.Effect of equal channel angular pressing on the fracture behavior of commercially pure titanium
[J]. Metallurgical and Materials Transactions A, 2010, 41(3): 727-733. DOI: 10.1007/s11661-009-0111-z.Fracture toughness in Mg-Al-Zn alloy processed by equal-channel-angular extrusion
[J]. Scripta Materialia, 2006, 54(4): 633-638. DOI: 10.1016/j.scriptamat.2005.10.029.Influence of ARB technique on the microstructural, mechanical and fracture properties of the multilayered Al1050/Al5052 composite reinforced by SiC particles
[J]. Journal of Materials Research and Technology, 2019, 8(5): 4287-4301. DOI: 10.1016/j.jmrt.2019.07.039.Experimental investigation of strain path effects on mechanical properties, forming limit curves, and texture evolution of AA1050 aluminum sheet
[J]. Journal of Central South University, 2023, 30(8): 2472-2484. DOI: 10.1007/s11771-023-5396-3.The effect of annealing on the formability of aluminum 1200 after accumulative roll bonding
[J]. Journal of Manufacturing Processes, 2017, 30: 241-254. DOI: 10.1016/j.jmapro.2017.09.013.Mohammad Delshad GHOLAMI, Mojtaba KHODAKARAMI, Mohammad ABADIAN and Ramin HASHEMI declare that they have no conflict of interest.
Mohammad Delshad GHOLAMI, Mojtaba KHODAKARAMI, Mohammad ABADIAN, Ramin HASHEMI. Annealing temperature influence on forming limit curve and fracture toughness of aluminium/silver bilayer sheets [J]. Journal of Central South University, 2025, 32(1): 34-48. DOI: https://doi.org/10.1007/s11771-025-5870-1.