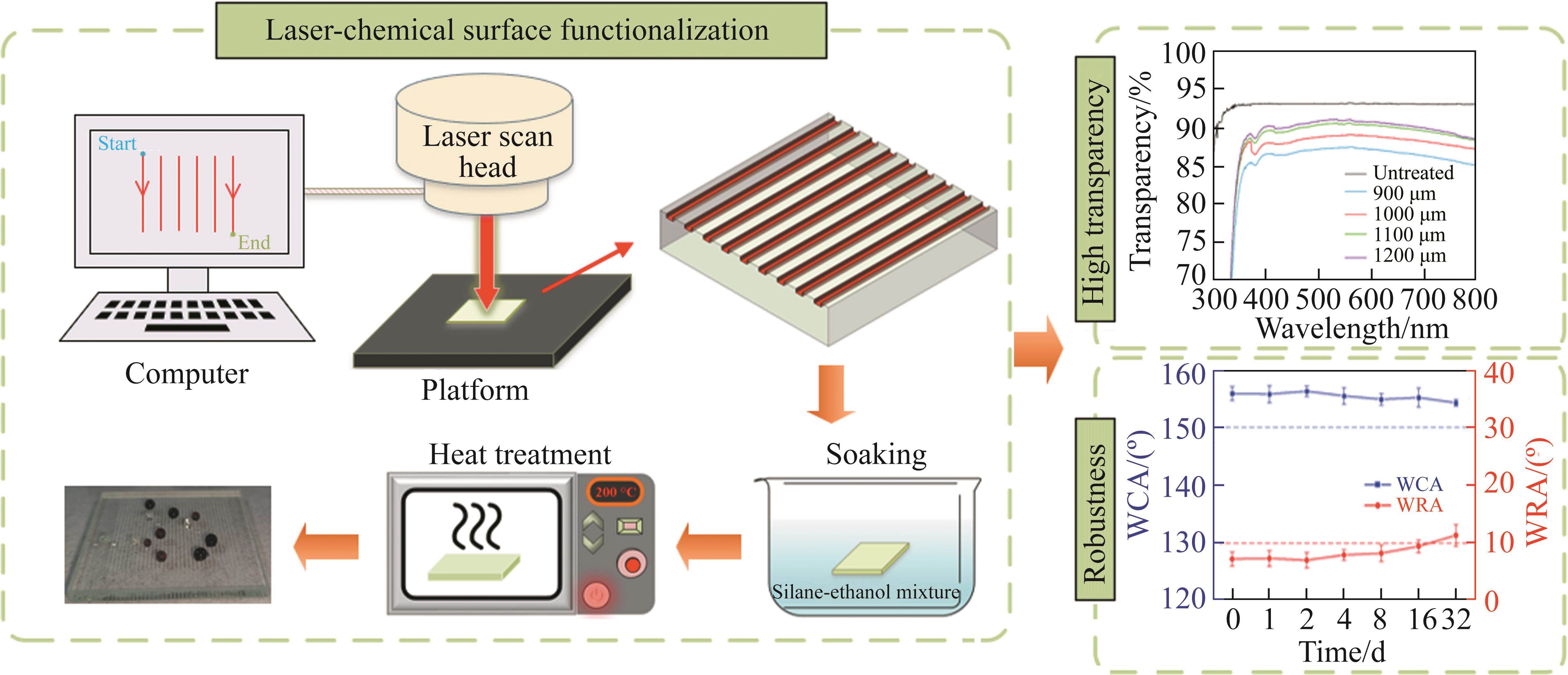
1 Introduction
Silica glass is regarded as an important industrial material with excellent physical and chemical stability and corrosion resistance. It is widely applied in optical sensors [1], transistors [2], solar panels [3] and other photoelectric fields. Fabrication of aviation insulation, glass products and vehicle glass can also be effectively realized due to high temperature resistance, high melting point characteristics and low expansion coefficient of glass material. However, when glass is used in medical devices such as endoscopes, the blood and contaminants in the human body tend to adhere to the surface on account of the intrinsic hydrophilicity of the glass surface [4, 5]. The image observation and equipment service life will be affected and the cost will be significantly increased. Moreover, the solar panel equipped with the glass is likely to absorb pollution such as dust in the air and the energy collection efficiency will be reduced [6]. It is also often frozen in rain and snow, which also affects its applications. In order to solve these problems, superhydrophobic strategies inspired by natural organisms have been regarded as an effective way [7-11]. The droplets can quickly roll off the surface and carry away surface contamination on the superhydrophobic glass surface. This phenomenon provides a potential reference for the better application of glass in industrial equipment.
As is well-known, in order to achieve superhydrophobicity of the surface, it is necessary to ensure that hierarchical micro/nanostructure with graded roughness and chemical property with low-surface energy are realized on the surface [12-15]. This hierarchical micro/nanostructure can be effectively induced on materials such as metals or ceramics [16, 17]. For the glass surface with high transparency requirements, the surface roughness will be significantly increased by the micro/nanostructure [18]. According to Mie scattering theory [19], the surface scattering will be increased and the surface transparency will be decreased on the microscopic scale due to the increased surface roughness. The application of glass materials can be obviously limited by the large loss of surface transparency. To alleviate the contradiction between the surface micro/nanostructure and transparency, many attempts have been carried out by researchers. LI et al [20] considered the relationship between the volume and surface properties of the coating material and the surface transparency. The nanoscale porous structures assembled by silica nanoparticles were prepared on the glass substrate. Because the pores in the nanoporous structure can retain a large amount of air with a tiny roughness, 90% of the transparency and superhydrophobicity can be displayed on the glass surface. ZHAO et al [21] prepared superhydrophobic glass by coating a ZnO/epoxy resin solution onto the surface. The effect of superhydrophobic coating position on the floating state and load bearing capacity of glass was studied. This superhydrophobic glass surface showed high transparency and marvelous drag reduction efficiency, providing relevant strategies for enhancing buoyancy and reducing drag. Although the above-mentioned coating methods achieve superhydrophobicity on glass surfaces with high transparency, these coatings frequently present durability and stability problems due to the low adhesion of the coating to the substrate surface [22, 23]. Therefore, there is an urgent need for more potential methods to obtain highly transparent and robust superhydrophobic glass.
Laser surface texturing has become a new technology for the fabrication of superhydrophobic surfaces because of its high machining precision, high controllability and non-contact characteristic [24-29]. In particular, the micro/nanostructure can be induced on almost any material surface by laser beam to realize surface modification [30, 31]. In contrast to additive manufacturing, the changing process of surface morphology caused by laser beam is irreversible and belongs to the reduction manufacturing, which contributes to the stability and durability of surface modification. This stable superhydrophobicity is also suitable for surface modification of glass material. At present, laser texturing technology has been widely applied by many researchers to fabricate highly transparent and robust superhydrophobic glasses. LEE et al [32] used femtosecond laser to ablate the surface of endoscope lens line by line and chemically modified it with fluorinated self-assembled monolayer and perfluorocarbon lubricant. The liquid repellent surface with transparency of more than 70% was successfully prepared. The directly carved micro/nanostructure provides excellent mechanical robustness to the lens, allowing it to maintain clear visibility throughout typical procedures. LIN et al [19] textured distributed period micro-pits with self-organized micro/nano rods, nano-ripples and nanoparticle by using femtosecond laser on the surface of silica glass, and coated the surface with a layer of fluoroalkyl silane molecules to achieve great superhydrophobicity (contact angle of 161° and roll-off angle of 2°). The surface transparency of laser-textured glass is as high as 92% due to sufficient unprocessed areas. This highly transparent superhydrophobic glass also has excellent impact resistance and thermal stability. LI et al [33] induced micro/nanostructures on the glass substrate by the combination of picosecond laser texturing and imprinting. The prepared superhydrophobic glass surface has remarkable temperature resistance and stability under high temperature, acid-base and friction environment. Simultaneously, high transparency can be maintained on the glass surface due to the SiO2 nanoparticles laid on the mold. However, most of the above-mentioned laser texturing processes are quite expensive and less efficient under the action of femtosecond or picosecond lasers. The researches on the fabrication of highly transparent and robust superhydrophobic glass by typical facile nanosecond laser are still to be explored.
In this work, a UV nanosecond laser is applied to fabricate the superhydrophobic glass surface. The hierarchical micro/nanostructure is induced on the glass surface by laser beam, and the laser-textured surface is modified by silane solution to realize extreme wettability. Meanwhile, the surface morphology, chemical composition and wettability of the glass before and after laser texturing are evaluated by characterization equipment. The transparency and robustness of superhydrophobic glass surface is investigated by the light transmission test, durability test and stability test. The superhydrophobic glass prepared by the laser-chemical surface functionalization (LCF) method is expected to provide a potential reference for the industrial applications of highly transparent glass.
2 Materials and methods
2.1 Materials
In this work, glass materials consisting mainly of silica are cut into 15 mm×15 mm×2 mm and 30 mm×30 mm×2 mm samples. Before laser texturing, all samples are ultrasonically cleaned in anhydrous ethanol for 5 min to remove surface contaminants, and then dried and stored in air for study. The silane solution used in the post-treatment process is 1H,1H,2H,2H-C16H19F17O3Si (AIKON, Nanjing), and the anhydrous ethanol solution (Meryer, Shanghai) is HPLC grade with a concentration of 99.8%.
2.2 Laser-chemical surface functionalization of superhydrophobic glass
The glass surfaces are pretreated by laser texturing, and the processing route and flow are shown in Figure 1. The relevant processing parameters are listed in Table 1. The whole process of laser texturing is carried out in the air environment, and the focused beam is emitted by laser scan head controlled by computer software. The glass surface is scanned by laser beam in a palisade path to induce periodic grooves and micro/nanostructures on the surface. In the post-treatment process, the glass surface textured by laser beam is immersed in a mixture of silane and ethanol with a volume fraction of 1: 50 for 2 h. It is then heated in an oven at 200 ℃ for 0.5 h. Eventually, the wettability of the glass surface can be turned into superhydrophobicity.
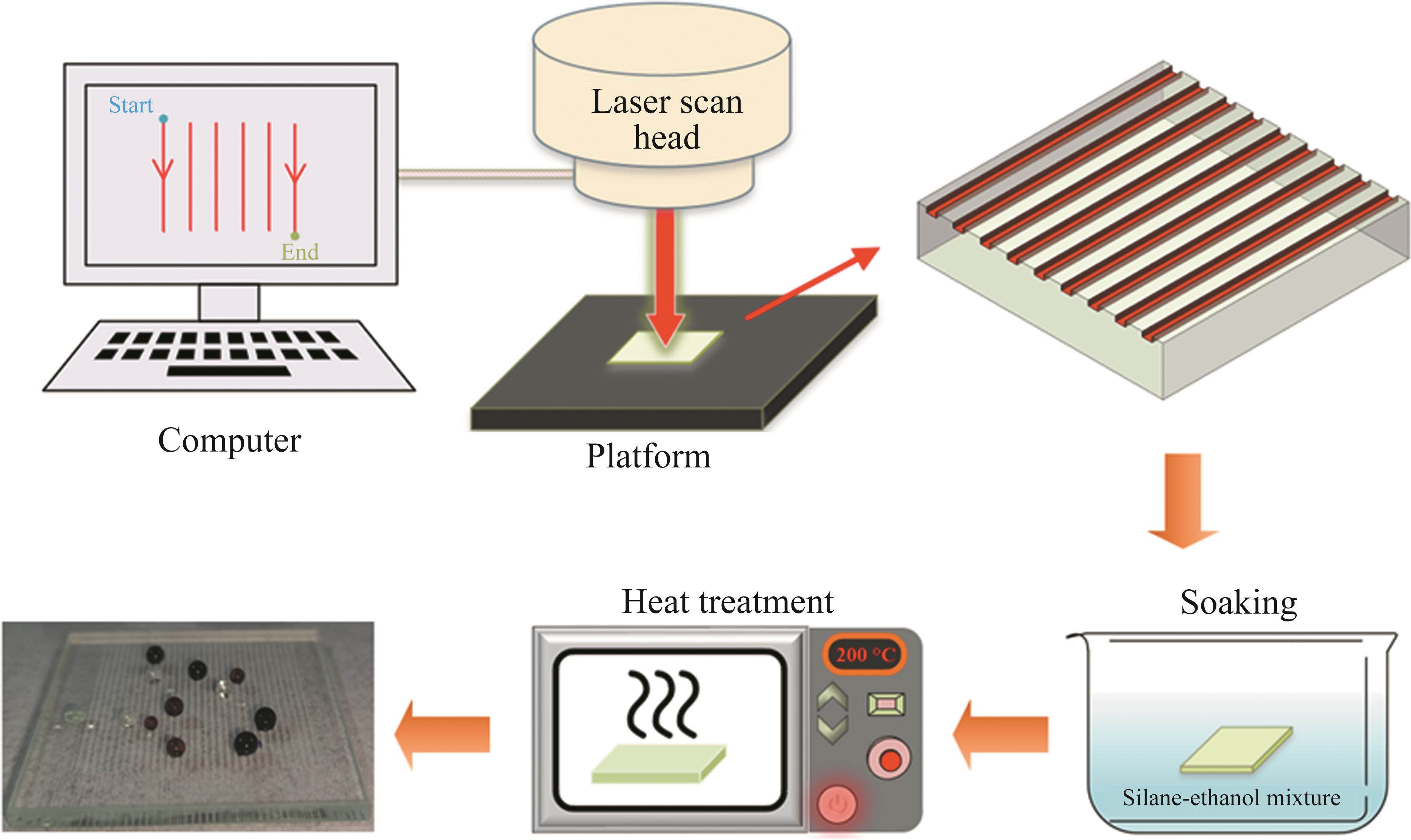
Parameter | Value |
---|---|
Wavelength/nm | 355 |
Average power/W | 6 |
Repetition rate/kHz | 40 |
Pulse width/ns | 14 |
Scanning speed/(mm∙s-1) | 50-200 |
Line spacing/µm | 900-1200 |
Power intensity/(GW∙cm-2) | 0.53 |
Pulse energy/mJ | 0.15 |
2.3 Surface characterizations
The surface morphology and chemical composition of the glass surface before and after laser processing are characterized by scanning electron microscopy (SEM, Hitachi Regulus 8100) and energy-dispersive X-ray spectroscopy (EDS, Navo Nano 450). The accelerated voltage of SEM is set at 5 kV. The surface wettability of the glass is evaluated by a contact angle goniometer (SDC-200), and the average water contact angle (WCA) value of the deionized water droplets of 5 μL dropping at 3 different locations on the glass surface is taken as the final result. The surface transparency of the glass before and after laser processing is measured by a UV-visible spectrophotometer (SHIMADZU, UV 2600), and the optical wavelength range is set from 300 nm to 800 nm. The stability experiment is carried out by evaluating WCA and water roll-off angle (WRA) after adhesive tape friction under the action of 200 g weight with various friction cycles. The durability of superhydrophobic glass is evaluated similarly by soaking the superhydrophobic glass in 0.9% NaCl saline environment for several hours.
3 Results and discussion
3.1 Surface morphology
The surface morphology of the glass can be significantly altered by the laser beam. In order to evaluate the surface morphology of the initial flat glass surface after nanosecond laser ablation, SEM was applied for local scanning. Figure 2 shows the SEM images of the glass surfaces prepared by different laser line spacings. At the laser scanning speed of 100 mm/s, the width and height of the microgrooves induced by laser beam are basically the same (Figures 2(a)-(d)). The cluster structures consist of a large number of nanoparticles are scattered on both sides of the microgrooves. These cluster structures are attributed to the fact that when nanosecond pulse laser irradiates the glass surface, the multiphoton absorption of the glass engenders avalanche ionization and produces surface plasma [19]. These plasmas are rapidly aggregated and deposited as nanoclusters at high temperatures and high pressures. The micro/nanostructure composed of microgrooves and nanoclusters can resist the invasion of droplets to a certain extent, which is also regarded as a critical factor in achieving superhydrophobicity [34]. In addition, with the increase of laser line spacing (from 900 to 1200 µm), the number of grooves observed in the SEM images will change under the same multiple. The contact area between the droplets and the glass surface can also be enlarged, and the capillary and van der Waals forces on the surface will be magnified under the action of increased contact areas [35]. At this point, the droplets may stick to the surface with a high WCA. It can also be seen from Figures 2(b)-(d) that some microcracks are generated on the glass surface due to laser ablation. Nevertheless, these microcracks will not affect the surface wettability of the glass as a whole.
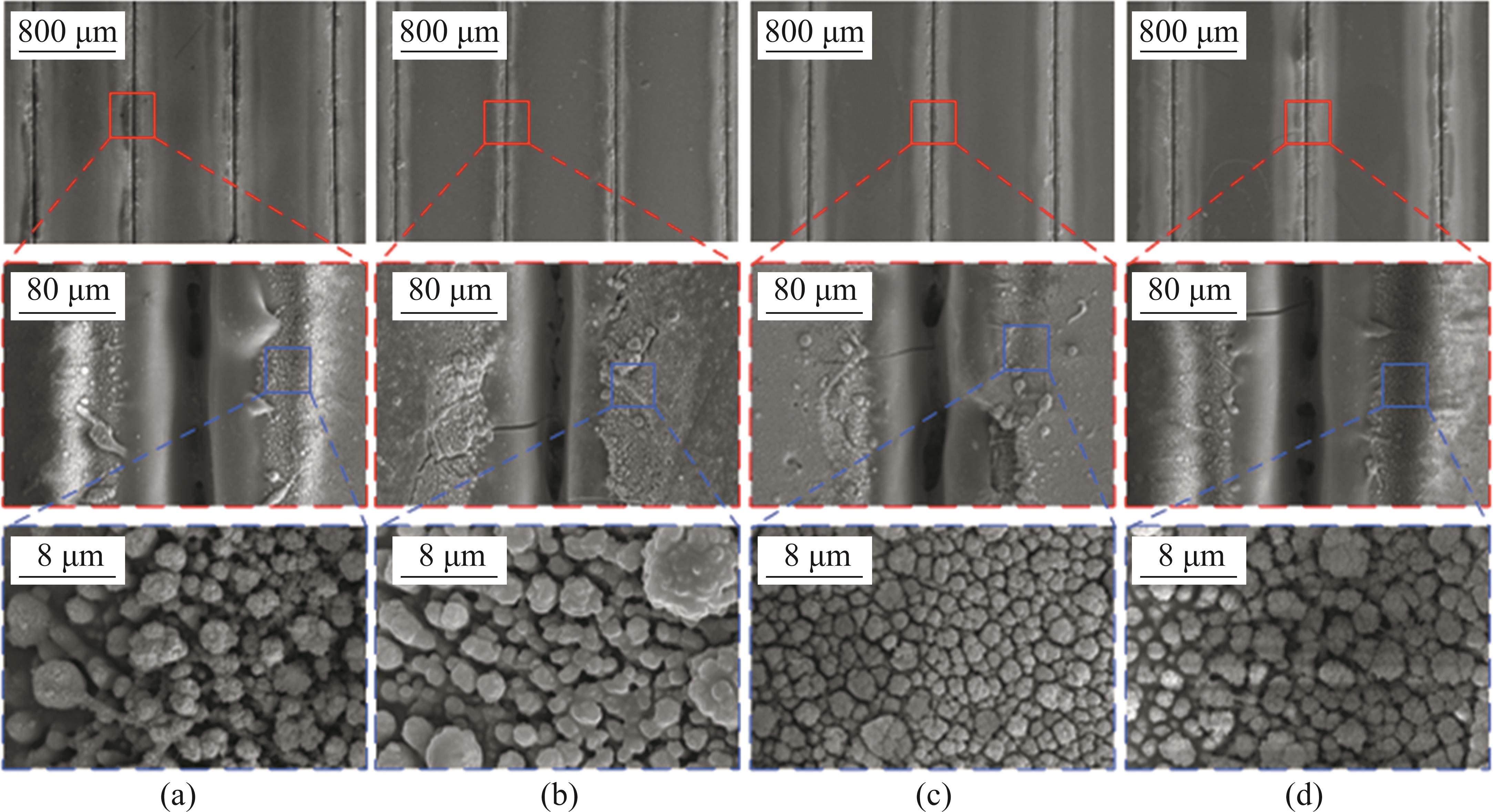
Actually, the hierarchical micro/nanostructure on the glass surface can also be significantly changed by the laser scanning speed. Figure 3 shows the SEM images of the glass surfaces prepared by different laser scanning speeds. When the scanning speed is 50 mm/s (Figure 3(a)), the laser texturing duration on the glass surface is longer, and the number of single point pulses is increased. Compared to the greater scanning speed, the deeper depth of the microgrooves can be clearly seen. Such deep microgrooves could theoretically trap more air and thus increase hydrophobicity of glass surface [7, 36]. However, in practical applications, excessive ablation of the glass surface caused by long-term laser scanning must be taken into account, which will engender irregular damage of the surface structure. Therefore, the laser scanning speed must be controlled within a certain range to effectively ensure the superhydrophobicity of the glass. With the increase of scanning speed (Figures 3(b) and (d)), the glass surface is subjected to fewer single point pulses, and the laser beam is mainly scanned on the shallow surface. This allows the laser-induced microgroove structure to develop in a shallow and wide direction. Meanwhile, fewer laser pulses contribute to a sharp reduction in the nanoparticles formed by the plasma expansion spatter. At this time, the surface droplets are difficult to be effectively supported by micro/nanostructures, resulting in the failure of superhydrophobicity. In addition, when the size of the droplet is much smaller than the spacing, the droplet is only affected by surface chemistry in the unprocessed area and may not be able to reach a superhydrophobic state. However, this kind of microdroplet is easily evaporated in the air environment, and generally does not affect the physical and chemical properties of the glass surface. Therefore, in order to ensure high transparency, large spacing is necessary.
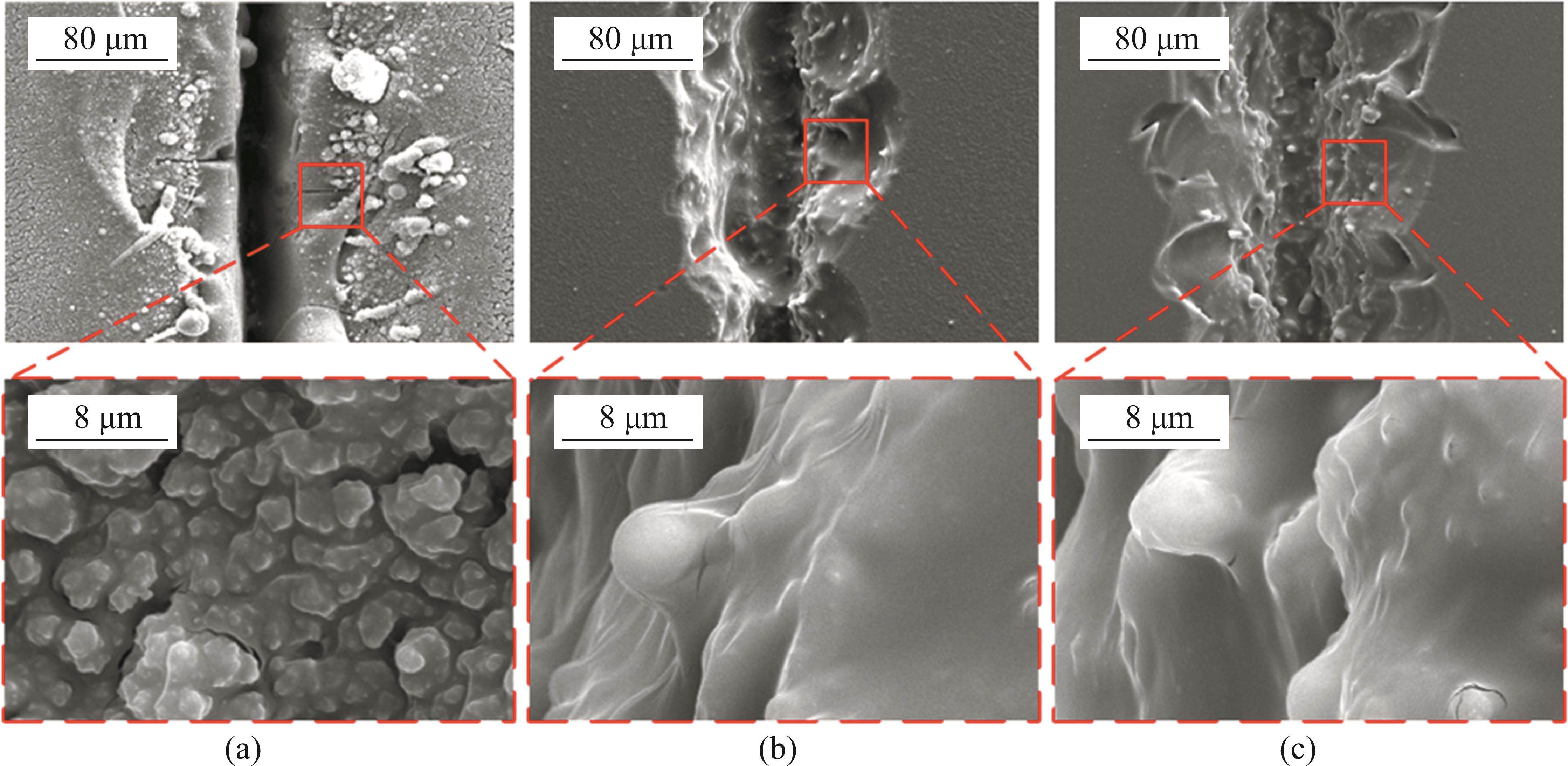
3.2 Surface chemistry
The surface free energy controlled by surface chemical composition is regarded as a critical factor affecting surface wettability [37]. In order to investigate the changes in the chemical composition of the glass surface before and after laser processing, EDS tests are utilized to analyze the changes in the content of four elements including C, O, F and Si, as shown in Figure 4 and Table 2. The C on the glass surface is mainly derived from the deposition of carbon-containing organic compounds in the air and the residual pollution compounds in the equipment during SEM and EDS testing [38]. The O and Si on the surface are mainly derived from the substrate material of silica glass. For untreated glass surfaces (Figure 4(a)), O and Si make up the majority of the surface chemical composition, and trace amounts of F are also present on the surface. The presence of F is not supposed to be on ordinary glass surfaces. It may be due to the common storage and detection of the untreated and laser-textured surfaces and LCF glass surfaces. The silane-ethanol mixture solution on the LCF surface is partially volatilized in the air and slowly deposited on other surfaces. In addition, significant increase in the content of O element from 35.68% to 42.76% can also be induced by laser texturing, as shown in Figure 4(b). This is because a violent oxidation reaction will be generated on the glass surface due to the laser ablation. A large number of hydroxyl functional groups (—OH) are induced on the surface and combined with Si to form silicon hydroxyl groups (Si—OH) [39]. The surface energy of glass will be significantly increased by this polar hydrophilic Si—OH. This allows water droplets touching the surface of the grooved array to rapidly penetrate into the microgroove under the capillary effect [40]. Therefore, the surface exhibits superhydrophilicity under the combined action of the laser-induced micro/nanostructure and high surface energy. After silane heat treatment on the laser-textured glass surface, the content of C and F increases to 25.12% and 21.65% respectively. This is attributed to the accelerated surface deposition of carbon-containing hydrophobic alkyls (CH2 and CH3) in the air and C—F chemical bonds (CF2 and CF3) in silanes [41]. Simultaneously, the contact between fluoroalkyl silane and glass will produce siloxane molecules through the hydrolysis effect according to Arkles theory [42]. The hydroxyl content increased by laser ablation will be reduced by the dehydration reaction between these siloxane molecules and Si—OH. The surface energy of the glass can be effectively reduced under the combined action of the decrease of the hydrophilic group and the increase of the hydrophobic group. Superhydrophobicity can also be formed on the surface in combination with hierarchical micro/nanostructures.
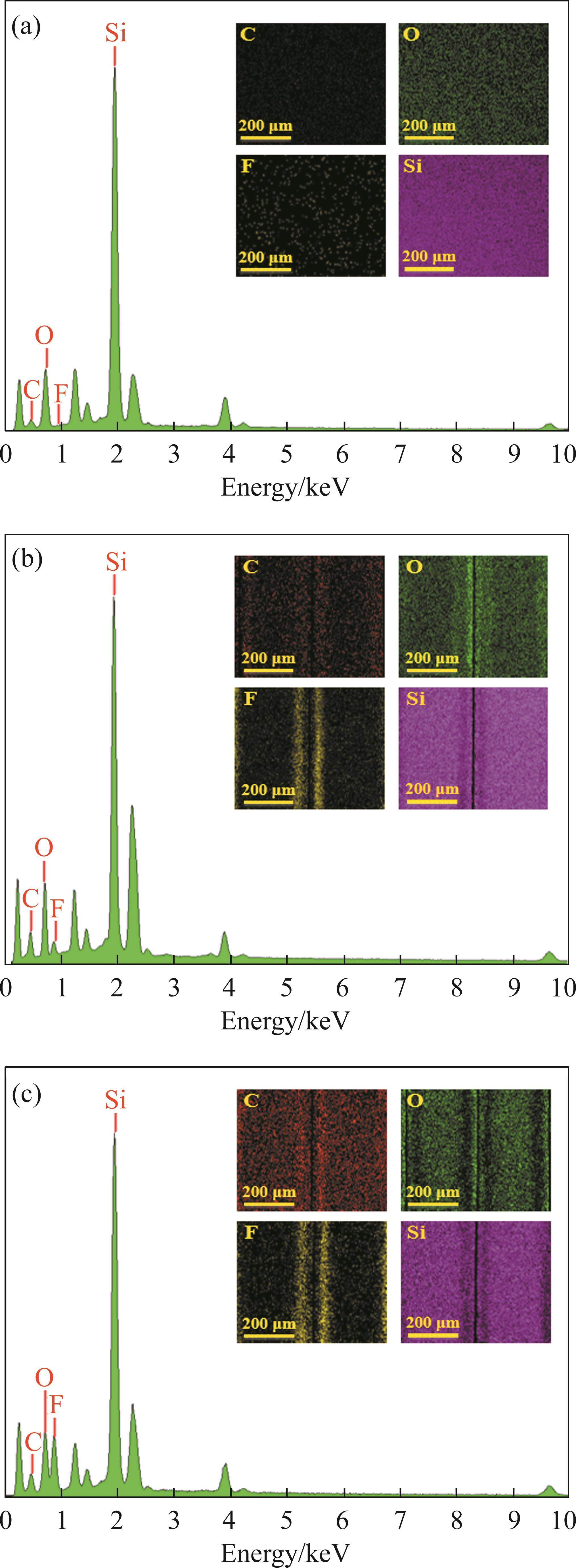
Element | Untreated | Laser-textured | LCF |
---|---|---|---|
C | 18.50 | 19.50 | 25.12 |
O | 35.68 | 42.76 | 22.43 |
F | 1.38 | 1.81 | 21.65 |
Si | 44.44 | 35.93 | 30.80 |
3.3 Surface wettability
As mentioned above, the wettability of the droplets on the glass surface is determined by both the surface morphology and the chemical composition. The WCA on a typical glass surface is about 32.2° (Figure 5(a)). At this time, when the lower surface of liquid is in contact with the flat glass surface, the droplet will be firmly adsorbed on the surface due to the interfacial tension between the solid and liquid so that the surface exhibits intrinsic hydrophilicity. The microgroove and microcolumn structures can be induced on the glass surface by laser texturing, and the top of the microcolumn is also distributed with nanoscale particle clusters. The droplets will be adsorbed in these micro/nanostructures under the action of extremely high surface energy caused by strong laser oxidation reaction, which significantly enlarges the solid-liquid contact area and thus increases the interfacial tension [43]. As a result, the laser-textured glass surface exhibits superhydrophilicity with a WCA of 0°. The post-treatment process that includes silane infiltration and heat treatment can effectively decrease the surface energy of the glass and thus reduce the interfacial tension between the solid and the liquid. According to Cassie state theory [44], the air layer between solid and liquid can be trapped by the surface micro/nanostructure. This allows the lower liquid surface of the droplet to contact only the nanoclusters at the top of the microcolumn. Point contact is formed between solid and liquid rather than area contact, which further reduces the interfacial tension. Therefore, the LCF glass surface exhibits superhydrophobicity with a WCA up to 155.8°. Of course, the wettability of the glass surface will be significantly affected by laser processing parameters, as shown in Figures 5(b) and (c). It can be seen from Figure 5(b) that when the laser line spacing is greater than 1000 µm, the WCA on the glass surface is less than 150°, and the WRA is greater than 10°. This means that the superhydrophobicity cannot be maintained on the LCF surfaces. With the further increase of line spacing, the surface hydrophobicity will be weakened gradually. This is mainly due to the increased line spacing leading to more liquid intrusion into the surface microgroove. The droplets cannot be adequately supported by the air layer trapped in the microgroove [45]. Hence, the lower surface of liquid is gradually adhered to both sides of the microgroove, which weakens the hydrophobicity. The effect of laser scanning speed on surface wettability is realized in another way. With the increase of scanning speed to 150 mm/s (Figure 5(c)), the superhydrophobicity cannot be obtained on the surface, and even WRA increases sharply. This is attributed to the fact that the excessive scanning speed leads to fewer single laser pulses on the glass surface, and fewer nanoparticles are sputtered by the plasma expansion. The microcolumn clusters composed of nanoparticles were almost not formed on both sides of the laser-induced microgroove. At this time, even if the glass surface possesses a low surface energy, it cannot effectively support the droplet. The surface wettability will gradually transform from superhydrophobicity to typical hydrophobicity. Moreover, the balance between surface wettability and high transparency also needs to be taken into account for glass surfaces. This is reflected in the subsequent surface transparency analysis.
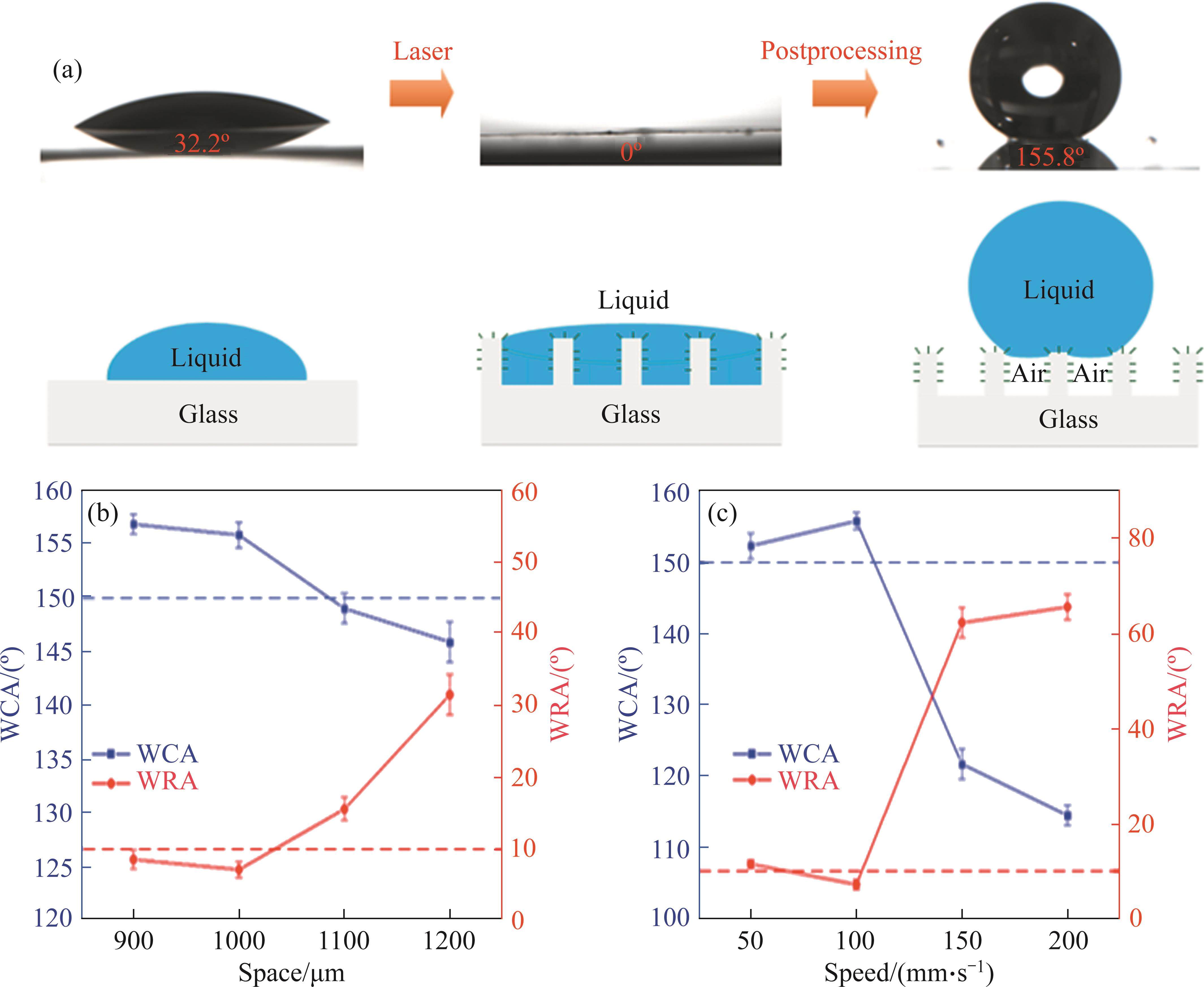
3.4 Surface transparency analysis
The high transparency of glass surface is regarded as a critical factor in the field of industrial glass. Obviously, the surface transparency will be affected by the micro/nanostructures induced by laser processing. The incident light is weakened after many reflections in the laser-induced surface micro-groove or micro-convex structure, thus reducing the surface transparency [41]. In order to investigate the change of surface transparency before and after laser processing, ultraviolet visible spectrophotometer is utilized to obtain the change curve of transparency with a wavelength of 300-800 nm, as shown in Figures 6(a) and (b). Table 3 shows the average transparency of visible light from 400 to 700 nm for the glass surface prepared by different laser parameters. Compared with 93.35% of surface transparency on the untreated glass surface, the transparency of the glass surface after laser processing is reduced by 3%-10%. Meanwhile, with the decrease of laser line spacing, the surface transparency is also significantly weakened. This is mainly due to the increase in the density of the microgrooves produced by laser ablation, which gradually reduces the flat glass box area, and eventually leads to the loss of surface transparency [41]. In addition, the surface roughness will be increased by the hierarchical micro/nanostructure on both sides of the laser-induced microgroove, resulting in visible light to scatter or diffuse reflection in different directions when it irradiates the glass surface [46]. However, this slight reduction in transparency will not affect the haze of the glass surface. This is due to the fact that the laser-induced microgrooves and nanoparticles are micro-scale structures, which have little effect on the haze, and the surface can still maintain a low haze (less than 2%) [47]. The proportion of micro/nanostructures will be effectively reduced due to the increased line spacing, so that the light scattering is more concentrated, and thus higher surface transparency is obtained. The influence of laser scanning speed on the surface transparency may be more obvious. At a scanning speed of 50 mm/s, the surface transparency of the glass is only 80.33%. This is attributed to the excessively small scanning speed that results in excessive ablation of the laser-induced microgrooves on the glass surface. The incident light will dissipate gradually after many reflections and refractions in the excessively deep microgroove. With the increase of the scanning speed to 100 mm/s, the surface transparency is also increased to 87.93%. These results show that the appropriate increase of the line spacing and scanning speed is more conducive to achieving high transparency under the premise of ensuring the superhydrophobicity. Therefore, the line spacing of 1000 µm and scanning speed of 100 mm/s are applied to fabricate superhydrophobic glass surface with high transparency. Such high transparency can be intuitively reflected in the university logo in Figure 6(c). Although the grating pattern that affects transparency on the glass surface has been induced by the laser texturing, the university logo is still clearly visible under the laser-textured surface compared to the untreated surface. The visibility of the logo also gradually improves with the increase of scanning speed and line spacing. According to the above-mentioned analyses, it can be concluded that the laser processing parameters must be carefully controlled and regulated to reduce the loss of surface transparency.
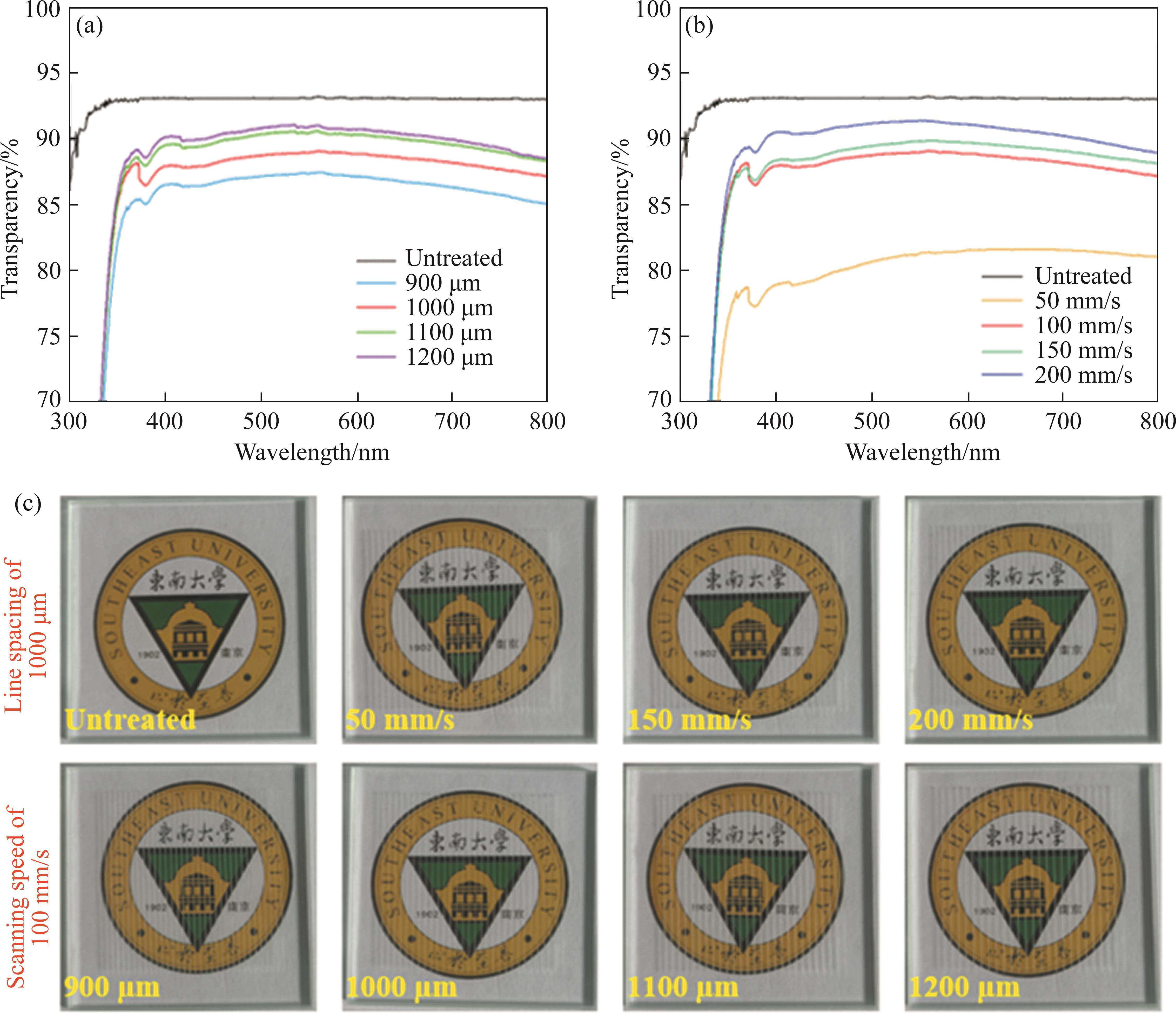
Parameter | Untreated | Line spacing | Scanning speed | ||||||
---|---|---|---|---|---|---|---|---|---|
900 µm | 1000 µm | 1100 µm | 1200 µm | 50 mm/s | 100 mm/s | 150 mm/s | 200 mm/s | ||
Transparency | 93.35 | 86.24 | 87.93 | 89.56 | 90.77 | 80.33 | 87.93 | 88.42 | 91.10 |
3.5 Superhydrophobic robustness
The superhydrophobic robustness of material surface has always been regarded as the most critical factor for the application of superhydrophobic surface [48, 49]. The superhydrophobic glass surface fabricated by LCF process provides a potential reference for meeting the robustness requirements. When the laser-prepared superhydrophobic glass surface is placed in the air environment for a month, the WCA on the surface can still maintain at 154.2° (Figure 7(a)). This is almost identical to the initial WCA value of the superhydrophobic surface. Although the WRA decreases slightly with the increase of time, it can still maintain around 10°. This durable superhydrophobicity indicates that the chemical composition on the superhydrophobic glass surface is stable. The surface energy of the laser-textured glass surface is reduced effectively and persistently by the post-treatment process. Simultaneously, the micro/nanostructures induced by the laser beam on the glass surface also have excellent wear resistance, as shown in Figure 7(b). After several cycles of tape stripping experiments on the superhydrophobic glass surface, WCA and WRA will decrease and increase with the increase of cycles, respectively. However, this change is not enough to affect the surface superhydrophobicity of the glass. After 50 wear tests, WCA and WRA of the surface are still stable at 152.7° and 11.8°. The droplets can still roll off the glass surface easily. This superhydrophobic stability is due to the fact that the hardness of the material can be enhanced by the laser-induced surface micro/nanostructures [50]. This allows the microgroove structure that stores air to retain its original shape and size during wear. Of course, the nanoparticles on the microstructure will inevitably be slightly worn, which is also the reason for the distinct change in WRA. In addition, it is also necessary to consider the durability of the superhydrophobic glass in the human physiological environment when used as an endoscope. After soaking the superhydrophobic glass in 0.9% NaCl saline environment for several hours, the WCA is decreased to 152.2° and the WRA is increased to 13.1° as compared with the original superhydrophobic surface. This indicates that the excellent superhydrophobic stability in NaCl solution can be realized on the superhydrophobic glass surface fabricated by LCF process. The droplet will not adhere to the inclined surface but will roll off the surface, which also carry away the surface contaminants. This stable self-cleaning effect will further expand the medical value of superhydrophobic glass. In fact, the robustness of the laser-prepared superhydrophobic glass can also be further improved by increasing the density of the surface micro/nanostructure. However, this will obviously reduce the surface transparency of the glass material. Therefore, the balance between superhydrophobic robustness and high transparency will be regarded as a key avenue that needs to be further explored.
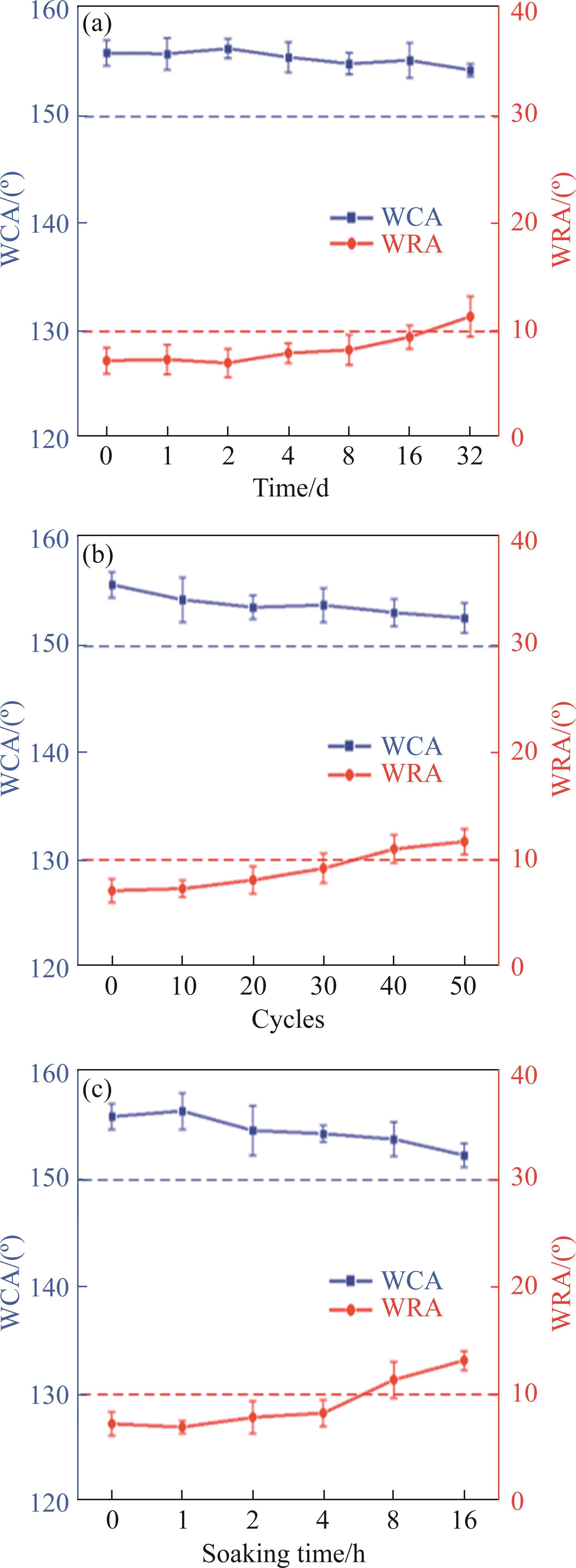
Moreover, in order to further realize the practical application of superhydrophobic transparent glass, cost and efficiency are also important factors to consider. In this work, the surface modification time of the glass is 2-2.5 h. Compared with the existing fabrication process [19, 33, 51], the duration of chemical treatment process time is not largely increased. However, the amount of superhydrophobic glass samples fabricated per unit time can be significantly increased by nanosecond laser beam, which is not possible with other femtosecond or picosecond lasers [52, 53]. Meanwhile, the reagent used in the chemical treatment surface functionalization process is very cheap with only $21.4/L. This suggests that this laser-chemical surface functionalization process can produce large quantities of superhydrophobic glass at low cost, especially for the medical equipment with small area such as endoscopes. In addition, this laser-chemical process can now also be applied to titanium alloys [45], zirconia ceramic [54], silicon carbide [55] and other metal/non-metallic materials. Subsequent superhydrophobic modification of other transparent materials will also be further explored.
4 Conclusions
In summary, an efficient laser-chemical surface functionalization method including nanosecond laser texturing and chemical treatment is adopted to fabricate robust superhydrophobic glass surface with high transparency. Based on the experimental results, the following conclusions can be drawn:
1) The air layer between the droplet and the glass material can be effectively trapped by laser-induced hierarchical micro/nanostructure of the surface. This will support the droplet, leaving it in a Cassie state on the surface.
2) The hydrophobic functional groups containing carbon and fluorine (CH2, CH3 and CF2, CF3) can be rapidly adsorbed and deposited on the glass surface by the chemical modification process. The surface energy of the glass can be effectively reduced under the action of the increase of the hydrophobic group.
3) The glass surface exhibits robust superhydrophobicity with a water contact angle of 155.8° under the combined action of stable micro/nanostructure and continuous low surface energy. The more unprocessed box area also ensures the high transparency of the superhydrophobic glass. The prepared superhydrophobic glass can still maintain superior superhydrophobicity under multiple wear conditions.
In the future, it is believed that this highly efficient laser-chemical surface functionalization method will expand the application prospects of glass materials in biomedicine and other related fields, and its functional stability in more extreme environments will also be the focus for future exploration.
Evaluating and minimizing induced microbending losses in optical fiber sensors embedded into glass-fiber composites
[J]. Journal of Lightwave Technology, 2021, 39(22): 7315-7325. DOI: 10. 1109/JLT.2021.3112484.High-current-density indium nitride ultrathin-film transistors on glass substrates
[J]. Applied Physics Letters, 2016, 109(14): 142104. DOI: 10.1063/1.4964422.Innovative hydrothermal technique in efficient disengagement of waste solar panels
[J]. Waste Management, 2024, 177: 196-202. DOI: 10.1016/j.wasman.2024.01.045.Laparoscopic lens fogging: Solving a common surgical problem in standard and robotic laparoscopes via a scientific model
[J]. Surgical Endoscopy, 2018, 32(3): 1600-1606. DOI: 10.1007/s00464-017-5772-x.A novel one-step lens cleaning device using air and water flow for endoscopic surgery
[J]. PLoS One, 2018, 13(7):Recent progress on transparent and self-cleaning surfaces by superhydrophobic coatings deposition to optimize the cleaning process of solar panels
[J]. Solar Energy Materials and Solar Cells, 2023, 257: 112347. DOI: 10.1016/j.solmat. 2023.112347.Bioinspired nanoflakes with antifouling and mechano-bactericidal capacity
[J]. Colloids and Surfaces B: Biointerfaces, 2023, 224: 113229. DOI: 10.1016/j.colsurfb.2023.113229.Hybrid laser ablation and chemical modification for fast fabrication of bio-inspired super-hydrophobic surface with excellent self-cleaning, stability and corrosion resistance
[J]. Journal of Bionic Engineering, 2019, 16(1): 13-26. DOI: 10.1007/s422 35-019-0002-y.Construction of transparent, robust and haze-selectable superhydrophobic coatings with honeycomb structure
[J]. Chemical Engineering Journal, 2024, 483: 149319. DOI: 10.1016/j.cej. 2024.149319.Nanosecond pulsed laser etching anti-reflective gratings and synchronous laser annealing for performance optimization of Ag/AZO thin films
[J]. Ceramics International, 2024, 50(15): 27176-27187. DOI: 10.1016/j.ceramint.2024.05.015.Superhydrophobic synergistic antibacterial ZrO2-based surfaces with tertiary hierarchical structures fabricated by femtosecond laser texturing and surface modification
[J]. Journal of Alloys and Compounds, 2024, 1002: 175331. DOI: 10.1016/j.jallcom.2024.175331.Antibacterial performance of Zr-BMG, stainless steel, and titanium alloy with laser-induced periodic surface structures
[J]. ACS Applied Bio Materials, 2022, 5(1): 272-284. DOI: 10.1021/acsabm.1c01075.Improvement of corrosion resistance of H59 brass through fabricating superhydrophobic surface using laser ablation and heating treatment
[J]. Corrosion Science, 2021, 180: 109186. DOI: 10.1016/j.corsci.2020.109186.Achieving hierarchical structure with superhydrophobicity and enhanced anti-corrosion via electrochemical etching and chemical vapor deposition
[J]. Applied Surface Science, 2023, 610: 155362. DOI: 10.1016/j.apsusc.2022.155362.Fabrication of extreme wettability surface for controllable droplet manipulation over a wide temperature range
[J]. International Journal of Extreme Manufacturing, 2022, 4(4):Photothermal superhydrophobic copper nanowire assemblies: Fabrication and deicing/defrosting applications
[J]. International Journal of Extreme Manufacturing, 2023, 5(4):Recent progress in bio-inspired macrostructure array materials with special wettability-from surface engineering to functional applications
[J]. International Journal of Extreme Manufacturing, 2024, 6(1):Rational construction of highly transparent superhydrophobic coatings based on a non-particle, fluorine-free and water-rich system for versatile oil-water separation
[J]. Chemical Engineering Journal, 2018, 333: 621-629. DOI: 10.1016/j.cej.2017.10.006.Durable and robust transparent superhydrophobic glass surfaces fabricated by a femtosecond laser with exceptional water repellency and thermostability
[J]. Journal of Materials Chemistry A, 2018, 6(19): 9049-9056. DOI: 10.1039/C8TA01965G.A facile, multifunctional, transparent, and superhydrophobic coating based on a nanoscale porous structure spontaneously assembled from branched silica nanoparticles
[J]. Advanced Materials Interfaces, 2015, 2(13): 1500201. DOI: 10.1002/admi.201500201.Application of ZnO/epoxy resin superhydrophobic coating for buoyancy enhancement and drag reduction
[J]. Colloids and Surfaces A: Physicochemical and Engineering Aspects, 2022, 651: 129714. DOI: 10.1016/j.colsurfa.2022.129714.Tool wear mechanisms and micro-channels quality in micro-machining of Ti-6Al-4V alloy using the Ti(C7N3)-based cermet micro-mills
[J]. Tribology International, 2019, 134: 60-76. DOI: 10.1016/j.triboint.2019.01.030.A transparent superhydrophobic coating with mechanochemical robustness for anti-icing, photocatalysis and self-cleaning
[J]. Chemical Engineering Journal, 2020, 399: 125746. DOI: 10. 1016/j.cej.2020.125746.Robust and durable liquid-repellent surfaces
[J]. Chemical Society Reviews, 2022, 51(20): 8476-8583. DOI: 10.1039/D0CS01 033B.Laser-induced fast assembly of wettability-finely-tunable superhydrophobic surfaces for lossless droplet transfer
[J]. ACS Applied Materials & Interfaces, 2022, 14(31): 36246-36257. DOI: 10.1021/acsami.2c09410.Laser surface functionalization to achieve extreme surface wetting conditions and resultant surface functionalities
[J]. Journal of Central South University, 2022, 29(10): 3217-3247. DOI: 10.1007/s11771-022-5140-4.Underwater gas self-transportation along femtosecond laser-written open superhydrophobic surface microchannels (<100 µm) for bubble/gas manipulation
[J]. International Journal of Extreme Manufacturing, 2022, 4(1):Selective laser ablation preparation of Ag grid transparent electrodes with fractal-combined structures and optimization of fractal grid pitch
[J]. Optics & Laser Technology, 2022, 156: 108597. DOI: 10.1016/j.optlastec.2022.108597.Laser layered scanning strategy for fractal Ag mesh transparent conductive electrodes using selective laser ablation and its application to transparent heaters
[J]. Optics & Laser Technology, 2024, 174: 110674. DOI: 10.1016/j.optlastec.2024.110674.Fabrication of fractal Ag mesh/FTO transparent electrodes/heaters with enhanced electrical conductivity based on mesh hierarchy and shape optimization
[J]. Optics & Laser Technology, 2024, 168: 109895. DOI: 10.1016/j.optlastec. 2023.109895.Enhancing overall performances of Cu/Ag/AZO multilayer films for transparent heaters via laser/furnace step-by-step annealing mode
[J]. Materials Science in Semiconductor Processing, 2024, 170: 107956. DOI: 10.1016/j.mssp.2023.107956.Lubricant-infused directly engraved nano-microstructures for mechanically durable endoscope lens with anti-biofouling and anti-fogging properties
[J]. Scientific Reports, 2020, 10(1): 17454. DOI: 10.1038/s41598-020-74517-8.Fabrication of superhydrophobic surfaces on a glass substrate via hot embossing
[J]. Ceramics International, 2023, 49(16): 26338-26347. DOI: 10.1016/j.ceramint.2023.05.169.Nanosecond laser induced microstructure features and effects thereof on the wettability in zirconia
[J]. Ceramics International, 2020, 46(15): 24173-24182. DOI: 10.1016/j.ceramint.2020.06.197.Facile laser-based process of superwetting zirconia ceramic with adjustable adhesion for self-cleaning and lossless droplet transfer
[J]. Applied Surface Science, 2023, 638: 158069. DOI: 10.1016/j.apsusc.2023.158069.Superhydrophobic mechano-bactericidal surface with photodynamic antibacterial capability
[J]. ACS Applied Materials & Interfaces, 2023, 15(1): 723-735. DOI: 10.1021/acsami.2c21310.Roles of chemistry modification for laser textured metal alloys to achieve extreme surface wetting behaviors
[J]. Materials & Design, 2020, 192: 108744. DOI: 10.1016/j.matdes.2020. 108744.Temperature-responsive, femtosecond laser-ablated ceramic surfaces with switchable wettability for on-demand droplet transfer
[J]. ACS Applied Materials & Interfaces, 2023, 15(10): 13740-13752. DOI: 10.1021/acsami.2c22335.Transparent superhydrophobic solar glass prepared by fabricating groove-shaped arrays on the surface
[J]. Applied Surface Science, 2017, 426: 957-964. DOI: 10.1016/j.apsusc.2017.07.169.Superhydrophilicity/superhydrophobicity of nickel micro-arrays fabricated by electroless deposition on an etched porous aluminum template
[J]. Chemical Engineering Journal, 2012, 203: 1-8. DOI: 10.1016/j.cej.2012.06.128.High-throughput laser-based surface functionalization for fabrication of superhydrophobic soda-lime glass
[J]. International Journal of Applied Glass Science, 2024, 15(1): 57-72. DOI: 10.1111/ijag.16643.Femtosecond laser weaving superhydrophobic patterned PDMS surfaces with tunable adhesion
[J]. The Journal of Physical Chemistry C, 2013, 117(47): 24907-24912. DOI: 10.1021/jp408863u.Wettability of porous surfaces
[J]. Transactions of the Faraday Society, 1944, 40: 546. DOI: 10.1039/tf9444000546.Laser-based fabrication of superwetting titanium alloy with enhanced corrosion and erosion-corrosion resistance
[J]. Colloids and Surfaces A: Physicochemical and Engineering Aspects, 2024, 688: 133648. DOI: 10.1016/j.colsurfa.2024. 133648.Direct laser patterning for transparent superhydrophobic glass surfaces without any chemical coatings
[J]. Applied Physics A, 2020, 126(6): 462. DOI: 10.1007/s00339-020-03653-9.Fabrication of transparent wear-resistant superhydrophobic SiO2 film via phase separation and chemical vapor deposition methods
[J]. Ceramics International, 2022, 48(21): 32143-32151. DOI: 10.1016/j.ceramint.2022.07.154.Superhydrophobic concrete coating with excellent mechanical robustness and anti-corrosion performances
[J]. Colloids and Surfaces A: Physicochemical and Engineering Aspects, 2024, 684: 133157. DOI: 10.1016/j.colsurfa.2024. 133157.Flexible and mechanically robust superhydrophobic silicone surfaces with stable Cassie–Baxter state
[J]. Journal of Materials Chemistry A, 2016, 4(37): 14180-14186. DOI: 10.1039/C6TA06493K.Laser treatment of zirconia surface for improved surface hydrophobicity
[J]. Journal of Alloys and Compounds, 2015, 625: 208-215. DOI: 10.1016/j.jallcom. 2014.11.069.Hybrid superhydrophobic/hydrophilic patterns deposited on glass by laser-induced forward transfer method for efficient water harvesting
[J]. Journal of Colloid and Interface Science, 2022, 625: 383-396. DOI: 10.1016/j.jcis.2022.06.039.Stable and drag-reducing superhydrophobic silica glass microchannel prepared by femtosecond laser processing: Design, fabrication, and properties
[J]. Materials & Design, 2023, 225: 111501. DOI: 10.1016/j.matdes.2022.111501.Preparation of superhydrophobic glass surface with high adhesion
[J]. Colloids and Surfaces A: Physicochemical and Engineering Aspects, 2022, 633: 127861. DOI: 10.1016/j.colsurfa.2021. 127861.Fabrication of antibacterial and anti-corrosive zirconia ceramics with extreme wettability by facile laser-based surface modification
[J]. Ceramics International, 2024, 50(13): 22733-22747. DOI: 10.1016/j.ceramint.2024.03.376.Laser-based functionalization for superhydrophobic silicon carbide with mechanical durability, anti-icing and anti-fouling properties
[J]. Ceramics International, 2024, 50(20): 39307-39317. DOI: 10.1016/j.ceramint.2024.07.303.LIU Chao, WANG Qing-hua, GE Zhi-qiang, LI Hao-yu, FU Jia-jun, WANG Hui-xin and ZHANG Tai-rui declare that they have no conflict of interest.
LIU Chao, WANG Qing-hua, GE Zhi-qiang, LI Hao-yu, FU Jia-jun, WANG Hui-xin, ZHANG Tai-rui. Laser-based fabrication of superhydrophobic glass with high transparency and robustness [J]. Journal of Central South University, 2025, 32(1): 160-173. DOI: https://doi.org/10.1007/s11771-025-5853-2.
刘超,王青华,葛志强等.高透明和鲁棒性超疏水玻璃的激光制备[J].中南大学学报(英文版),2025,32(1):160-173.