磨矿作业是实现矿物选择性分离的核心单元,为了实现有用矿物与脉石矿物充分解离,必须对其进行高效、选择性磨矿处理[1-2]。磨矿作业是选矿前重要的作业,一方面,矿物磨碎过程中的能耗与钢耗巨大,据统计,我国磨矿能耗约占全国总能耗的1.15%,钢耗约占选矿厂总钢耗的50%以上[3];另一方面,磨矿产品特性在很大程度上决定了后续选别过程的指标[4]。因此,如何降低磨机运行中的能耗、钢耗与优化磨矿产品特性是当今磨矿领域研究的热点。
磨矿介质是影响磨矿能耗、钢耗与磨矿产品特性中最重要的因素之一[5-6]。磨矿介质是磨矿过程中能量的传递体以及矿石破碎的作用体。磨机的磨矿效率受磨机内磨矿介质的形状、尺寸、配比、运动形式以及介质空间分布的影响,其中介质空间分布的影响最显著[7-8]。工程实践表明,对粗颗粒采用大尺寸介质进行冲击破碎,而对细颗粒采用小尺寸介质进行研磨,可选择性磨矿进而避免矿物被过粉碎[9-10]。王宇斌等[11]发现筒磨机内部矿物的轴向空间分布呈现入料端颗粒粗、排料端颗粒细的特点,并提出了微阶段磨矿技术,其对于提高磨机处理量、改善磨矿产品特性具有重大意义。国内外针对磨矿介质在磨机内部轴向空间分布的优化开发了2项独特技术:一是通过在磨机内部增加隔板,将磨机分成几个隔室,每个隔室的介质尺寸不一致,从而达到大球冲击大矿石、小球研磨小矿石的目的;二是研制了哈丁磨机,该磨机结构的入料端为圆柱形筒体,排料端为圆锥形,从而达到优化钢球空间分布的目的[12]。这两种技术虽然在一定程度上降低了磨机的单位能耗及钢耗和矿物的过粉碎,并提高了磨机处理量,但在生产制造、维修以及钢球补加等方面都存在很多问题,阻碍了它们在工业生产中的推广应用。
磨机衬板既是磨机筒体的保护者,又是矿石磨碎的参与者。一方面,筒体衬板可保护磨机筒体不被磨矿介质和矿石强烈冲击、研磨与化学腐蚀;另一方面,它可以将磨机筒体的能量传递给磨矿介质和矿石,使其通过运动达到磨矿的目的。磨机衬板形状对磨机处理量、运转率、衬板使用寿命、能量利用效率等具有显著影响[13-15]。CLEARY等[16]通过离散元法对筒磨机进行数值模拟分析,得到了各部分相互作用的碰撞能量谱,确定了磨机的能量分配;RAJAMANI等[17]通过离散元法对筒磨机进行仿真研究,分析了衬板的磨损和矿石的研磨行为;赵元等[18]基于离散元法研究了颗粒形状对磨矿的影响,并定量分析了颗粒形状对负载特性的影响规律;蔡改贫等[19]利用离散元软件建立了半自磨磨矿仿真模型,研究了衬板高度对半自磨机磨矿效率的影响规律,以提高磨机磨矿能力;RODRIGUES等[20]采用半自磨机和自磨机对铁矿石进行工业试验,并对磨矿产品粒度特性、能耗与台效等进行了比较;XIE等[21]基于离散元法系统研究了磨机转速、充填率、钢球级配与衬板结构参数对半自磨的磨矿过程的影响,并选取磨机功率与碰撞能量作为量化指标,确定了半自磨机最佳磨矿参数;ASGHARI等[22]研究了半自磨机操作参数与衬板结构参数对磨矿产品粒度特性的影响;ROUX等[23]根据磨矿速率曲线分析了磨矿过程,并优化了磨矿时间;WANG等[24]基于离散元的方法优化了半自磨机运行过程转速。
虽然关于衬板与钢球级配的研究很多,但大多数学者都是单独针对衬板形状或钢球级配进行优化研究,鲜有学者将衬板形状与钢球级配设计进行联合研究,而对衬板形状参数对钢球轴向空间分布的影响规律的研究更少。为此,本文采用离散元法系统研究衬板组合对钢球轴向空间分布的影响,以提升筒磨机的磨矿效能。
1 试验方案
本文选用3种不同衬板结构,如图1所示。4种不同衬板结构组合见表1。图2所示为 90°-75°-45°-45°衬板组合,其中,第一段衬板的提升条面角为90°,第二段衬板的提升条面角为75°,最后两段衬板的提升条面角为45°。磨机的直径为0.4 m,各段的筒体长度为0.2 m,筒体总长度为0.8 m,介质充填率为35%,钢球的直径分别为 40 mm(大球)、30 mm(中球)与20 mm(小球),各级别质量比例为m(Φ40)꞉m(Φ30)꞉m(Φ20)=1꞉1꞉1。首先,选择单段长度为0.2 m筒体为研究对象,研究衬板结构对钢球运动状态的影响以及磨机内部碰撞能量分布;其次,对4种衬板组合在转速率为75%时进行数值模拟分析,探究衬板组合对钢球轴向空间分布的影响规律。由于磨机的转速率对钢球的运动状态影响很大,最后,选取90°-75°-45°-45°衬板组合在不同转速率(55%、65%、75%、85%与95%)下进行仿真试验。试验方案设计见表2,离散元数值模拟仿真参数见表3。
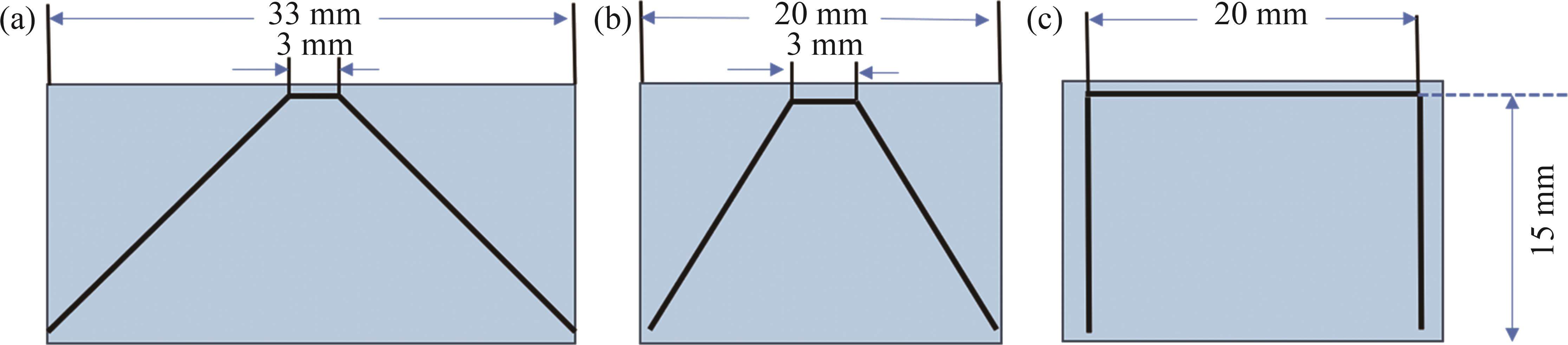
衬板结构 | 第一段(入料端) | 第二段 | 第三段 | 第四段(出料端) |
---|---|---|---|---|
1 | 75° | 75° | 75° | 75° |
2 | 90° | 75° | 45° | 45° |
3 | 90° | 75° | 75° | 45° |
4 | 75° | 75° | 45° | 45° |
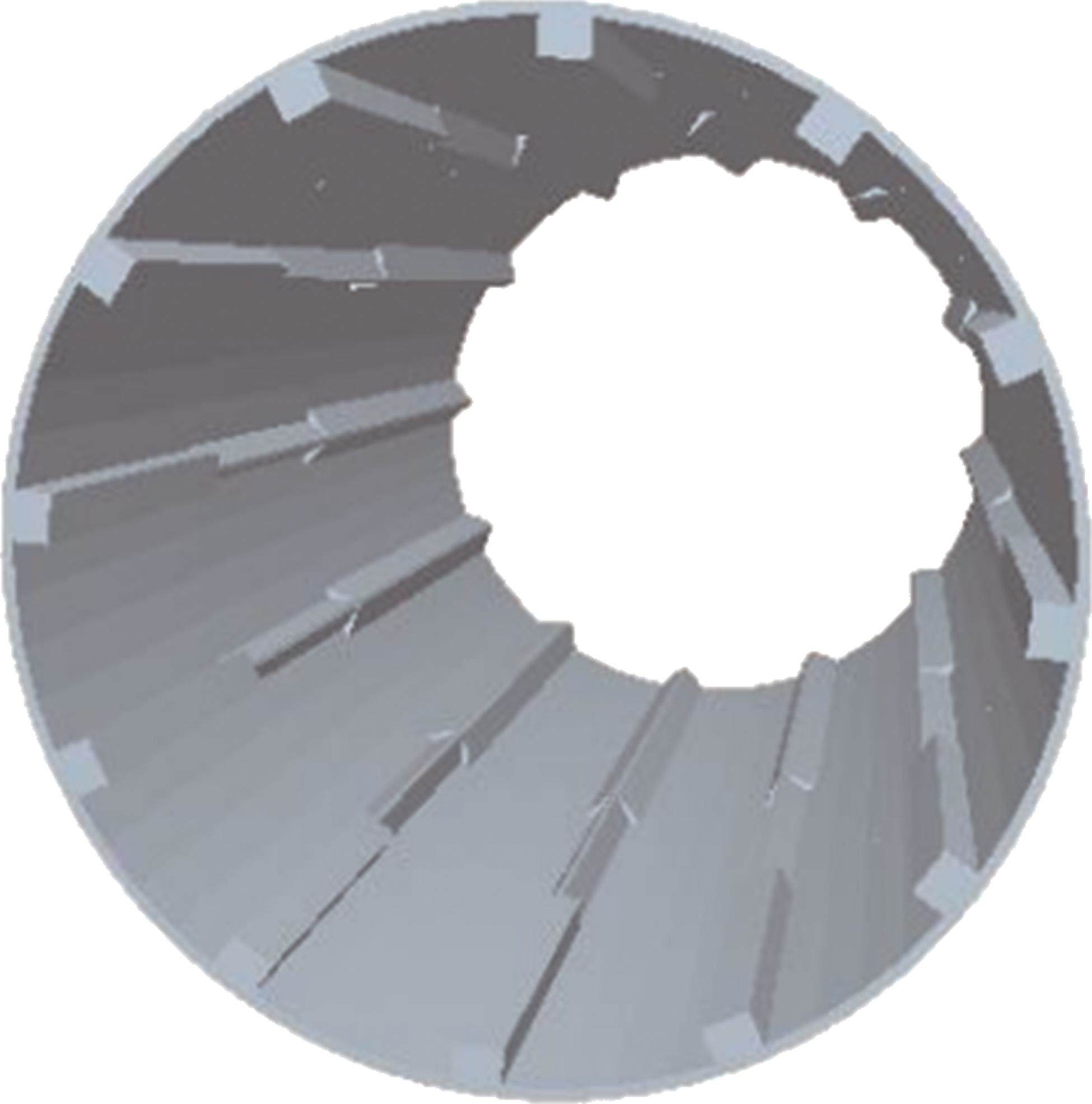
方案 | 转速率/% | 衬板结构 |
---|---|---|
1 | 75 | 单段90° |
2 | 75 | 单段75° |
3 | 75 | 单段45° |
4 | 65,75 | 75°-75°-75°-75°组合 |
5 | 55,65,75,85,95 | 90°-75°-45°-45°组合 |
6 | 65,75 | 90°-75°-75°-45°组合 |
7 | 65,75 | 75°-75°-45°-45°组合 |
模拟参数 | 数值 |
---|---|
钢球、衬板密度/(kg·m-3) | 7 850 |
钢球、衬板的泊松比 | 0.3 |
钢球、衬板的剪切模量/MPa | 10 000 |
钢球-钢球、钢球-衬板的弹性恢复系数 | 0.6 |
钢球-钢球、钢球-衬板的静摩擦因数 | 0.4 |
钢球-钢球、钢球-衬板的滚动摩擦因数 | 0.01 |
2 结果分析与讨论
2.1 不同衬板结构对钢球运动状态的影响
设定筒磨机转速率为75%,在仿真运转120 rad后,选择单段衬板稳定段开展分析。提升条面角对磨机载荷运动行为具有显著影响的参量,其对磨机内钢球的运动状态的影响如图3所示。由 图3可知:当提升条面角为90°时,钢球被提升的高度最高,运动形态主要以抛落式为主;而当提升条面角为75°与45°时,钢球的运动状态相似,运动状态主要以泻落式为主。提升条面角对载荷被抛落时的高度及水平位移均有影响,钢球与衬板接触位置的高度不断减小,钢球直接碰撞衬板的次数减少,进而增加了衬板的使用寿命。数值模拟结果显示,当提升条面角为90°、75°与45°时,磨机的功率分别为189.28、198.15与203.01 W,模拟结果与文献[12]中的试验结果一致。提升条面角不同时钢球动能的分布规律如图4所示。由图4可知:当提升条面角为75°时,钢球累积动能最大,为17.77 J;而当提升条面角为90°时,钢球累积动能最小,为14.69 J;当钢球累积动能小于0.5 J时,3种提升条面角下钢球累积能量曲线基本相同;当钢球累积动能大于0.5 J时,75°面角的钢球累积能量增长最快。导致这种现象的原因是:钢球动能取决于钢球的质量和落下时的高度,90°面角虽然使钢球提升的高度高,但落回点的角度减小,导致钢球的脱离点与落回点之间的距离最小,因此,钢球携带的动能最小。数值模拟结果进一步印证了文献[12]中的结论。


2.2 不同衬板组合对钢球运动状态的影响
由2.1节可知,提升条面角会显著影响钢球的运动状态以及动能分布。因此,可以通过多段衬板组合控制钢球的运动轨迹优,化钢球的轴向空间分布,从而达到与多隔室磨机和哈丁磨机同样的磨矿效果。在转速率为75%时,90°-75°-45°-45°衬板组合运行120 rad后的钢球提升高度如图5所示。由图5可知:90°提升条面角钢球提升高度最高,75°面角提升高度次之,45°面角提升高度最低。
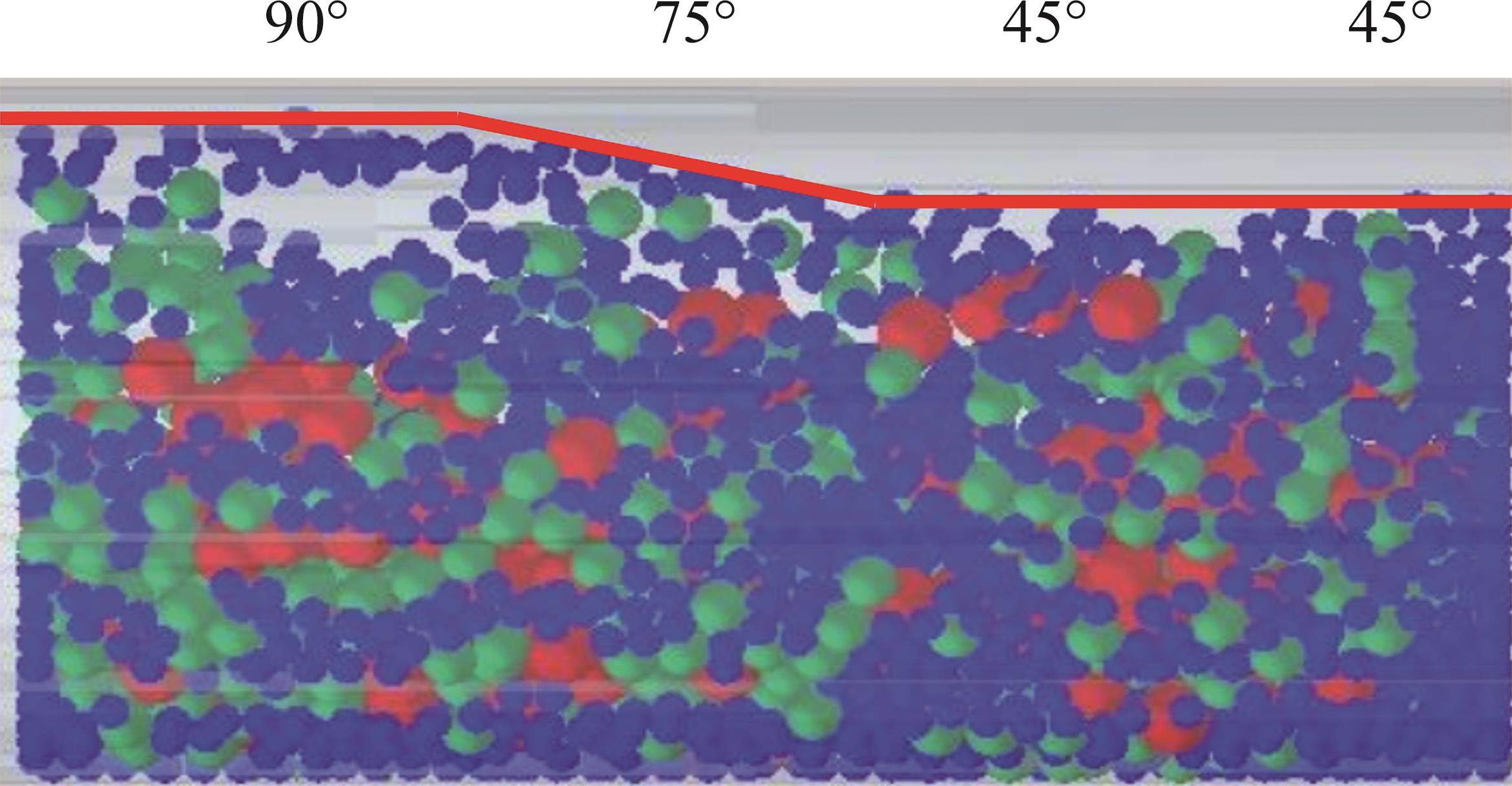
对90°-75°-45°-45°衬板组合运转120 rad后钢球轴向空间分布进行统计分析,结果如图6所示。从图6可见:当钢球运行120 rad后,直径为 20 mm的钢球向面角为45°的方向靠拢(见图6(b));而直径为40 mm的钢球向入料端即90°与75°面角方向靠近(见图6(d))。由此可见,可以通过改变各段提升条面角调控钢球的轴向空间分布。
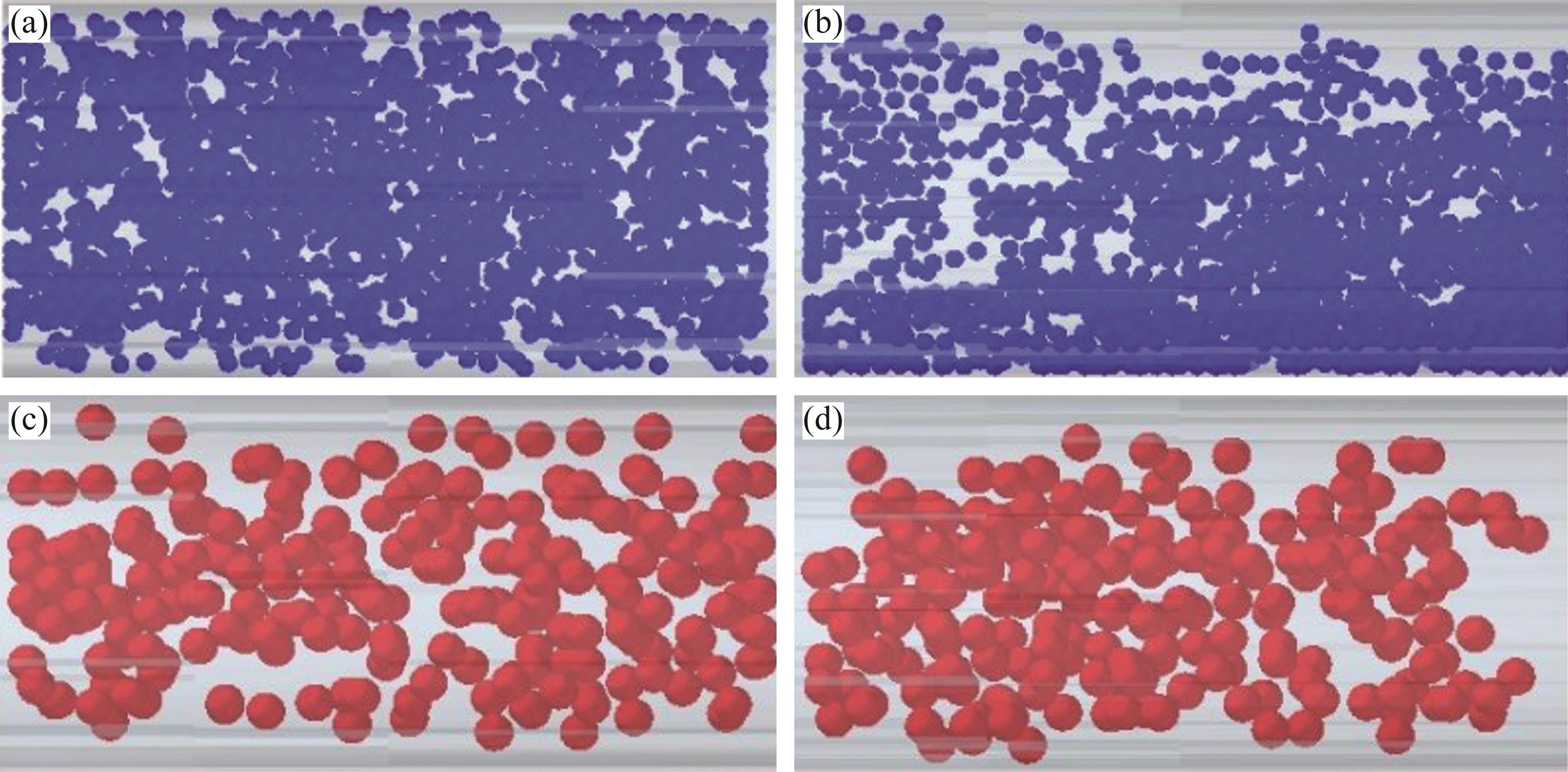
2.3 衬板组合对钢球轴向离析的影响
为了进一步量化钢球的空间分布状态,分别对每段筒磨机中各尺寸钢球的质量分数进行统计,结果如图7所示,其中,紫色代表直径为20 mm 钢球,黄色代表直径为30 mm的钢球,绿色代表直径为40 mm的钢球。按照图5所示的衬板组合,规定整个筒体左端为入料端,右端为出料端,从左往右依次命名为1、2、3、4。由图7(a)可知:75°-75°-75°-75°衬板组合导致大球、中球向中间汇聚,而小球向两端分散。图7(b)所示为90°-75°-45°-45°衬板组合下钢球的空间分布情况。从图7(b)可以看出:大球与中球主要向90°面角集中,大球与中球质量分数之和为78.50%;而小球主要向45°面角汇聚,小球质量分数为47.95%。图7(c)所示为在90°-75°-75°-45°衬板组合下钢球的空间分布情况。从图7(c)可以看出:前3段钢球分布比较均匀,而第四段小球质量分数较高,为53.49%。图7(d)所示为在75°-75°-45°-45°衬板组合下钢球的空间分布情况,可以看出,大球与中球主要集中在第二段,两者质量分数之和为81.53%。
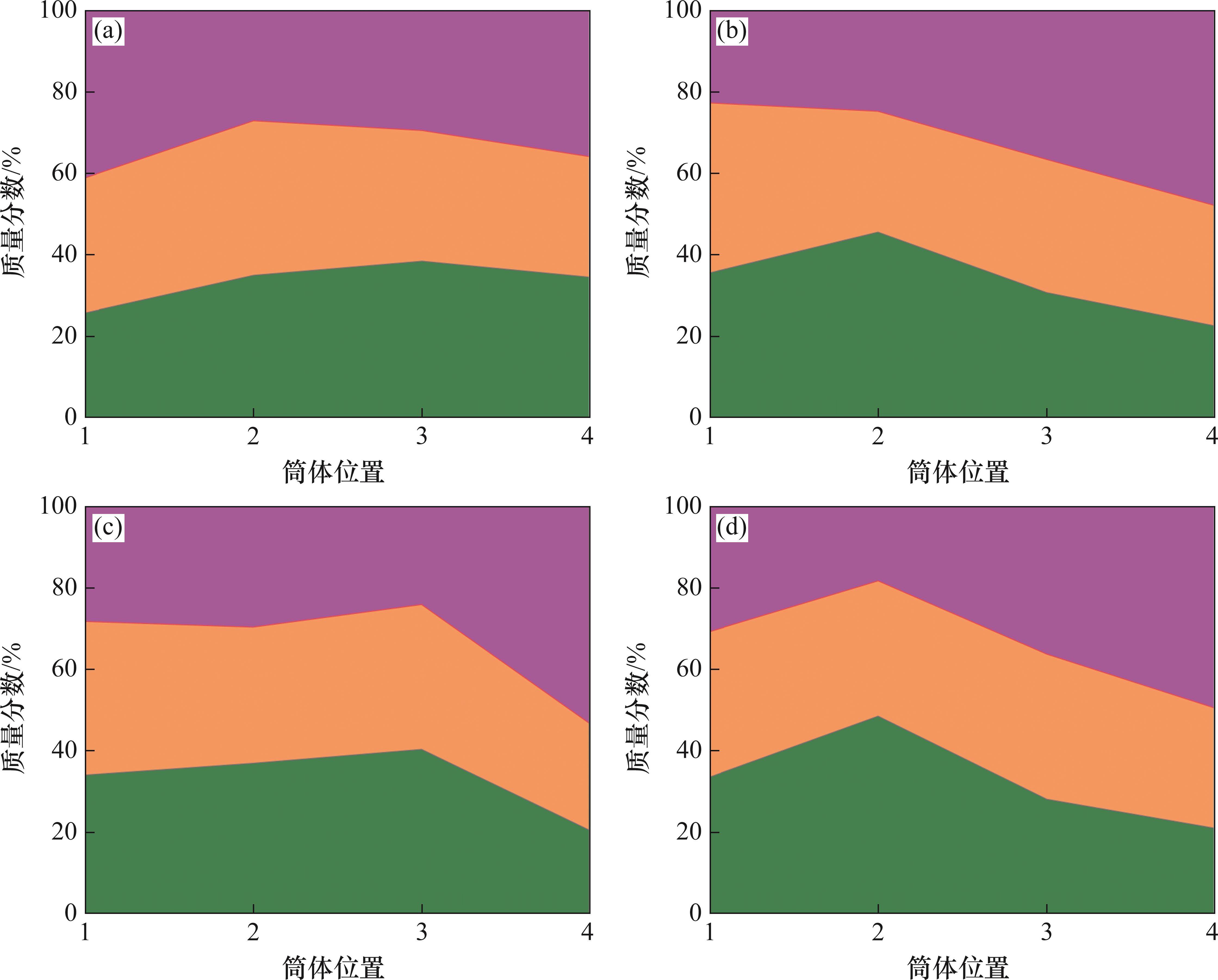
从以上分析可知,筒磨机中衬板组合会显著影响钢球尺寸的轴向空间分布,不同的衬板组合对应着特定的钢球质量分数空间分布,因此,可以通过优化衬板组合来调控钢球的空间分布。研究结果表明,筒磨机的入料端矿石的尺寸较大,出料端矿石尺寸较小。为了实现大球冲击大矿石、小球研磨小矿石的选择性磨矿效果,有必要科学、合理布置衬板。从图7可见:90°-75°-45°-45°衬板组合能更好地实现大球集中于入料端,小球分布在出料端,从而实现高效选择性磨矿。
衬板组合对筒磨机的运行功率的影响如图8所示。由图8可知:衬板组合会影响磨机的运 行功率,75°-75°-75°-75°、90°-75°-45°-45°、90°-75°-75°-45°与75°-75°-45°-45°衬板组合下 磨机运行功率分别为801.26、789.23、788.38与795.25 W。因此,可以通过优化衬板结构组合达到磨矿节能的效果。筒磨机在运行过程中,转速率同样会影响钢球的运动状态,有必要研究转速率对不同衬板结构组合下钢球功率的空间分布。

2.4 转速率对不同衬板组合下钢球轴向离析的影响
为了进一步考察转速率对不同衬板组合下钢球尺寸轴向空间分布的影响,将单段筒磨机再分成两段统计,采样点数加倍,由4个点变为8个点,规定整个筒体左端为入料端,右端为出料端,从左往右依次命名为1、2、3、4、5、6、7和8。对4种衬板组合在转速率为65%与75%下钢球的质量分数分布进行统计,结果如图9所示。由图 9(a)、(b)可知:转速率越大,小球向出料端更富集,由于第一段筒磨机受壁面效应的影响,导致小颗粒在其附近集中,但转速率增加会减弱壁面效应;当转速率为65%时,第二段到第七段中小球的质量分数均小于平均值,而当转速率为75%时,后3段的小球的质量分数明显提高。由图 9(c)、(d)可知:转速率对中球的空间分布状态影响较小,4种衬板组合中各个位置的中球质量分数在平均值附近波动。由图9(e)、(f)可知:当转速率为65%时,大球主要集中在第二段到第七段;随着转速率增加,大球向入料端转移。
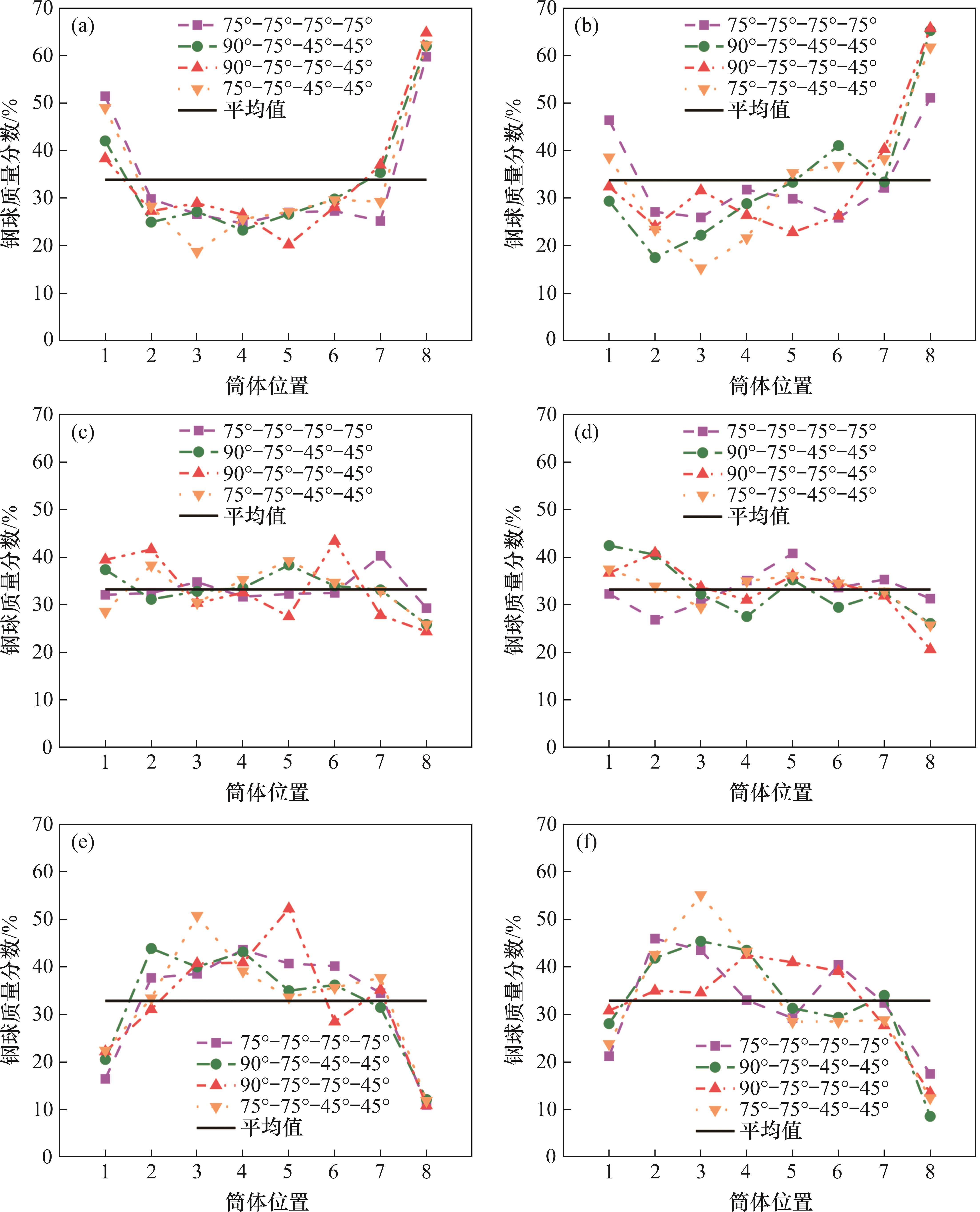
由图7(b)与图9可知:90°-75°-45°-45°衬板组合可更好地实现大球集中在入料端,小球富集在出料端,从而实现大球冲击大矿石、小球研磨小矿石的选择性磨矿。以90°-75°-45°-45°衬板组合为研究对象,研究55%、65%、75%、85%与95%转速率下钢球数量的轴向空间分布特征,并以入料端小球的数量来表示轴向离析程度,结果如图10所示。由图10可知:随着转数增加,最后一段小球的数量呈现线性波动增加;当转速率由55%变化到65%时,最后一段小球数量增加显著,由534个增加到603个;当转速率继续从65%增加到85%时,小球数量只增加了56个;若再继续提高转速率至95%,最后一段小球的数量较转速率为85%时的659个降低到597个,说明当转速率超过一定值时,小球轴向离析程度降低。出现这种现象的主要原因是:随着转速率增加,磨机中的钢球会产生离心运动,钢球之间的相对运动减小,阻碍了小尺寸钢球的轴向穿层运动。
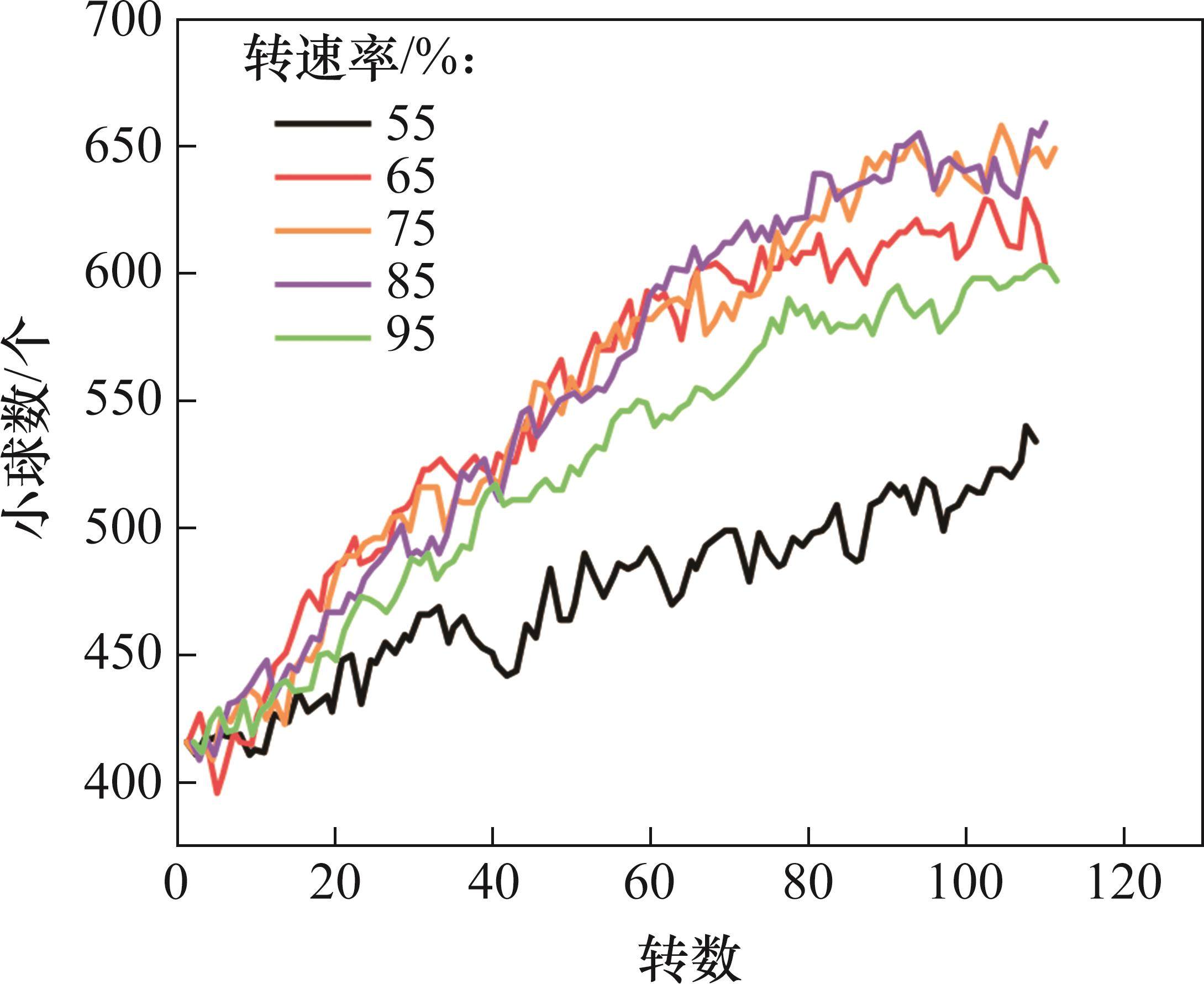
对不同转速率下的磨机功率进行统计,结果如图11所示。从图11可知:随着转速率增加,磨机的功率呈现先增加后降低的趋势;当转速率为65%~85%时,磨机的功率变化不显著,当转速率低于65%或超过85%时,磨机功率变化较大,这与文献[25]中的试验结果一致。在实际生产过程中,磨机的转速率一般为75%~85%。数值模拟结果也证实了在这个转速率范围内,磨机功率最高且稳定。
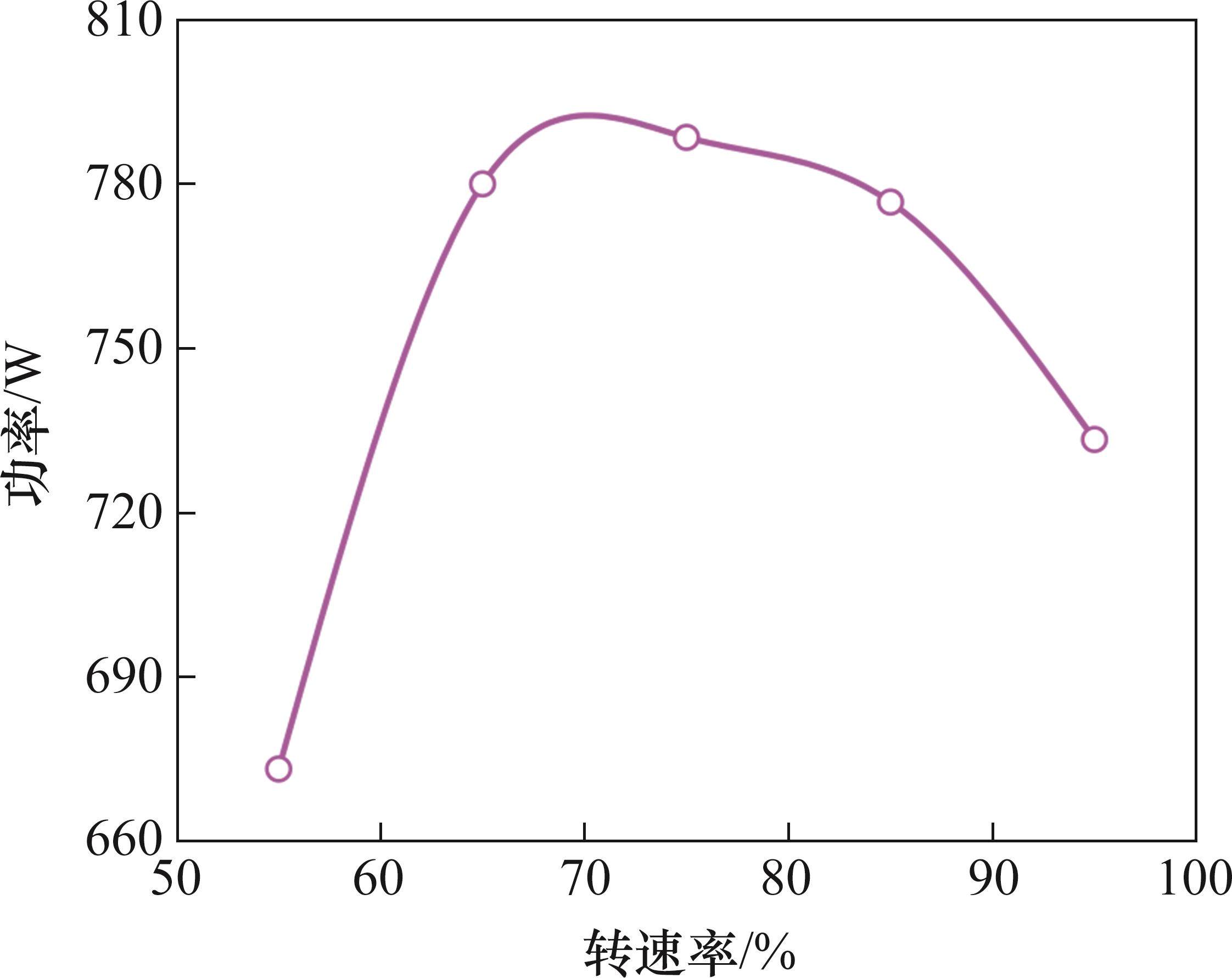
3 结论
1) 提升条面角显著影响磨机内钢球的运动特性。当提升条面角为90°时,钢球提升高度大,主要以抛落为主,但钢球累积动能较75°与45°时的小。
2) 衬板组合会影响钢球的轴向空间分布,其中,90°-75°-45°-45°衬板组合可更好地实现大球集中在入料端、小球富集在出料端,从而实现大球冲击大矿石、小球研磨小矿石的选择性磨矿。
3) 在一定的转速率范围内,增加转速率会加快磨机内钢球向轴向空间分布,但当转速率超过某个特定值时,反而会降低钢球向轴向空间分布。
4) 提升条面角、衬板结构组合以及转速率均会影响磨机功率,对于特定的衬板结构存在最优的磨机转速率。
周强, 汪轶凡, 肖庆飞, 等. 衬板改型优化钢球轴向空间分布及改善磨矿效果的数值模拟研究[J]. 中南大学学报(自然科学版), 2024, 55(12): 4422-4430.
ZHOU Qiang, WANG Yifan, XIAO Qingfei, et al. Numerical simulation study on optimizing axial spatial distribution of steel balls and improving grinding efficiency through liner modification[J]. Journal of Central South University(Science and Technology), 2024, 55(12): 4422-4430.