隧道作为穿越深山峡谷、江河湖海的控制性工程,已成为现代综合交通运输体系中不可或缺的部分。然而,火灾事故的风险及危害性不容小觑,一度成为社会安全的重点关注问题[1-2]。由于内部空间封闭、通风排烟条件差、救援通道不足,隧道火灾安全保障面临极其严峻的挑战。如何高效并快速排出火灾产生的高温有毒烟气,避免受困人员吸入过量烟气而窒息,成为亟待解决的难题[3-4]。近年来,结合纵向和横向排烟的侧向集中排烟模式,在实际工程中得到了广泛应用[5],其优势在于可充分利用隧道结构特性,增强防救灾的功能和灵活性。然而,侧向集中排烟的潜能尚未被完全挖掘[6]。由于纵向气流和横向气流均存在于系统中,烟气在隧道、排烟口及排烟道等受限空间约束下的运动极其复杂,排烟过程中产生的各种烟气流动现象严重影响排烟效率,排烟系统设计仍待优化。目前,学者们针对烟气层吸穿现象展开了大量研究[7-9],发现了吸穿对排烟的不利影响,同时指出排烟口参数及排烟策略是其关键影响因素[10-11]。然而,除烟气层吸穿外,还会发生边界层分离现象[12-13],引起烟气过流面积减少,使得本身就较小的排烟空间其有效利用率极低。YAO等[14]分析了竖井倾斜角对排烟的影响,发现倾斜角较小时有效排烟面积亦较小,不利于排烟。XU等[15]研究发现,侧向集中排烟模式下因排烟口尺寸较小,火源热释放速率较大时极易发生边界层分离,且排烟口参数和排烟速率具有较大影响。XU等[16]研究发现,侧向集中排烟模式下边界层分离同时发生在排烟口及排烟道内,并通过分析不同排风量下各边界层分离区域面积及其占比的变化规律,得到了有效排烟面积。由此可见,在隧道火灾排烟边界层分离研究方面,多集中于现象及影响因素分析,较少关注有效排烟空间与排烟效率的关系,不足以为侧向集中排烟系统优化设计提供充分依据。基于此,本文考虑侧向集中排烟模式下边界层分离的影响,量化分析有效排烟空间。通过某3车道沉管隧道火灾缩尺模型试验,观察分析排烟口及排烟道内边界层分离现象。结合数值模拟,揭示有效排烟空间与排烟效率的关系,提出排烟口设置与排烟策略优化设计参数。研究工作旨在充分挖掘侧向集中排烟系统潜能,为高效排烟提供科学依据,对于提升隧道火灾安全保障能力具有重要意义。
1 缩尺模型试验
1.1 缩尺模型概况
缩尺模型按照某3车道沉管隧道1∶10建造,长30 m,宽1.5 m,高0.7 m,如图1所示。模型一侧设置排烟道,长30 m,宽0.45 m,高0.35 m。隧道侧壁设置排烟口,以连接隧道与排烟道,共5组,每组间距6.75 m。每组内设置3个排烟口,长0.4 m,高0.2 m,宽0.1 m,可实现单个排烟口间距0.2~0.6 m,高度0.5~0.6 m,宽高比1:2~2:1调节,如图2所示。同时,模型配备通风排烟系统,包括集烟罩、整流格栅与变频射流风机、变频排烟风机等,以满足通风排烟试验需求。
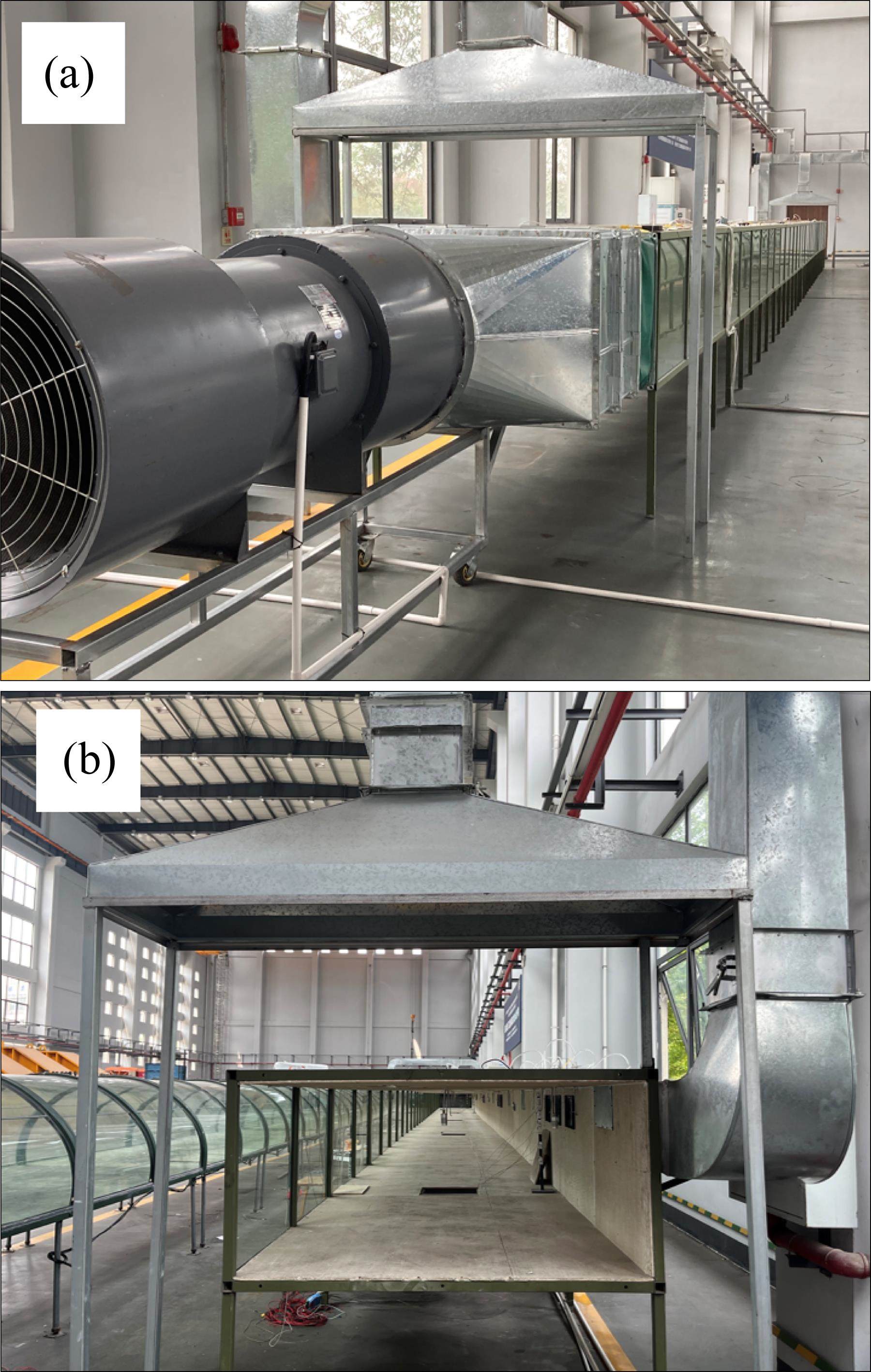
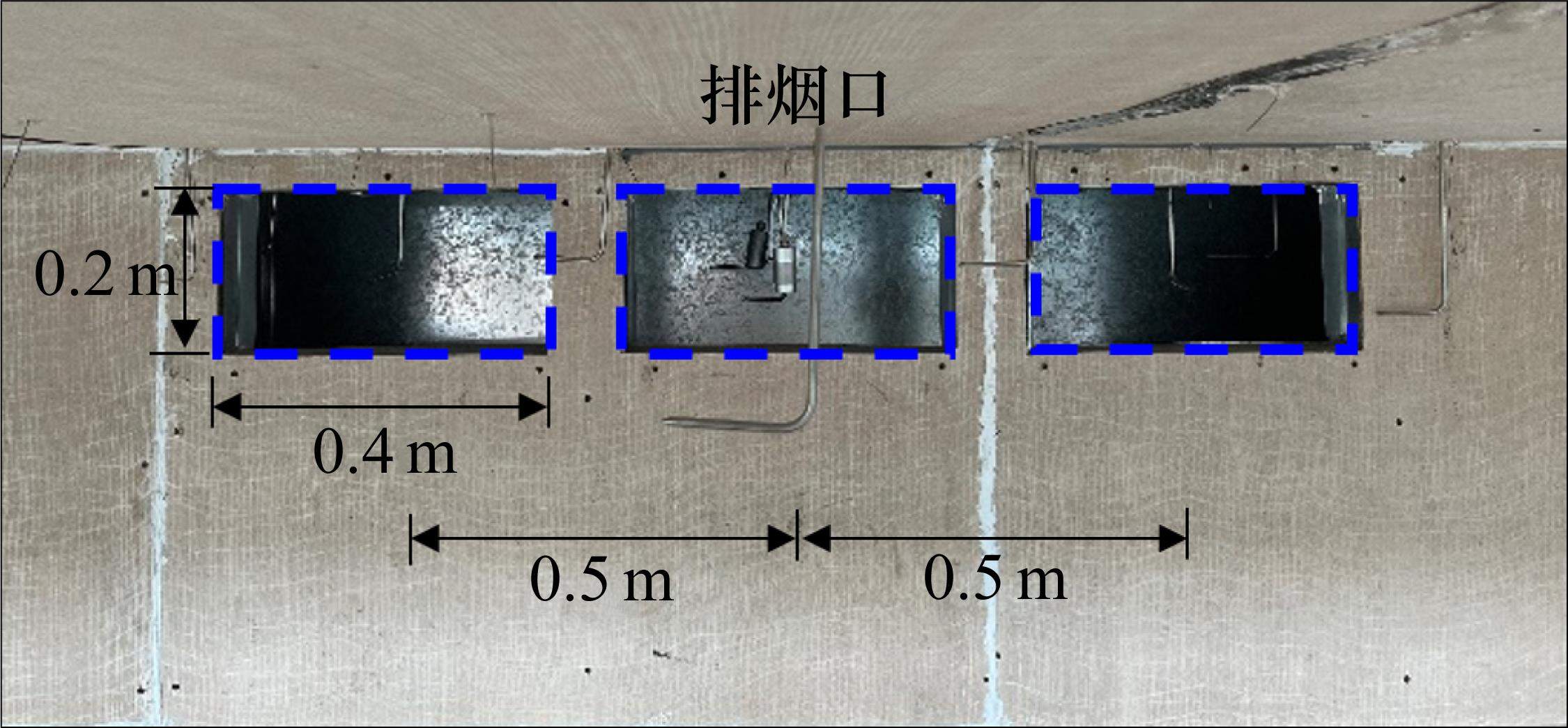
1.2 火源标定及设置
为避免高温有毒烟气造成的污染,采用清洁燃料无水乙醇,其纯度为99.7%。为确定不同尺寸油盆下火源热释放速率,通过电子天平测量燃料质量损失速率,计算其热释放速率,如式(1)所示。
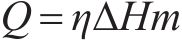
式中:Q为热释放速率,MW;η为燃烧效率,一般取值为0.8~0.9;ΔH为燃料的燃烧热值,MJ/kg,无水乙醇为29.7 MJ/kg;m为燃料质量损失速率,kg/s。
火源标定如图3所示。根据标定结果,可确定不同热释放速率下所需的油盆尺寸,如表1所示。
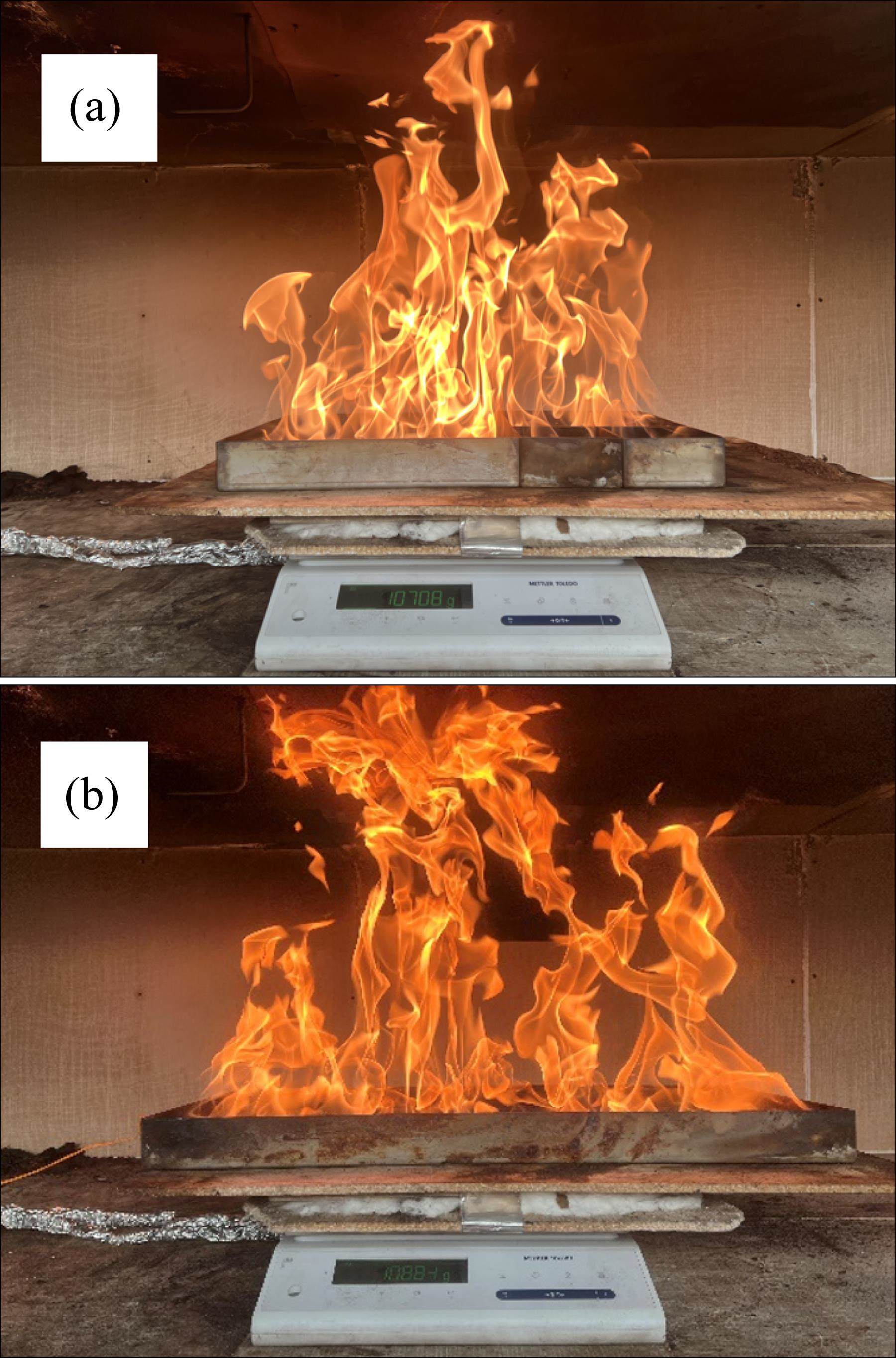
编号 | 油盆尺 寸/cm | 缩尺热释放速率/kW | 足尺热释 放速/MW |
---|---|---|---|
1 | 20×20 | 15.81 | 5 |
2 | 50×30 | 63.25 | 20 |
3 | 70×30 | 94.87 | 30 |
4 | 70×50 | 158.1 | 50 |
由此,可分别代表真实隧道中小汽车、大型客车、载重货车发生火灾时的最大热释放速率[17]。由于火灾发生的随机性,火源可能出现在隧道内任何位置。然而,火灾发生在某组排烟口正下方的概率相对较低,故本文将火源位置设为2组排烟口中部。此外,研究发现[18-19]临界纵向风速及最小排烟风量下,侧向集中排烟系统开启火源下游4组排烟口时,烟气能被较好地控制在300 m内,满足规范要求[20]。因此,本文将火源及烟饼置于第1组和第2组排烟口中心位置。
1.3 观测系统及测点布置
测量系统包括皮托管、微差压传感器及采集模块,以测量烟气流速。在隧道、排烟口、排烟道内设置烟气流速测点,并按照隧道、排烟口处(隧道侧壁)、排烟口内、排烟道内纵向进行布置,如图4所示。
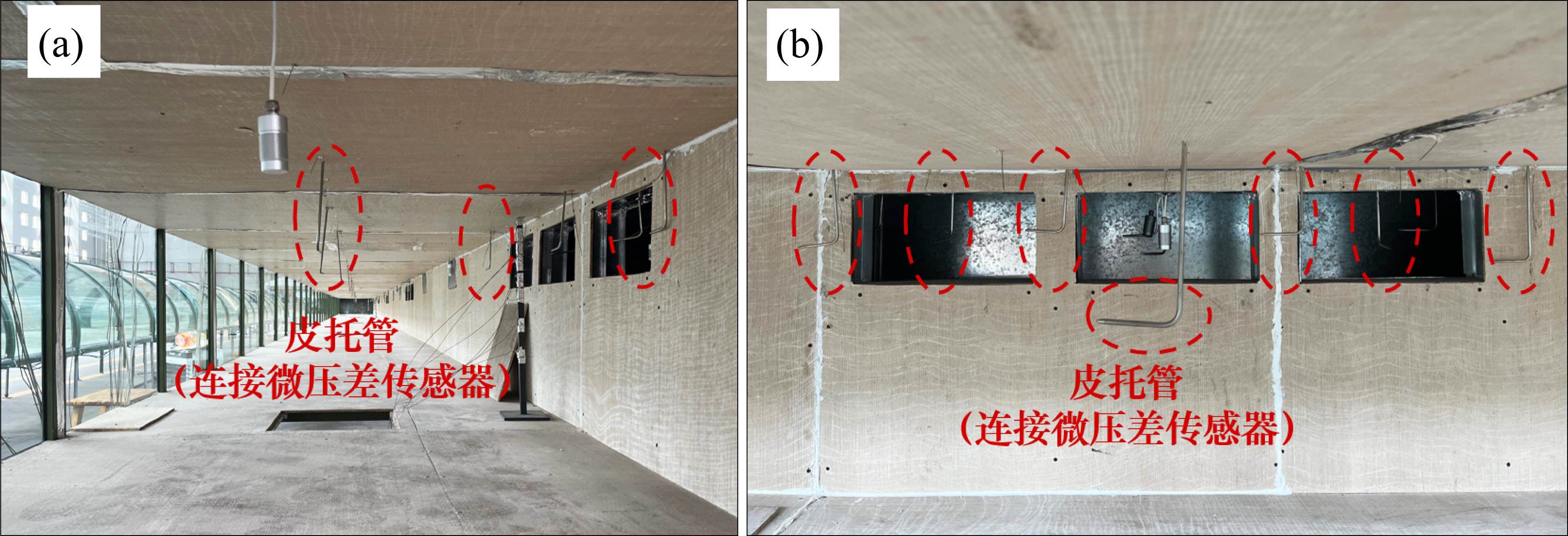
采用发烟量较大的特级烟饼模拟隧道火灾产生的烟气,同时利用出光张角和片光方向可调节的激光片光源和高清摄像机观测火源及烟气流动现象。试验现场如图5所示。
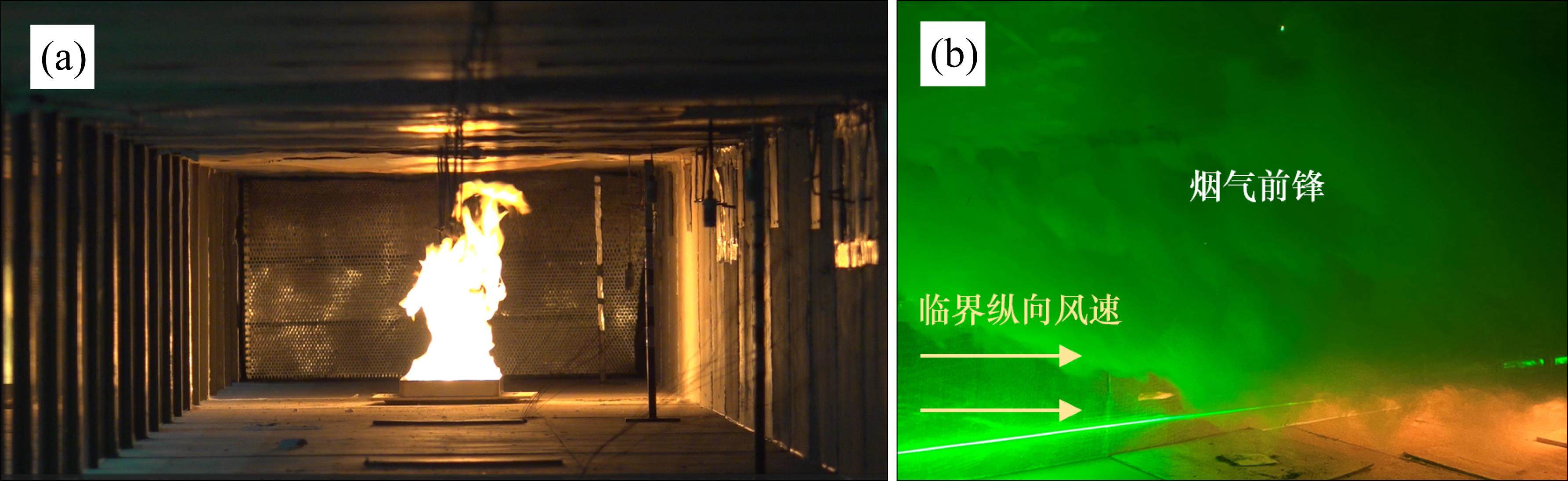
模型试验可直观展示边界层分离等烟气流动现象,但无法精确量化有效排烟空间大小,且测点布置受限,模拟较大火源热释放速率时也极具危险,故本文将结合数值模拟方法作进一步探究[21]。
2 数值模拟
2.1 仿真模型及边界条件
如何测量有效排烟空间至关重要,这依赖于边界层分离区的判定。根据普朗特分离判据,边界层分离可通过烟气纵向和横向流速判定,即排烟口或排烟道内边界层分离的临界判据为烟气流速沿纵向和横向流动的任一分量小于等于0[16]。因此,烟气流速测点间距应足够小,以避免测点布设间距过大而造成的误差,并且应能测量烟气沿不同方向的流速。本研究采用在隧道火灾领域得到广泛应用和可靠性验证的仿真模拟软件FDS,其优势在于可以通过布设3D速度切片及后处理提取每个网格对应的精细化数据。这样,不仅可获得满足研究需求的精细化数据,还能节省因实体试验或模型试验测点密集布设而耗费的巨额资金。
依据某实际隧道建立仿真模型,该仿真模型为缩尺模型试验的原型,如图6所示(以排烟口宽高比1∶2为例)。由于临界纵向风速下烟气不再往火源上游蔓延,因此仅设置火源下游4组排烟口。每组排烟口设为3个,单个排烟口间距固定为3 m、面积为2 m2。隧道入口设为入风口,即模拟射流风机提供纵向风速;排烟道出口设为出风口,模拟排烟风机即提供排风量。环境温度设为20 ℃。
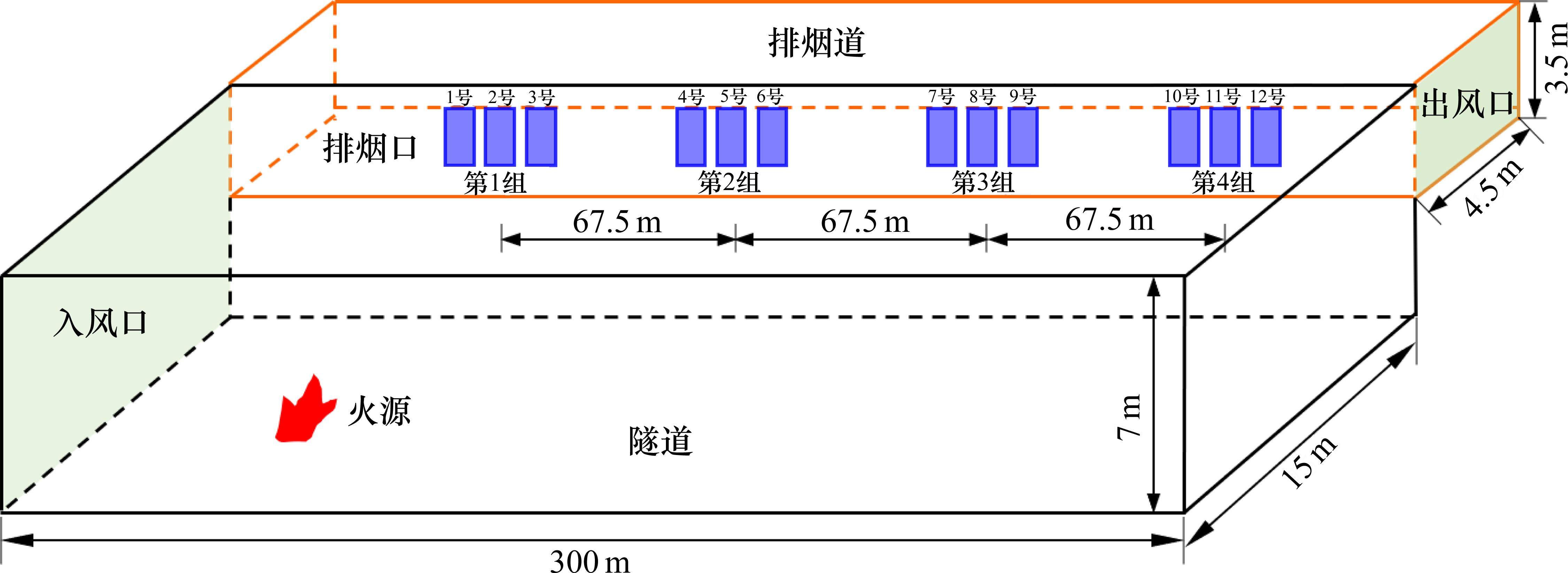
依据工程实际情况,本文将火源按重型货车发生火灾考虑,即火源热释放速率依据该隧道的火灾设防标准设为50 MW。火源位置与缩尺模型试验保持一致。
为测量烟气流速大小以求得有效排烟空间,在排烟口及排烟道内设置3D速度切片。同时,为获得排烟效率,本文选取CO2质量流率代替烟气质量流率[22-24],并布置CO2质量流率测量设备。
2.2 网格划分与工况设置
根据火源特征直径计算式[25],可得到火源热释放速率为50 MW时,建议网格尺寸为0.3~1.2 m。考虑仿真模型在3个维度的尺寸存在较大差异及计算精度、时间等多种因素,模型采用2套网格。网格敏感性通过排烟口中心高度处隧道侧壁烟气流速分布进行了分析,如图7所示。最终确定隧道及排烟道选用0.50 m×0.30 m×0.30 m的非立方体网格,排烟口选用0.10 m×0.10 m×0.10 m的立方体网格。
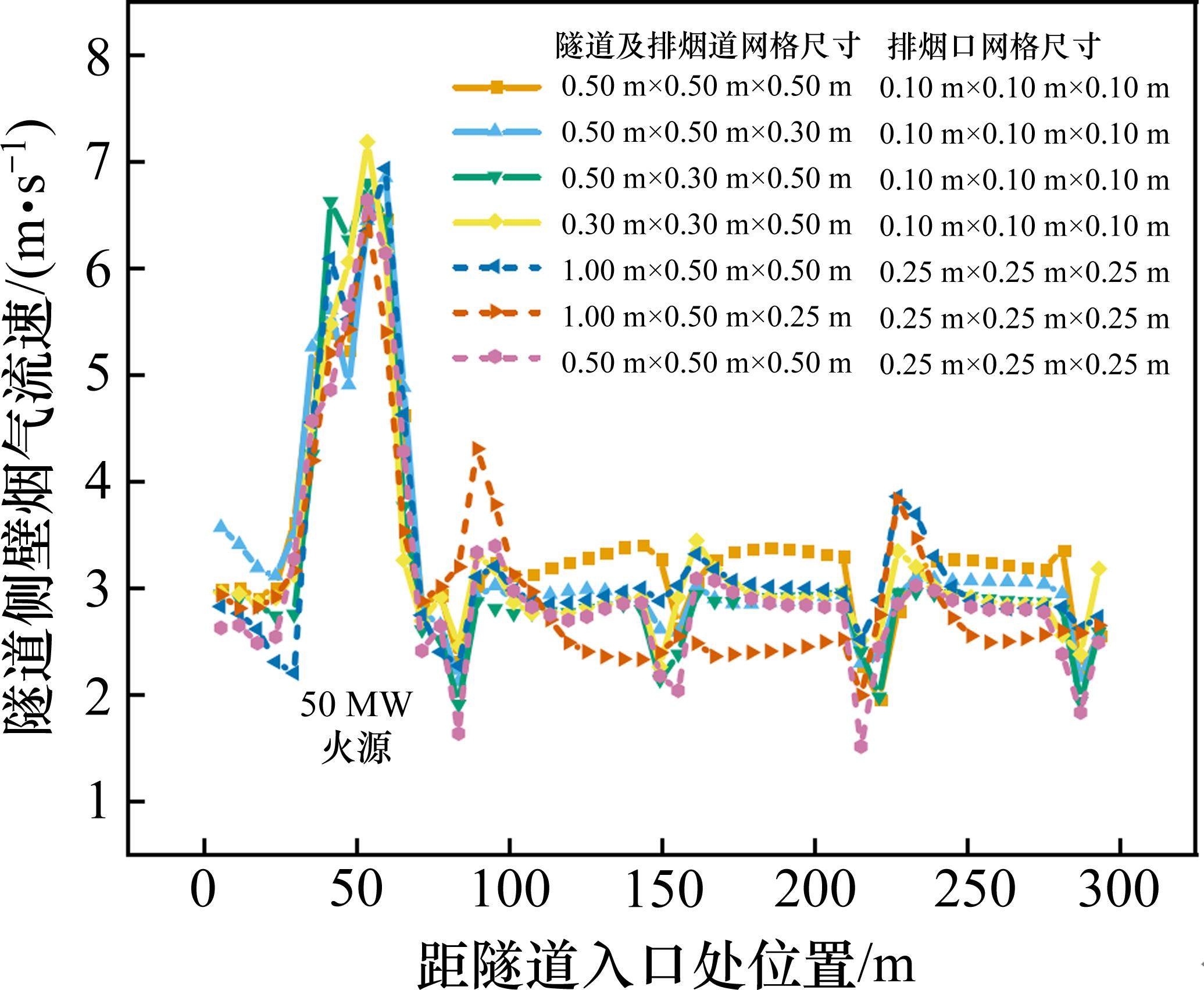
由于开展50 MW缩尺模型试验极具危险性,基于Froude相似原理,将缩尺模型试验5,20和30 MW下排烟口内烟气流速换算为足尺试验中的烟气流速,与数值模拟结果进行对比,以验证有效性,如图8所示。结果表明,3种火源热释放速率下数值模拟与缩尺模型试验所测得的排烟口内烟气流速误差最大不超过10.4%,证明数值模拟结果可靠。
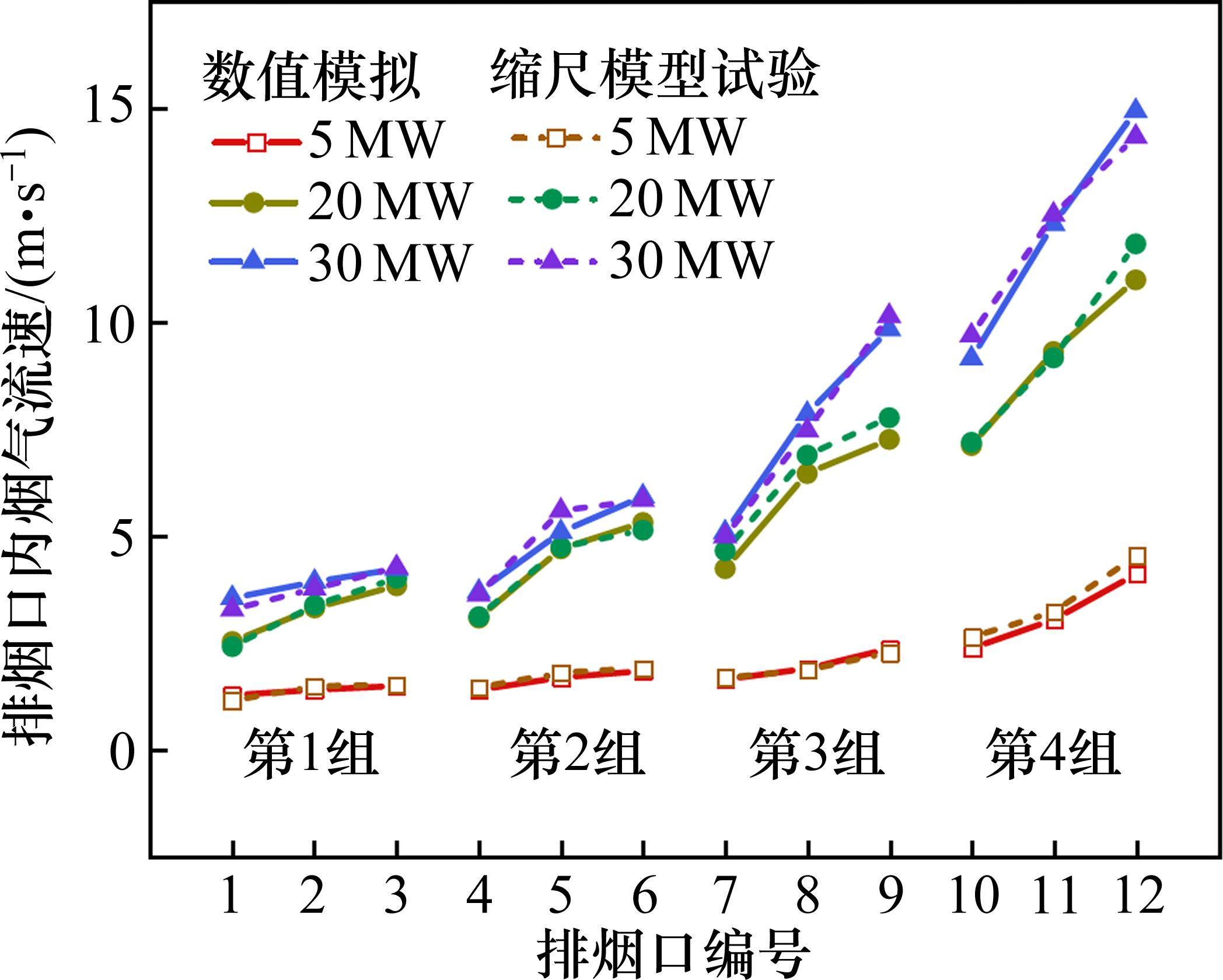
为探究排烟风量Vf、排烟口宽高比n、排烟口布设高度h的影响,本文设置工况如表2所示,且数值模拟工况与缩尺模型试验相同。为方便对比各因素的影响,A4与B1设为同一工况、B5与C3设为同一工况。其中,工况A1与实际隧道排烟系统设计方案相同。
影响因素 | 工况编号 | Vf /(m3∙s-1) | n | h/m |
---|---|---|---|---|
排烟风量(Vf) | A1~A5 | 240,280,320,360,400 | 1:2 | 5.5 |
排烟口宽高比(n) | B1~B5 | 360 | 1:2,3:4,1:1,4:3,2:1 | 5.5 |
排烟口布设高度(h) | C1~C5 | 360 | 2:1 | 5.0,5.25,5.5,5.75,6.0 |
3 结果与分析
3.1 排烟口及排烟道内边界层分离现象
侧向集中排烟模式下,隧道火灾产生的烟气在纵向风驱动下沿隧道纵向往火源下游流动,一部分烟气在排烟口处受横向抽吸作用,由隧道向排烟口内流动,即“隧道-排烟口”排烟过程。另一部分烟气仍继续往下游流动,直至遇到下一排烟口。流入排烟口的烟气,在惯性力作用下流入排烟道,而后又在纵向抽吸作用下,向排烟道下游流动,即“排烟口-排烟道”排烟过程。
上述过程中,因“隧道-排烟口-排烟道”连接型式的特殊性,即边壁多次发生突变,导致烟气流速大小和流动方向发生变化,进而造成烟气与边壁发生脱离,靠近边壁的区域内烟气因受摩擦阻力作用而停止流动或发生回流,形成低速区。从缩尺模型试验中可以发现,每个排烟口所在位置分别形成3个边界层分离区,如图9所示。其中,边界层分离区Ⅰ和Ⅱ位于排烟口内,边界层分离区Ⅲ位于排烟道内。数值模拟中也可观察到侧向集中排烟中排烟口处所发生的边界层分离现象,如图10所示。可见,边界层分离区的存在使有效排烟空间减小,制约烟气从隧道向排烟口内横向流动以及从排烟口向排烟道内纵向流动,严重影响排烟效率。
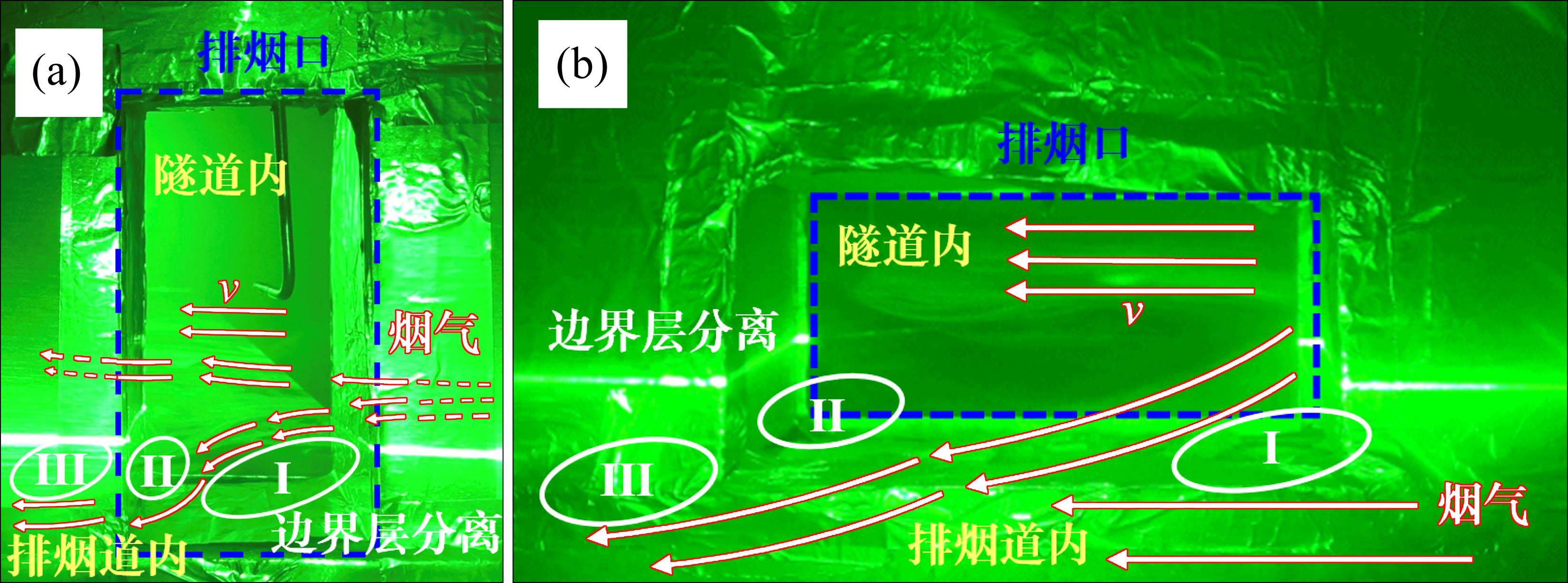
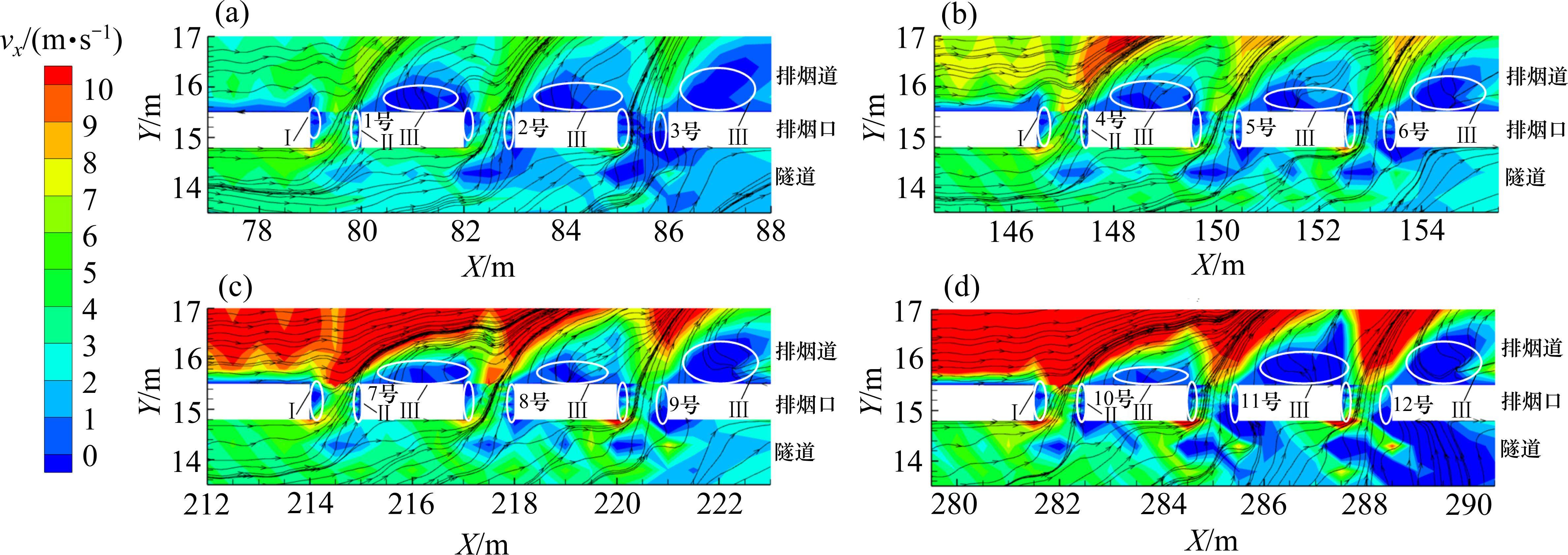
3.2 有效排烟空间与排烟效率
为量化有效排烟空间大小,定义有效排烟空间为除边界层分离区外的排烟空间体积与原排烟空间体积的比例。其中,排烟口有效排烟空间为

式中:Vsv为排烟口体积;Vbs1、Vbs2分别为边界层分离区Ⅰ、Ⅱ的体积。其中,边界层分离区体积根据烟气流速判定后,筛选边界层分离区所在网格,再由网格大小计算其体积。
排烟道有效排烟空间为

式中:Vsd为排烟道体积(排烟口下游处);Vbs3为边界层分离区Ⅲ的体积。
排烟效率基于数值模拟所测CO2质量流率进行计算[26],即
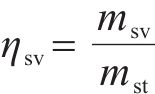
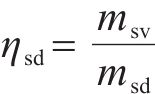
式中:ηsv、ηsd分别为“隧道-排烟口”、“排烟口-排烟道”排烟过程中排烟效率,即排烟口排烟效率、排烟道排烟效率;mst为隧道内(排烟口上游处)CO2质量流率;msv为排烟口内烟气质量流率;msd为排烟道内(排烟口下游处)CO2质量流率。
由于排烟口数量多,取各组排烟口有效排烟空间与排烟效率的平均值进行分析,即从单组排烟口的角度展开分析。不同影响因素下排烟口及排烟道有效排烟空间与排烟效率如图11所示。可以发现,“隧道-排烟口”排烟过程中有效排烟空间改变时,其排烟效率变幅较大;“排烟口-排烟道”排烟过程中有效排烟空间改变时,其排烟效率几乎不变。由此可说明排烟口内边界层分离区的存在极大地影响了其排烟效率,而排烟道内边界层分离区的存在对排烟效率的影响较小。
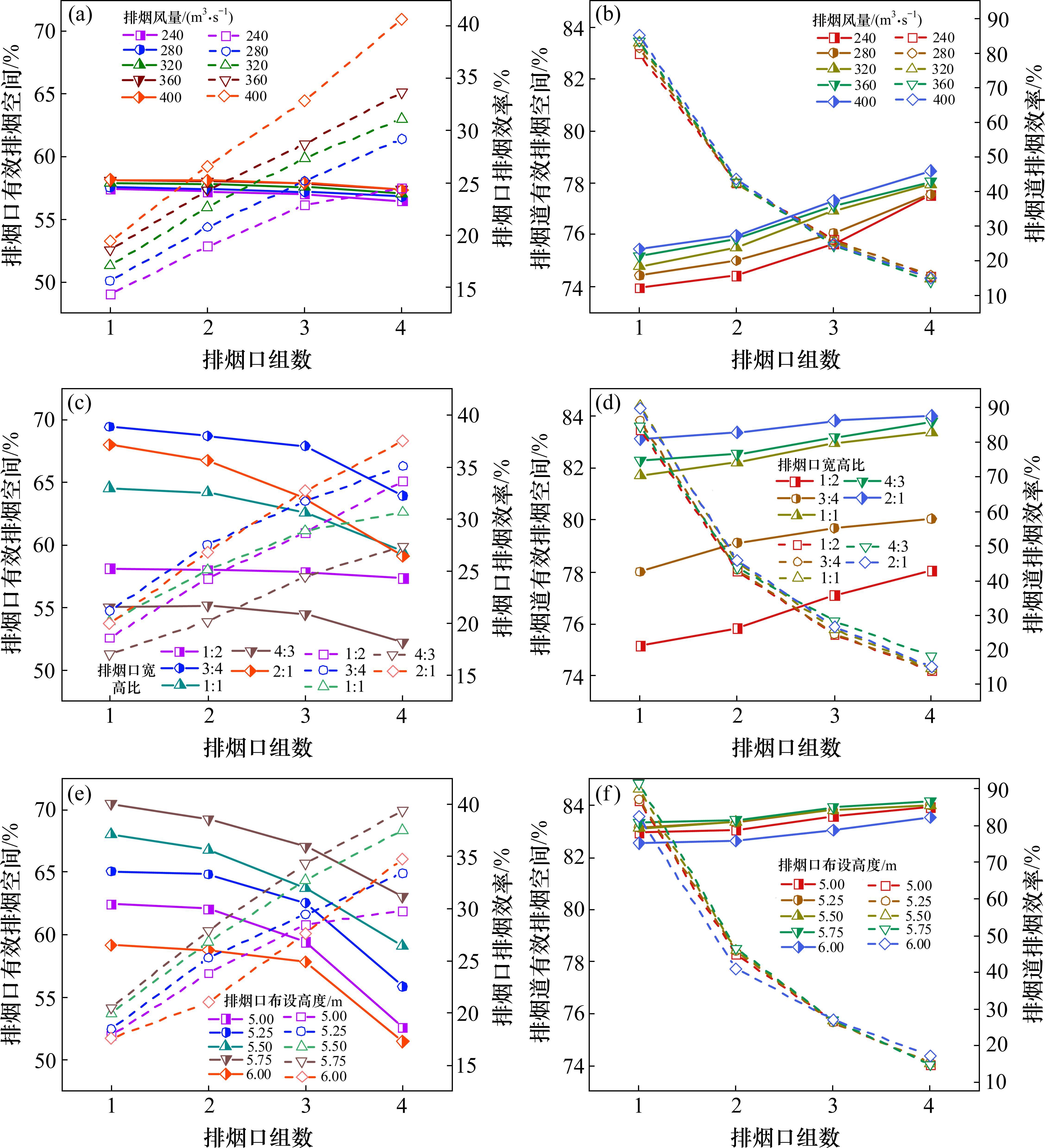
由图11还可以发现,“隧道-排烟口”排烟过程中,排烟效率随单组排烟口距离的增加而增大,即靠近排烟风机处的第4组排烟口排烟效率最大,但难以高于40%,且有效排烟空间不超过64%;而在“排烟口-排烟道”排烟过程中,排烟效率随单组排烟口距离的增加而减小,即靠近火源的第1组排烟口排烟效率最大,接近90%,且有效排烟空间不低于73.9%。由此可知,为提高排烟效率而优化侧向集中排烟系统时可不考虑边界层分离区Ⅲ,应重点关注如何避免排烟口内边界层分离对排烟效率造成的负面影响。
排烟口和排烟道内有效排烟空间均与排烟效率均呈负相关关系,即随着有效排烟空间的增大,排烟效率反而降低,这似乎并不合理,并不能说明边界层分离的存在会对排烟效率造成负面影响。分析原因可知,有效排烟空间可代表烟气过流面积,而排烟效率根据烟气质量流率计算,不仅与烟气过流面积有关,还与排烟速率有关。因此,排烟效率与有效排烟空间的关联性并不能直接通过两者的数值大小进行比较,还需考虑排烟速率大小。为此,将排烟口及排烟道内排烟速率无量纲化,得到各影响因素下有效排烟空间和无量纲排烟速率两者乘积与排烟效率的对比,以此表明边界层分离对排烟效率造成的影响,如图12所示。
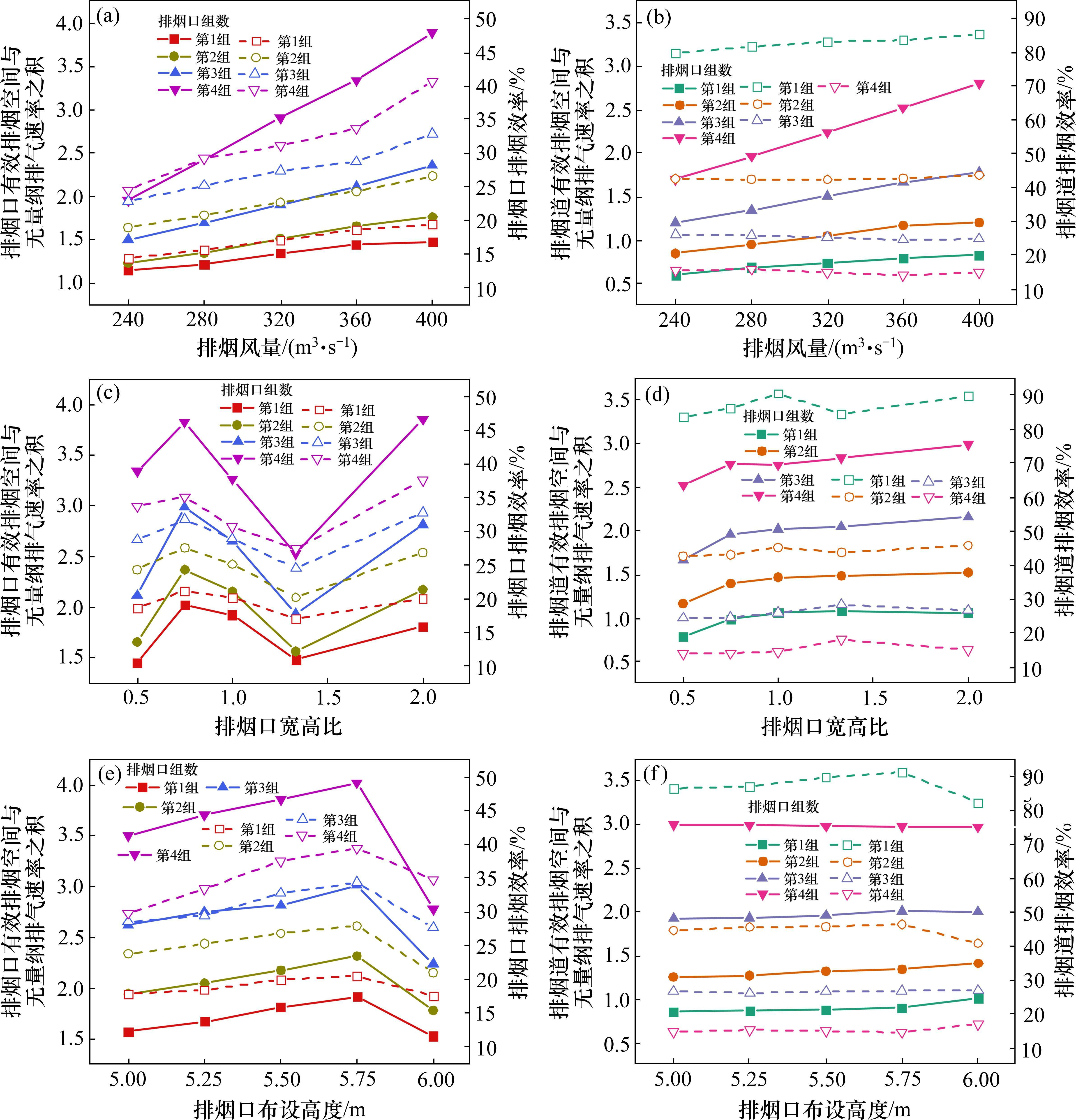
由图12可知,ηsv和ηsd分别与
同时,可以发现,排烟口内边界层分离在排烟口宽高比n=2∶1、排烟口布设高度h=5.75 m、排烟风量Vf=360 m3/s得到有效抑制时,其对应的排烟效率高。相较于某实际隧道现有排烟系统设计,各组排烟口排烟效率可提高6.2%~14.9%。这表明通过优化排烟口参数设计与排烟策略时,可削弱边界层分离对排烟效率的负面影响,提高有效排烟空间。
然而,各组排烟口排烟效率差距仍然较大,这并不能通过优化排烟口参数设计与排烟策略得以实现。因此,结合图11中排烟效率难以高于40%,以及排烟口有效排烟空间随排烟口组数增大而减小的规律,可知各组排烟口排烟效率仍有提升空间,可设法通过干预排烟口内边界层分离区的大小及排烟速率实现。例如,在排烟口内加装排烟阀片[27],在改变烟气流动方向对边界层分离进行干预的同时,实现各组排烟口均匀排烟以优化排烟速率。如此,既可干预离排烟风机较近的排烟口内边界层分离区大小,又能提高离排烟风机较远的排烟口内排烟速率。
由上述分析可知,排烟风量与排烟道、排烟口几何参数是影响有效排烟空间的重要因素。此外,由于各排烟口间的距离相差较大,导致不同排烟口处有效排烟空间差异较大。因此,排烟口位置也是影响有效排烟空间的重要因素,即排烟口与火源的距离。
进一步,从侧向集中排烟系统的角度分析排烟效率与有效排烟空间,如图13所示,可以发现有效排烟空间与排烟效率间呈正相关关系。对比排烟口与排烟道排烟效率及有效排烟空间可知,尽管排烟口有效排烟空间(54.2%~67.5%)小于排烟道有效排烟空间(75.4%~83.7%),但排烟口有效排烟空间改变时可大幅提高排烟效率(65.7%~93.3%),而排烟道有效排烟空间改变时排烟效率变化不大(71.1%~80.4%),再次说明排烟口边界层分离的存在对排烟效率具有明显影响。
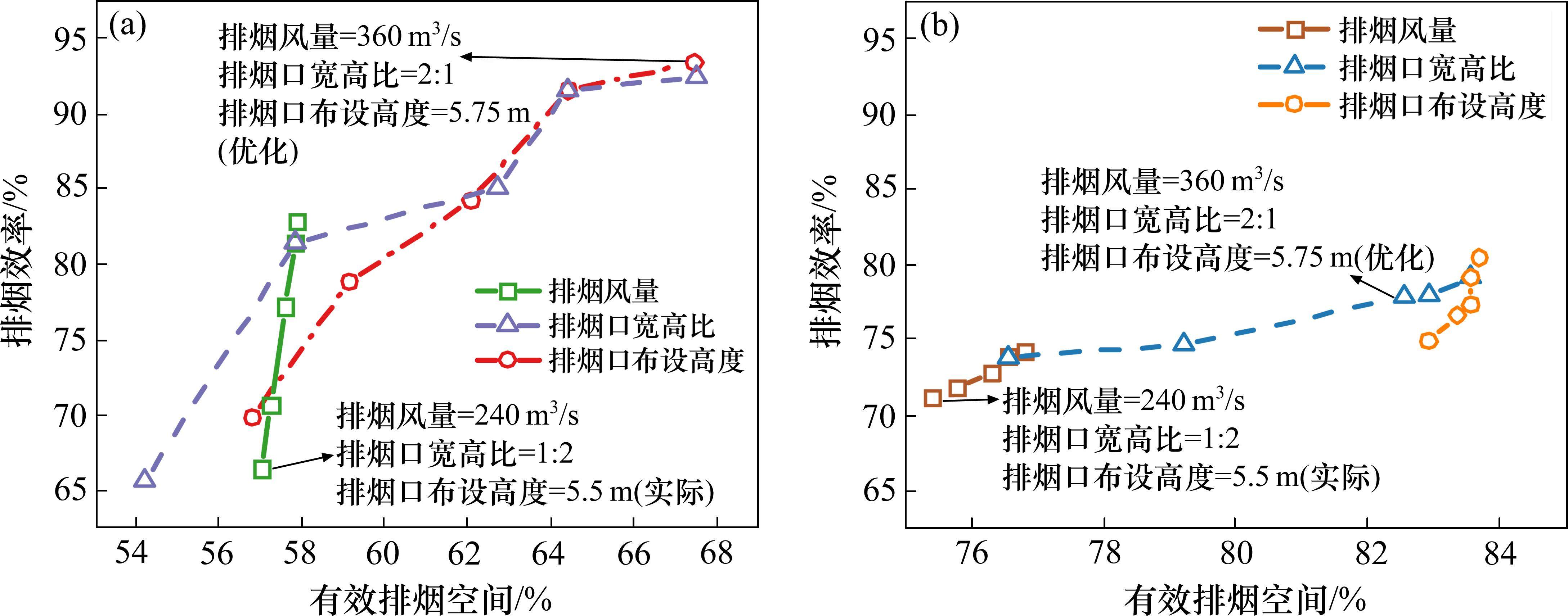
由于侧向集中排烟应重点关注排烟口内边界层分离,现对排烟口排烟效率随有效排烟空间变化的增长幅度展开分析,以说明排烟口参数与排烟策略对排烟效率及有效排烟空间的影响程度。
由图13可知,排烟口宽高比对排烟口有效排烟空间的影响最大(Δχsv=13.3%),排烟效率提升幅度也最大(Δηsv=26.7%);排烟口布设高度对排烟口有效排烟空间的影响次之(Δχsv=10.7%),排烟效率提升幅度也次之(Δηsv=23.5%);排烟风量对排烟口有效排烟空间的影响极小(Δχsv=0.9%),排烟效率提升幅度最小(Δηsv=16.4%)。由此说明排烟口布设高度和宽高比改变而引起的有效排烟空间变化是影响排烟口排烟效率的关键原因,而排烟风量改变而引起的有效排烟空间变化并非影响排烟口排烟效率的主要原因。
因此,通过优化排烟口参数设计对边界层分离进行干预,提升有效排烟空间,是提高侧向集中排烟系统排烟效率的有效举措。排烟口宽高比n=2∶1、排烟口布设高度h=5.75 m、排烟风量Vf=360 m3/s时,边界层分离可得到有效抑制,是最优设计参数,此时排烟系统有效排烟空间χsv为64.4%、χsd为83.6%,排烟系统效率ηsv高达91.5%、ηsd为79.1%。相较于某实际隧道现有排烟系统设计,χsv提升了7.4%,ηsv提升了25.1%,χsd提升了8.2%,ηsd提升了8.0%。
4 结论
1) 隧道侧向集中排烟模式下,因边壁发生突变,各排烟口附近会形成3个边界层分离区,制约烟气由隧道向排烟口、排烟道流动,造成有效排烟空间减小,进而影响排烟效率。
2) 排烟口有效排烟空间较排烟道小,且排烟口内边界层分离对排烟效率的影响较排烟道内大。可忽略排烟道内边界层分离对排烟效率的负面影响,重点关注排烟口内边界层分离,尤其是边界层分离区Ⅱ。
3) 排烟口参数对有效排烟空间及排烟效率的影响大于排烟策略。排烟效率与有效排烟空间、排烟速率密切相关,重视排烟口布设高度、宽高比设计,以有效干预边界层分离、增大有效排烟空间,并提高排烟速率,是提升侧向集中排烟系统性能的关键。
4) 火源热释放速率50 MW下,排烟口宽高比2:1、排烟口布设高度5.75 m、排烟风量360 m3/s时,可有效抑制边界层分离,增大有效排烟空间,提高排烟效率。
朱代强,徐湃,蒋树屏等.考虑边界层分离的隧道侧向集中排烟有效空间及效率研究[J].铁道科学与工程学报,2025,22(02):817-828.
ZHU Daiqiang,XU Pai,JIANG Shuping,et al.Study on effective area and efficiency of lateral concentrated smoke exhaust in tunnel considering the boundary layer separation[J].Journal of Railway Science and Engineering,2025,22(02):817-828.