在城市的建筑密集区进行轨道交通建设,将不可避免地近接或下穿既有建(构)筑物和河流,加之地质条件的复杂多变性,带来极高的施工风险。青岛地铁某区间为双线圆形断面TBM(Tunnel Boring Machine)地铁隧道,其中李村河段为典型的下穿河流隧道。该段地铁隧道水文地质条件复杂,并且李村河常年积水,河水深度常年维持在0.5~1.5 m,地层富水性强且李村河内存在一条破碎带,因此在隧道开挖的影响下,应力场发生变化的同时会引起地下水的运移。不同于单一地层或力学特性相近的地层,隧道在穿越破碎带地层时,由于地层中软硬岩石间不连续的特点,TBM在穿越破碎带过程中极易诱发塌方、大变形、涌水突泥等工程事故,造成TBM卡机停机等危害,对施工造成不利影响[1-4]。在TBM隧道掌子面稳定性研究现状方面,KIRSCH等[5-7]分别采用半尺寸模型试验、透明土模型试验和全尺寸模型试验对盾构掌子面失稳破坏进行了研究,直观展现了不同地层中盾构隧道掌子面失稳形态。陈恺[8]针对饱和软土地层,通过镜像法推导了非达西渗流条件下浅埋圆形盾构隧道周围土体孔隙水压力分布解析解。在数值模拟方面,XUE等[9]以跨高比、隧道埋深、地下水条件、土体渗透性、内摩擦角、土体黏聚力和推进速度为分析指标,运用层次分析法和熵权法确定了各评价指标的权重,构建了下穿河流盾构施工掌子面稳定性评价模型,为掌子面稳定性评估提供了定量分析的方法。DANG等[10]建立了有限元-离散元耦合的数值分析模型,分析了掌子面的压力分布,真实再现了掌子面破裂、滑移及失稳的全过程。隧道穿越破碎带围岩稳定性及控制技术方面,冯非凡等[11]考虑注浆对既有隧道横向收敛、混凝土应力以及螺栓应力的影响,建立注浆对既有隧道作用的计算模型。袁国栋[12]以深圳地铁7号线盾构隧道穿越断层破碎带工程为例,采用数值模拟方法分析了盾构隧道穿越断层破碎带施工力学响应,并对加固方案进行了优化。王晓杰等[13-14]以青岛地铁过海区间穿越破碎带为研究对象,对施工风险进行了评估,分析了隧道施工围岩稳定性并提出了施工安全控制措施。前人针对TBM施工的掌子面稳定性、空间变形规律及施工控制措施等开展了较多的研究,但对于青岛地区的风化花岗岩地层缺乏适用性,特别是硬岩地层下穿河流破碎带的变形演化规律及其掘进控制参数需进一步探索。因此,本文以青岛地铁某区间下穿李村河破碎带段为工程背景,深入分析TBM穿越河下破碎带围岩变形规律,通过FLAC3D数值模拟软件,建立三维数值分析模型,研究TBM穿越河下破碎带隧道围岩应力场、位移场和渗流场演化规律,剖析围岩失稳灾变机理;提出破碎带地表注浆加固措施,分析不同注浆范围的围岩加固响应,进一步明确最优注浆加固范围,设计现场注浆加固方案并进行应用;研究合理的双护盾TBM下穿河流破碎带控制参数,确保TBM下穿河流破碎带施工安全,并为类似条件下的工程施工和优化设计提供科学依据。
1 依托工程概况
青岛地铁1号线线路起于东郭庄站,止于王家港站,总体呈南北走向,全长60.11 km,共设置车站41座,全部为地下车站。某区间采用单洞单线圆形断面,采用DSUC型号的双护盾TBM进行隧道掘进,两线间距由小里程端16 m逐渐扩大至33 m,隧道埋深约16.4~31.5 m。右线全长1 370.920 m,左线全长1 352.529 m,TBM开挖外径6.3 m,隧道衬砌采用C50预制钢筋混凝土管片,其外径6.0 m,内径5.4 m,管片厚度0.3 m,每环宽度1.5 m。某区间在K46+385.00~+640段下穿李村河,该段地层为典型的上软下硬岩土复合地层,其地质纵断面如图1所示。
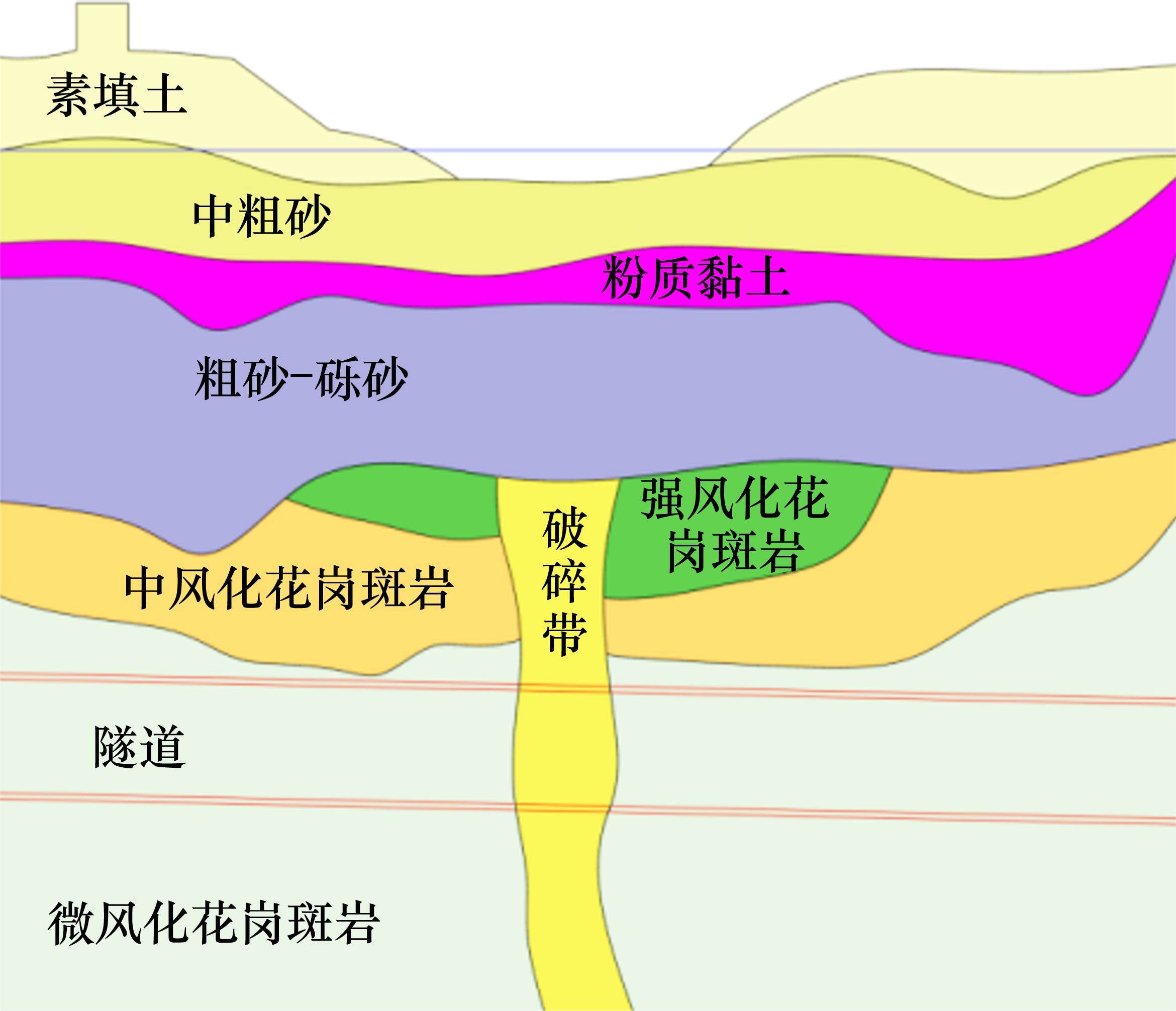
隧道上覆岩土主要分为素填土、中粗砂、粉质黏土、粗砂-砾砂、强风化花岗斑岩、中风化花岗斑岩及微风化花岗斑岩,隧道埋深约为22 m,洞身穿越微风化花岗斑岩层和破碎带。破碎带与水平面的夹角约为85°,宽度为6~10 m,李村河常年积水河水深度常年维持在0.5~1.5 m,地下水类型主要为第四系孔隙水和基岩裂隙水,主要赋存在第四系松散砂土层及基岩的裂隙中。其中,第四系孔隙水主要分布于中粗砂和粗砂-砾砂中,富水性强;基岩裂隙水主要分布于强风化花岗斑岩和破碎带中,并且第四系孔隙水和基岩裂隙水之间存在较为稳定的水力联系。断层破碎带围岩松散破碎、导水性较大、稳定性差,TBM掘进期间易发生塌方、涌水过大等问题。
2 三维数值仿真模型构建
城市轨道交通隧道中护盾式TBM施工一旦出现卡机事故,脱困措施少、处理难度大,因此,在工程实际中需要提前做好穿越断层区域预案,避免卡机事故。为了保障护盾式TBM顺利下穿李村河及断层破碎带,在TBM穿越该区域前,通过数值模拟分析法确定断层区域预先加固范围及方案。
2.1 模型建立
本文选用FLAC3D6.0有限差分数值分析软件对围岩稳定性进行数值分析,通过其内置的building blocks进行模型的构建。根据圣维南原理,隧道开挖仅对3~5倍洞径范围内的围岩产生影响,三维仿真模型的整体尺寸为:66.6 m(X)×60 m(Y)×46 m(Z),其地层及网格划分如图2所示。
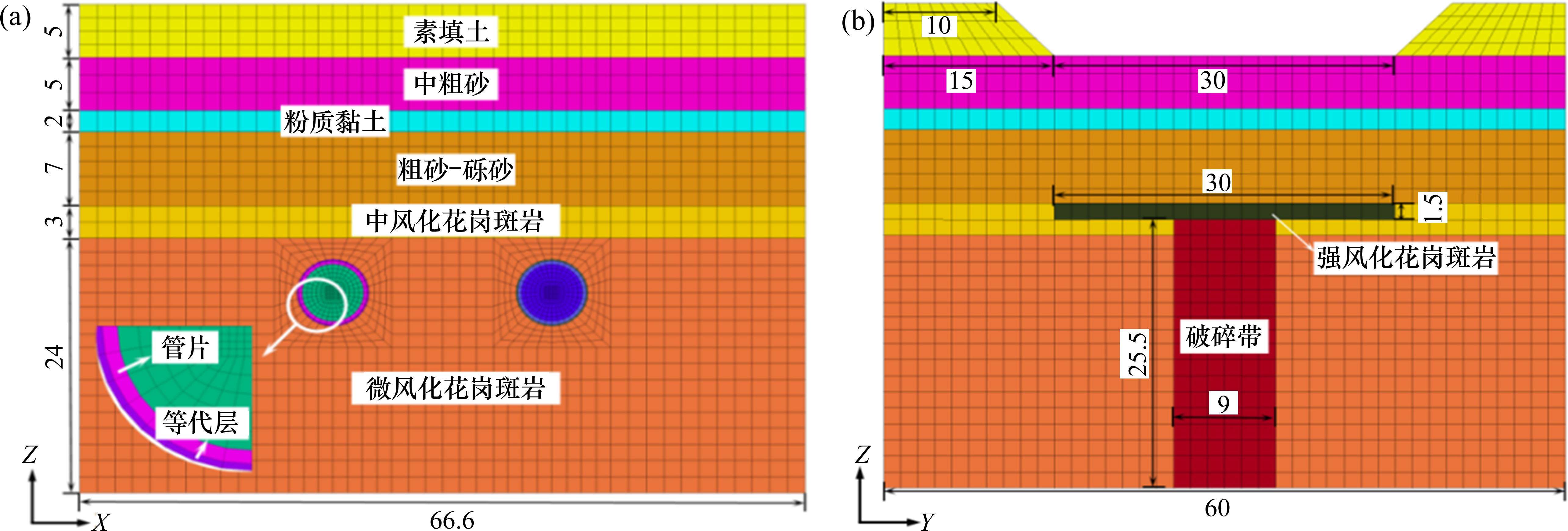
2.2 TBM施工数值模拟实现
由于双护盾TBM掘进过程中,开挖完成且管片支护前TBM护盾暂时起到支护作用,在断层破碎带区段护盾的支护作用影响更加明显。因此,为了使数值模拟过程更好地贴合双护盾TBM开挖隧道工程实际,本文建立了不同的柱体单元以及柱形壳体单元来模拟双护盾TBM刀盘以及前后盾壳对隧道开挖的影响,并在开挖完成后模拟管片支护以及壁后吹填豆砾石并注浆的过程,双护盾TBM设备前后盾的盾壳厚度取60 mm,管片厚度取300 mm。模拟中每循环进尺为1.5 m。具体开挖步骤如下。
1) 将整个模型设为摩尔-库伦本构,地应力平衡后,将位移、塑性区清零;
2) 在掌子面处设置法向推力,以模拟掘进过程中双护盾TBM推力;
3) TBM向前开挖一环,挖去隧道、管片、注浆层单元,TBM刀盘、前后护盾向前推进一环,以模拟TBM前、后护盾对围岩的支撑作用;
4) 在盾尾环处设置管片衬砌单元,赋予管片参数;
5) 重复第3~4步,对等代层赋予鼓吹豆砾石注浆加固硬化后的材料参数;
6) 按照上述循环开挖,直至隧道贯通。
2.3 模拟参数选取
各土体、岩体单元采用摩尔-库伦本构模型,根据现场岩土工程勘察报告,各岩土层物理力学参数如表1所示。本模型将TBM刀盘、前后护盾视为刚体材料,其他各单元材料采用弹性模型,考虑TBM自身重力对围岩变形的影响,将TBM护盾及配套设施重力等效为护盾重力;管片单元材料等效设置为C50混凝土,考虑螺栓连接对管片刚度的整体削弱作用,对单管片刚度乘以相应的折减系数;简化豆砾石吹填及注浆过程,其单元参数采取豆砾石吹填完成并注浆凝固后参数[15-18],其模拟参数如表1所示。
地层名称 | 弹性模量/MPa | 泊松比 | 密度/ (kg∙m-3) | 黏聚力/MPa | 内摩擦 角/(°) | 渗透系数/ (m2∙Pa-1∙s-1) | 孔隙率 | 抗拉强度/MPa |
---|---|---|---|---|---|---|---|---|
素填土 | 9 | 0.35 | 1 800 | 0.1 | 20 | 4.13×10-8 | 0.39 | 0.27 |
中粗砂 | 35 | 0.25 | 2 030 | 0.02 | 30 | 2.60×10-8 | 0.30 | 0.03 |
粉质黏土 | 15 | 0.32 | 1 990 | 0.15 | 25 | 1.15×10-11 | 0.32 | 0.11 |
粗砂-砾砂 | 38 | 0.28 | 1 990 | 0.03 | 21 | 3.2×10-8 | 0.36 | 0.08 |
强风化花岗斑岩 | 111 | 0.26 | 2 300 | 1.56 | 32 | 9×10-9 | 0.10 | 2.49 |
中风化花岗斑岩 | 5 100 | 0.25 | 2 620 | 6.69 | 38 | 2.0×10-10 | 0.05 | 8.56 |
微风化花岗斑岩 | 10 000 | 0.22 | 2 670 | 7.70 | 45 | 1.7×10-10 | 0.03 | 7.70 |
破碎带 | 100 | 0.30 | 2 200 | 0.54 | 10 | 1×10-8 | 0.20 | 3.06 |
管片 | 32.6 | 0.20 | 3 250 | — | — | — | — | |
TBM前后护盾 | 200 | 0.30 | 95 400 | — | — | — | — | |
充填注浆单元 | 0.35 | 0.25 | 2 500 | — | — | — | — |
3 双护盾TBM穿越断层数值模拟分析
纵向异质软弱地层对于围岩变形的影响不仅存在于软弱地层范围内,其同样会对周围一定范围的岩体产生影响。布置拱顶、左帮、右帮、底板4个数值分析监测点对TBM施工过程中的围岩变形进行分析。
3.1 TBM穿越破碎带围岩变形分析
为重点分析TBM穿越破碎带时的围岩变形情况,将TBM穿越破碎带的过程分为5个工况进行分析。工况1:TBM位于破碎带远端距离破碎带左边界4.5 m位置处;工况2:TBM位于破碎带左边界处;工况3:TBM位于破碎带中间位置处;工况4:TBM位于破碎带右边界处;工况5:TBM位于破碎带远端距离破碎带右边界4.5 m位置处。
右线隧道竖向变形云图如图3所示。工况1的情况下,隧道最大的拱顶变形位于距离掌子面后方,约为4.18 mm;工况2时,最大竖向变形位于掌子面上变形值约为2.38 cm;工况3、4和5的情况下,破碎带处出现了最大竖向变形,掌子面在接近破碎带时,整个破碎带就已产生较大的变形且方向向下,证明开挖扰动会使得破碎带向下滑移,因此使得底板处隆起很小。随着TBM持续掘进,拱顶围岩变形逐渐增大,在工况3情况下,掌子面正处于破碎带中间位置,此时的变形约为1.22 cm。
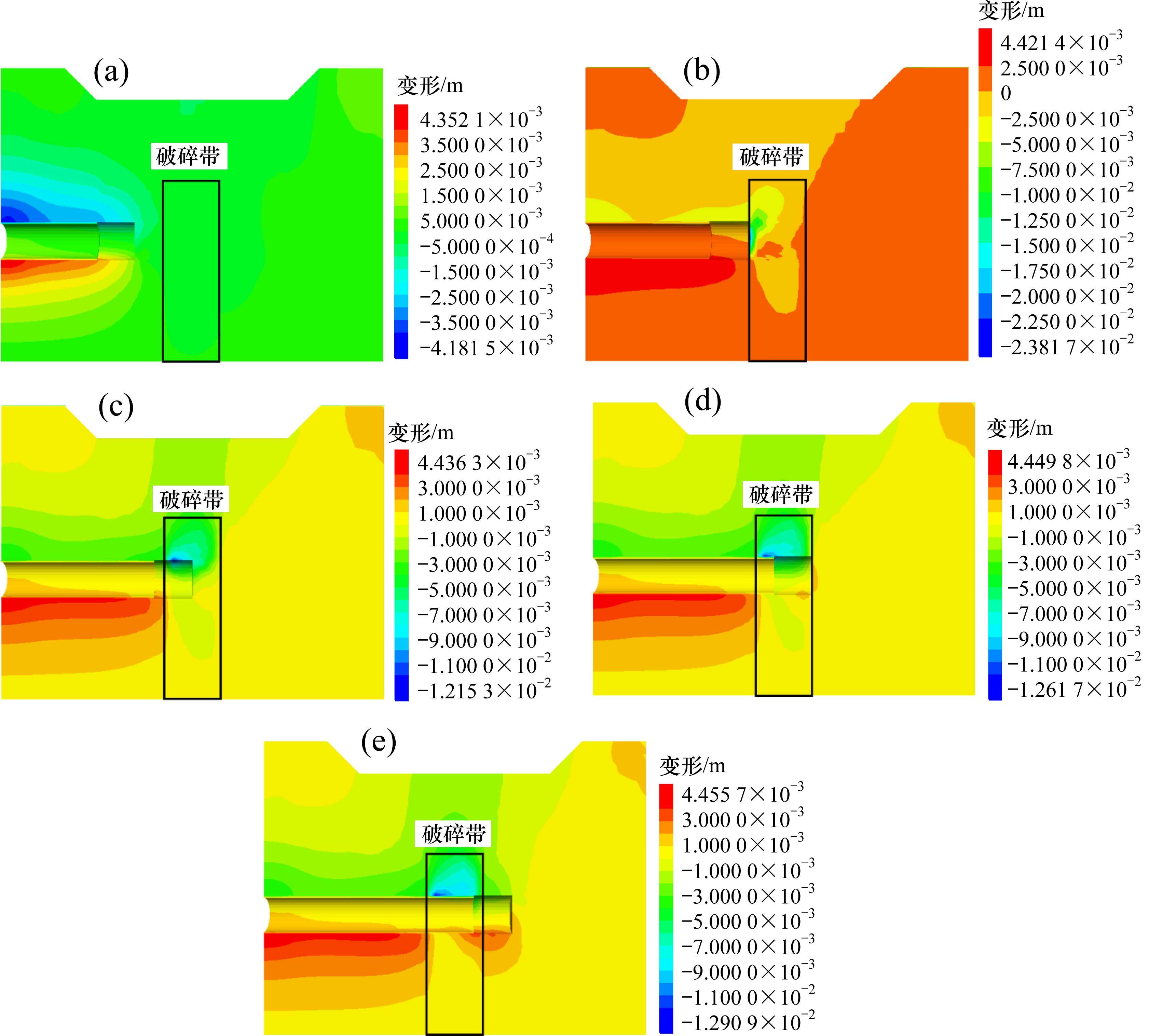
不同工况下右线隧道拱顶处的围岩变形如图4所示。在工况1的情况下,开挖扰动会对前方破碎带产生一定的变形;在工况2的情况下,破碎带变形急剧上升最大变形已经达到1 cm以上;工况3时,当TBM过破碎带中间后,会在破碎带中间产生最大变形,并且随着掌子面的持续推进变形量逐渐增大;工况4时,破碎带最大变形就已很大,此时变形增加缓慢;工况5时,破碎带已达最大变形值,证明掌子面过Y=39 m时,隧道开挖不会使破碎带处的变形增大,此时破碎带处的变形已经稳定。
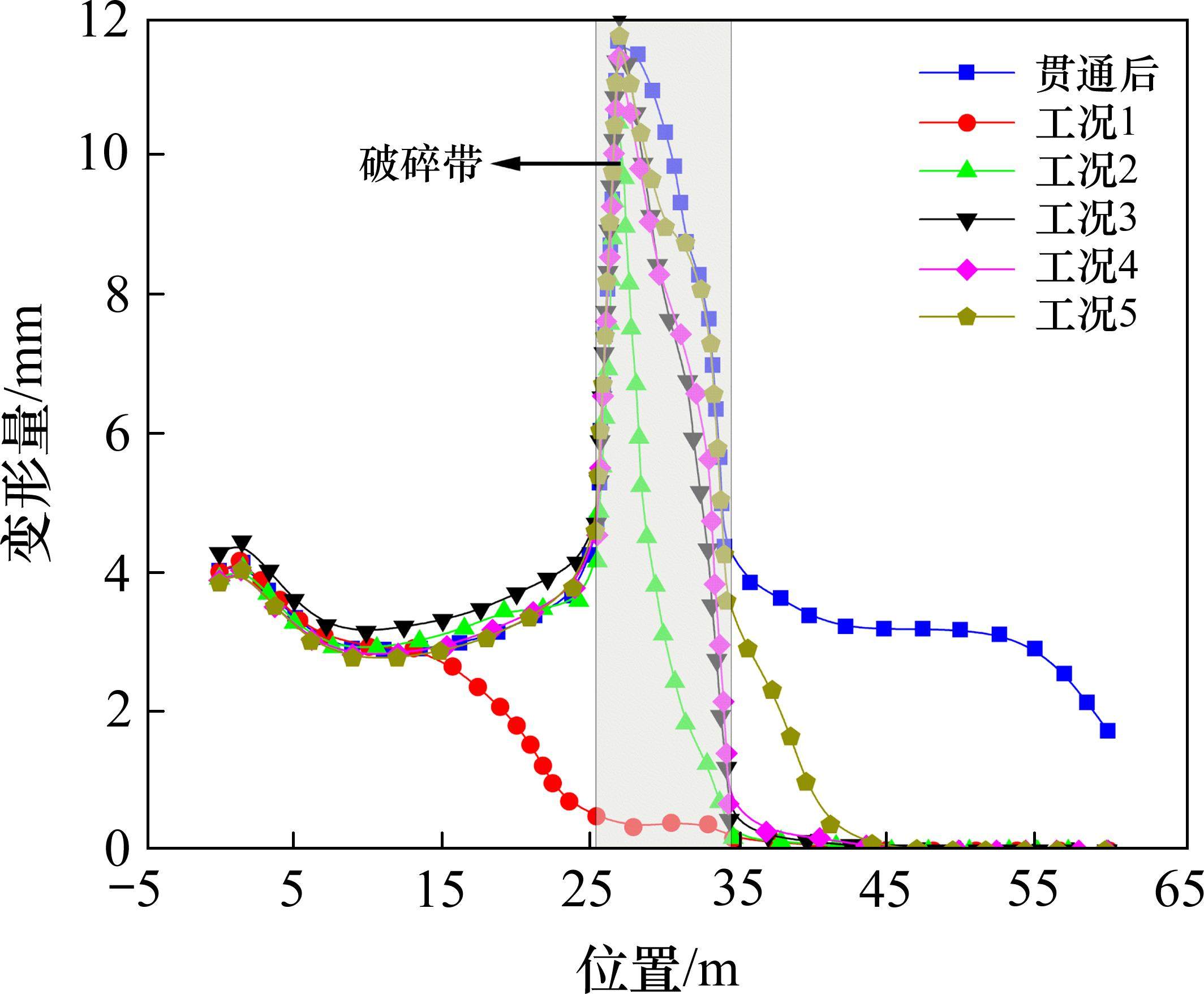
3.2 不同工况下围岩渗流场
右线隧道岩体孔隙水压力云图如图5所示。隧道开挖引起地下水大范围运移,并在破碎带两侧形成高水压区,随着掌子面的不断推进,破碎带左侧高水压区的水压逐渐降低并逐渐消散。右侧高水压区的孔隙水压力也将会随着掌子面的推进不断消散。当掌子面位于破碎带之外时,开挖扰动就使得破碎带以外区域的地下水向破碎带内迁移。此外,TBM掘进过程中掌子面前方形成低压区,地下水会向掌子面产生运移甚至渗透,对比工况2、3和5,可见,TBM在穿越破碎带的过程中,由于破碎带处的渗透系数更大,引起地下水的运移范围更大,极易造成掌子面突涌水,对围岩稳定性产生极大影响。
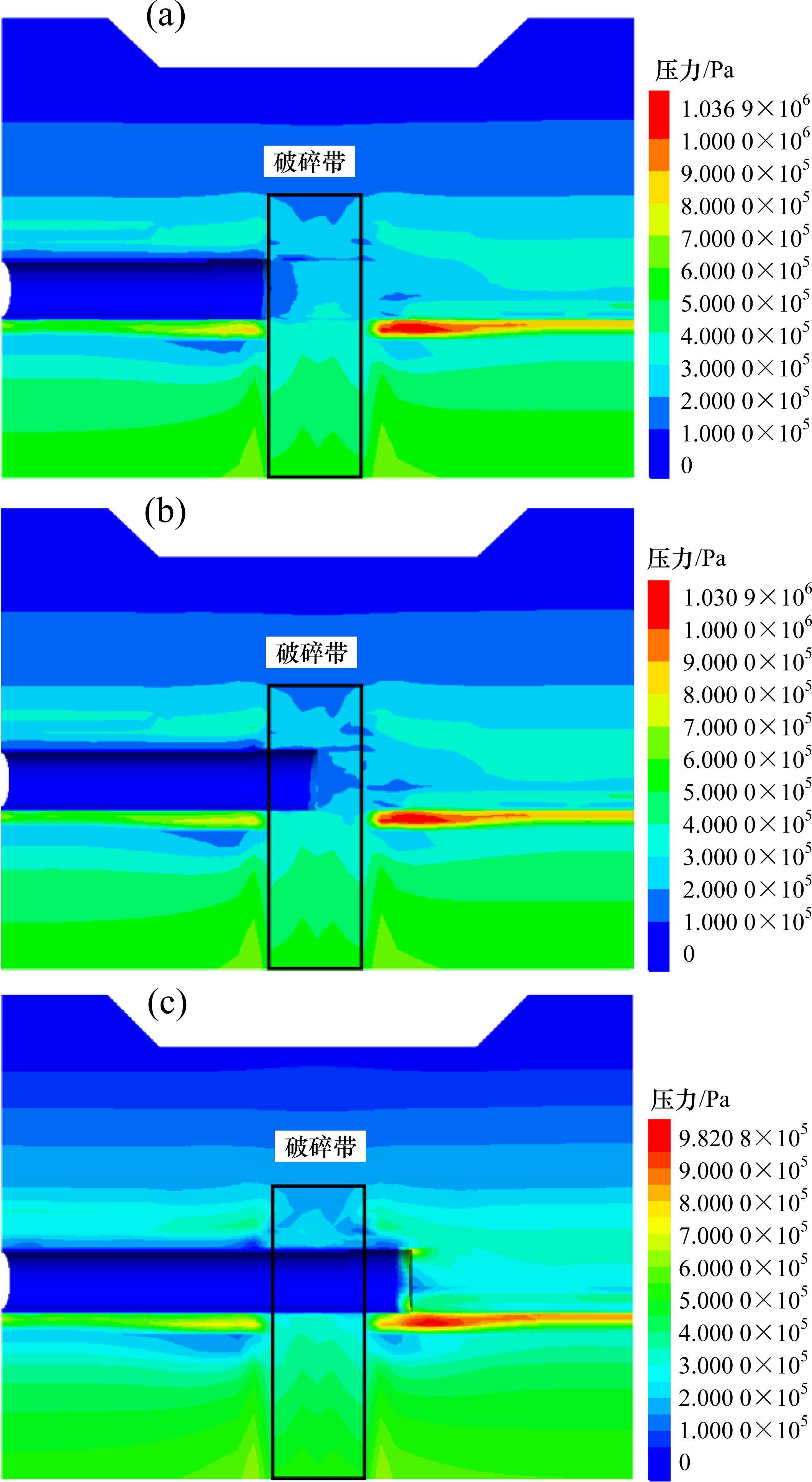
右线隧道拱顶处的孔隙水压力如图6所示。不同工况下的孔隙水压力曲线都在破碎带处产生孔隙水压力极值,不同于围岩应力曲线和变形曲线,其变化规律性较差,隧道未贯通之前的孔隙水压力曲线出现不同程度的波动,其并未按照贯通之后的曲线趋势发展,随着掌子面的不断推进,整体的孔隙水压力场产生剧烈扰动,证明开挖扰动对于孔隙水压力场的影响更为强烈。

4 注浆加固优化设计
4.1 注浆加固方案初步设计
目前来说,破碎带注浆加固主要分为掌子面超前注浆和地表深孔注浆两大类,其不同之处在于注浆孔分别打设于掌子面和地表。
针对该隧道,若采用掌子面超前注浆,TBM需停机并在刀盘前方预留工作空间,并且注浆完毕后,浆液需一段时间凝固进而TBM无法立即工作,不便于施工的同时又极大程度地影响了工期,因此采用掌子面超前注浆的方式并不是最佳选择。然而,采用地表深孔注浆的方式则可在TBM掘进之前完成注浆,届时浆液已完全凝固,破碎带处岩体的强度得到了提高并且形成止水屏障,极大程度地提高了施工安全且并未影响工期,因此采用地表深孔注浆的方式对破碎带进行加固。
根据补勘情况,施工单位初步提出了地表深孔隧道全断面注浆加固施工方案,对水平范围ZSK46+360~+379,ZSK46+518~+534,ZSK46+556~+572,YSK46+395~+413,YSK46+557~+573,YSK46+591~+606进行注浆加固。竖向加固范围以隧道底线下3 m开始向上12.3 m,注浆区域宽度为12 m,长度根据各个区间范围确定。
4.2 注浆加固方案模拟分析及优化
根据室内岩石力学试验,注浆区域物理力学参数的取值如表2所示。在前述数值模型破碎带隧道周围添加了2个注浆区域,选取L为8、10、12 m和河水深度0.5、1、1.5 m进行模拟。
弹性模量/MPa | 泊松比 | 密度/(kg∙m-3) | 黏聚力/MPa | 内摩擦角/(°) | 渗透系数/(m2∙Pa-1∙s-1) | 孔隙率 |
---|---|---|---|---|---|---|
1 000 | 0.25 | 2 500 | 2.02 | 24 | 1×10-9 | 0.15 |
4.2.1 围岩变形
以右线隧道为例,不同注浆范围和河水深度的围岩竖向变形云图如图7所示。相同注浆范围情况下,围岩变形云图形态基本一致,仅在围岩的变形的变形量上存在一定差异,相同的是围岩竖向变形随河水深度增大而减小,但减小幅度很小。以注浆范围L=8 m为例,hw=0.5 m时的围岩最大变形约为6.02 mm,hw=1 m时为6.04 mm,hw=1.5 m时为6.07 mm,河水深度对于围岩变形的影响在10-2 mm级,证明河水深度对注浆加固后的围岩竖向变形影响很小。相同河水深度情况下,围岩竖向变形随注浆范围增大而减小。以hw=1.5 m为例,注浆范围L=8 m时,围岩最大竖向变形约为6.07 mm,L=10 m时约为5.27 mm,L=12 m时约为5.01 mm,证明注浆加固大幅提高了破碎带处围岩的抗变形能力,且注浆加固对拱顶围岩变形影响较大,对底板变形影响较小。施工过程中,可以忽略河水深度对注浆加固后围岩变形的影响。
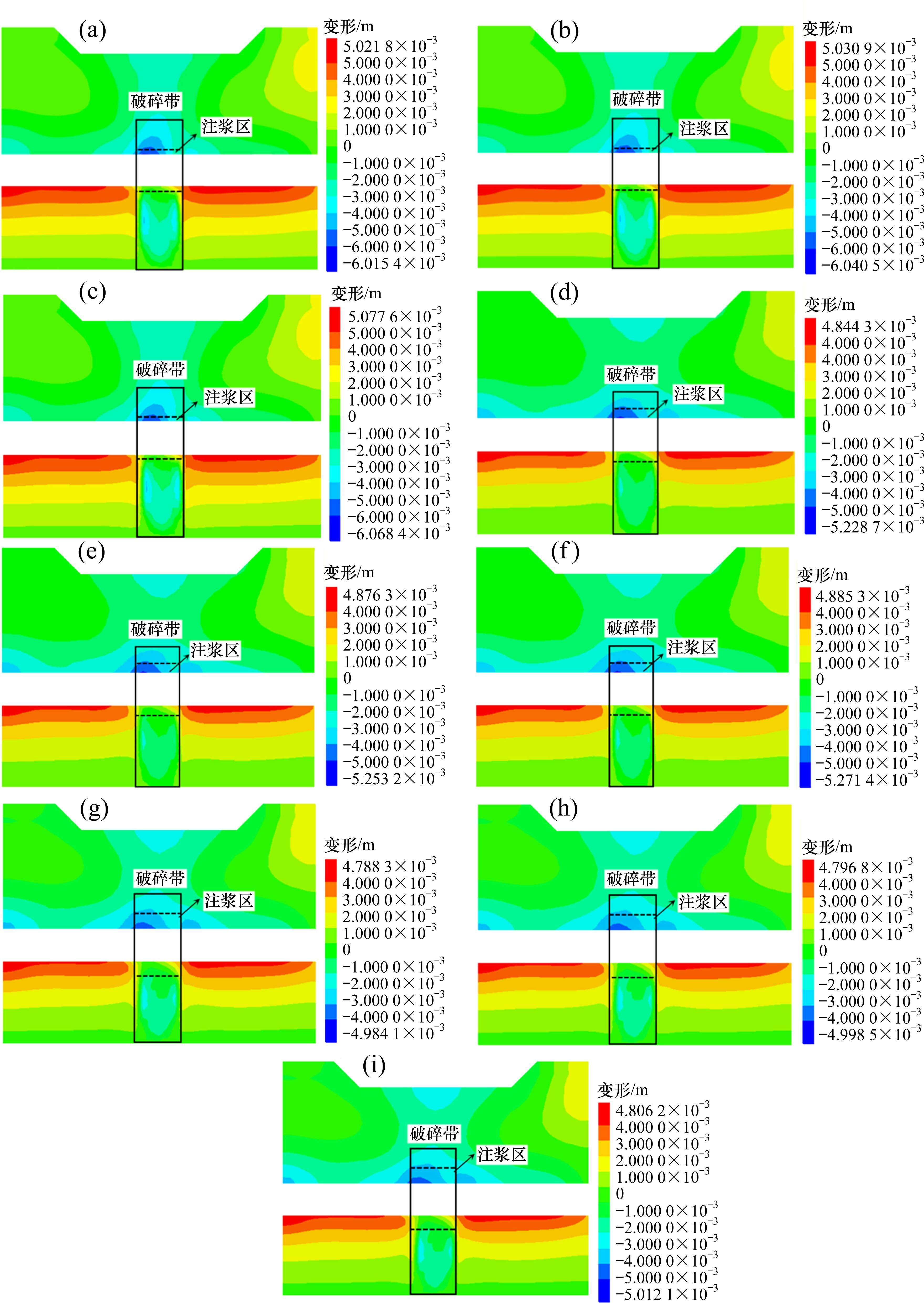
hw=1.5 m时,不同注浆范围情况下右线隧道拱顶竖向变形曲线如图8所示。整体而言,注浆加固后的拱顶竖向变形要远远小于不注浆的情况,注浆加固作用不仅仅使得破碎带处的变形减小,同样使得破碎带以外的未注浆区域的拱顶变形减小,说明注浆加固不仅能提高被注浆处的岩体抗变形能力,同时能提高岩体的整体性和协同变形能力。
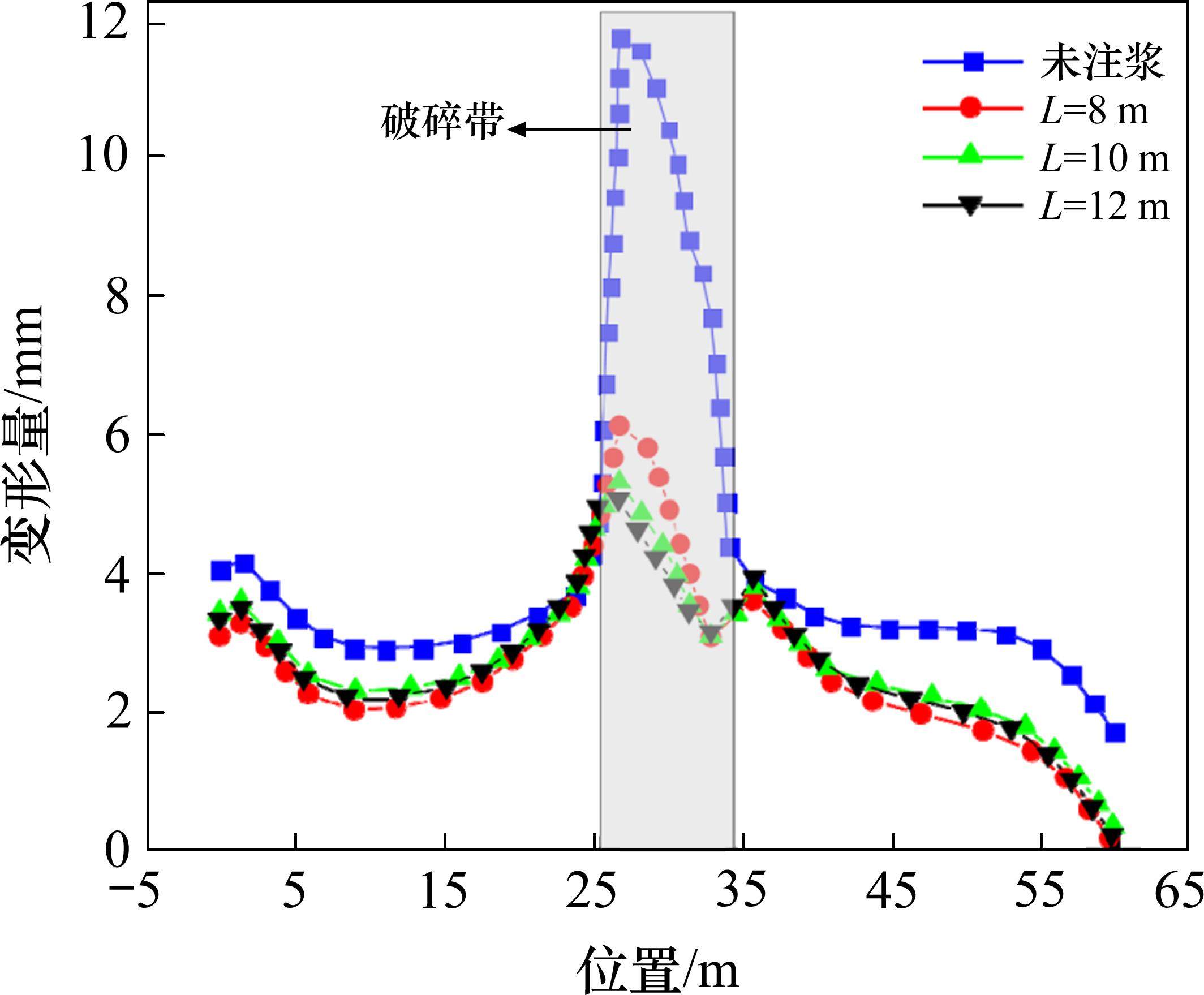
hw=1.5 m时,不同注浆范围的围岩最大拱顶变形值如表3所示。对比不注浆时的围岩最大拱顶变形,注浆范围L=8 m时,减少了约47.59%,注浆范围L=10 m时,减少了约54.57%,注浆范围L=12 m时,减少了约56.81%。可以发现,注浆区域继续增大,拱顶最大变形减小的幅度越大,注浆效果越好。
注浆范围 | 围岩最大变形/mm |
---|---|
不注浆 | 11.60 |
L=8 m | 6.07 |
L=10 m | 5.27 |
L=12 m | 5.01 |
4.2.2 注浆范围优化设计
通过对注浆范围L=8、10和12 m进行模拟,注浆范围越大,破碎带处最大围岩变形越小,塑性区范围越小,但盲目增大注浆范围会造成成本的增加,且对围岩稳定性的提高作用有限,因此选取一个合适的注浆范围至关重要。以最大围岩变形为控制因素来优选注浆加固的范围,由于隧道开挖直径为6.3 m,注浆范围中L须大于6.3 m,注浆加固才能有效果,因此引入一个新的变量d对注浆范围进行更精确的描述,d为隧道开挖边界距注浆区域边界最近的距离。令围岩最大变形为dmax,不同d情况下的围岩最大变形如表4所示。
注浆范围 | d/m | dmax/mm |
---|---|---|
不注浆 | 0 | 11.60 |
L=8 m | 0.85 | 6.08 |
L=10 m | 1.85 | 5.27 |
L=12 m | 2.85 | 5.01 |
dmax和d的指数函数关系相关度可达99%,因此可认为dmax和d呈现指数函数的关系。随着注浆范围的不断增大,围岩最大变形逐渐减小,但注浆范围的增大对于围岩变形控制的增长率越来越低,即单位注浆所降低的围岩变形减小,拟合函数进行求导可得:

以d=2 m为界,可将注浆加固范围划分成2个部分,d<2 m为注浆对变形影响较大的区域,d≥2 m为注浆对变形影响较小的区域。因此,可以认为当d=2 m时的注浆范围为最优的注浆范围,此时L=10.3 m,因此工程应用中选取L=10.3 m对破碎带进行注浆。
4.2.3 注浆加固实施
根据前文分析,现场具体加固方案及要求如下:
1) 注浆孔地表打设间距为1.2 m×1.2 m,梅花型布置,注浆孔孔底的间距为2.625 m×2.625 m。注浆孔排布方式如图9所示。
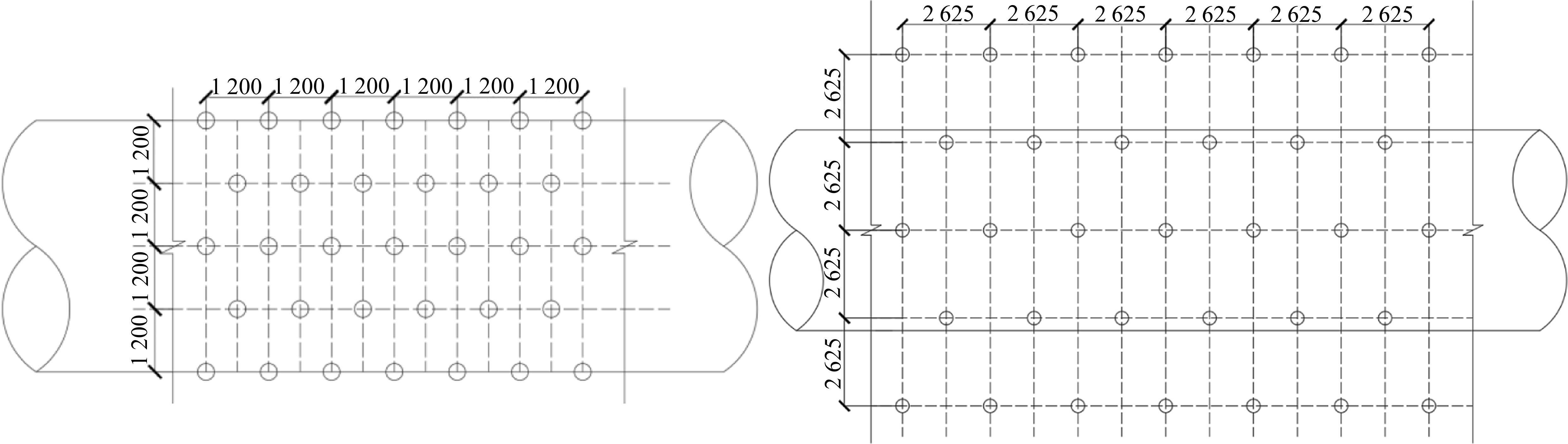
2) 浆液采用水泥-水玻璃双液浆,水灰比1∶1,注浆压力为1.5 MPa,实际注浆压力根据注浆效果和注浆试验调整。
3) 注浆效果探查。采用微动探测技术进行注浆效果探查,结果出现明显异常高速区(图中标记为A3、A4),如图10所示,此区域为注浆加固范围,注浆加固效果良好。
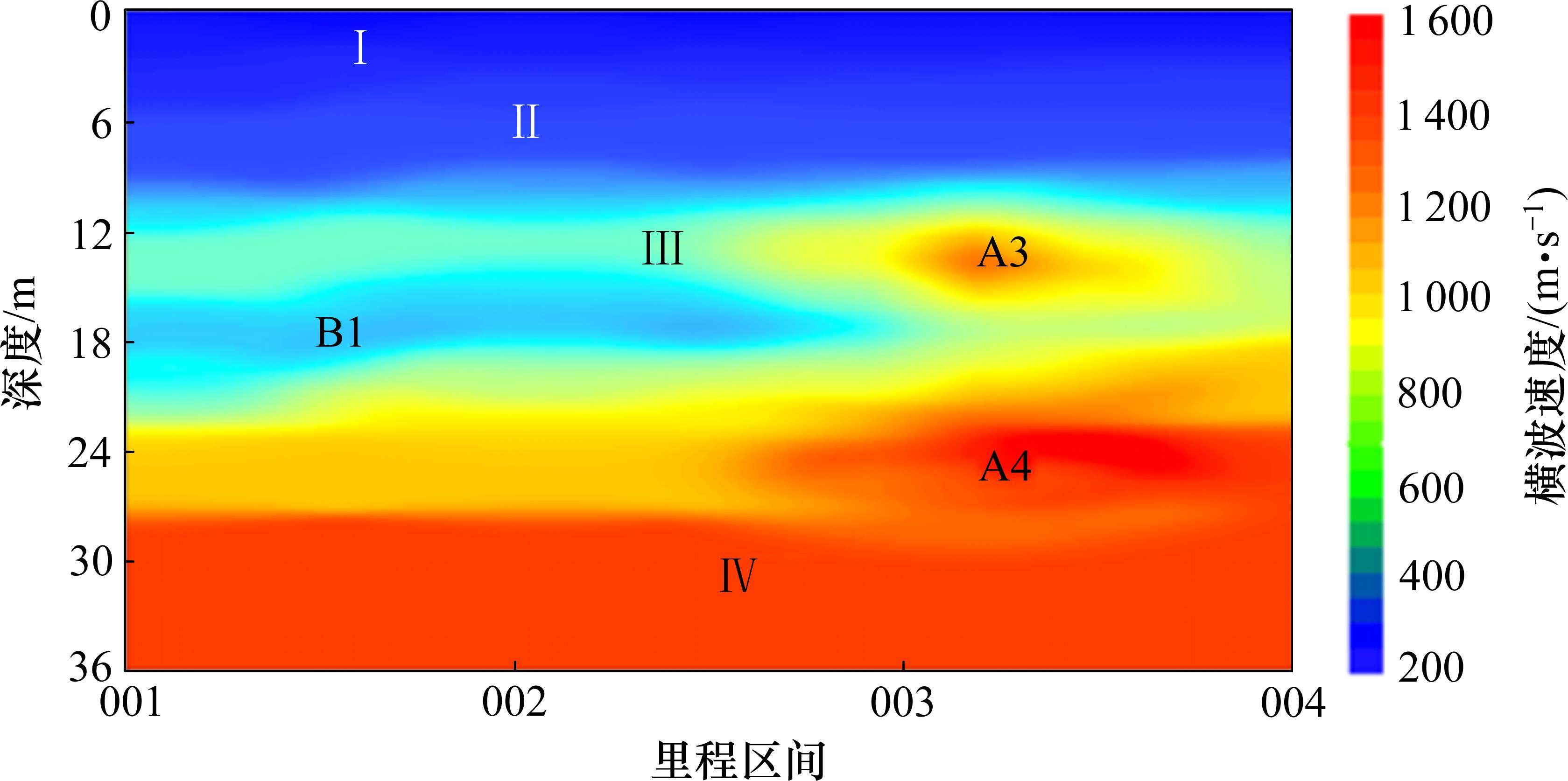
5 双护盾TBM穿越河流破碎带的掘进参数
5.1 掘进参数统计分析
TBM穿越破碎带时,若控制参数匹配不合理极易导致刀盘卡死[18-19],因此双护盾TBM穿越断层破碎带区域时,通过分析选择合理的掘进参数可以减弱开挖对围岩的扰动,有效避免施工事故。为合理确定TBM施工参数,通过盾构施工监控系统采集穿越断层前段50环的掘进参数,所采集的参数包括推力、扭矩、转速和推进速度[20]。
图11为双护盾TBM穿越断层区域的系统推力采集统计图。断层区域的TBM推力主要分布在4 000~6 000 kN,均值为5 200 kN,波动较小,确保不对岩体造成过大的扰动。
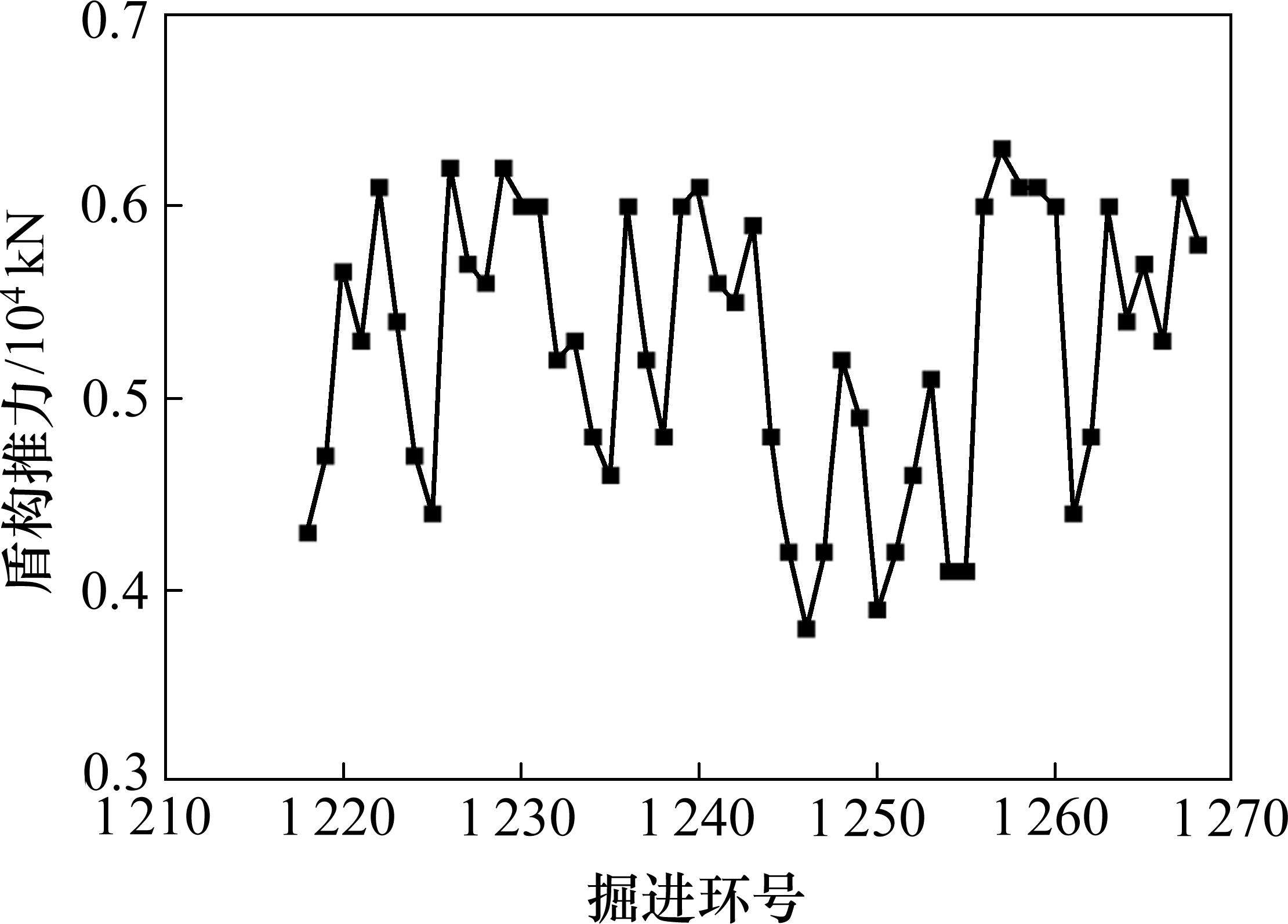
图12为断层区域刀盘转速和扭矩的统计图。盾构开始掘进时,刀盘转速较低,随着掘进环号的增加,刀盘转速渐趋稳定,主要控制在7.37 r/min左右,且波动较小,即进入断层后,双护盾TBM通过降低刀盘转速来减少对掌子面岩体的扰动。断层内刀盘扭矩波动较大,主要分布在400~800 kN∙m之间,均值为566 kN∙m,施工中应重点关注刀盘扭矩变化,防止塌落体卡死刀盘。
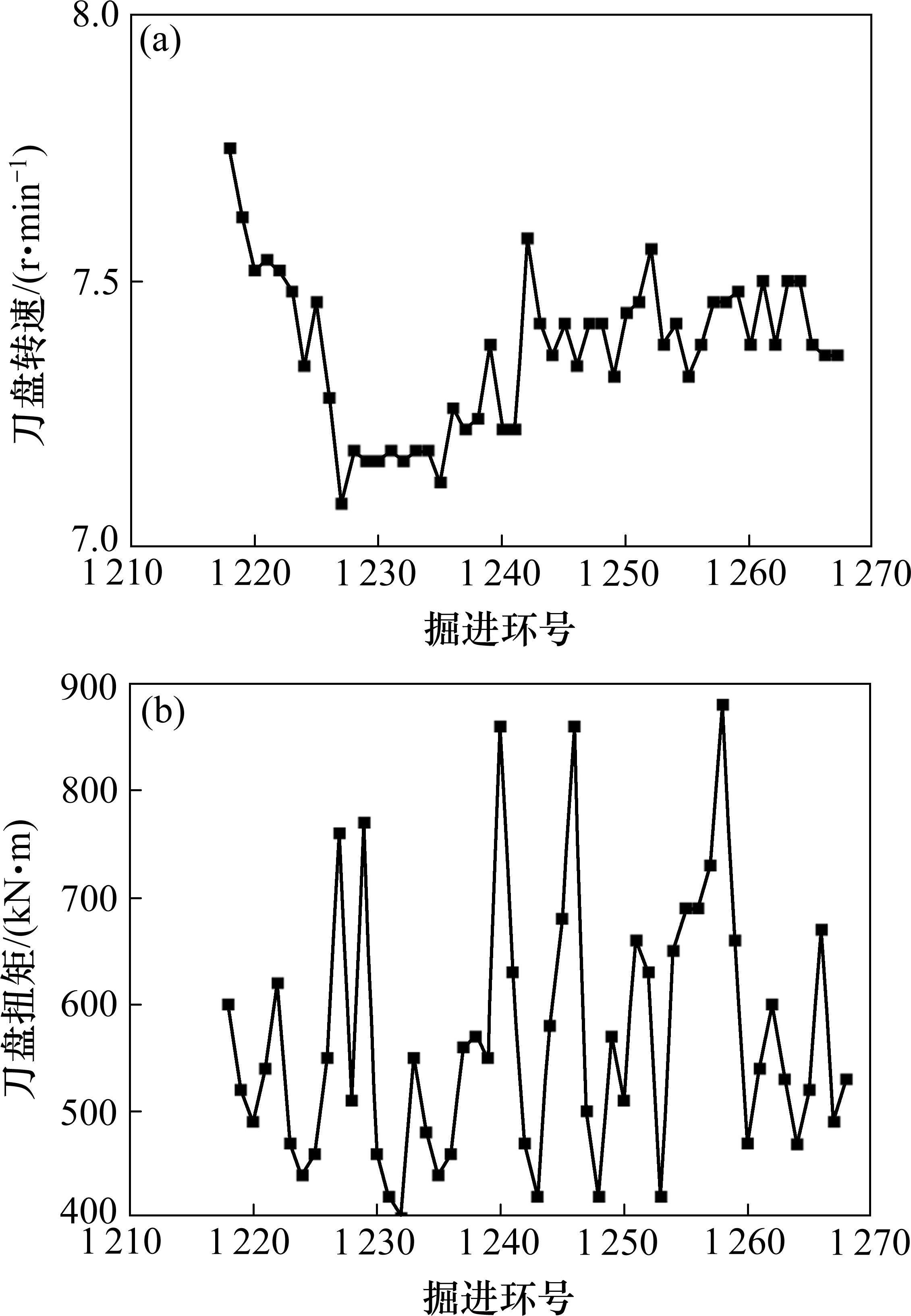
图13为双护盾TBM穿越断层区域的推进速度采集统计图。在该掘进区段,掘进速度主要控制在30~40 mm/min之间,平均值为34.8 mm/min,整体上变化较为平稳,保持匀速推进,确保隧道及时成型,防止冒顶涌水、地下水流失造成的地层失稳等风险出现。
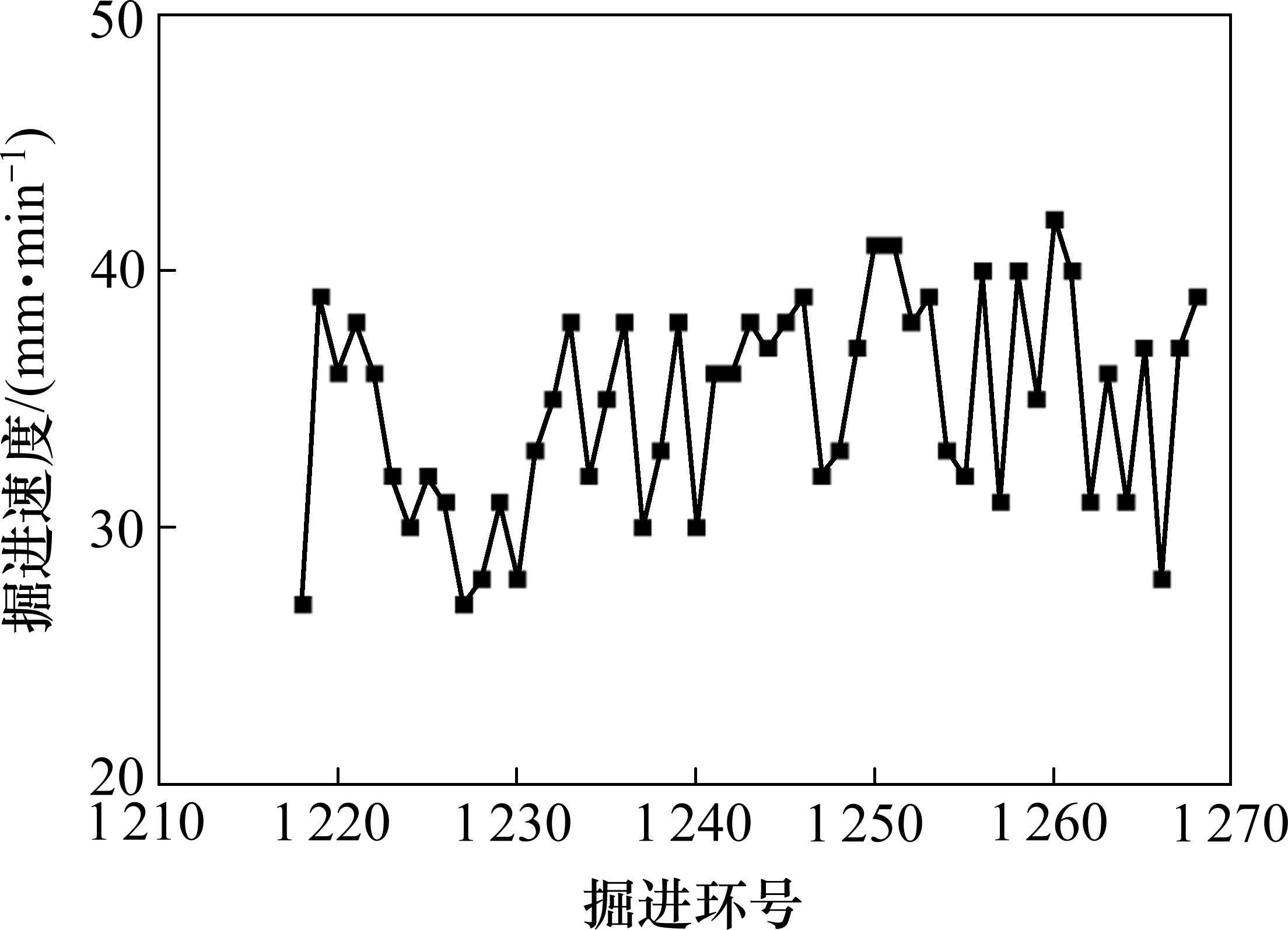
5.2 监控量测与掘进控制参数
为验证注浆加固效果及优化设计TBM控制参数,在加固区外侧河道布设地表沉降监测点,纵向测点按5 m的间距布置。通过现场监测,左右两线隧道地表沉降监测值如图14所示。左右两线隧道都在20~40 m处(河流破碎带)出现了最大沉降值,左右两线隧道沉降值变化趋势大致相当且最大沉降值为3.75 mm,都远小于沉降控制标准值30 mm,满足施工安全的控制要求。
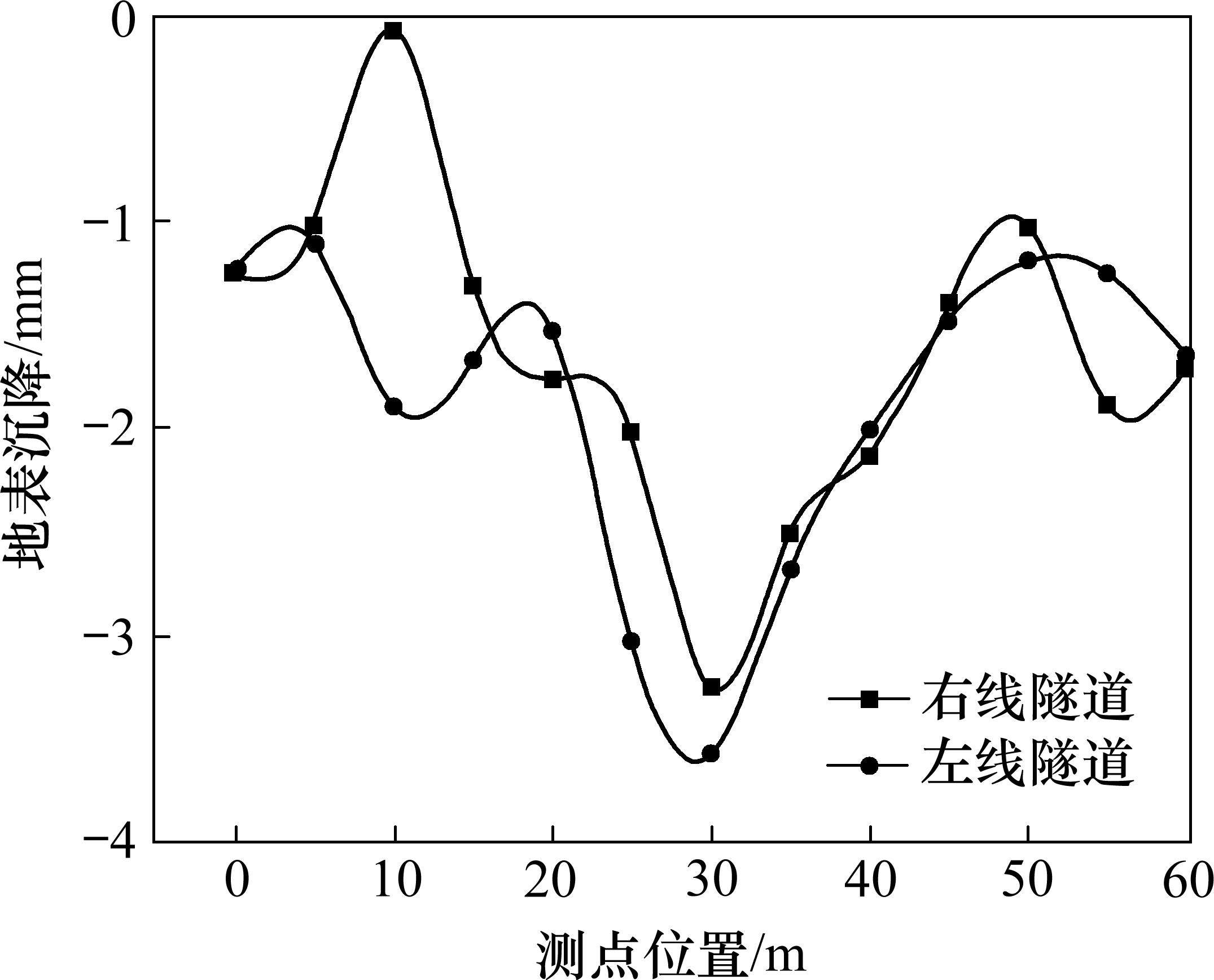
而对于拱顶沉降,布置如图15所示的3个测点。监测点实测位移时程曲线如图16所示。围岩变形整体上呈现缓慢增加—最终稳定的趋势,但会出现小幅度的波动,稳定变形后测点1处变形最大,最大值约2.80 mm,测点2和3处变形大小相当,但均远远小于控制值,表明注浆加固与TBM施工参数控制较好。
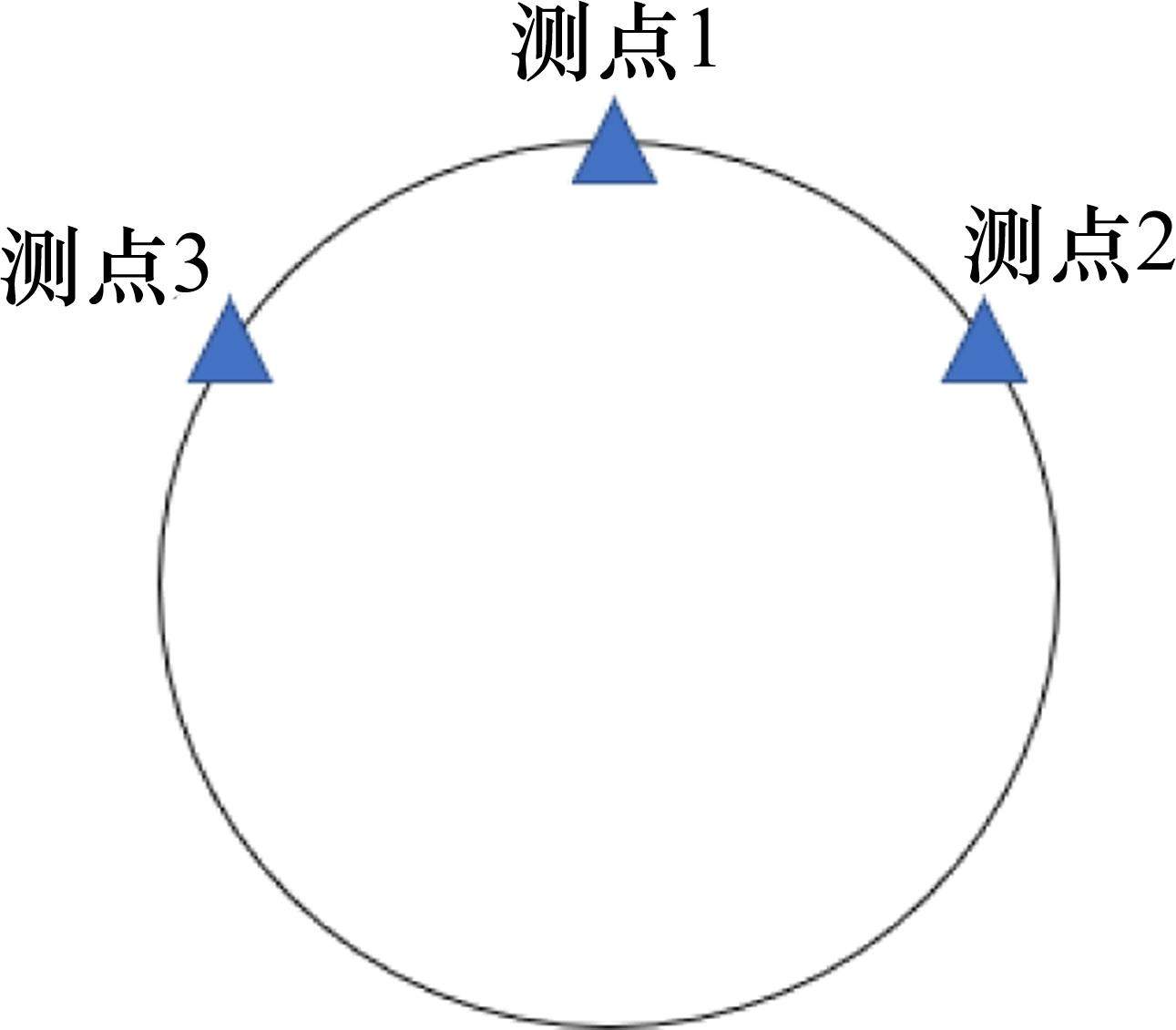
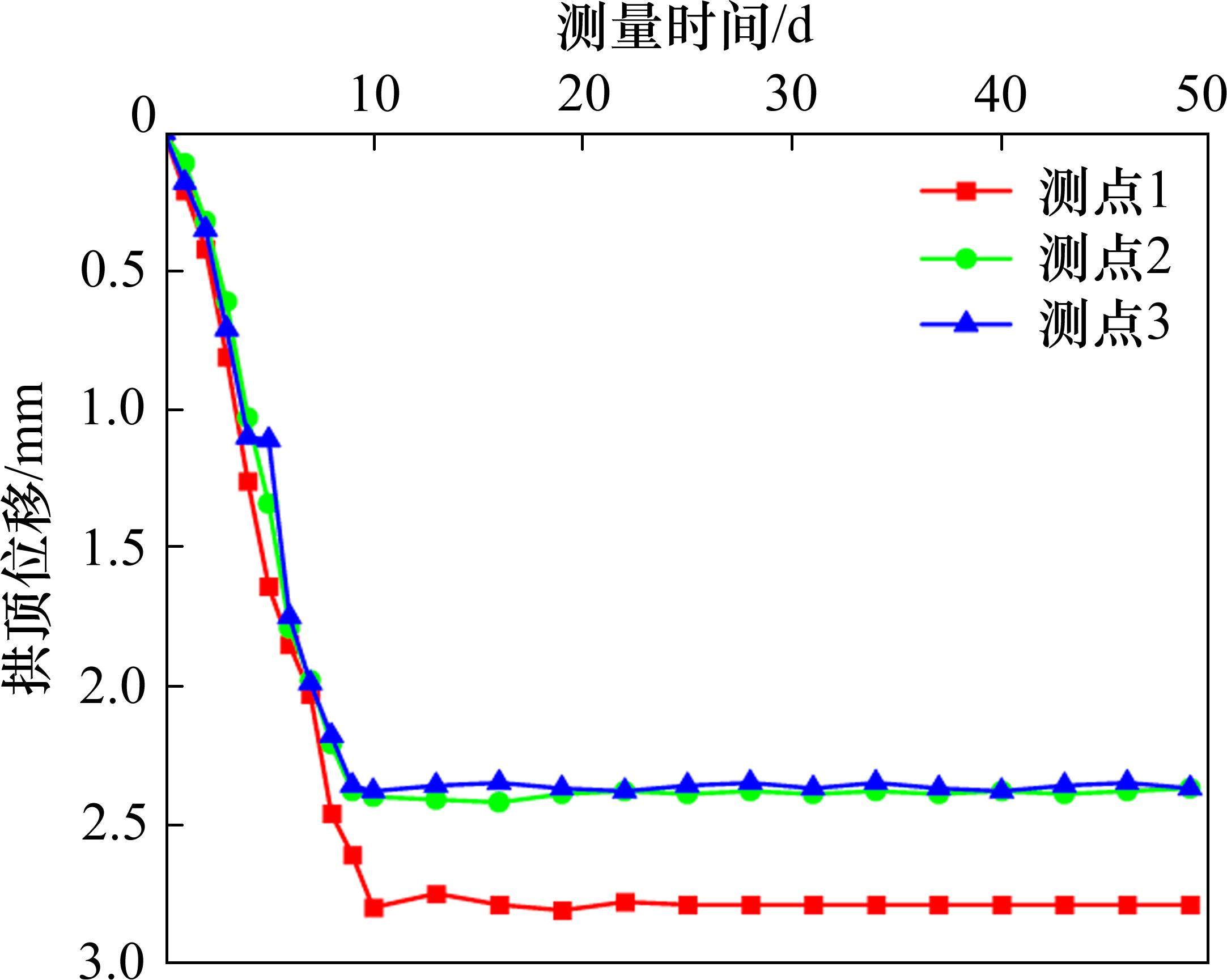
通过对下穿李村河流破碎带区间双护盾TBM掘进参数的统计分析,确定此段TBM掘进参数设置如下:推力控制在4 000~6 000 kN,刀盘扭矩控制在500~800 kN∙m,刀盘转速控制在6~8 r/min,推进速度控制在30~40 mm/min。其中,最优掘进参数为推力5 200 kN、扭矩566 kN∙m、刀盘转速7.37 r/min、推进速度34.8 mm/min。
6 结论与建议
1) 双护盾TBM在穿越河流破碎带施工前,应对勘察孔进行加密处理,以便进一步明确破碎带位置,减少TBM停机时间。TBM选型应确保地层适应性,配备超前地质预报设备,结合地质勘探、地质素描,提前进行地质预测预报,防患于未然。
2) 双护盾TBM穿越河流下断层破碎带施工时,应通过数值模拟分析优化设计注浆加固方案,并确定合理的注浆参数对断层破碎带进行超前加固,河流破碎带下注浆一般选用水泥-水玻璃双液浆,注浆压力为1.5 MPa,水泥浆水灰比为1∶1。
3) 双护盾TBM穿越河流破碎带施工前主要采用地表深孔隧道全断面注浆对破碎带进行加固处理,注浆加固范围由隧道直径和隧道开挖边界距注浆区域边界最近的距离综合确定。
4) 双护盾TBM穿越河流破碎带施工时,应适当调整TBM姿态及施工参数,合理设置TBM千斤顶总推力与扭矩、转速,以及协调控制总推力与掘进速度,施工中应适当提高推进速度、降低刀盘转速,稳定推力和扭矩,确保TBM下穿施工时保持匀速、连续通过不停机。
李志军,王明年,于丽等.护盾式TBM施工下穿河流破碎带稳定性分析及变形控制技术[J].铁道科学与工程学报,2024,21(11):4612-4623.
LI Zhijun,WANG Mingnian,YU Li,et al.Deformation and settlement control technology of shield TBM tunnel construction under river fracture zone[J].Journal of Railway Science and Engineering,2024,21(11):4612-4623.