随着轻量化、精密化发展战略的持续推进,使用高性能材料替代部分基础材料已成为新的发展趋势[1-2]。钢作为一种重要的工业原料,制备工艺相对成熟,易于大规模生产和加工,并因其高强度和高韧性的特点,在建筑、桥梁、机械零件等领域具有重要作用[3]。然而,科技进步带动高精尖微电子产品和科研事业迅速发展,对材料性能的要求越来越高。钢虽然具备出色的力学性能,但其导电和导热性能相对较差,这在一定程度上限制了其广泛应用。
金属复合材料同时具备两种金属的优点,使其满足一些特定的工作环境要求[4]。铜及铜合金作为金属复合材料的重要组成部分,因其独特的物理化学性能受到国内外学者关注[5-6]。纯铜具有良好的导电性、导热性、延展性以及可回收利用等优点,这使得它在集成电路、半导体器件等电子元器件领域有着广泛应用[7]。铜与钢结合形成的层状复合材料,既保留了钢高强度、耐腐蚀的特性,又克服了其导电、导热性差的缺点,已广泛应用于电力行业、核工业、热交换器、汽车零部件、航空发动机等领域[8]。但是,由于铜和钢力学性能差异较大,在材料结合过程中通常伴随有钢侧变形抗力大、铜/钢变形不协调、界面结合强度低等问题[9-12]。为此,研究人员已开发出不同的制备工艺和技术,通过调整不同的工艺参数、研究元素扩散、引入中间层和外加能场等方法,可以有效降低变形抗力、改善变形协调性,进而提高铜/钢界面的结合性能。
本文对铜/钢复合板制备工艺和方法进行了全面的综述,探讨了各种制备方法的最新研究进展,并对它们的优缺点进行了细致的分析对比。从铜/钢复合板界面调控的角度出发,分析了不同处理方法对铜/钢复合界面微观形貌、组织结构及力学性能的影响,探讨了这些方法对界面结合强度的影响机理,为进一步优化铜/钢复合板结合性能提供了参考,从而推动铜/钢复合材料在更广泛、更复杂领域的应用和发展。
1 铜/钢复合板制备方法
目前,铜/钢双金属复合板的制备方法主要有爆炸焊接法[9]、扩散焊接法[10]、轧制复合法[11]、固-液复合法[12]以及搅拌摩擦焊接法等,不同方法制备的铜/钢双金属复合板界面生成相成分、组织形貌、复合机理及界面力学性能不尽相同。
1.1 爆炸焊接法
对于双金属复合板而言,爆炸焊接法可以将熔点、导热性、热膨胀系数等物理化学性能差异较大的金属结合在一起,如铜/铝[13]、铝/钢[14]、钛/钢[15]、铜/钢等。爆炸焊接法起源于1944年美国人CAEL的一次爆炸成形试验,十年后其才被推广到实际生产中[16]。我国采用爆炸焊接法制备双金属复合板的研究从20世纪60年代陆续开始,经过多年发展,我国已基本掌握了异种金属两层及多层复合材料的制备技术,并已实现产业化[17-18]。爆炸焊接法制备铜/钢复合板的原理是将铜金属覆材和钢基体整齐地叠放在一起,利用爆炸产生的巨大冲击力冲击铜覆材,使铜覆材和钢基体瞬间发生高速碰撞,铜覆材和钢基体表面的氧化膜被碰撞点产生的瞬间高压击碎,暴露出的新鲜金属相互接触,从而实现铜覆材和钢基体的结合,如图1所示[19]。
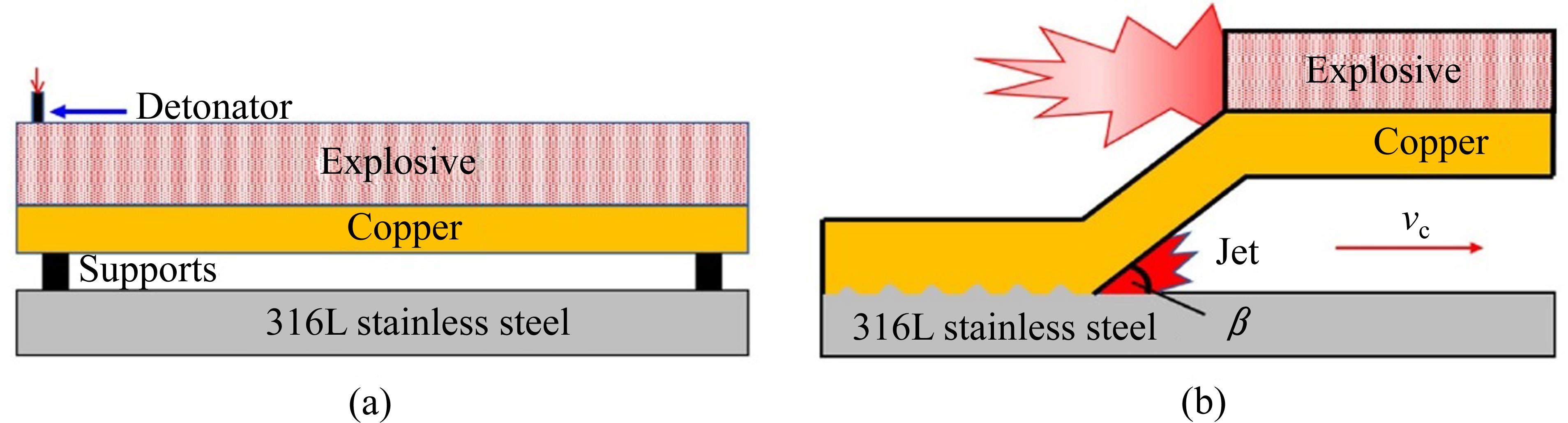
爆炸焊接过程中,覆板和基板的高速碰撞会产生较高的温度和压力,导致界面冶金反应和波纹状界面形成,并产生加工硬化现象[20]。ZHU等[4, 19]以T2铜为覆板,316L不锈钢为基板,采用硝酸铵燃料油(ANFO)混合物炸药制备出铜/不锈钢复合板。复合板的抗拉强度约为336.6 MPa,剪切强度约为183 MPa,复合界面呈现周期性波纹状形貌,且界面处产生了动态再结晶和晶粒细化现象,靠近界面两侧的铜和不锈钢硬度明显升高。为了消除高速碰撞导致的加工硬化现象,将制备得到的复合板在620 ℃温度下进行保温处理,随退火时间的延长,复合板强度降低,伸长率和塑性得到改善。退火20 h后,复合板抗拉强度下降到224.6 MPa,剪切强度下降到131 MPa。在后续的拉伸断裂试验中,铜侧率先发生断裂,表明复合板结合良好。山东理工大学的FENG等[21]用爆炸焊接法制备了铜/304不锈钢复合板,并在600 ℃温度下退火3 h,其复合界面产生波纹状结构,波长为1~2 mm,波高为400~600 μm。在界面处可以明显观察到两种典型层:一种是厚度为2~3 μm且元素呈阶梯分布的扩散层,如图2(a)所示;另一种厚度约为50 μm的融化层仅出现在304不锈钢一侧,如图2(b)所示;由于退火温度较低,不锈钢晶粒内部仍存在高密度位错,不锈钢侧和界面区域晶粒细小,而铜侧晶粒再结晶温度较低,发生晶粒粗化现象。姜超等[22]用爆炸焊接法制备出T2/06Cr19Ni10不锈钢复合板,界面结合强度达到280 MPa,界面附近组织的显微硬度明显升高。紫铜与不锈钢爆炸焊接后形成了规律的波状界面,波峰与波谷区域分别嵌入了不连续的漩涡状铸态组织,该组织主要由ε-Cu、γ-Fe及不锈钢微粒组成,如图3所示[22]。并且界面附近不锈钢组织中形成了绝热剪切带,奥氏体不锈钢发生了马氏体转变,紫铜组织中能够观察到退火和再结晶现象。
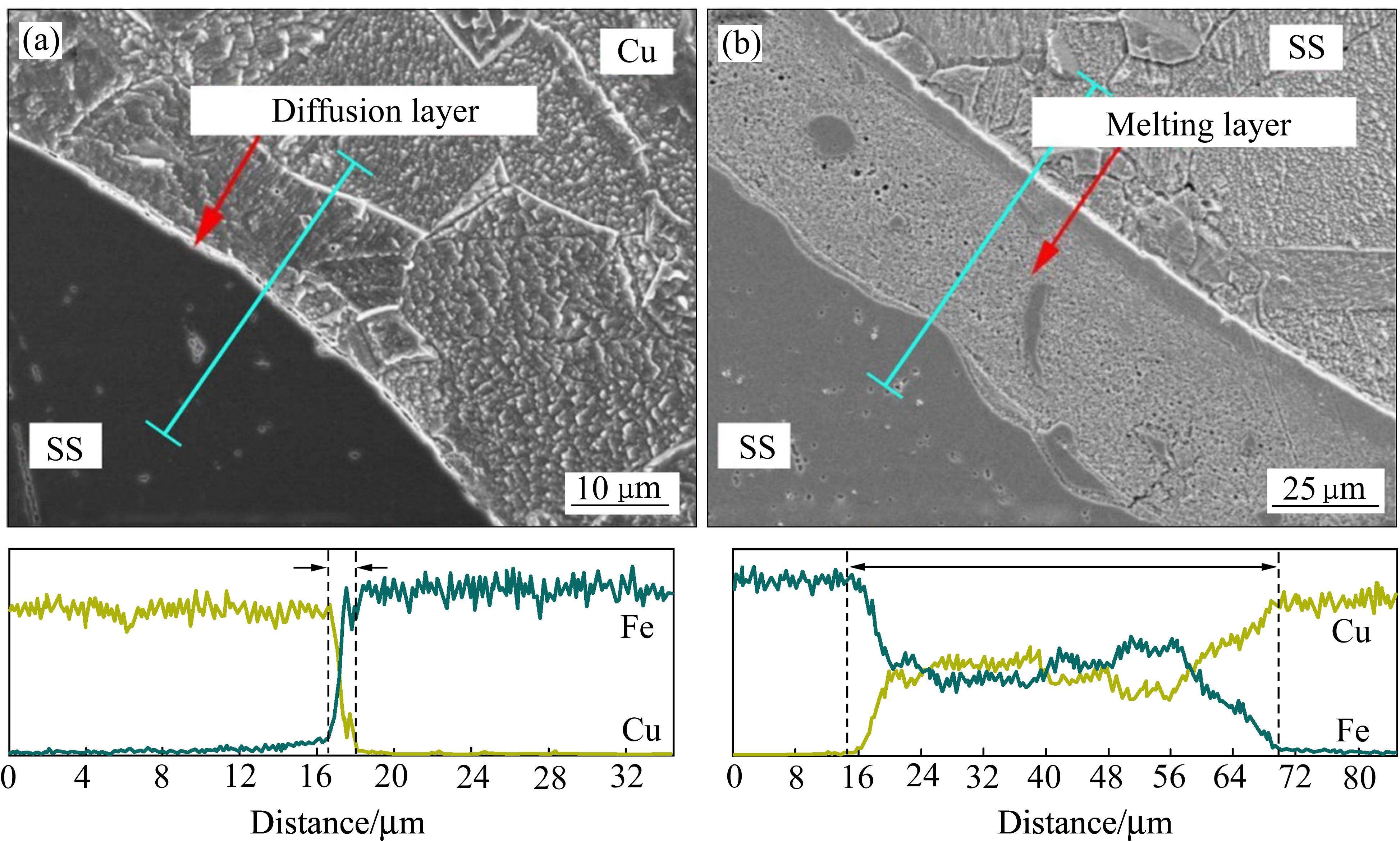

由于爆炸焊接过程短暂且难以控制,复合板结合质量直接取决于材料性能和工艺参数配置。CARVALHO等[23]从铜和不锈钢的物理特性角度分析了复合板的结合质量。研究发现,基板与覆板密度之比越大,界面处波纹的波长越大;当材料的导热系数相差较大且一种材料熔点较低时,制备得到的复合板结合质量极差。在ZLOBIN等[24]的研究中,基板与覆板厚度之比越大,界面处波纹的波长越小。KHANZADEH等[25]研究发现,随着基板与覆板间距增大,青铜/St37碳钢复合板的界面会变得更加起伏。经500 ℃退火16 h后,界面生成的金属间化合物层厚度由30 μm增加到65 μm,并且由于位错运动导致内应力的降低,界面硬度由HV180降低到HV86。此外,SARAVANAN等[26]通过大量实验研究了基板与覆板之间的角度和碰撞速度与铜/钢复合板界面类型的关系,绘制出铜/钢爆炸焊接窗口,通过选择合适的碰撞速度和碰撞角度,可以获得波纹状复合界面。
近些年,一些学者通过理论分析和数值计算的方法对双金属爆炸焊接的技术参数进行事先设计,成功缩短了试验周期和有效降低了试验成本。大连理工大学的王宇新等[27]利用特征线差分法对TU1铜/316L不锈钢爆炸焊接窗口、覆板飞行姿态进行计算,确定合理的技术工艺参数,制备出大厚度铜/不锈钢复合板,其满足核聚变用复合板的技术标准和质量要求。南京理工大学的YANG等[28]通过集成光滑粒子流体动力学(SPH)模拟、微观表征和理论分析,深入研究了爆炸焊接过程中的界面瞬态行为,根据模拟数据重建了爆炸过程,发现剪切失稳引起的圆周运动和早期形成的空腔的共同作用,导致覆板对波浪中部产生冲击,左侧呈现内凹弧形,如图4所示。通过模拟分析还能够观察到涡流区晶粒熔化、机械混合、Fe晶粒形核、Cu晶粒形核、长大的演变过程。南昌大学的SONG等[29]用无网格划分的广义插值质点法(GIMP)对铜/不锈钢板爆炸焊接过程进行了三维数值模拟,并对界面波进行了二维数值模拟,对爆炸焊接工艺参数进行了计算,通过对试验得到的样品进行剪切测试、显微硬度分析和界面EDX分析,发现其满足核聚变设备的性能要求。
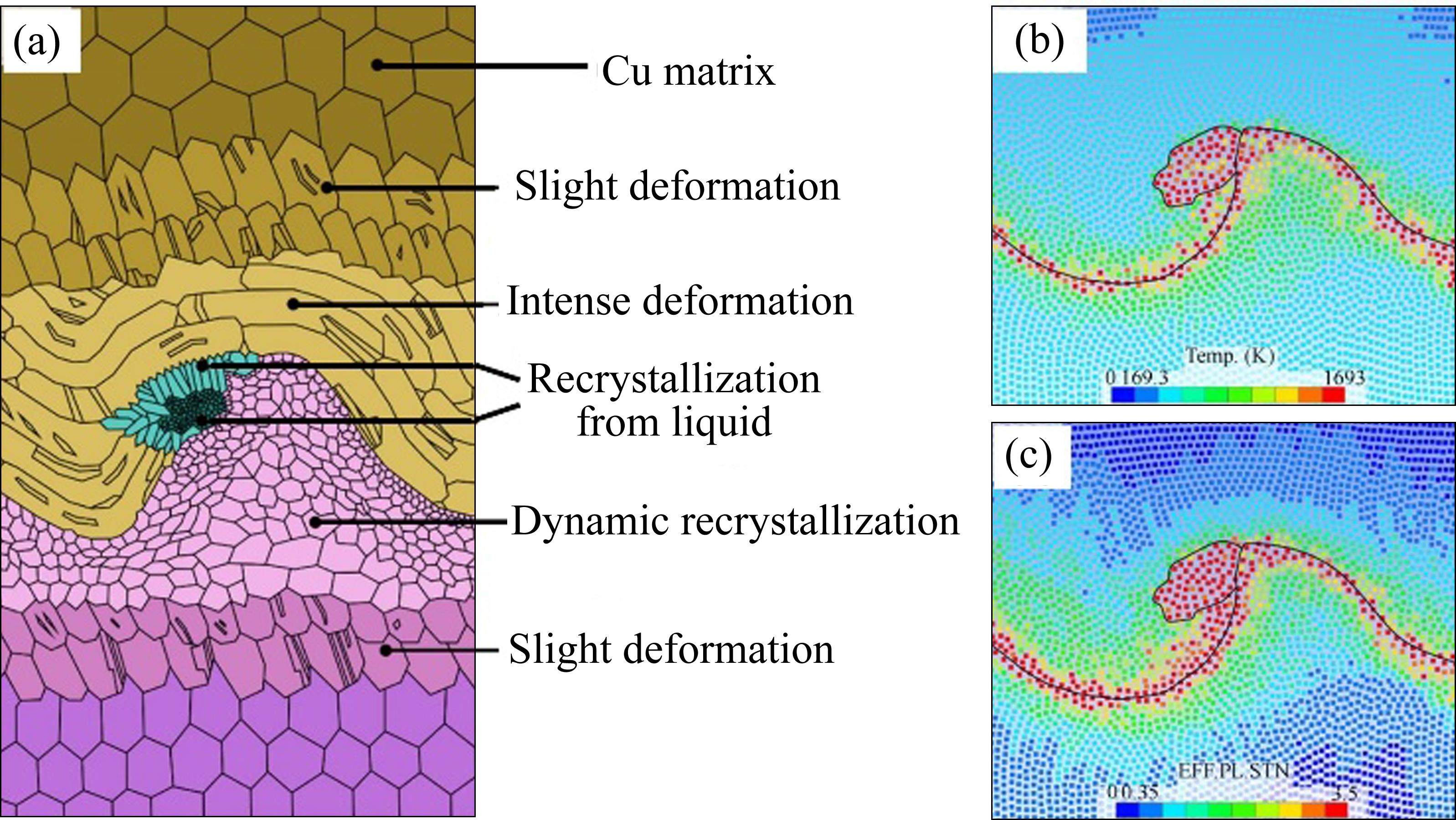
综上所述,利用爆炸焊接法制备的铜/钢复合板界面呈波纹状,界面两侧金属层显微硬度明显增大,产生了明显的塑性变形,并且界面处存在明显的扩散层,材料的各项性能均满足要求。但是爆炸焊接大多需要在户外操作,其产生的噪声、震动以及有毒气体均会对环境产生污染,而且工艺操作本身受制于气候因素,此外,机械化程度低、劳动条件差也使得爆炸焊接工艺难以得到广泛应用。
1.2 扩散焊接法
扩散焊接技术是一种固态焊接方法,其在高温条件下对层状金属施加压力,使金属材料之间紧密接触,并通过原子间的相互扩散实现冶金结合,如图5所示[30]。这种复合方法适用于异种金属材料、高温合金以及复合材料间的结合。扩散焊接过程可以分为三个阶段:首先是物理接触阶段,在压力和温度共同作用下,工件表面的微小不平处发生塑性变形,接触面积逐渐扩大,形成紧密接触;然后是扩散阶段,原子相互作用形成牢固的结合层;最后是结合层向体方向发展,形成可靠结合。这三个过程相互交叉进行,最终通过扩散和再结晶实现固态冶金结合。
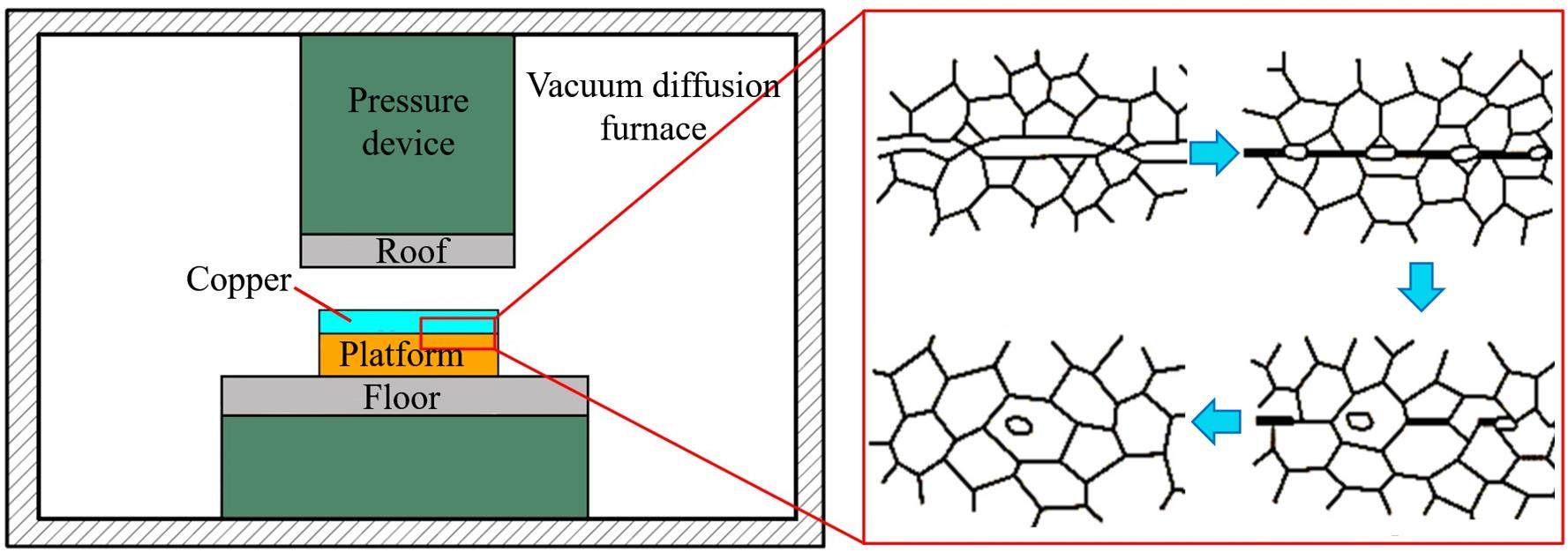
采用扩散焊接法制备复合板时,通常需要考虑异种金属材料之间元素扩散能力以及金属间化合物的生成情况。由于Ni与Fe和Cu之间有良好的互溶性,SABETGHADAM等[31]在铜板和马氏体不锈钢(410级)间使用Ni夹层,在800~950 ℃的温度范围和真空环境下,通过施加12 MPa载荷,并持续60 min的扩散焊接工艺成功制备出铜/不锈钢复合板。铜板和不锈钢板的厚度分别为3 mm和10 mm,中间Ni夹层的厚度为0.1 mm。研究表明,随着温度的升高,复合板界面剪切强度先升高后降低,在900 ℃时达到最大剪切强度145 MPa。扩散焊接过程中,Cu/Ni和Ni/SS界面均形成不同的扩散区,且随着温度升高,扩散层厚度明显增大。采用X射线衍射和能谱分析发现,在Ni/SS界面处有Ni、FeNi3、αFe、γFe、σFeCrNi和γFeNi形成,在Cu/Ni界面处有Cu、αNiCu、CuO和Ni形成。重庆大学的YUAN等[32]以脉冲压力代替恒定载荷,在825~875 ℃温度范围和真空环境下,以12.5 μm和50 μm厚度的纯Ni为中间层,在5~20 MPa的脉冲压力下扩散20 min,制备出纯铜/304不锈钢复合板。在850 ℃条件下可以明显发现,扩散初期界面会产生形状不规则的微孔,但随着时间推移,微孔消失,结合强度明显提高,如图6所示。而且Ni作为过渡层阻碍了Fe、Cr和Cu元素的相互扩散,在没有Ni箔的情况下,在界面区发现了厚度约为3 μm的含有Cu、Fe和Cr的薄区。其制备的铜/不锈钢复合材料在400 ℃温度下退火1 h后,抗拉强度达到217.2 MPa,而没有Ni辅助时,相同黏结条件下的结合强度约为174.2 MPa。
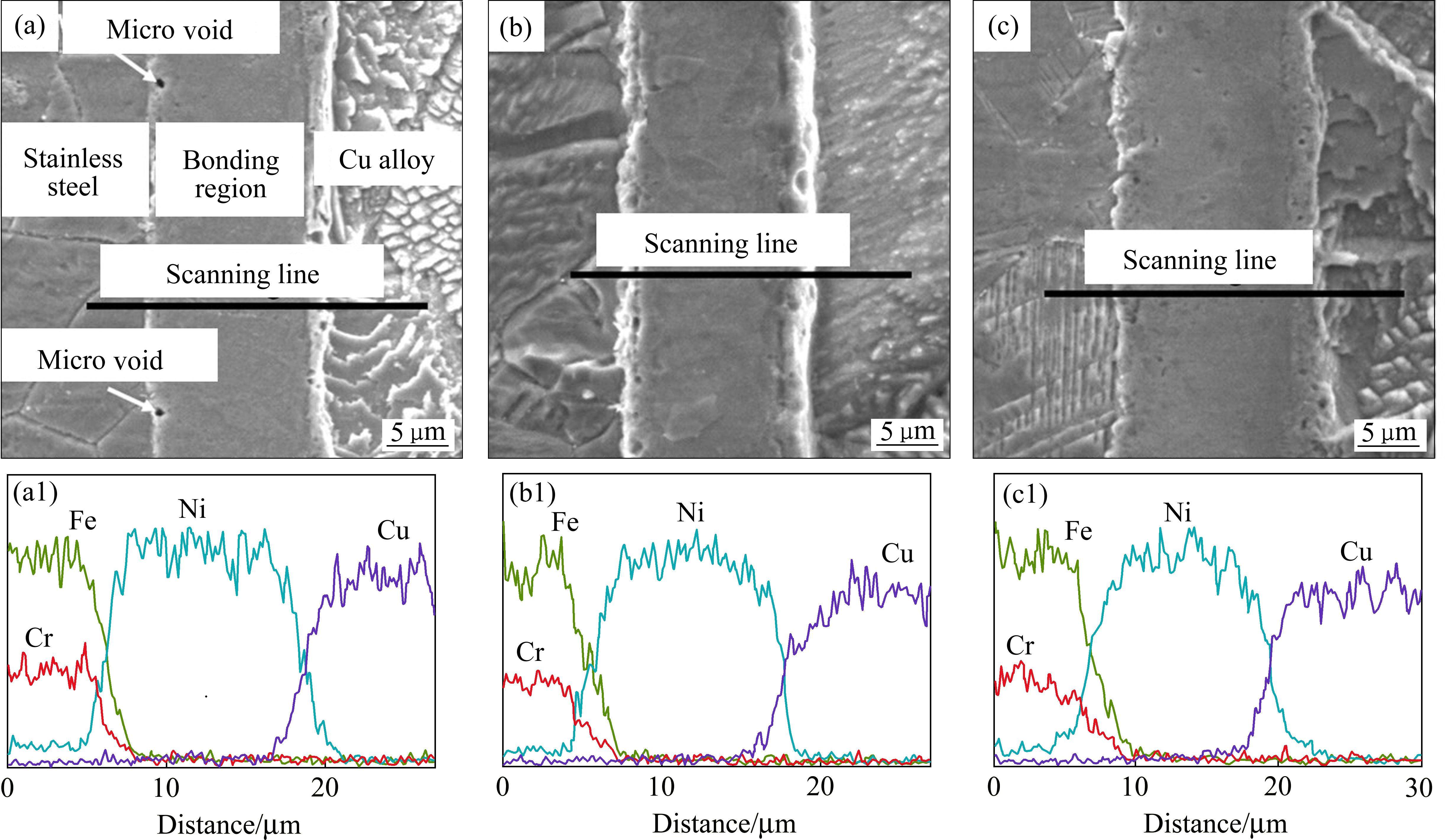
扩散焊接主要依靠元素扩散行为,复合板的结合质量直接取决于扩散温度、压力和时间等参数[33]。YILMAZ[34]研究了电解铜与304不锈钢之间的扩散结合,通过多次试验,发现在800~850 ℃温度范围、4~6.5 MPa压力下持续扩散15~20 min,复合板的抗拉强度达到了247 MPa。NISHI等[35-37]研究了氧化铝弥散强化铜(DS Cu)与316不锈钢的扩散焊接,发现扩散焊接温度对复合材料结合质量和力学性能的影响大于扩散压力或时间,且随着温度升高,材料力学性能有所提升。当温度达到1000 ℃时,在9.8 MPa的压力下持续扩散2 h,复合材料的抗拉强度达到了380 MPa。此外,他们还比较了Au、Cu和Ni分别作为中间夹层对复合材料力学性能的影响,发现将20 μm厚的Au作为中间层时复合材料拉伸性能更好,在850 ℃、9.8 MPa条件下持续扩散2 h,复合材料抗拉强度达到了405 MPa。哈尔滨工业大学的张洪雨[38]采用真空扩散焊技术制备出50 mm/50 mm大厚度TU1铜/304不锈钢复合材料。通过比较不同温度、扩散压力和保温时间,发现扩散焊接压力为2 MPa、保温时间为60 min、真空度为5.0×10-3 Pa、扩散焊接温度为950 ℃时,材料的力学性能最佳,抗拉强度能够达到290 MPa,比母材强度高出90%。
为了研究多层材料之间的扩散行为,VIGRAMAN[39]将厚度均为0.1 mm的铜箔与304不锈钢箔材依次堆叠,在925 ℃施加4 MPa压力 60 min时,复合板硬度达到最大值342.6 VHN,剪切强度达到72.8 MPa。由于扩散焊接独特的结合方式,复合板可以在小变形下实现结合,并且复合界面平直,层间有啮合特征,铜层在高温作用下发生回复与再结晶,形成退火组织,提高了多层复合材料抗裂纹扩展能力[40]。为了进一步制备出更薄的多层复合材料,YANG等[41]采用重复扩散轧制的方式制备了无氧铜(OFC)/电纯铁片复合板,其基本工艺流程如图7所示。Cu和Fe片经过交替堆叠,先在真空炉中以850 ℃的温度和10 MPa的压力扩散焊接30 min。然后采用冷轧进行减薄,将扩散焊接和冷轧交替重复多次,最终得到多层复合薄板。当板层厚度在25 μm以上或总减薄小于99%时,宏观上可以得到平直的界面。扩散焊接后通过第一道次轧制变形的界面结合强度由190 MPa提高到280 MPa,接近Cu的抗拉强度。
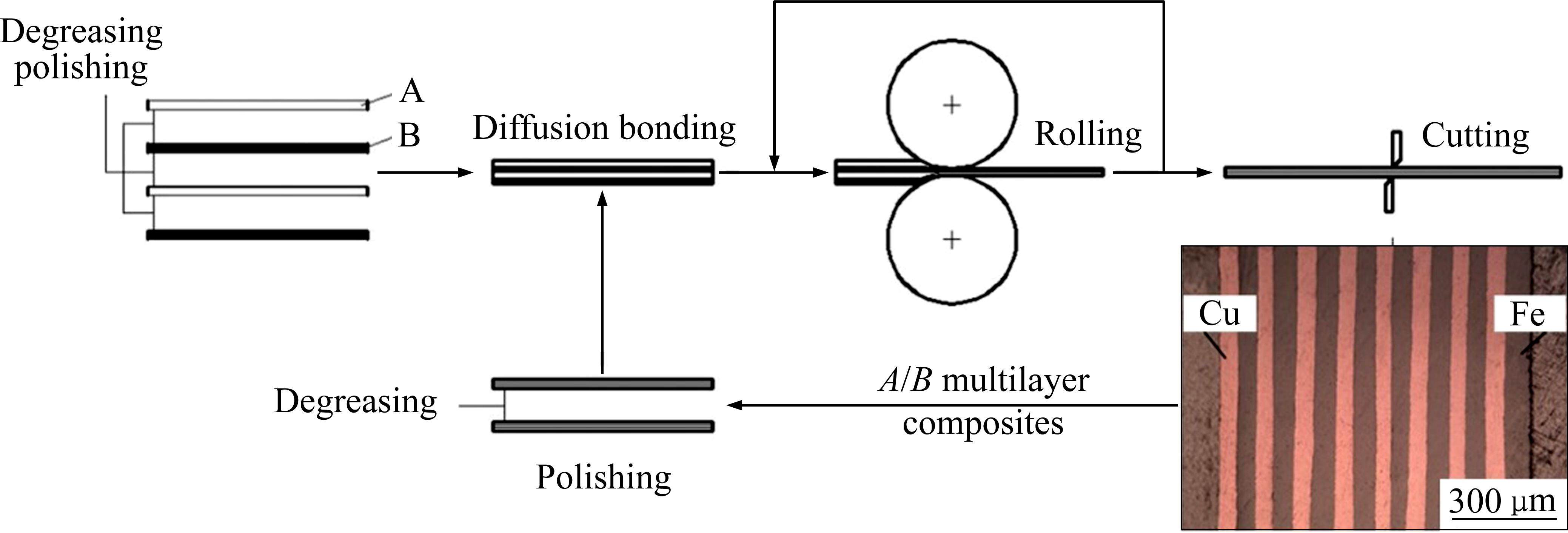
总而言之,扩散焊接对真空环境要求高,参数设置不当会导致扩散焊接后母材晶粒过大,影响整体力学性能,且扩散焊接法受限于设备和工艺水平,设备的加热腔体尺寸制约了可加工工件的尺寸,导致产品规格有限。此外,扩散焊接周期较长,生产效率低,批量连续生产困难。
1.3 轧制复合法
轧制复合法是指在巨大的轧制压力作用下,基体金属表面的氧化膜发生破碎,出现明显的塑性流动,使得金属原子在界面周围紧密接触,通过热输入和原子扩散形成良好的结合界面,其工艺原理如图8所示。
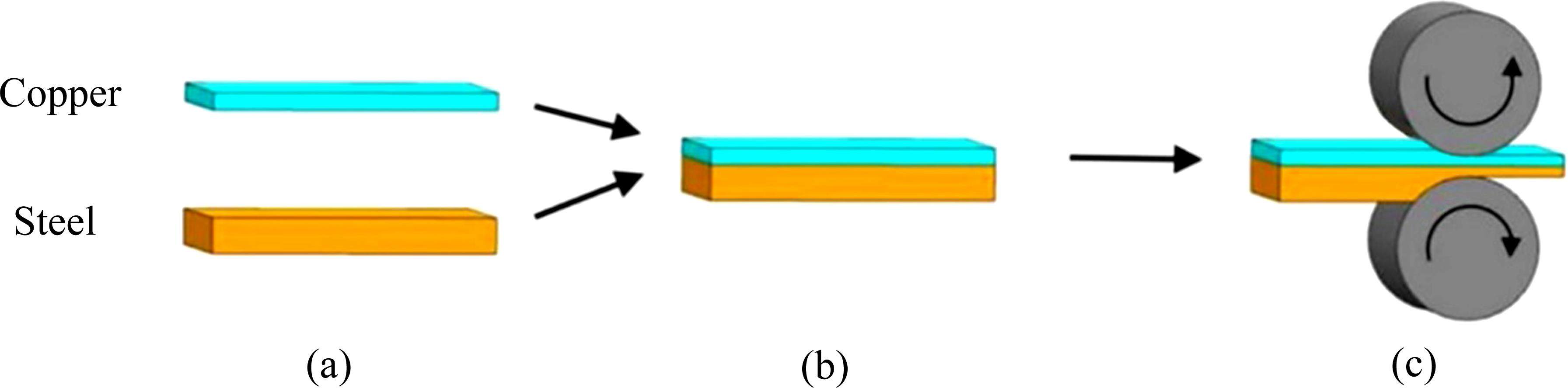
根据轧制温度的不同可将轧制复合法分为热轧复合法和冷轧复合法。利用热轧复合法制备金属层状板最早出现于20世纪40年代,其广泛应用于厚板的制造。该方法是对两种或多种金属材料进行加热,待金属材料达到一定温度时,利用热轧机对材料施加一定的压力,在高温高压环境下,使相同或者不同的金属材料实现复合。热轧复合前,基体金属要预热到一定温度,以降低材料变形抗力,避免界面裂纹的形成。同时,还要添加惰性气体以避免界面金属间化合物的生成和表面金属氧化[42]。与之相比,冷轧复合法是在常温环境下对金属原材料实施一系列冷加工,将金属加工成不同样式的板材。该方法虽然对轧机性能要求高,但是不需要真空设备,且生产速度快、产量高。冷轧复合制备工艺主要过程为表面处理→冷轧复合→扩散退火,首道次压下量一般为60%~70%。在轧制过程中铜和钢表面的脆性加工硬化层破裂,露出新鲜金属,在压力作用下形成机械结合,经过后续退火以消除内应力,使界面结合更牢固。
VASEGHI等[43]采用冷轧复合的方法,将黄铜和St14钢复合在一起,制成铜/钢/铜三层复合板。通过不同压下量的轧制实验,发现界面结合强度随着压下量的增大而增大,并且在压下量为48%时,复合板成功结合在一起,界面剥离强度达到12 N/cm。当压下量达到66%时,界面剥离强度达到最大值33 N/cm。然而,利用冷轧复合法制备出的复合板往往在界面内存在一定的残余应力,不同的热处理方式可以促进原子扩散,改善复合板力学性能。沈阳大学的李祥平[44]通过冷轧复合的方式制备了T2铜/45钢/T2铜层状复合板,其初始厚度为1.8 mm/1.2 mm/1.8 mm,冷轧压下量为55%,得到的铜/钢复合板抗拉强度达到了390.5 MPa。通过比较不同的热处理工艺,得到最佳退火温度为850 ℃,保温时间为2 h,此时复合界面已完整结合且结合面积最大。制备得到的复合板具有较好的塑性成形能力,反复弯曲次数均在8次以上时覆层才开始出现微裂纹。并且在拉伸过程中其结合界面并未发生分离,拉伸断口的微观形貌韧窝丰富,表现为明显的塑性断裂。
为了满足高性能化、微型化发展的要求,一些学者对厚度小于0.5 mm的铜/钢复合薄带进行了一系列研究。河北工业大学的LIU等[45]进行了大变形量的轧制,采用冷轧复合→中间退火→冷轧减薄的工艺,得到350 μm厚的铜/钢/铜复合板,其厚度比达到了1∶100∶1。选取与轧制方向成不同角度的试样进行拉伸试验,其拉伸断裂过程如图9所示[45]。试验发现,铜/钢复合板沿轧制方向的屈服强度为232.4 MPa,且随着拉伸角度的增大,试样屈服强度先增大后减小,当拉伸角为45°时,复合板的屈服强度和极限强度分别达到最大值261.0 MPa和335.9 MPa。通过后续退火处理,当温度为450~800 ℃时,复合界面出现2~3 μm厚的扩散层,且复合板的拉伸极限强度和断裂伸长率均随着退火温度的升高而逐渐降低。由于退火作用,轧制变形产生的残余应力得到释放,界面实现冶金结合。受各向异性的影响,退火温度为600 ℃和700 ℃的复合板的所有断裂角几乎均为90°,而退火温度为800 ℃时各向异性消失,断裂角远离90°。与此同时,东北大学的陈敬琪等[46]通过冷轧复合(75%压下率)→中间退火(400~1000 ℃,保温2 h)→冷轧减薄(厚度为0.06~0.3 mm)→轧后退火(200~500 ℃,保温2 h)的工艺制备出不同规格的铜/钢/铜复合薄带。通过比较,厚度为0.1 mm的复合薄带经过500 ℃、2 h退火后,反复弯曲达到650次。随着复合带厚度逐渐减小,其弯曲性能近似线性增强,退火温度与弯曲性能基本呈指数关系变化。微观表征发现,铜层和钢层内部经历较大塑性变形后产生大量的位错和晶格畸变等缺陷,经过退火后残余应力得以消除,缺陷的存在还促进了异种原子之间的相互扩散,从而增加了复合带的界面结合强度。
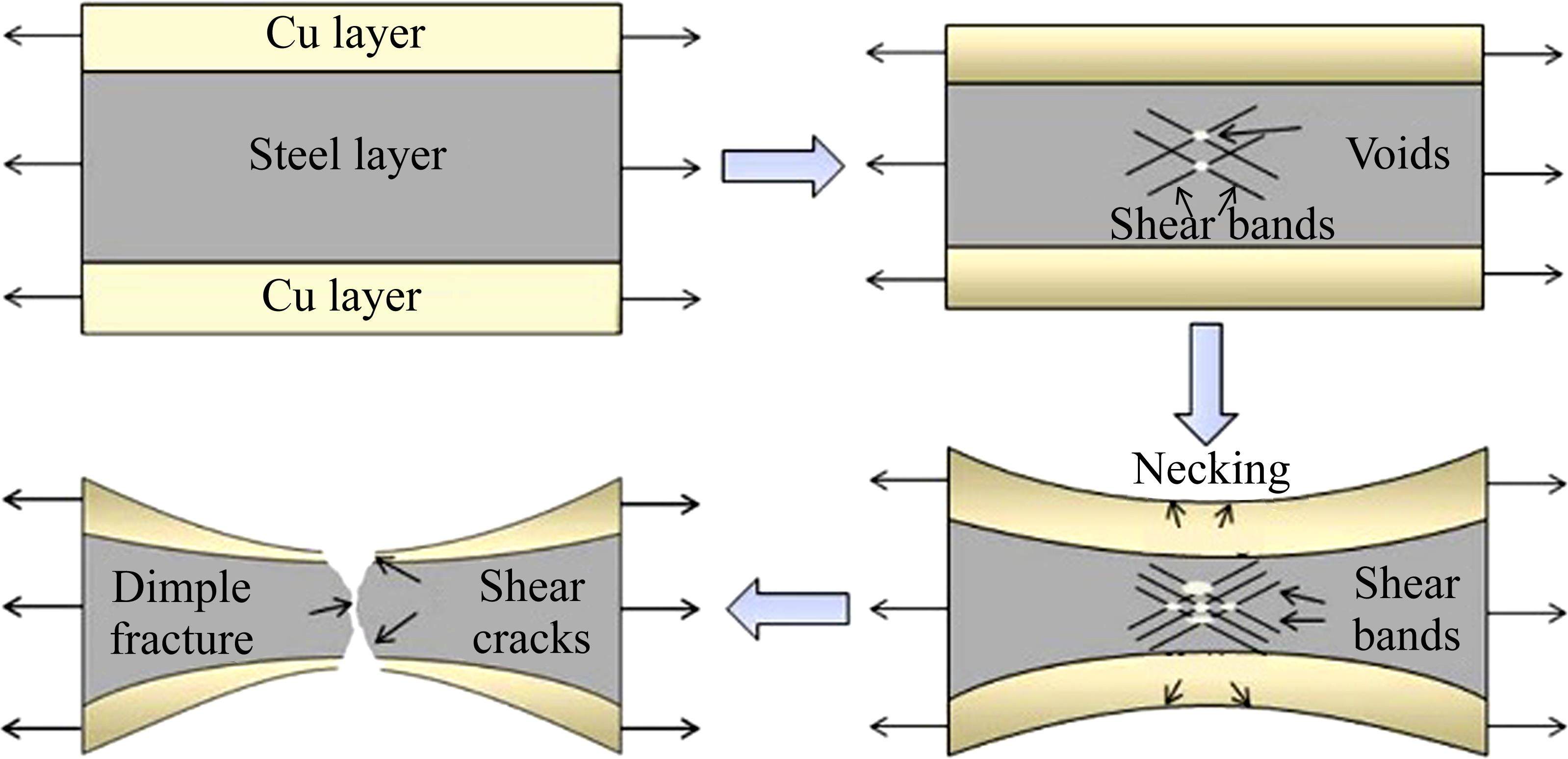
总而言之,在热轧过程中,高温环境容易导致金属元素间的相互扩散和反应,从而形成中间层或中间化合物,这些化合物对复合板结合性能的影响不同。在冷轧过程中,金属板材的塑性降低,变形抗力增大,从而使轧制过程变得困难,可能导致复合界面结合不良,影响复合板质量。
1.4 固-液复合法
固-液复合法制备铜/钢复合板的基本原理是将液态金属或合金浇注到固态金属板材的表面,通过控制浇注温度、速度和冷却条件等参数,使液态金属与固态金属发生冶金结合,从而制得具有优良性能的复合板。由于铜和钢在物理性能上的差异较大,通常是将熔融的铜液浇注到钢基体上,其示意图如图10所示[47]。
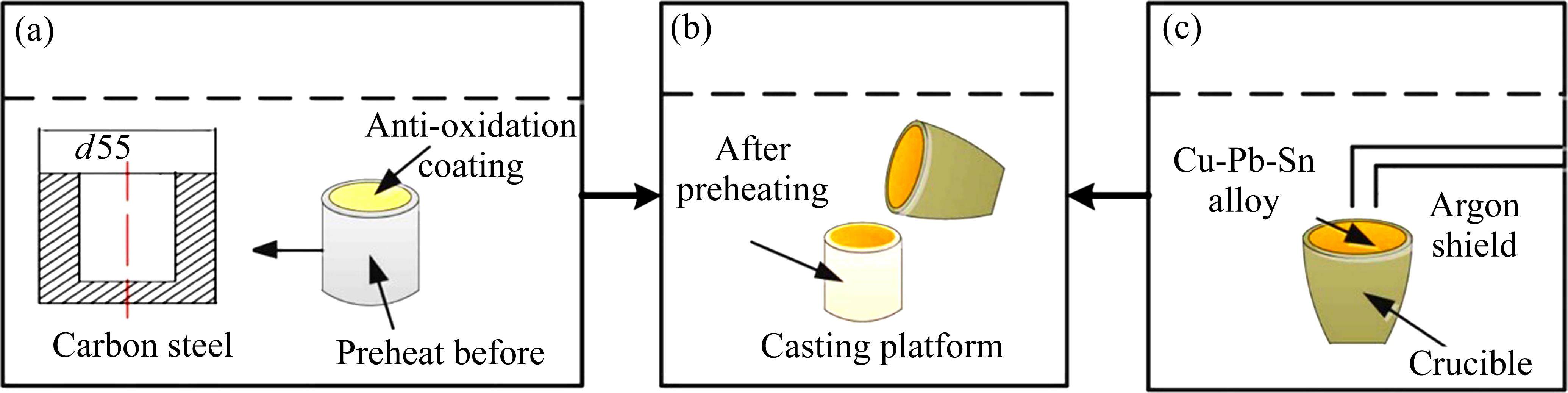
固-液复合过程中,钢基体的材料、预热温度和预热时间对复合板的性能有很大影响。中北大学的邢明等[48]采用正交试验法研究了不同钢基体参数对铜/钢界面的影响。比较发现,钢基体为45钢、预热温度为1200 ℃、预热时间为2.5 h时,铜/钢复合界面结合效果达到最佳,此时界面结合强度达到133 MPa,Cu原子和Fe原子之间的扩散距离达到14 μm。除此之外,铜合金中的一些元素对复合板界面结合强度也有显著影响。KANG等[47]将P含量为0~0.25%(质量分数)的Cu-Pb-Sn铜合金加热后浇注在预热温度为(1150±30) ℃的钢基体上,制备出铜/钢复合材料。研究发现,随着P含量的增大,Cu-Fe元素扩散层也增大,但同时生成了硬脆的Fe3P沉淀层,导致界面剪切强度下降,其界面结合机理如图11所示[47]。而当P含量为0.1%时,复合界面实现冶金结合,Fe与Cu的界面原子扩散距离达到11.55 μm,材料剪切强度达到最大值157.89 MPa。
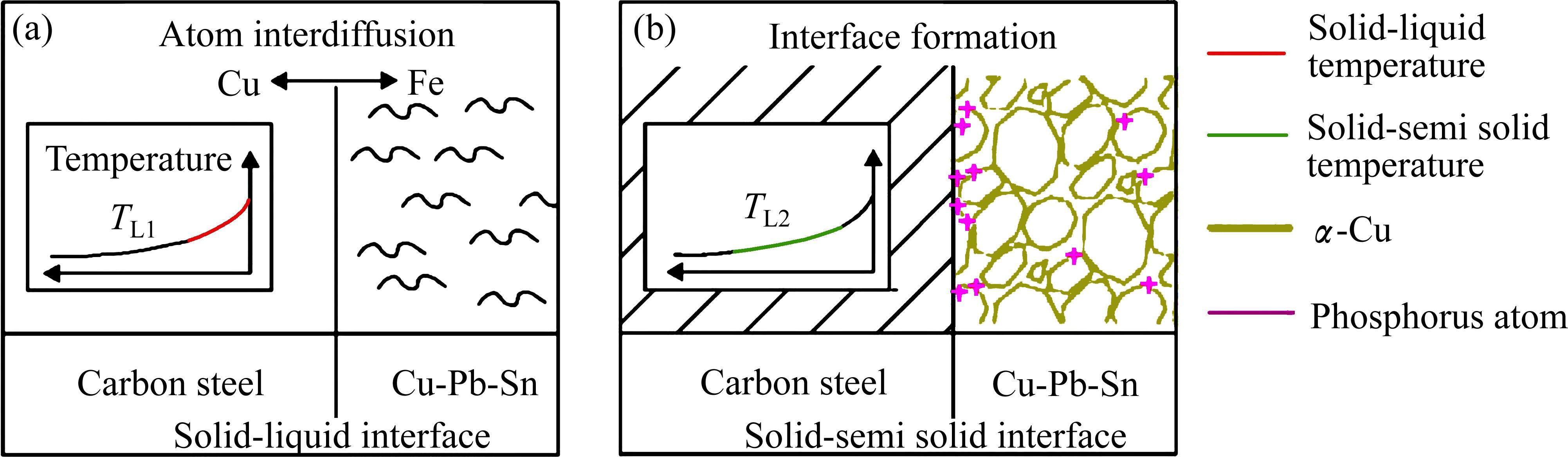
相比于直接浇注,采用熔铸工艺可以减少能量消耗。这种工艺通过在模具中直接加热双层金属,使得熔点较低的铜合金率先融化,然后在冷却过程中实现材料的复合。任冰冰等[49]研究了加热条件和冷却速率等熔铸工艺参数对高铅青铜CuPb15Sn7/45钢复合界面和组织性能的影响规律。当装炉温度为900 ℃、保温温度为1015 ℃、保温时间为5 min并采用氮气冷却时,铜/钢界面形成冶金结合,界面拉伸断裂强度达到200 MPa;铜合金区中铅颗粒分布均匀,铅元素烧损量低于1%;钢基体的组织和晶粒尺寸分布合理,表现出优异的熔铸复合效果。
除了改善工艺参数,施加机械振动也能够有效细化晶粒,改善力学性能,消除疏松缩孔,减少气孔和裂纹等缺陷[50]。合肥工业大学的杨世豪等[51]通过在CuPb10Sn10铜合金/45钢熔铸工艺的冷却过程中对铸件施加机械振动,研究了在0.2 mm振幅条件下,振动频率对铜合金凝固组织和铜/钢复合材料结合面的影响。结果表明:在铸件冷却阶段,随着振动频率增大,铜合金晶粒表现出先细化后粗化的趋势,如图12所示[51]。当施加机械振动的振幅为0.2 mm、频率为40 Hz时,铜侧凝固组织得到有效细化,硬度显著提升,铜合金晶粒由树枝晶转化为等轴晶,铅元素偏析和聚集现象得到明显改善,气孔和显微缩松被有效消除。通过微观组织表征,发现铜合金和钢基体之间形成了冶金结合,且机械振动频率不会改变元素扩散速率,而振动后α+δ硬脆相的重新分布会导致剪切强度降低。
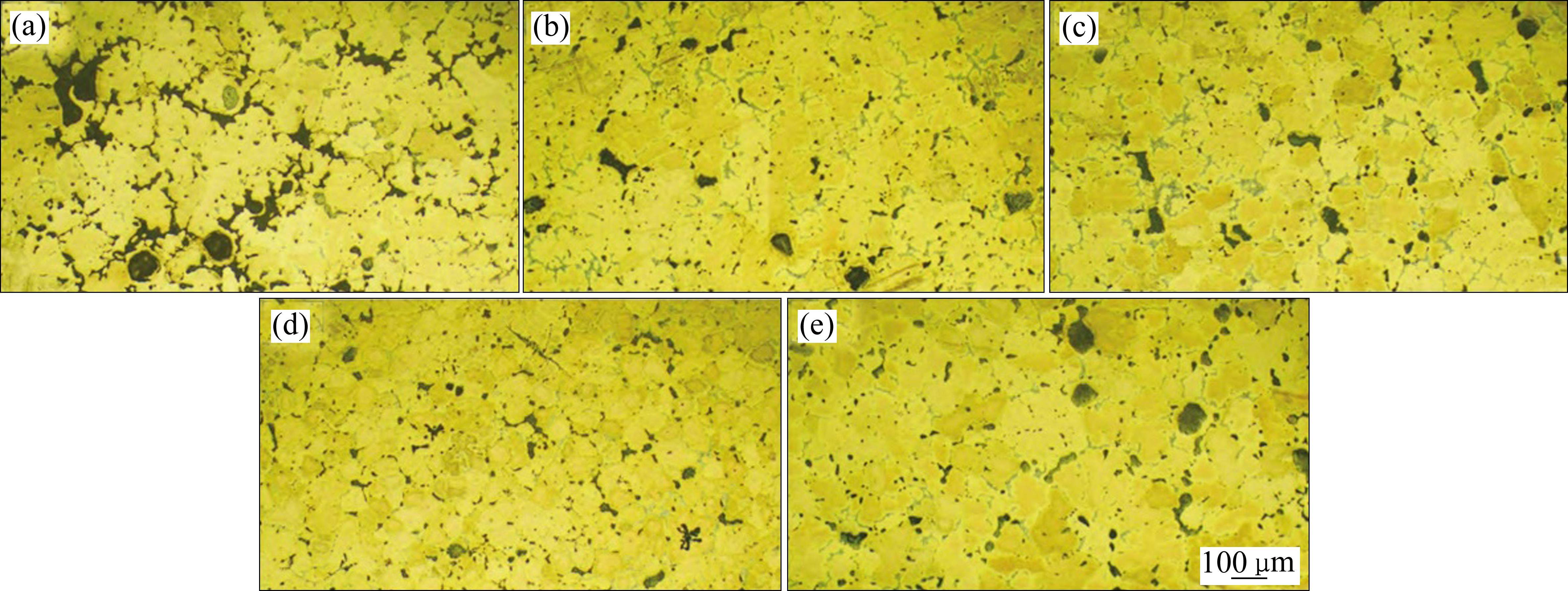
在固-液浇注过程中,液态金属与固态金属的界面控制较为困难,也容易出现表面不平整、夹杂物等问题,影响复合板的表面质量,为此将固-液浇注后的复合板再进行单道次轧制复合,可以明显改善表面粗糙度,提高复合板的力学性能[52]。冯丹竹等[53]以液态纯铜浇注固态EH420钢制备出铜/钢复合材料,研究了复合板的形变量对其界面结合性能的影响。研究发现,随着复合板的形变量增大,晶粒更加细小,界面过渡层逐渐增大。在40%变形量下,界面元素扩散距离可以达到17 μm。而刘承斌[54]进一步采用连续固/液浇注法成功制备了复合界面良好的铁白铜(Cu-10%Ni-1%Fe,质量分数)与钢(SAE1010)的双金属复合板。通过对铸态复合板分别进行冷轧和热轧(温度为700~900 ℃)处理,发现冷轧复合板的形变量从30%到70%所对应的界面扩散距离为1.57~1.03 μm,热轧复合板的扩散距离为1.90~0.99 μm,且扩散层厚度随形变量增加不断减小。比较发现,冷轧并没有促进界面元素扩散,而热轧初期对界面元素扩散有促进作用,但当复合板形变量超过50%时,无论冷轧还是热轧,对扩散层厚度的影响都很小。当冷轧形变量达到70%时,复合板界面剪切强度明显提高,由铸态的228.3 MPa提升到545.0 MPa。冷轧初期复合板形变量对弯曲断裂强度的提升不明显,形变量达到70%时,弯曲断裂强度由851 MPa升高到1105 MPa,较高的弯曲断裂强度表明复合板结合状况良好,具有良好的抗弯能力。
总而言之,固-液复合法制备铜/钢复合板操作流程复杂,液态金属的浇注温度、速度、冷却速度,以及钢基体的材料、预热温度、时间等因素均会影响复合板的成型质量。此外,受限于模具,复合板厚度较大,而且界面结合强度不高,需要经过进一步加工,难以实现大批量生产。
1.5 搅拌摩擦焊接法
搅拌摩擦焊接法(FSW)是一种固态连接技术,通过搅拌头的旋转和前进运动产生摩擦热,使接触部分的材料被局部加热,并在搅拌头的搅拌作用下使异种材料复合在一起[55]。采用搅拌摩擦焊接法制备的铜/钢复合板通常用于储存核废料的罐体、国际热核反应堆以及海洋船体表面防腐,其工艺原理如图13所示[56]。
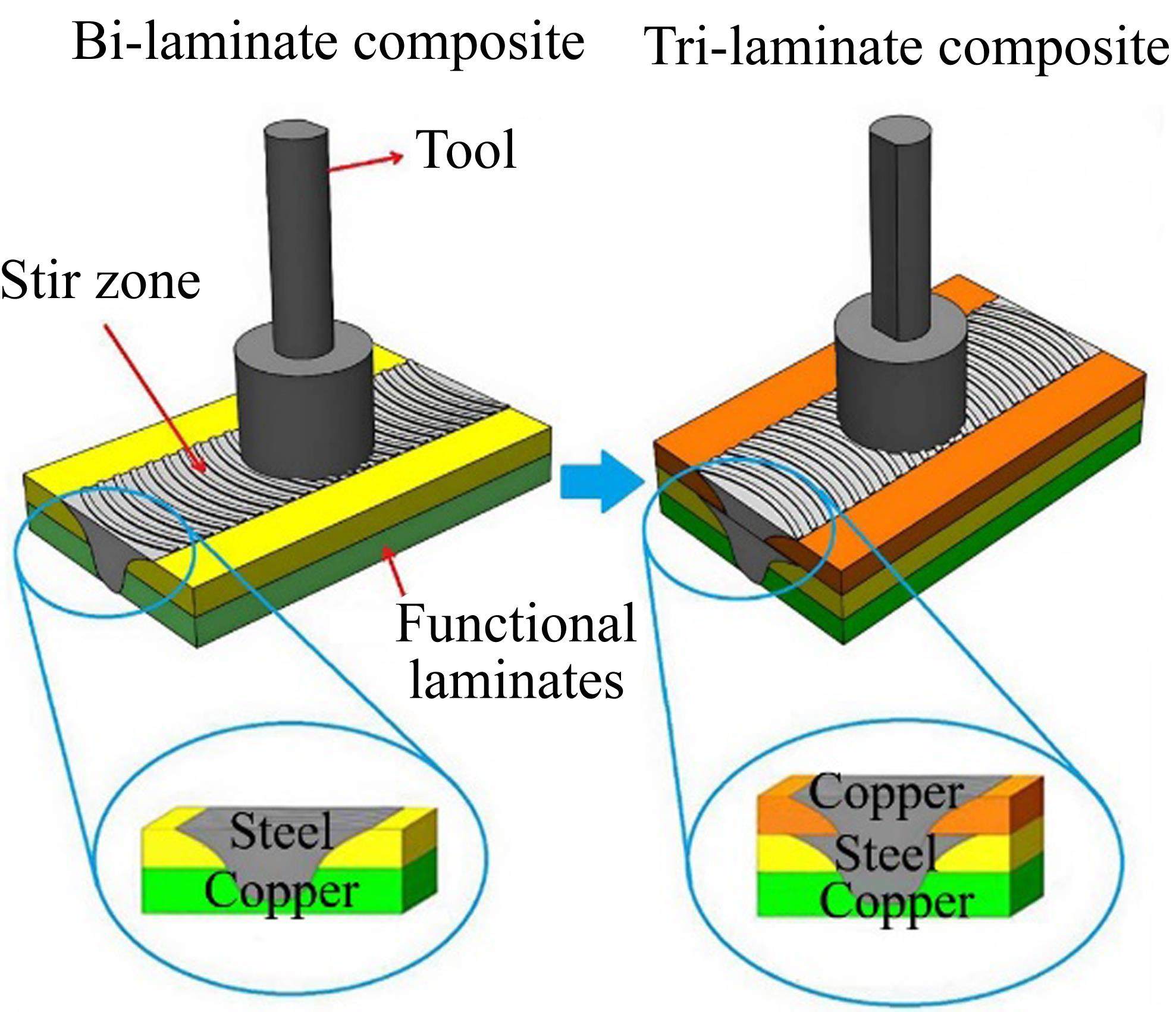
搅拌摩擦焊接法的主要工艺参数有主轴转速、刀具行程速度、倾斜角以及刀具偏移量等。MAHTO等[57]采用搅拌摩擦焊接法将厚度分别为3 mm和6 mm的商用铜板和AISI1018钢板复合在一起,研究了不同工艺参数下界面结合性能和复合板力学性能。结果表明,刀具偏移量会影响焊接效率和界面结合强度,当主轴转速为700 r/min、焊接速度为100 mm/min、刀具偏移量为6 mm和8 mm时,界面氧化层破裂,并能实现良好重叠,形成一个没有表面喷射效应和氧化物污染的搅拌区。制备得到的铜/钢复合板屈服强度和抗拉强度介于基体铜和钢板之间,分别达到了261 MPa和359 MPa。MAHTO等[58]进一步测试了铜层材料的耐腐蚀性能,观察到铜/钢复合界面处,铜侧晶粒没有细化,而钢侧晶粒明显细化。铜/钢界面出现明显的波浪状,并伴随着机械互锁,微观结构如图14所示。
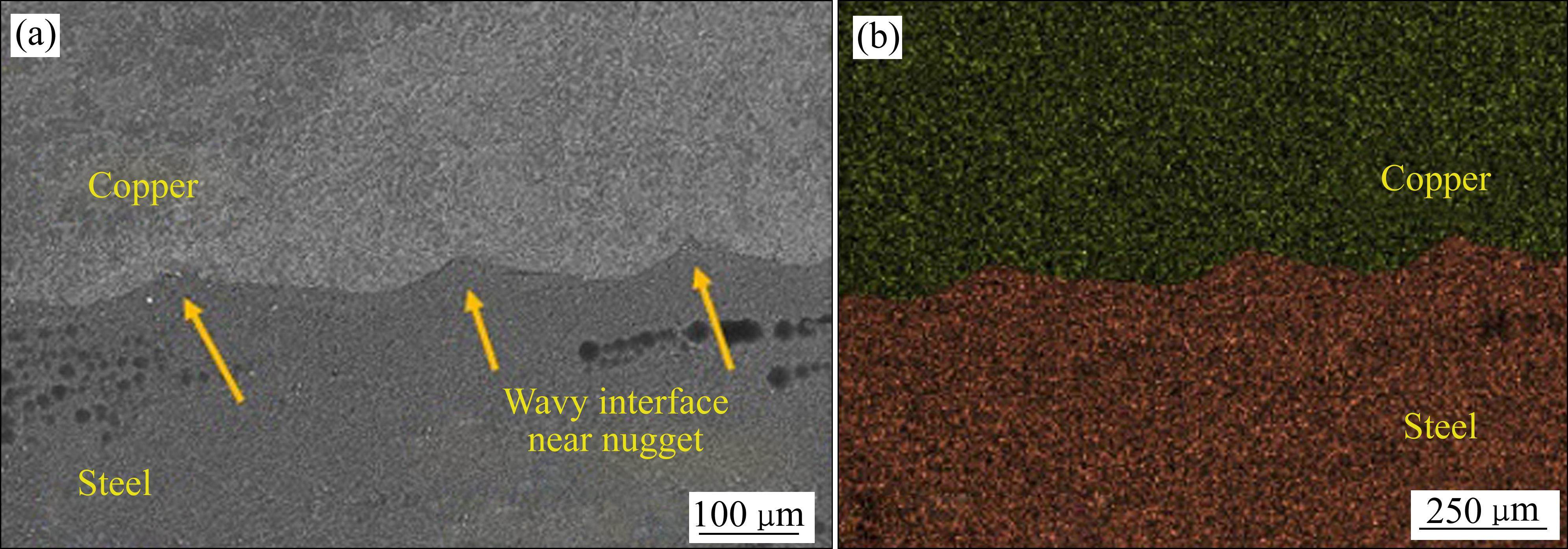
搅拌摩擦增材制造法(FSAM)作为一种新型技术,将增材制造和搅拌摩擦结合在一起。其基本原理是将刀具插入重叠板的顶部,该刀具向前移动,导致板材由于摩擦热和较大的塑性变形而黏合在一起[59]。这种方法一方面克服了增材制造过程中的内部孔隙、夹杂物和微观结构缺陷,另一方面通过搅拌摩擦还能细化晶粒,并显著提升材料的机械性能,因而成为金属材料固态复合的重要方法[60]。太原理工大学的GUO等[61]采用FSAM技术将厚2 mm的T2纯铜和厚4 mm的Q235钢板成功复合在一起,如图15所示。其采用的搅拌刀具转速为600 r/min,行走速度为50 mm/min,倾斜角为2.0°,刀具在钢基体中的穿透范围为1.0~1.4 mm。通过微观结构表征,发现铜和钢之间形成了波浪状界面,且元素扩散明显,实现了冶金结合。复合板的力学性能明显提高,抗拉强度和剪切强度分别为435 MPa和345 MPa。
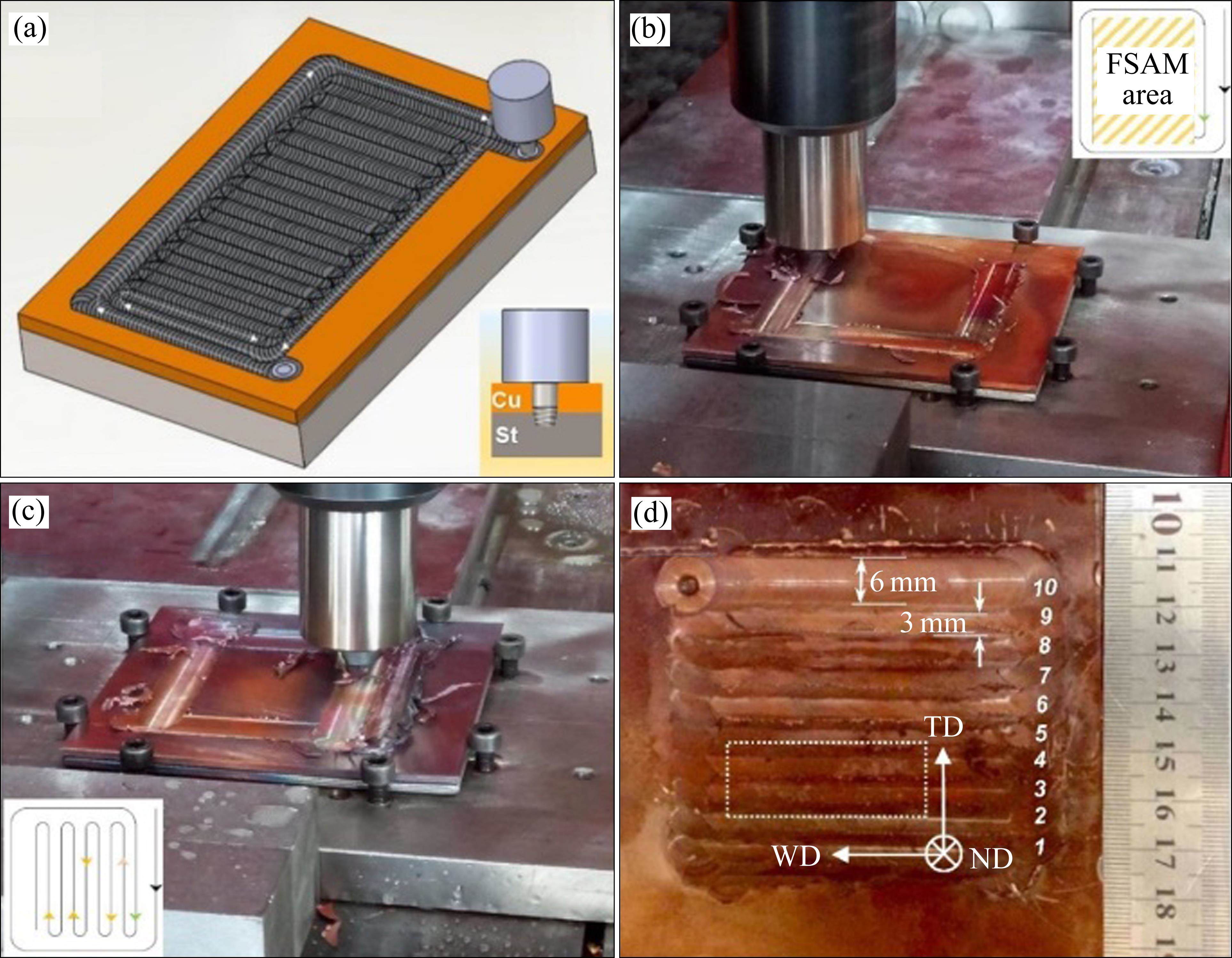
总而言之,采用搅拌摩擦焊接工艺制备的复合板界面实现了冶金结合,并且形成波纹状界面,力学性能和机械性能提高。但是,搅拌过程中的几何和工艺参数(如刀具移动速度、切入深度等)如果选取不当,容易影响金属流动性,从而产生内部孔夹杂、氧化物和表面缺陷等[62]。另外,搅拌摩擦焊接法制备复合板效率较低,不适用于异种金属薄带和中厚板界面复合,难以实现大批量生产。
通过上述对比分析可知,不同的制备工艺具有不同的优缺点,具体如表1所示[20, 33, 63]。轧制复合法研究最为广泛,但铜/钢复合板轧制复合过程中首道次压下率较大,对设备要求较高;在相同温度条件下铜层和钢层变形不协调,复合板内残余应力较大,需要对轧制得到的板料进行后续热处理。爆炸焊接法制备的铜/钢复合板会产生波纹状界面,结合质量较高,但是炸药对环境友好性较差。扩散焊接法也是一种有效的铜/钢复合板制备方法,在热量和压力的共同作用下,元素需穿过表面的氧化膜才能发生互扩散,与轧制复合法相比,扩散焊接法所需温度较高,一般高于850 ℃,且对设备要求高,需要真空环境,得到的复合板表面粗糙度大。固-液复合法和搅拌摩擦焊接法也可以制备界面性能良好的铜/钢复合板,但是其操作过程复杂,需要考虑金属熔化后的凝固条件、凝固顺序等因素。
Preparation process | Applicable materials | Advantage | Disadvantage |
---|---|---|---|
Explosive welding method | Large area and thickness dissimilar metal materials | Corrugated interface; Metallurgical bonding; High bonding strength; No external heat source required | High equipment cost; Significant noise and vibration; Greatly affected by explosion parameters |
Diffusion welding method | High melting point and small size dissimilar materials | Organization homogeneity; High interface bonding strength | Poor surface quality; Vacuum environment; Long cycle and low efficiency |
Rolling compound method | Large area and long dissimilar materials | Mechanical combination; High production efficiency | Generation of residual stresses; Localized oxidation of materials; Not applicable to brittle materials; High requirements for rolling mills |
Solid-liquid complex method | Thin plates and small parts; Significant differences in melting points | Small material deformation; High interface bonding strength; Mature technology, simple operation and strong flexibility | Material size is limited by the mold; Greatly affected by process parameters |
Friction stir welding method | Light alloys; Large area and thickness dissimilar metal materials | Corrugated interface; Metallurgical bonding; Mechanical combination; Good mechanical properties | Low productivity; Poor surface quality; High technical requirements |
1.6 其他复合工艺
随着科技发展,一些制备铜/钢复合板的新型技术如增材制造、激光熔覆、冷喷涂、激光辅助冷喷涂等逐渐受到学者的广泛关注。这些新型技术的基本原理是通过热效应或者冲击压力,使铜作为涂层覆盖在钢基体表面,最终实现冶金结合。
其中,增材制造技术应用最为广泛。由于纯铜在热交换器和其他电器元件中具备不可替代的优良导电导热性能,采用增材制造技术能够解决纯铜在复杂零件成型方面的问题,提高零件的机械力学性能[64]。OSIPOVICH等[65]以高能电子束作为热源,将304不锈钢丝和C11000铜丝作为原料,在钢质基板上分别沉积了10层钢丝和5层铜丝,形成了60 mm厚度的铜/钢梯度层状材料。通过逐层分析发现,当铜丝开始沉积时,钢丝沉积层会发生部分重熔,铜在奥氏体不锈钢的晶界中沉积凝固,形成网格树枝晶间、晶界层和小铜颗粒;随着铜丝进一步添加,铜聚集形成铜基薄片,并保留奥氏体的网格和粗铜颗粒,形成明显的过渡区域,伴随有纳米级铜颗粒从钢中铜的过饱和固溶体中析出。为了改善Fe/Cu组分的溶解度,ZYKOVA等[66]进一步对电子束送丝增材制造的铜/钢复合试样进行搅拌摩擦处理,其工艺流程如图16所示。经过搅拌摩擦加工后,复合试样的显微硬度提高了50%,摩擦因数降低了25%。
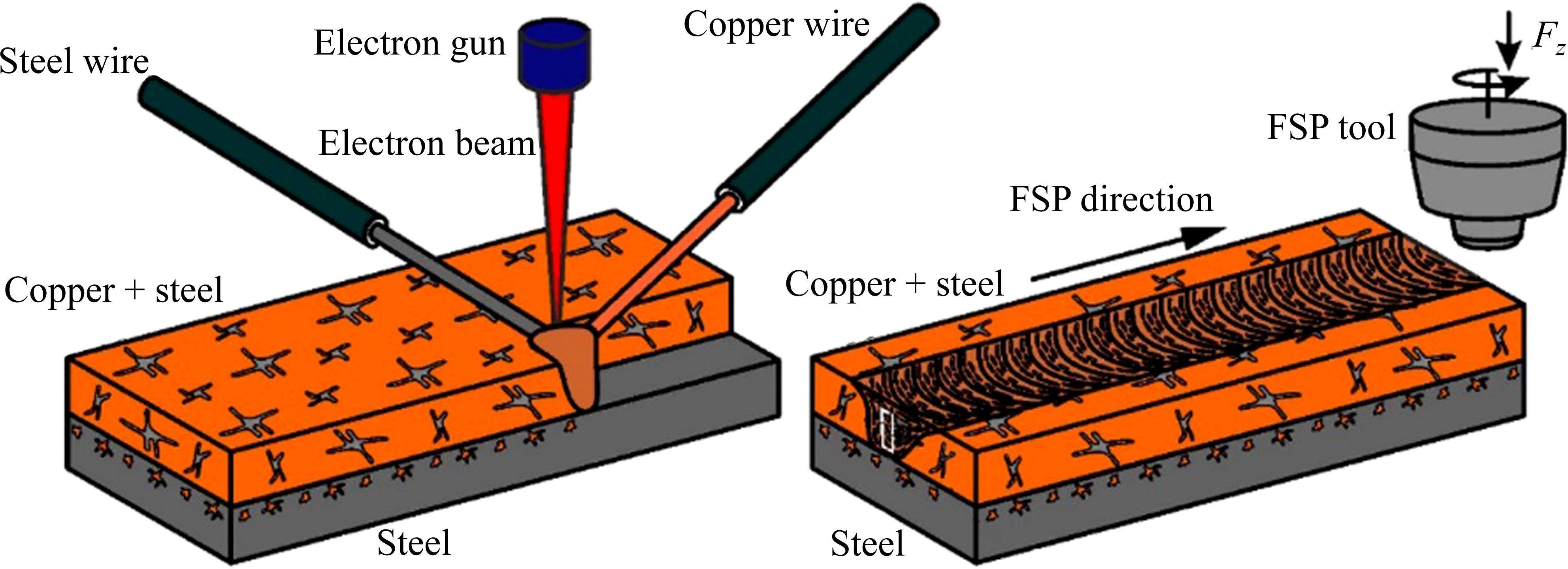
除了直接选用纯铜丝作为原料外,一些学者也将铜合金作为焊丝材料,使其与钢基体结合形成复合板来替代铸造铜合金材料。DHARMENDRA等[67]采用电弧增材制造的方法将60层镍铝青铜(NAB)沉积在10 mm厚的316不锈钢层上,制备了铜/不锈钢复合板。由于反复沉积的热效应和NAB中Al元素的扩散,铜/钢界面处形成了2 μm厚的Fe3Al层,界面实现了冶金结合。在另一项研究中,东南大学的CAI等[68]采用单通道电弧增材制造方法将1.5 mm厚的镍铝青铜(NAB)沉积在3 mm厚的316不锈钢层上下表面,铜/钢界面处只形成了1.3 μm厚的Fe3Al冶金层,而且低电流和Ni元素扩散抑制了不锈钢侧穿透裂纹的生成。在拉伸断裂过程中,裂纹优先出现在铜侧,表明复合界面结合良好,并且与离心铸造法制备的NAB相比,铜/钢复合板的抗拉强度由634.1 MPa提升到721.8 MPa,硬度从190HV提升到245HV,增幅接近30%。
与增材制造技术类似,使用激光熔覆技术时铜也发生了熔化。其基本原理是利用高能激光束照射覆盖在钢基体上的铜颗粒,使其快速熔化并与钢基层融合,形成具有双金属性能的复合板,如图17所示[69]。在激光熔覆过程中,往往会出现未熔合或过熔现象,复合界面的性能往往受到铜粉含量[69]、基板材料[70]和激光工艺参数[71]的影响。西安交通大学的缪喆宇等[72]研究了不同的激光功率、扫描速率参数对复合界面组织的影响。研究发现,在铜粉厚度为1 mm、粉胶比为1∶1的条件下,选择激光功率为1 kW、激光扫描速率为1000 mm/min时,复合界面组织最佳,界面处形成α-铜相、富铁相与Fe8CuS弥散相,实现了冶金结合。在另一项研究中,SINGH等[73]使用功率为3 kW的CO2激光系统将两种不同尺寸(直径<63 μm和直径>63 μm)的铜粉颗粒沉积在316不锈钢上,通过单次小粒径沉积和多次大粒径沉积分别得到了厚1 mm和3 mm的铜涂层,复合板界面结合强度约为48 MPa。研究发现,当铜涂层厚度为1~3 mm时,不会生成氧化层,但是在界面处生成了10 μm左右的孔隙,并且随着初始铜粒径的增大,孔隙的数量和尺寸都有所增大。此外,利用激光熔覆技术制备的铜涂层耐腐蚀性较好,可应用于铜铸铁罐以及储存核燃料的容器[74]。
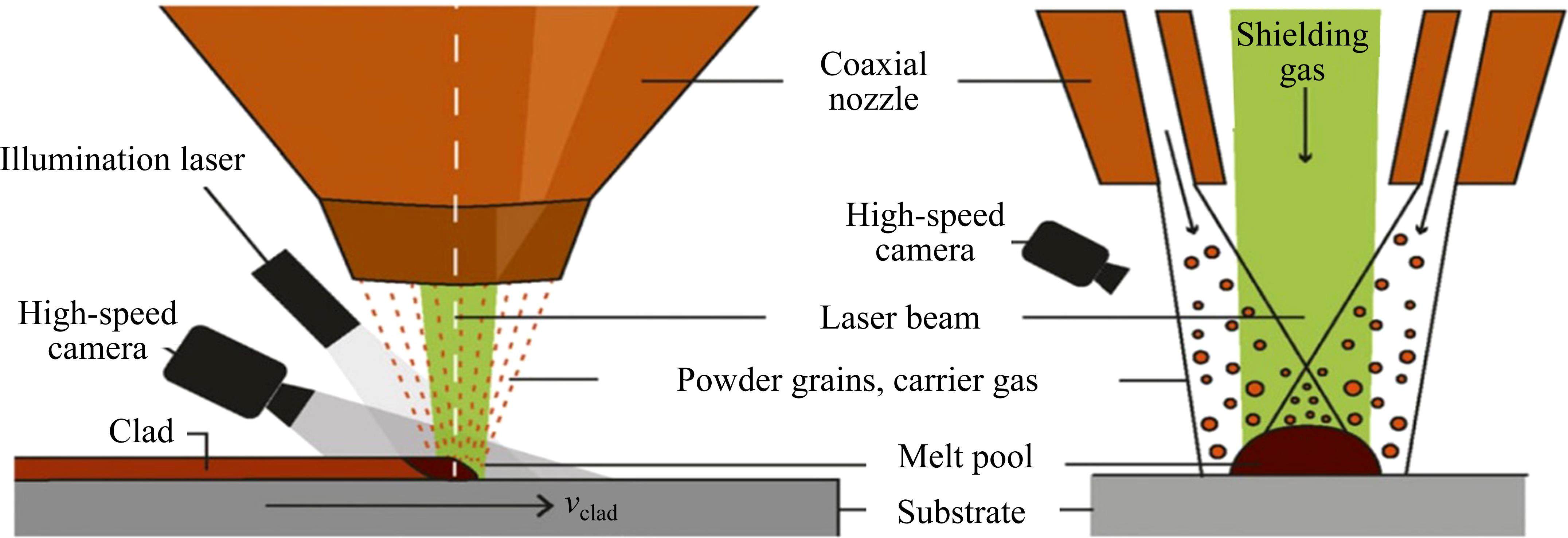
冷喷涂工艺是使铜粉颗粒在N2气体推进加速下,撞击基层钢板,使钢板发生明显的塑性变形,从而与基层钢板牢固地结合在一起,如图18所示[75]。冷喷涂技术通常在固态下实现,复合界面处没有新相和氧化组织出现,喷涂沉积得到的铜层具备较高的强度和延展性[76]。SINGH等[77]采用冷喷涂的方式,将粒径<38 μm的铜颗粒沉积在316不锈钢板表面,形成了厚约3 mm的铜涂层。研究发现,对钢基板进行Ni电镀处理能够使涂层结合强度由10.1 MPa提升到15 MPa,对复合板的抗拉强度和伸长率影响不大,但是选用Cu作为电镀层反而会导致电镀层在Cu粉颗粒冲击下与钢基体分离。SINGH等[78]在另一项研究中,具体分析了界面处钢侧铜粒子冲击的微观形貌,如图19所示。在常规冷喷涂工艺下,铜粒子撞击钢基体会使其形成一些裂纹,界面结合机理为机械咬合;铜粒子撞击电镀铜的钢基体后,基体表面无元素扩散,界面未结合;铜粒子撞击电镀镍的钢基体后,界面结合良好,存在机械咬合和冶金结合。SINGH等[79]还研究了316不锈钢基体表面粗糙度对复合板结合性能的影响,发现镜面抛光钢基体后涂层的结合强度由10.35 MPa提升到18.24 MPa,进一步对其进行热处理能够促进元素扩散,使界面结合更牢固。另外,QIAN等[80]采用微波加热技术代替热处理,对冷喷涂制备的铜/钢复合板进行快速加热,进一步降低了涂层的孔隙率,提高了界面的结合强度和弯曲强度。
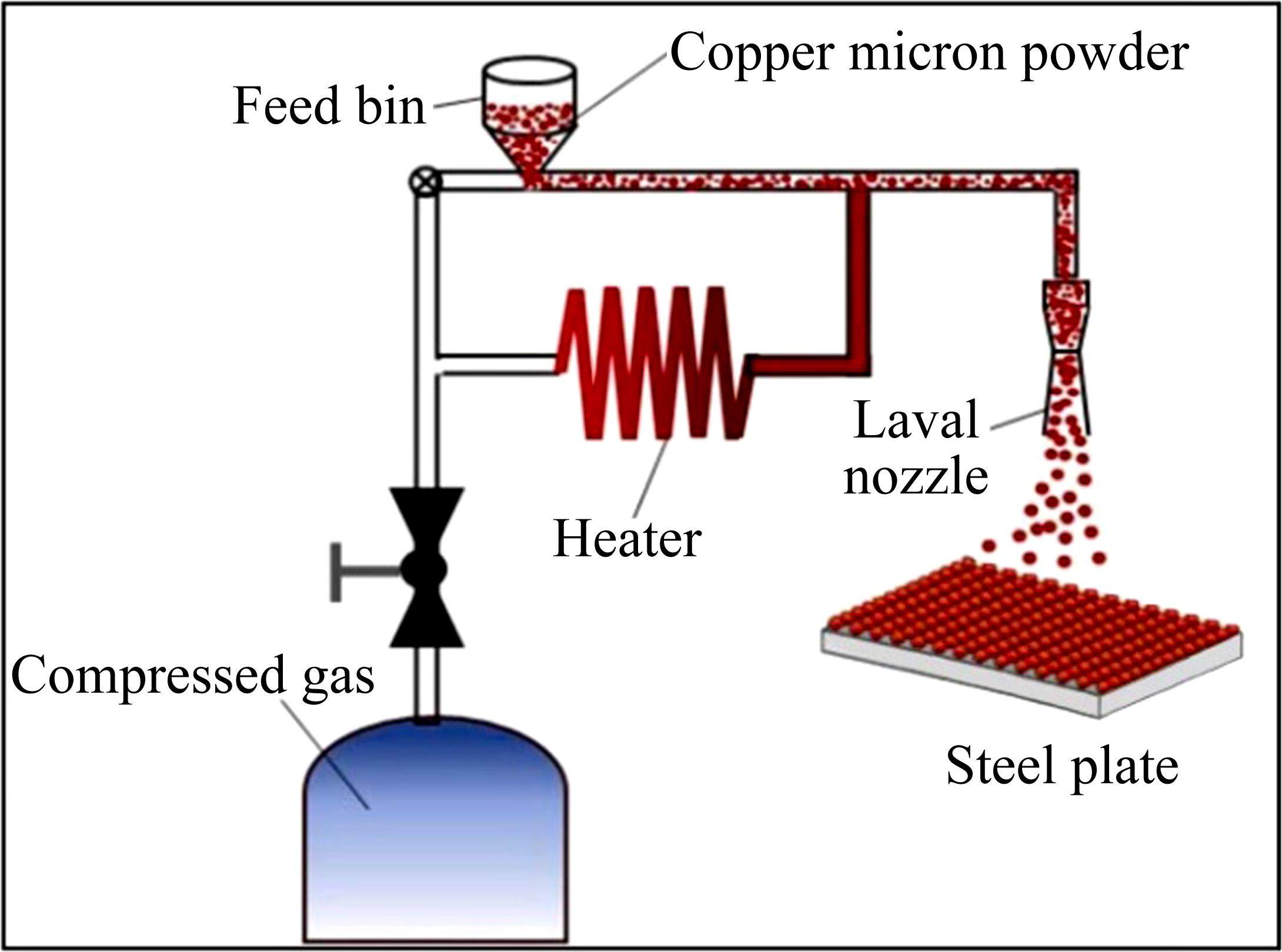
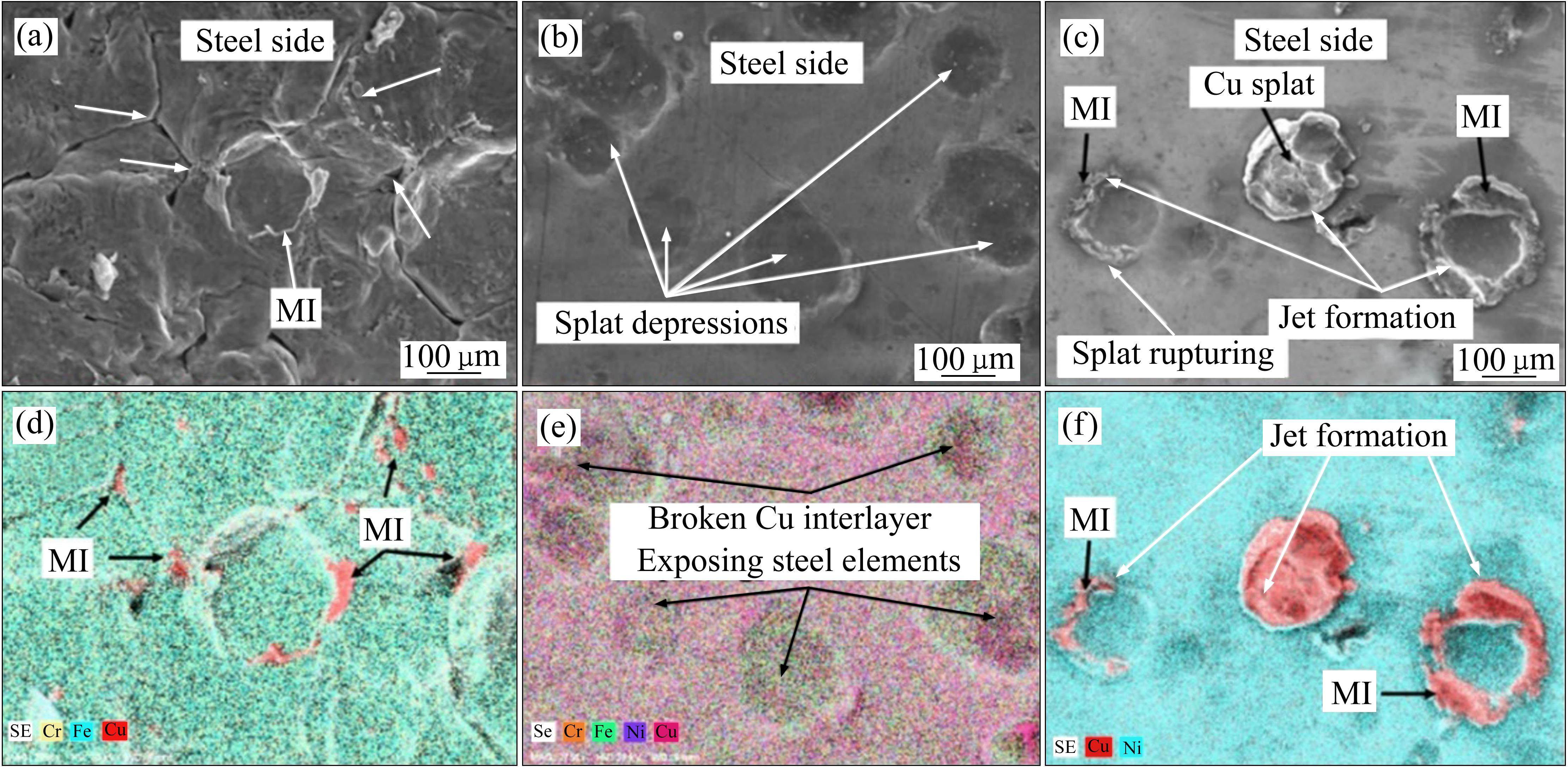
相较于冷喷涂制备复合板,采用激光辅助可以直接照射涂层粉末和基材,激光带来的热效应和能量加速了元素扩散,更有助于将铜沉积在钢表面。广西大学的QI等[81]采用激光辅助冷喷涂技术,在10 mm厚的Q235钢板上喷涂了一层铜,成功制备出铜/钢复合板,界面结合强度超过了68.5 MPa,其界面结合机理如图20所示。通过比较不同的工艺参数,发现随着激光功率增加,铜粉末和基材吸收的热量增多,促进了热软化和塑性变形,使界面结合强度增大,从而使沉积的铜涂层密度增加,孔隙率和显微硬度降低,晶粒先细化后又随着温度升高而粗化。最终得到制备Q235钢纯铜涂层的最佳工艺参数:激光功率4.0 kW,N2气体温度为800 ℃、气体压力为5 MPa。
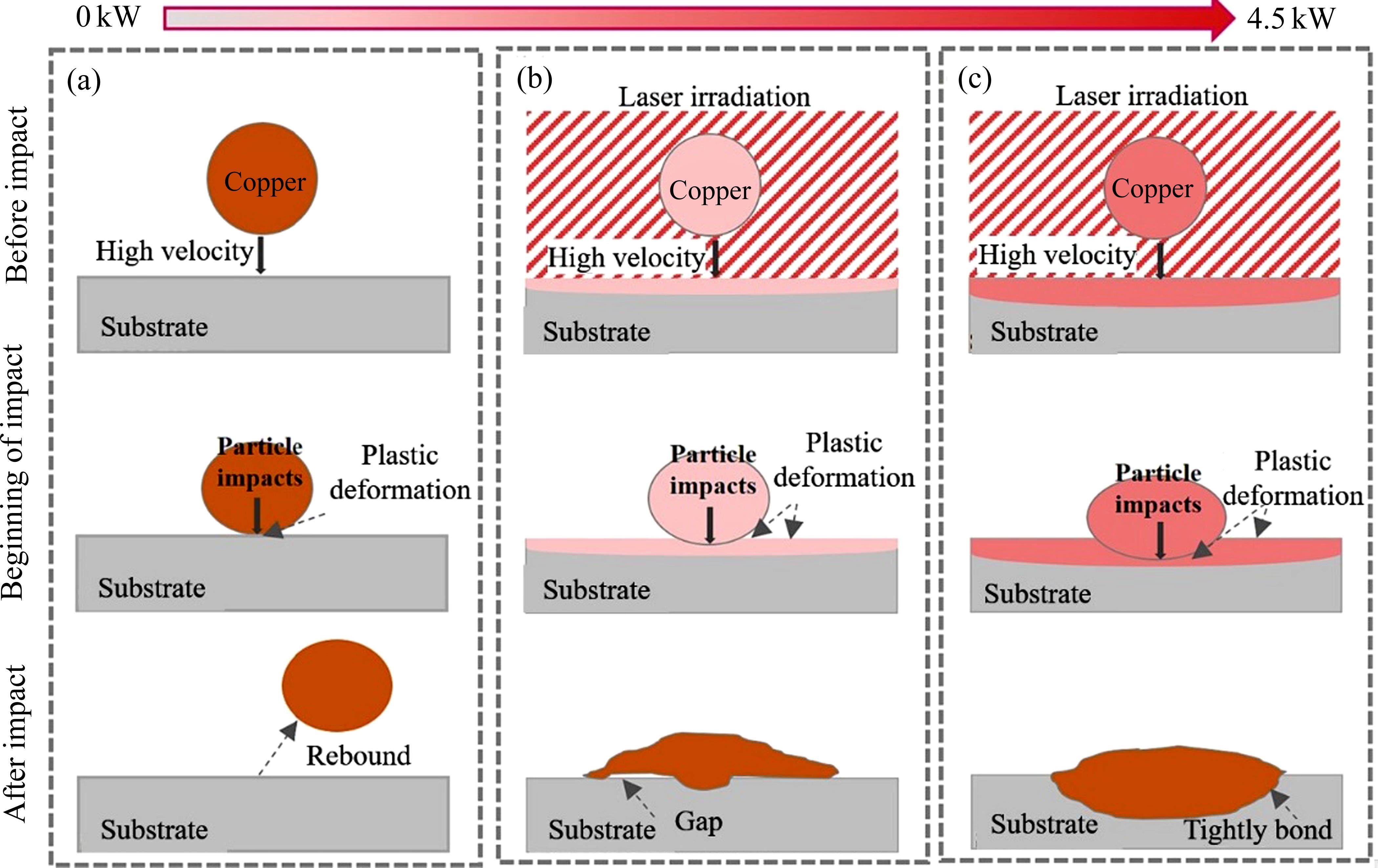
总而言之,增材制造、激光熔覆、冷喷涂、激光辅助冷喷涂等新型材料复合方法能够在钢板上固结一层箔材,实现复合板的制备。虽然涂层的厚度较薄,但是涂层的结合强度高,能够满足基本防腐要求。此外,这些方法也可用于制备铜/钢复合薄带,其相关工艺有待学者们进一步研究完善。
2 铜/钢复合材料界面结合强度调控方法
铜和钢的原子结构、原子键及物理性能差异较大,导致铜/钢变形不协调,从而使得复合界面处的性能不同于两侧金属,在界面处容易产生裂纹、应力集中等缺陷[82]。另外,在铜/钢复合板结合过程中,受工艺参数的影响,通常存在界面结合强度低的问题。鉴于此,可以通过选择合适的制备工艺改善界面的结合性能,在复合材料制备过程中添加合金元素,一方面能够起到固溶强化、细晶强化的作用,提高复合材料力学性能;另一方面能够替换部分原子,使这些原子周围的电子重新排列或是形成新的原子键,进而改善复合材料界面结合性能。在制备过程中添加外部能场或者后续通过热处理,也能够促进元素扩散,提高界面结合性能。下面将从铜/钢复合板界面调控的角度介绍不同的方法对界面结合强度的影响。
2.1 界面结合类型
铜/钢复合界面根据制备工艺和界面处的性能差异可以分为机械结合界面和冶金结合界面。机械结合也称为机械啮合,即通过外力作用将两金属板紧密压合在一起,其不依赖于元素间的扩散或化学反应形成化学键。常见的机械结合方法有爆炸焊接法、轧制复合法和搅拌摩擦焊接法等。这种结合方式所形成的界面横向拉伸强度较低,但纵向剪切强度很高。其缺点在于双金属结合界面粗糙,表面质量较差。
冶金结合则是通过温度和压力的作用使异种金属在界面处发生扩散、熔合或反应,生成金属间化合物,从而在分子或原子级别上实现紧密结合。这种结合方式需要严格控制温度、时间、压力等工艺参数,以保证界面达到稳定的结合状态。常见的治金结合方法有扩散焊接法、固-液复合法、搅拌摩擦焊接法、增材制造、激光熔覆和冷喷涂等。冶金结合的优点在于结合强度高、界面性能稳定、耐腐蚀性好,且能够在恶劣环境或高要求的工程领域应用。但是相对于机械结合,冶金结合的工艺过程更为复杂,生产成本也较高。
2.2 热处理对界面的影响
退火作为一种常用的热处理方法,可以明显改善复合板带组织结构、力学性能和复合界面结合强度,常被用于复合板制备过程的后续处理[83]。GHOLAMI等[84]研究了退火温度对冷轧法制备的黄铜/St14钢/黄铜复合板力学性能的影响,并通过实验得到了铜/钢/铜复合材料的成形极限图,如图21(a)所示。结果表明,冷轧复合工艺虽然提高了材料的拉伸强度和硬度,但会导致伸长率下降。通过退火处理,可以使St14钢层中发生再结晶现象,生成新的等轴晶,使得铜/钢/铜复合板的抗拉强度明显降低,伸长率增大,在600 ℃温度下伸长率达到最佳值41.1%,如图21(b)所示。GHOLAMI等[85]在另一项研究中,将压下量75%冷轧后的铜/钢/铜复合板在450~850 ℃温度下退火处理2 h,随炉冷却。通过微观结构表征,发现黄铜和St14钢的再结晶温度分别为450 ℃和600 ℃,且随着退火温度升高,再结晶晶粒逐渐长大;在铜/钢界面处没有中间化合物生成,且随着退火温度的升高,扩散层厚度增加,在850 ℃时达到最大值9.02 μm,而界面结合强度先增大后减小,在750 ℃时达到最大值,接近40 N/mm;另外,退火温度升高使得晶粒长大,进而导致断裂韧性降低,比较发现,退火温度为600 ℃时,黄铜/St14钢复合板的综合力学性能和断裂韧性最佳。
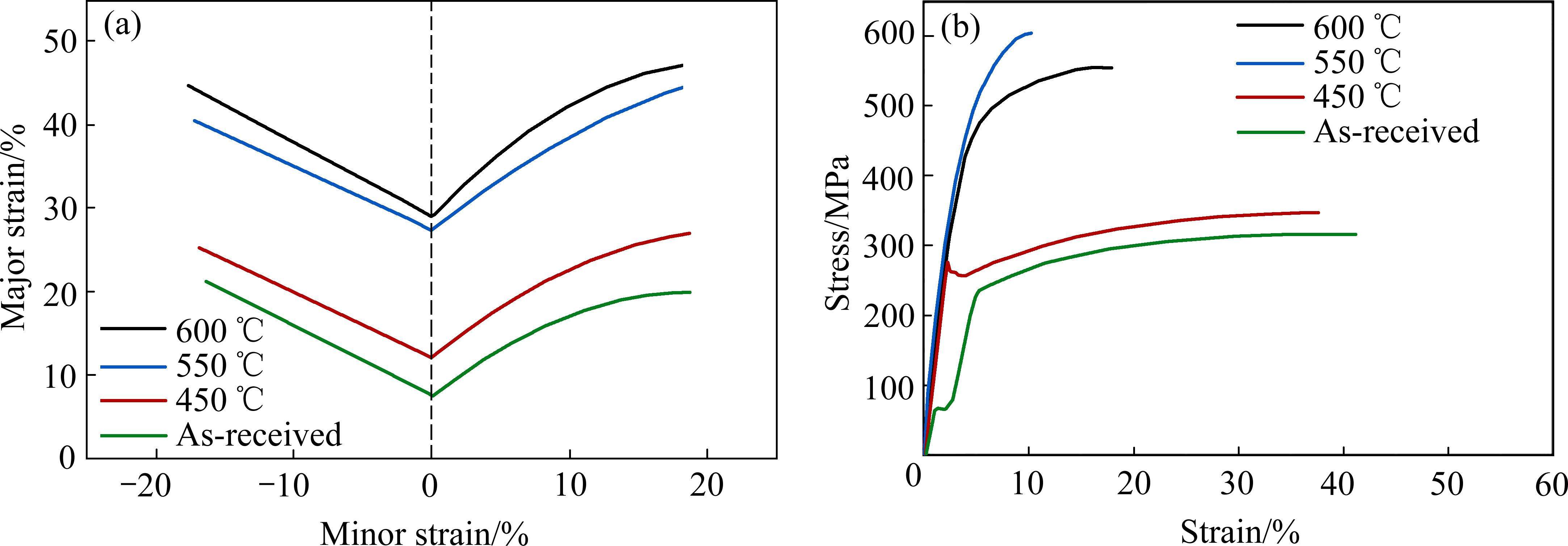
REN等[86]在400~900 ℃的温度范围内对爆炸焊接法制备的铜/SS304L复合板进行了1 h退火处理。研究发现,随着温度的升高,元素在界面处的扩散距离增加,在900 ℃时达到0.97 μm,并且抗拉强度先升高再降低,在500 ℃下达到最大值约970 MPa,伸长率约10%。退火温度超过500 ℃后,铜侧晶粒明显粗化,而在SS304L一侧可以观察到BCC到FCC的相变。退火温度升高产生的回复效果,也使得位错密度降低、残余应力消失、复合板软化,进而导致材料的硬度和强度降低,延展性显著提高,在900 ℃下,抗拉强度约为580 MPa,伸长率超过50%。
2.3 合金元素对界面的影响
对于固-液复合法制备得到的铜/钢双金属复合材料,铜晶粒要经历形核和长大的过程,在铜/钢界面处产生明显的合金元素扩散进入晶格的现象。对于铜/钢界面来说,两侧晶粒不同的晶体结构和堆垛方式对应不同的界面结构,其稳定性和结合性能也不相同。中北大学的朱旭东[87]分别选取γ-Fe和Cu的低指数晶面(100)、(110)、(111)进行表面收敛性测试,根据点阵错配度理论确定了Cu(100)/γ- Fe(100)、Cu(110)/γ-Fe(110)和Cu(111)/γ-Fe(111)三种稳定界面。然后,通过整体晶面平移的方式将Cu分别移动到γ-Fe(100)面的面顶点、边中点及面中心的位置,构建了3种不同的γ-Fe(100)/Cu(100)界面,如图22(a)所示;将Cu分别平移到Fe(110)面的面顶点、长边中点、面中心及短边中点的位置,构建了4种不同的γ-Fe(110)/Cu(110)界面,如图22(b)所示;将Cu分别平移到γ-Fe(111)面的面顶点和长对角线的1/3的位置,构建了2种Cu(111)/γ-Fe(111)界面构型,如图22(c)所示。通过比较,Cu(100)/γ-Fe(100)-down处(Cu移动到γ-Fe(100)面的面中心)的界面结合功达到最大值3.623 J/m2,得到稳定的界面构型,经过结合态密度分析可知,其界面处形成了Cu—Fe键。
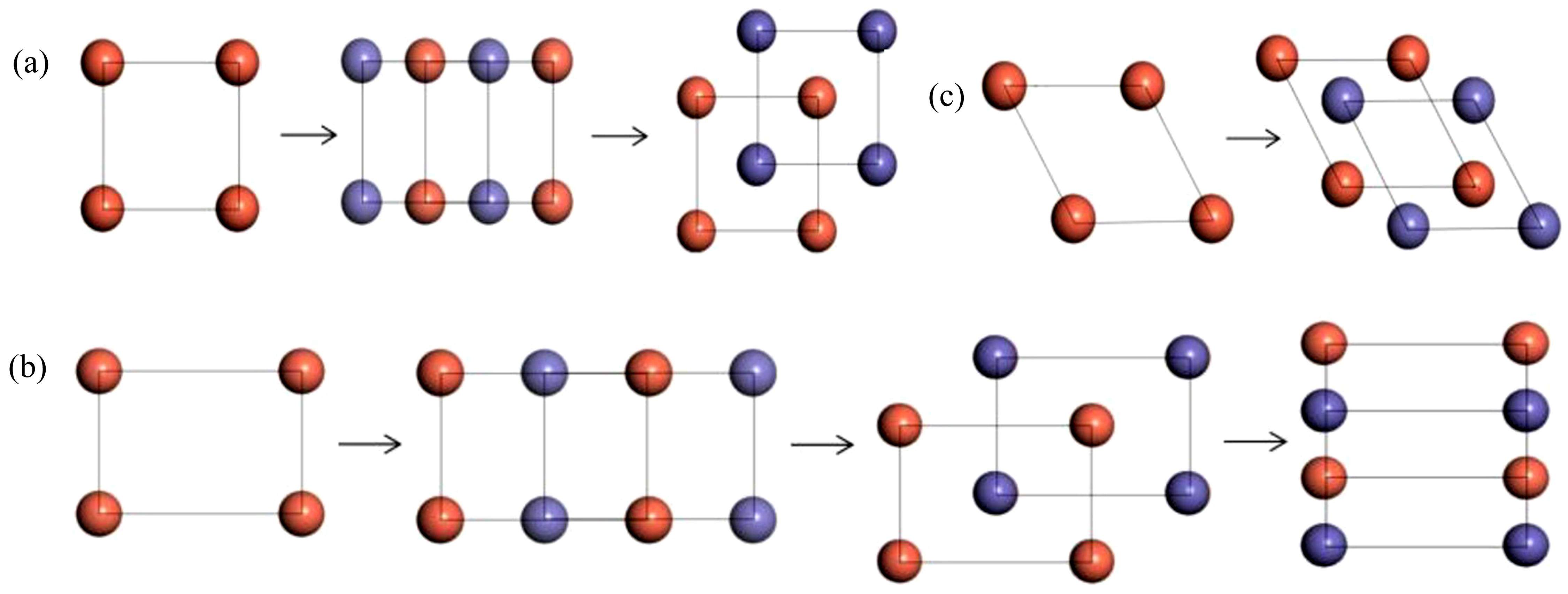
为了提高铜/钢双金属复合材料的性能,改善铜/钢界面处易形成裂纹与孔洞的缺陷。朱旭东[87]进一步根据第一性原理计算研究了铜中常见合金元素对Cu(100)/γ-Fe(100)界面结合性能的影响,发现Co、Ni、Si、Ti、Zn、A1、Fe能偏聚在γ-Fe(100)/Cu(100)界面处并形成化学键,从而增大γ-Fe(100)/Cu(100)界面的润湿性。通过进一步研究合金元素对力学性能的影响,发现Ni偏聚在界面处会提高界面强度,降低界面塑性;Ti偏聚在界面处会提高界面强度,不改变塑性和韧性;Co偏聚在界面处会降低界面塑性;Zn偏聚在界面处会降低界面的强度、塑性与韧性。吴迪等[88]也使用第一性原理计算研究了合金元素Cr、A1、Mo、W、Ni、Co、Mn对Cu(010)/γ-Fe(010)界面性能的影响,结果表明,合金元素C、Mo、W、Mn能够替换Cu原子,在界面处形成强X—Fe共价键,且X—Fe键共价性远高于Cu—Fe共价键,使界面结合功从1.61 J/m2提高到最大值3.87 J/m2,表明界面原子的结合力更大,界面更稳定。
除了铜合金中包含的元素,还有一些特殊元素,能够对铜/钢复合界面结合起到积极作用。KANG等[47]在固-液复合法制备的碳钢/锡青铜双金属试样中研究了P元素对界面微观结构和力学性能的影响,发现随着P元素含量增多,剪切强度先增大后减小。在750 ℃温度下α-Cu界面的晶界处析出了硬脆的Fe3P相,界面出现沉淀过渡带,使得剪切强度降低。而当P含量为0.1%时,剪切强度达到157.89 MPa,原子界面扩散距离为11.55 μm,此时碳钢与Cu-Pb-Sn合金形成了理想的冶金结合界面。
对于铜/不锈钢复合接头来说,两种材料的熔点、热导率和线膨胀系数差异较大,使焊接接头极易出现熔化未熔合、裂纹等缺陷。李继红等[89-90]采用Cu-Si和Cu-Ni药芯焊丝将T2铜/304不锈钢连接在一起,进一步研究了合金元素(Si、Ni)对铜/钢复合界面微观组织和力学性能的影响。结果表明,采用Cu-Si焊接接头的钢母材与焊缝交界处均存在明显的过渡区域,其组织可分为富铁相和富铜相,如图23所示[89]。而在Cu-Ni焊接接头中不存在明显的过渡区域,且焊缝中出现了较多的富铁相,这些富铁相多以树枝晶的形态存在。其原因是Si元素可以降低Cu与Fe之间的液相混合焓,促进熔池金属凝固过程中Cu和Fe的互扩散行为。而Ni与Fe元素在液相下可以无限互溶,使得熔融状态下的母材与熔池金属发生充分混合,并且由于溶质再分配效果,富铁相垂直于界面生长,并在成分过冷时由平面晶转变为树枝晶生长。此外,Si,Ni元素对材料拉伸性能提升不明显,但可以显著提高焊缝的冲击韧性,其中Cu-Ni焊缝的室温冲击吸收能量最高(AKV=54 J),可达铜母材的83%以上。
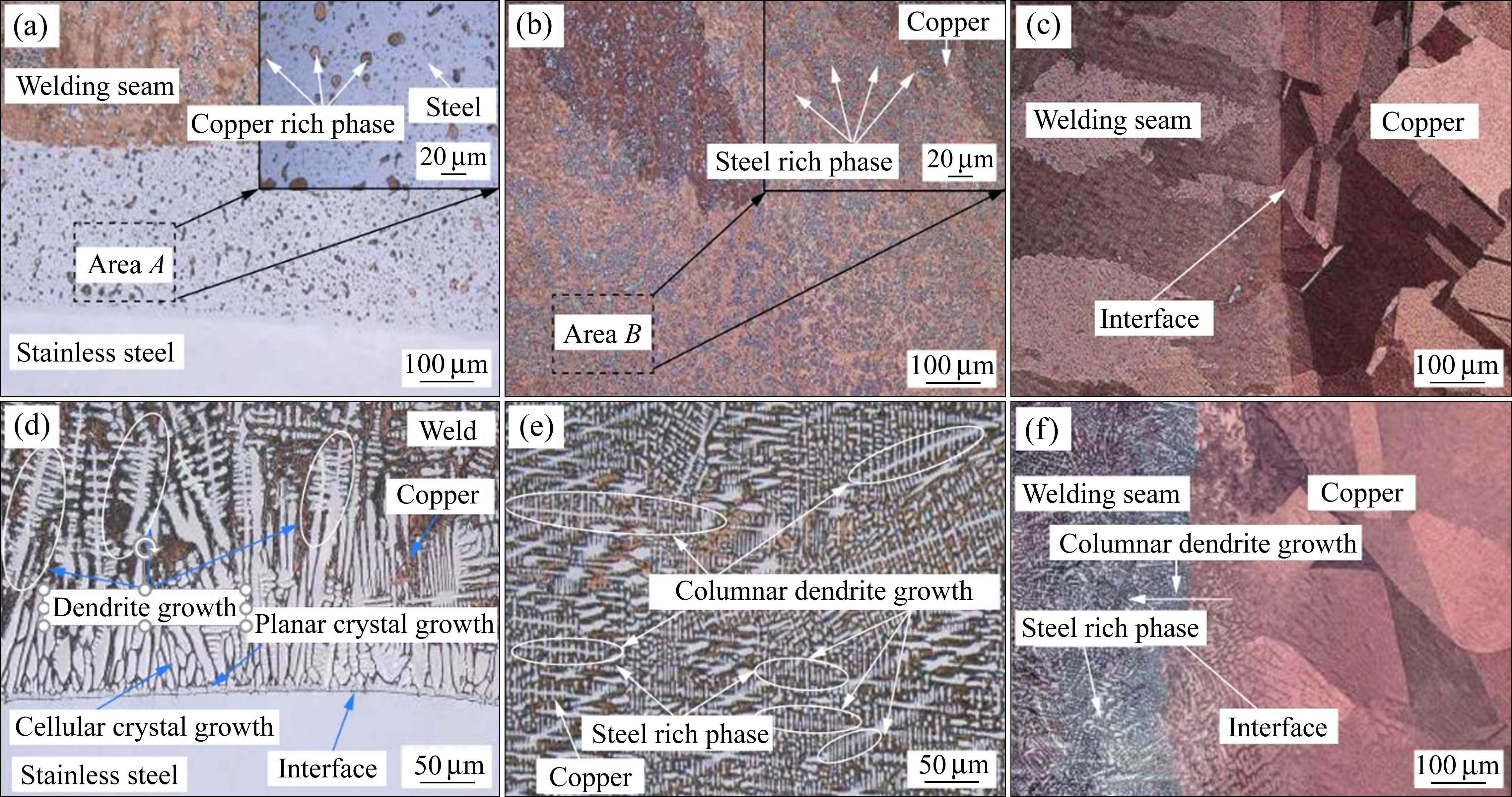
2.4 辅助板对界面的影响
为了提高界面结合性能,一般可以通过衬板辅助[91]或添加中间层[92-93]两种方式来改善复合板表面或界面的接触情况,进而影响元素扩散,使界面结合更牢固。衬板辅助是指在轧制过程中,通过在板材上下外表面添加一层较厚的硬质板材,改变界面传统结合方式,将轧辊与材料接触的强剪切力部分转化为压力,实现难变形金属单道次、大压下量轧制[94-95]。其工艺的特殊性使得剪切应力减小,大大抑制了板材在轧制过程中由剪切应力产生的边裂缺陷,提高了板材成形性[96]。一方面,衬板轧制可以改善板材的塑性,减少界面孔洞、间隙等明显缺陷[97]。另一方面,衬板轧制可以将平界面转变成波纹状,这样既实现了机械结合,也提高了界面结合强度[98]。
采用传统轧制方式制备铜/不锈钢复合薄带时,由于铜与不锈钢变形协调能力差,且对轧机性能要求高,在常规压下量下二者很难结合在一起。罗超[99]在0.3 mm厚的T2纯铜带与0.1 mm厚的304不锈钢带下方添加了1 mm厚的辅助轧衬板(Q235),使轧件可以顺利通过二辊轧机并达到所需的压下率,进而实现薄带复合,其工艺流程如图24所示。添加辅助衬板后,在轧制温度为400 ℃、有效压下量为39.5%的条件下,铜/不锈钢之间的扩散层厚度达到了1 μm,其复合薄带的抗拉强度达到了459 MPa,介于原始T2纯铜(326 MPa)和304不锈钢(841 MPa)之间,界面实现了良好结合。
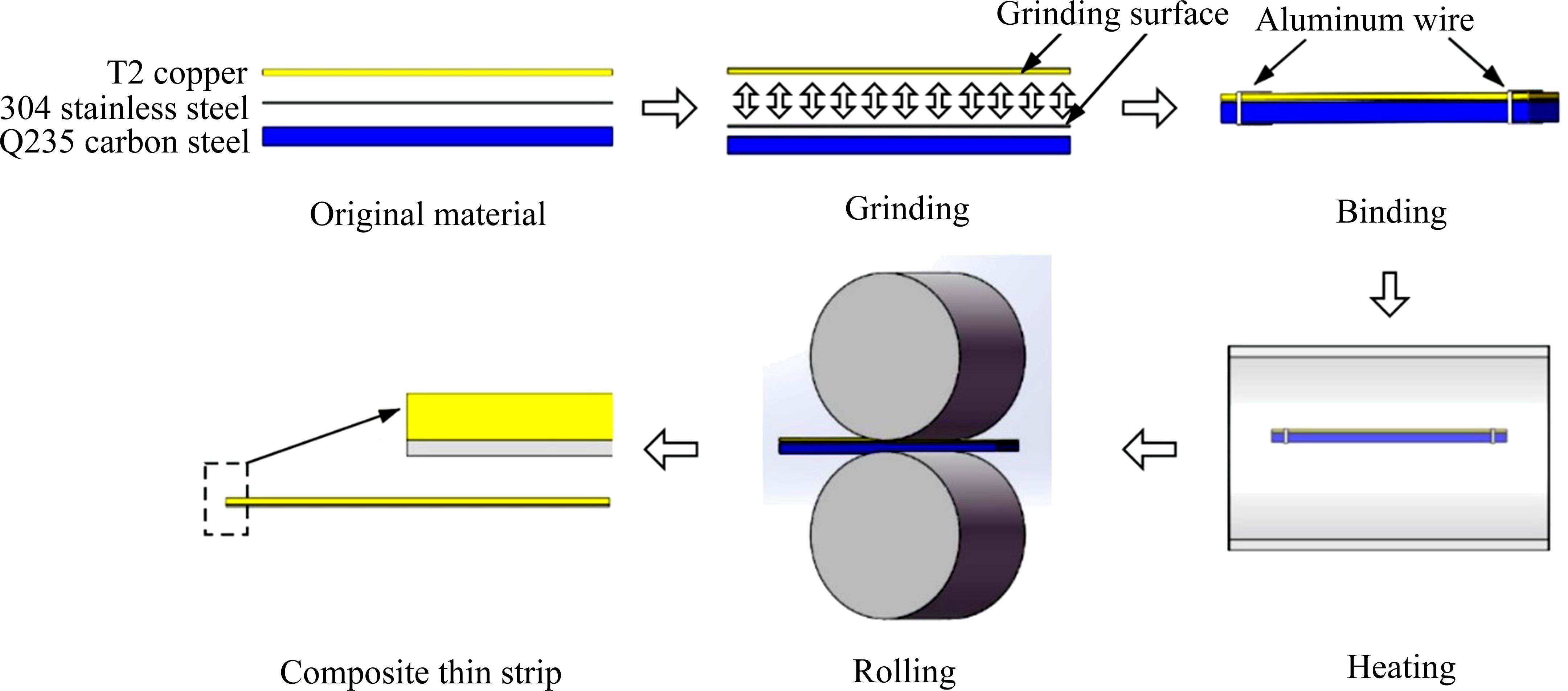
由于Ni和Fe之间以及Ni和Cu之间具有良好的相互固溶性,通常在铜和钢之间添加Ni夹层可以提高铜和钢之间的结合性能。SABETGHADAM等[31]在铜和410不锈钢之间添加0.1 mm厚度的Ni夹层,使用扩散焊接工艺制备了铜/不锈钢复合板。Cu/Ni和Ni/SS界面均形成不同的扩散区,且随着温度升高,扩散层厚度明显增大。在另一项研究中,YUAN等[32]以12.5 μm和50 μm厚的纯Ni为中间层,采用扩散焊接法制备出纯铜/304不锈钢复合板。在400 ℃温度下退火1 h后,界面结合强度达到217.2 MPa,在相同条件下,没有Ni辅助的界面结合强度约为174.2 MPa。
2.5 外部能场对界面的影响
近些年来,特殊能场被逐渐应用于复合板的制备和界面性能调控中[100]。常见的有超声振动[101]、激光辅助加热[78]和脉冲电流[102-103]等方式。超声振动辅助成形是对被加工材料施加特定方向、频率和能量的超声振动,利用高频振动能量辅助完成复合板的制备[104]。其产生的体积效应和表面摩擦效应,一方面可以破碎材料表面的氧化层,增大材料间的接触面积;另一方面可以改变金属的受力状态,促进异种金属材料协同变形[105]。激光辅助加热技术具有能量密度大、精确度高、功率容易调控的特点,能够通过外部热场辅助加热直接熔化异种金属,使界面处发生冶金结合,从而提高复合材料的结合性能[78]。
脉冲电流辅助技术源于对金属材料的电致塑性研究,其利用脉冲电流产生的集肤效应、热效应和非热效应,可以解决复合板在大下压率复合时异种金属协调变形差、界面氧化膜去除困难和界面处金属间化合物层生成等不易控制的问题[106]。上海交通大学的XU等[107]分别研究了T2纯铜和304不锈钢的电塑性行为,发现电流的非热效应促进了铜中沿不同晶体取向的位错运动,从而降低了电塑性效应的流动应力。而对于304不锈钢,电流的热效应起主导作用,也受到马氏体相变的影响。此外,脉冲电流还能降低材料变形抗力,进而降低轧制过程中的轧制力,减轻设备负担。张浩然等[108]将冷轧复合法制备的T2纯铜/304不锈钢复合薄带退火后进行通电拉伸试验。研究发现,随着脉冲电流增大,复合薄带的抗拉强度和延展性下降,当电流达到50 A时,抗拉强度由约700 MPa降低到约600 MPa,伸长率减少了50%。通过微观表征发现,随着电流增大,拉伸断口界面处韧窝数量减少,表现出由韧性断裂向脆性断裂转变的特点。
脉冲电流辅助还可以增大界面处元素扩散速率,使界面更好地结合在一起。TIAN等[109]利用大电流脉冲电子束对扩散焊接法制备的Cu/316不锈钢复合材料进行预处理。结果表明,虽然界面在800 ℃和850 ℃温度下并未结合,但是经过大电流脉冲电子束处理后,界面实现了良好的冶金结合,元素扩散距离分别由3.7 μm和4.2 μm增加到6.2 μm和8.3 μm,如图25所示[109]。在800 ℃和850 ℃温度下经脉冲电流处理后的界面剪切强度分别达到了103.1 MPa和134.8 MPa,相比于不施加脉冲电流分别提高了约1.95倍和1.70倍。
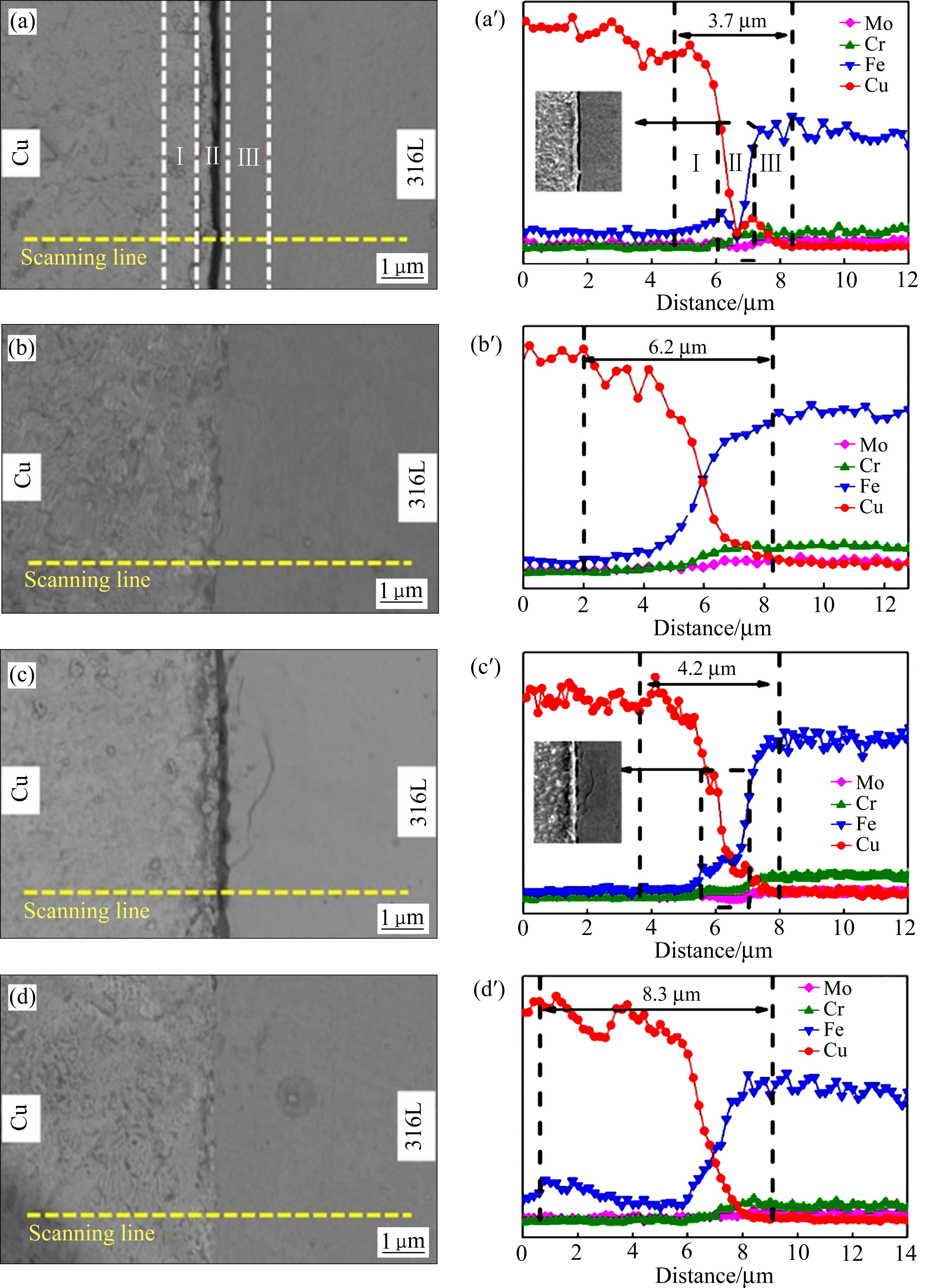
3 结论和展望
铜/钢复合板具备优良的导电导热性、高强度和耐腐蚀性,在微电子、热交换器等对材料性能要求较高的领域具有显著的应用前景。目前不同规格铜/钢复合板制备工艺日趋成熟,其制备方法具有不同的优缺点。采用传统的爆炸焊接、扩散焊接、轧制复合、固-液复合、搅拌摩擦焊接等方法时,不同的工艺参数对复合板结合性能、剪切强度影响较大;而采用新兴的增材制造、激光熔覆、冷喷涂、激光辅助冷喷涂等工艺制备的铜涂层虽然很薄,但是界面结合强度高,在表面防腐和微电子领域有不可替代的作用。
目前,针对铜和钢力学性能差异较大、界面结合质量低的问题,学者们已经开展了较为系统的研究工作,在调整工艺参数、改善元素扩散、引入中间层和外加能场等方面取得了很多成果,较好地指导了工程应用。但针对未来高质量发展趋势及新的使用环境,本文作者认为以下几方面值得进一步研究和探索。
1) 随着国家大力推动高性能铜及其合金材料的研发应用,铜/钢复合板更需要引入不同的铜合金与高性能钢进行匹配结合,利用合金元素促进界面结合,以达到特定的剪切强度、抗拉强度,满足高端市场的需求。
2) 针对小厚度铜/钢复合板的研究主要采用喷涂、熔覆等工艺制备涂层,但是这些工艺对设备和环境要求太高。采用轧制复合法制备铜/钢复合薄带可以批量生产且产品界面结合质量高、力学性能好,但是这方面的研究较少,理论和工艺还不成熟。
3) 外加能场特别是脉冲电流能够明显降低材料的变形抗力,其与轧制复合法相结合,能够起到调控界面性能的作用,但其工艺还需进一步完善。
王恒, 李国艳, 李莎, 等. 铜/钢复合板制备工艺及界面调控研究进展[J]. 中国有色金属学报, 2025, 35(1): 99-125. DOI: 10.11817/j.ysxb.1004.0609.2024-45176
WANG Heng, LI Guoyan, LI Sha, et al. Research progress on preparation process and interface control of copper/steel clad plate[J]. The Chinese Journal of Nonferrous Metals, 2025, 35(1): 99-125. DOI: 10.11817/j.ysxb.1004.0609.2024-45176